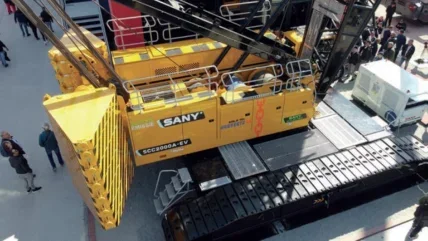
Crane owners looking to boost their fleet with a new lattice boom crawler crane were spoilt for choice at Bauma 2025 – where manufacturers showcased new models and innovations. From a heavyweight with a huge load moment, to clever counterweigh innovations, to fully electric options – lattice boom crane buyers were well catered for.
In the southern lot of the outside area at Bauma, Japanese manufacturer Tadano presented its new flagship CC 78.1250-1.
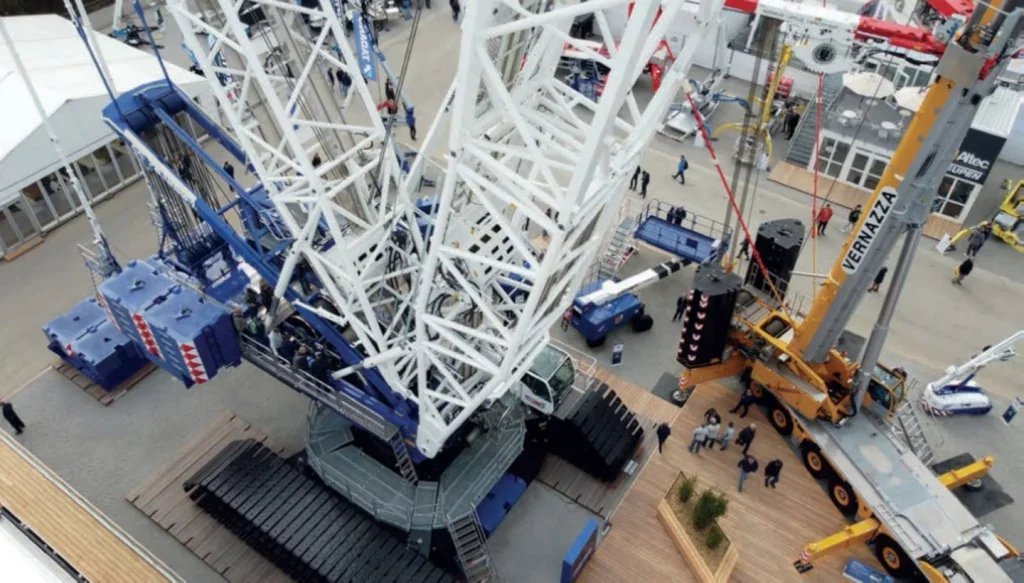
The crane marked Tadano’s keenly awaited return to the lattice boom crawler crane sector. It is a 1250-tonne capacity crawler aimed at wind, industrial, infrastructure and stadium applications.
The crane is the evolution of the CC68.1250-1 and incorporates advancements in performance, safety, efficiency, and transportability.
“With this crane we are reaffirming that we are back in the crawler crane business,” states Lance Rydbom, vice president of product management, Pan- America operations, at Tadano.
The CC 78.1250-1 retains the same 1250 tonne rating capacity as the CC68.1250-1 but Tadano has managed to increase the crane’s maximum load moment by 12 percent (from 15,800tm on the CC68.1250-1 to 17,900tm on the CC 78.1250-1).
“This is huge for users,” says Rydbom. “The longer boom configurations now possible mean the crane is well-suited all types of heavy lifting, including the wind industry where components are becoming ever bigger and heavier.”
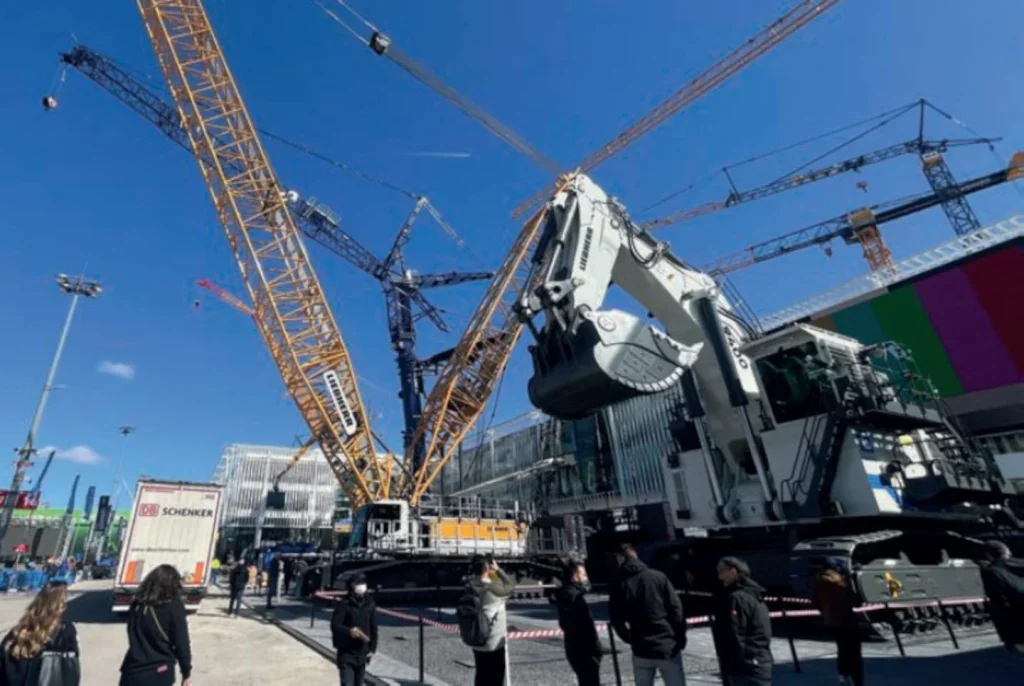
The crane has a maximum hook height of 224.5 metres when equipped with a 15-metre fixed jib. In