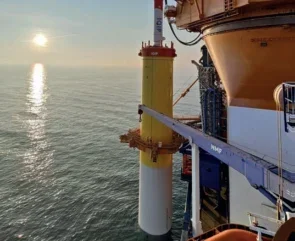
Offshore is very different from onshore. Scales are different – towers are much higher, blades much longer. Regional variations are also greater – not only in terms of shallow or deep inshore waters (the former allowing fixed farms, the latter requiring floating ones) but also in legalities and permitting – and politics and tax.
Nowhere is this clearer than in North America. The United States has nearly 1,500 gigawatts (GW) of fixed-bottom offshore wind potential; but over the last eight years, the nation’s 0.042 GW of installed capacity has lagged China (31 GW) and Europe (30GW) by almost three orders of magnitude.
President Biden has set an ambitious goal of achieving 30 GW of offshore wind by 2030. But last year a Danish developer cancelled two major offshore wind projects in New Jersey due to economic concerns. Perhaps more worryingly Donald Trump has vowed to immediately halt offshore wind energy projects “on day one” should he be elected to a second term as US president. In his most explicit threat to the industry yet he reportedly said at a fundraising dinner with oil executives in April: “I hate wind”.
The hatred has been reported to stem from the former President seeing offshore turbines from his Scottish golf-course and believing they spoil the view.
“If I were in the offshore wind industry, I would probably be pretty, pretty nervous,” a former Trump administration energy official told the Washington Post.
Nevertheless, in January this year the US’s first largescale offshore wind project, the Vineyard Wind development off the Massachusetts coast, produced power for first time, delivering around 5MW to the New England grid. The operator of the project said it expects to have five turbines operational in the early part of this year, before eventually having 62 turbines as part of the project, enough to power 400,000 homes. Unfortunately, in July this year, a blade became damaged – it is not clear how – and parts of it detached and fell into the sea. Debris washed ashore along Nantucket beaches for several days. The incident has not, of course, helped US offshore prospects.
The rest of the world has been rather more welcoming. Europe has positively embraced offshore wind, especially in the North Sea. Many of the suitable shallow-water sites have already been developed with or are scheduled for sea-bed farms; attention is now moving towards floating farms – which can be placed further from shore where winds are more consistent, and made with higher towers for more efficiency.
Asia is similarly ebullient. Global Wind Energy Council expectations are that Asian offshore wind capacity will reach 165GW by 2030. China will account for much of the growth, but analyst Wood Mackenzie recently forecast Japan’s offshore wind capacity would expand to 4GW by 2028 – a 62-fold increase from 2018. Public attitudes and policy in Japan are favourable: the government recently passed a law to allow construction of offshore wind farms beyond port-related zones.
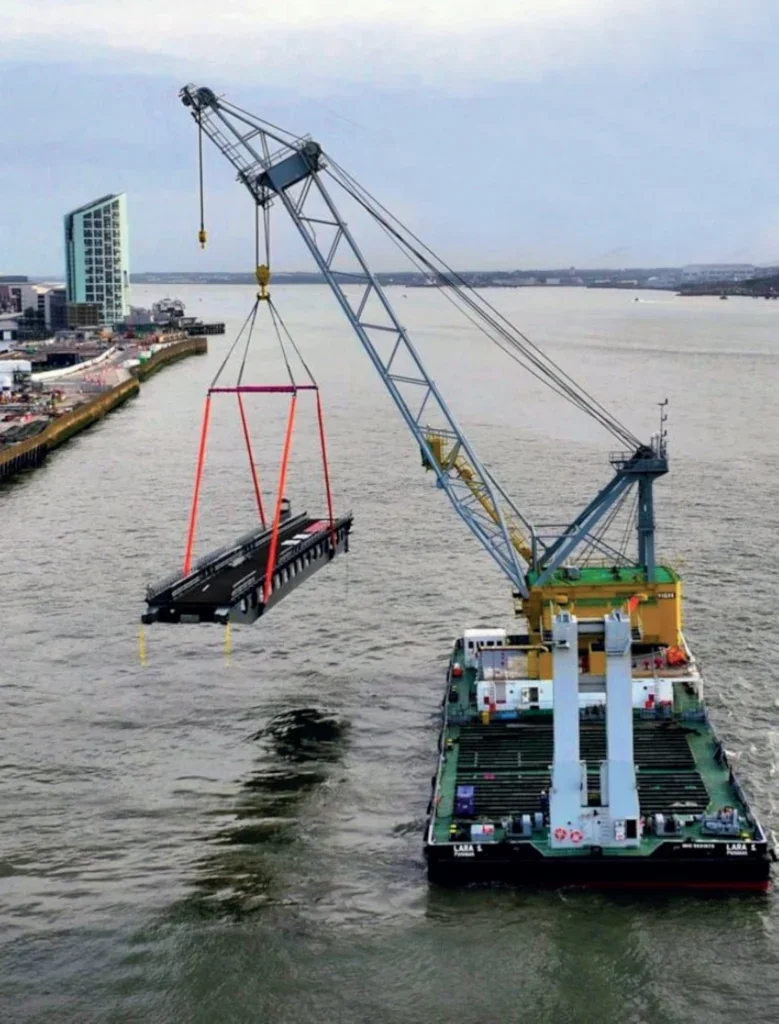
Delivering on these expectations though is challenged by the sharp increase in water depths close to the Japanese coastline, which limits areas suitable for sea-bed turbines. Maximising the energy output, therefore, requires large wind turbines – the installation of which in turn calls for large Wind Turbine Installation Vessels (WTIVs). With most such vessels tied up with duties in European waters, Japan has an urgent need for high performance WTIVs, purpose-built to do the job.
One such vessel is Van Oord’s giant new vessel Boreas, which was launched in May this year at the Yantai CIMC Raffles Offshore shipyard in China and is currently fitting out (see box). It will be commercially available from 2025 – though it will not initially ply Asian waters. Also in May Van Oord was awarded the contract for the transport and installation of the monopile foundations for the 1.6 GW Nordseecluster offshore wind project in the German sector of the North Sea, and this will be the first project for the Boreas. 44 Nordseecluster monopiles are planned for installation in 2025 and the remaining 60 monopiles by 2027.
Nordseecluster is far from Van Oord’s only North Sea operation, of course. In May Van the company’s offshore installation vessel Aeolus installed the first monopile foundation at the 1.4GW Sofia Offshore Wind Farm on the Dogger Bank 195km off England’s east coast. In the coming months, Van Oord will install a total of 100 monopile foundations. The 1.4 GW Sofia Offshore Wind Farm, one of the largest offshore wind projects in the world, will have enough capacity to power 1.2 million average UK homes.
The divide between onshoreand offshore is far from absolute though. Onshore lifting companies, great and small, are seeing opportunities at sea and are wanting to join in. Thus Durham Lifting, a hitherto land-oriented crane hire and services company usefully based on the North Sea coast, in April this year obtained a ‘Fit for Offshore Renewables’ (F4OR) accreditation status. F4OR is a programme designed to prepare the UK supply chain to enter and work in the offshore renewable energy sector. The programme does not require participants to have offshore experience but does require them, in its own worlds “to have identified offshore renewable energy as a strategic opportunity for growth.”
DOCKSIDE DEVELOPMENTS
Dockyard installations, and the companies that operate them, also span both sectors.
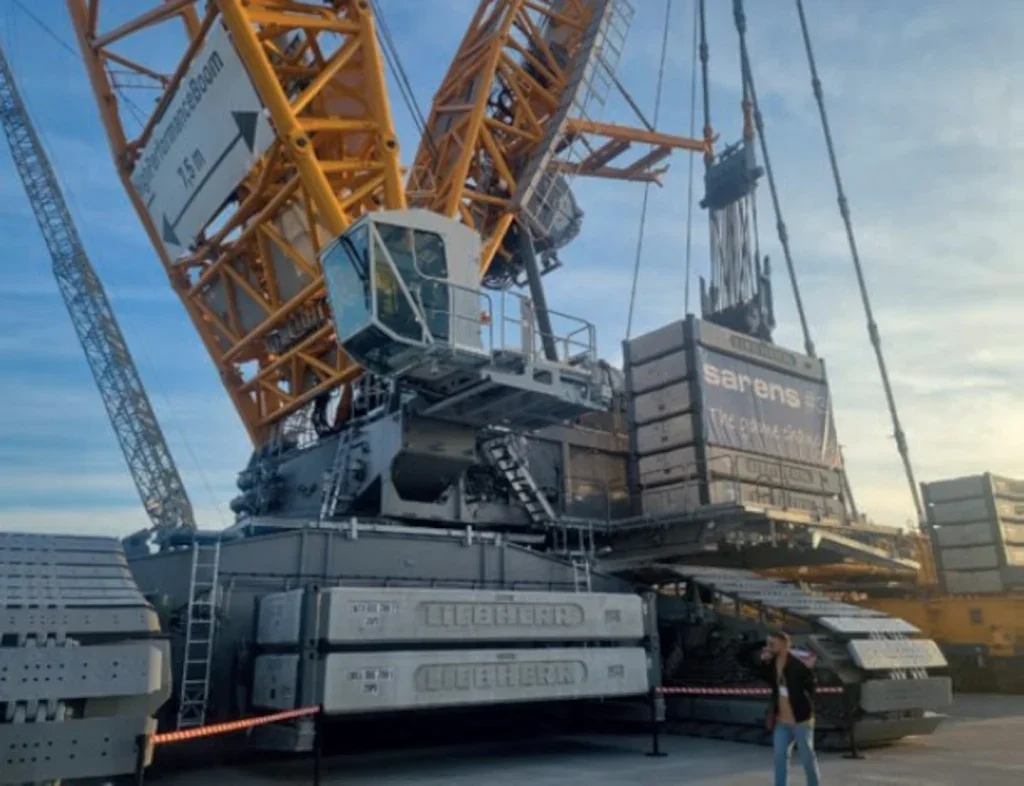
Seas offer space for movement of large components; but those components have to make the transition from their fabrication site on land, to their destination offshore. This becomes increasingly complex: just as installation vessels are having to become larger, so too do port and harbour installations.
Sarens, for example, is using very large crawler cranes for handling offshore components. It currently has three Liebherr LR12500-1.0 crawlers; it bought the first one last year, the other two this year.
Yannick Sel, Sarens’ group commercial director of projects, explains why: “We see a significant need for this type of crane and the type of job it can perform. This is why we decided to increase our arsenal. We are particularly focusing on jobs in renewables for the new 2500T crane. Handling offshore wind turbines at ports is becoming an important business segment as the weights of components continues to rise.
“One of the new cranes is in Norway serving a project for Siemens Gamesa, exchanging components for Hywind Tampen FLOAT offshore project. The other is in Eemshaven, the Netherlands, loading and uploading transition pieces and monopiles.”
Consider also Japanese crane manufacturer Tadano, whose lifting gear has hitherto been exclusively land-based.
Its largest crawler cranes, the CC 88.1600-1/ CC 8800-1, with a maximum lifting load of 1,600t, and the CC 88.3200-1 twin/ CC 8800-1 twin, with 3,200t capacity, have attracted interest for offshore wind base ports, of which there are currently four in Japan, for loading wind farm components on to installation vessels.
But Tadano has gone further: it announced in July this year a collaboration with Danish wind power manufacturer Vestas to develop and sell wind turbine nacelle cranes globally – beginning with versions for Vestas’ new V236 offshore wind turbines.
Nacelle cranes are permanently housed at the top of the tower in the nacelle itself; they are used to raise parts and equipment from ground (or sea) level for lifetime maintenance and servicing of the generator.
They are equally necessary for onshore and offshore farms but the offshore versions need higher lift heights (rope lengths) and greater weather protection.
Although details of the new cranes are not yet available, Tadano revealed that they will be extremely durable in order to withstand the extreme conditions, the strong winds and high salinity, of offshore use.
INNOVATIVE SOLUTIONS
Ports and harbours that cater for offshore wind are sometimes remote; and do not always have space for ever-larger facilities and equipment. In these cases ingenuity has been key – as, for example, Mammoet’s solution for offloading transition pieces at the port of Nigg for the Moray West offshore farm (see box opposite.)
Indeed, ingenuity has led to a whole new category of crane being created for handling offshore wind turbine items; in July Dutch company Tetrahedron completed a 130m prototype. The design has a completely new motion principle and structural force flow compared to conventional cranes, the company says.
A large scale non-slewing prototype shows this new motion principle; and the different force flow was verified based on strain and deflection measurements.
The design claims the advantage of higher lift compared to a luffing boom crane. The prototype was assembled according to plan and the crane performance meets the design requirements and matches the predictions of the design and engineering phase, say Tetrahedrons designers.
The Tetrahedron prototype crane’s drive and control systems are fully electric. A fast and smooth luffing motion reaches 130m lifting height above ground level – it would be only 90m for a luffing boom crane with the same footprint.
A very slender jib creates freedom to move the load, which is of interest for blade handling operations; and real time sideload measurement, which again is of special interest when lifting loads (i.e blades) that are designed to catch the wind.
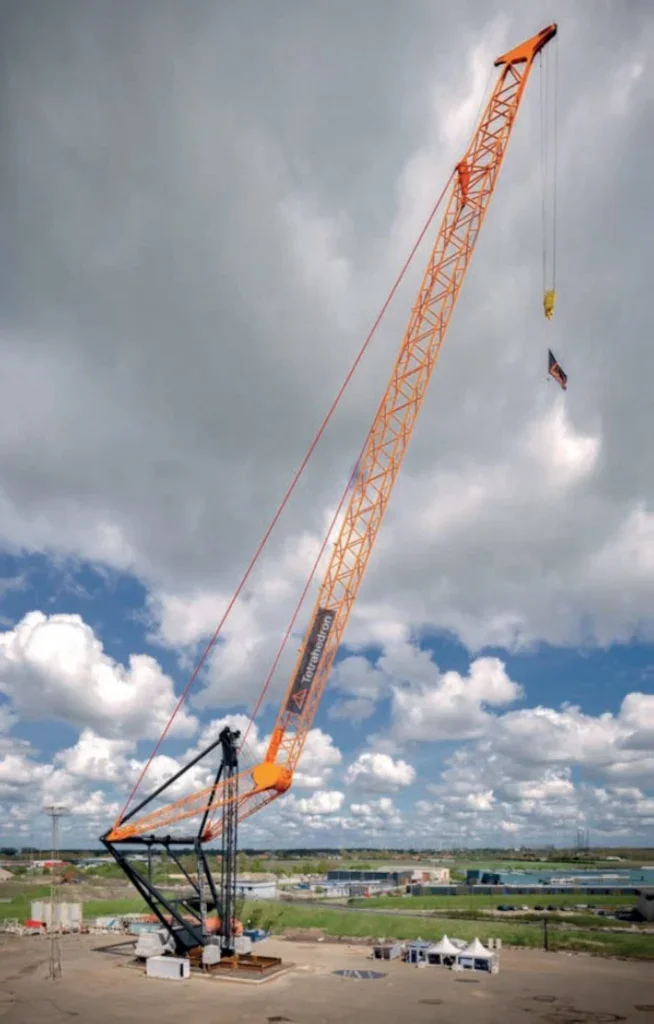
The prototype has been erected onshore but was intended to demonstrate the Tetrahedron crane’s offshore suitability for wind turbine handling, especially when installed on compact jackup vessels with tubular legs, where it would be capable of maintenance work on 10MW wind turbines.
These compact jackup vessels are nowadays typically used for accommodation and light works. At the start of the project there was little demand for such compact accomodation jackups and they would have been readily available for mounting such cranes; but, as we have seen, demand now is too great for the option of modifying these vessels towards wind turbine maintenance units. Therefore the installation of the Tetrahedron prototype crane on these vessels is for the moment suspended, and the prototype crane remains onshore for demonstration purposes waiting for a later-to-bedefined destination.
But offshore wind generation is not going away. Of all the nonfossil- fuel resources it remains the most practical, the most present, and the fastest-growing. Whether tower can get taller still and blades still longer is for engineers to determine. The lifting industry will find responses to the challenges that are set. Those responses will require imagination, ingenuity and hard work. Read these pages to follow them.
LARGEST OFFSHORE WIND TURBINE INSTALLATION VESSEL NEARS COMPLETION
The Boreas is part of Van Oord’s preparation for the increase in scale in the offshore wind industry. Upon completion it will be the largest vessel of its kind: it is 175 metres long. Huismann has supplied the vessel’s main, leg-encircling, crane, and this too will be the largest of its kind that Huisman has developed to date, in terms of lifting capacity, and of boom length, and of installed power. Its 155-metrehigh boom is able to lift over 3,200 tonnes. The system is fully electrically driven, giving high positioning accuracy; the new slew bearing system, developed in-house, increases this. The energy grid provides reduced maintenance and lessens the energy consumption of the crane significantly.
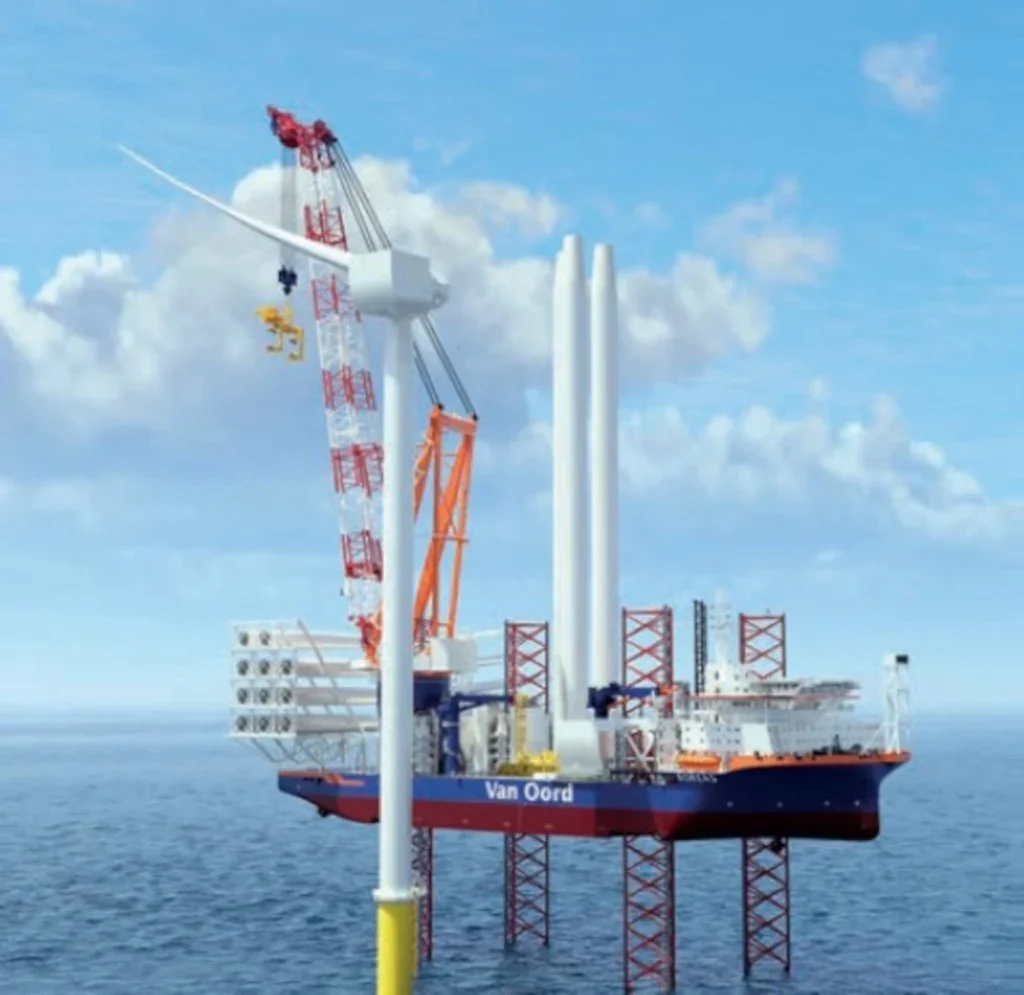
The boom’s unique design makes it stiff and lighter in weight, leading to reduced motion at the crane tip, and a small tail swing optimises free deck space.
The vessel has also an auxiliary hoist, of 500t capacity, and two auxiliary telescopic cranes which are supplied by MacGregor. One is a 27.5t 45m machine the other 17.5t with a 42m reach. They will be used to transport the cargo and for load handling during the installation of wind turbines in the offshore environment and are equipped with an anti-collision system. Four legs, each of 126 metres, allow the vessel to be jacked up and work in waters up to 70 metres deep. It will therefore be able to install the next generation of 20 MW offshore wind turbines at sea.
The Boreas is itself part of the energy transition, being the first of its kind to be able to run on the future fuel methanol, which will reduce the ship’s carbon footprint by more than 78 percent.
A battery pack of about 6,000 kWh can take peak loads and regenerate energy to reduce the fuel consumption and corresponding emissions even further.
MAMMOET SAVES TIME WITH MANOEUVRABLE CRANE AND SPMT TP TRANSFER
22 kilometres off the Scottish coast, Moray West marks the third offshore wind farm in the Moray Firth region, joining Moray East and Beatrice. Global Energy Group sought Mammoet’s guidance and engineering when a planned RoRo method of offloading Transition pieces (TPs) for the farm was no longer feasible.
Mammoet proposed transshipping the TPs onto Self-Propelled Modular Transporters (SPMTs) using a crawler crane, with its ballast supported by a separate axle line combination.
The method resulted in greater manoeuvrability and less downtime between lifts. It also prevented the shifting tides at the marshalling port from impacting the operation.
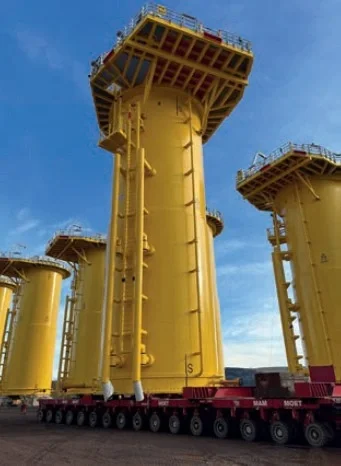
The TPs arrived by ship at the port of Nigg. The original plan was to drive them off the vessels using SPMT transport with a TP handler attachment. However, this plan had to be altered late in the planning stage. Oliver Smith, senior commercial manager at Mammoet, explains why:
“As things developed, new information about stowage plans, how the TPs were going to be set out on the delivery vessel, and the heights and the mooring arrangements meant this was no longer an option.
“It came down to the load-out methodology and the load-in not aligning, with a big part of that being the fact that the vessel would be moored stern on to the quay. This meant there wasn’t enough space to get a TP handler onto the vessel and get the TPs off it.”
Work-around solutions would have been possible, says Smith, but “ultimately to support a holistic approach to get the components from A to B we came up with a crawler crane solution”.
There were two TP types: 60 units weighing around 505t, to support offshore wind turbines, and two heavier Offshore Substation Platform transition pieces (OSP) weighing around 832t.
The 60 TPs were lifted off the vessel using a LR11350 crawler crane onto a 32-line configuration of SPMT. The crane was supported by a separate 24-axle line combination, which was used to maneuver the ballast tray.
Smith explains the time-saving benefits of this method: “It is possible to move the tray by crane, but we needed a quicker, more efficient mechanism, which is why we used SPMT transport.
“If you lift the tray by crane and have close to 600t worth of ballast, you must lift that block by block to relocate it. With the SPMT, once it takes the load of the ballast wagon it can move faster.”
The TPs arrived at the port in varying numbers, ranging in batch sizes from four to as many as 16. This caused challenges at times, especially if there were any delays to the vessels. The team were able to adapt, manage and prevent schedule changes from causing issues.
The crane solution also meant that the offloading stage wouldn’t be negatively impacted by the tides, as the components were lifted off the vessel instead of being rolled off.
“Our working relationship with the customer is one that has been built on years of trust, having performed previous successful heavy-lift and transport projects at the same site, including for Seagreen Offshore Wind Farm. We have a good working relationship with the port and have been able to work together in a very complimentary fashion,” closes Smith.
“I think its success was a testament to the start of the project, when we worked closely together, and offered transparent engineering feedback that enabled us to change the planning at the last minute to use the crane and complete the project to a faster schedule.”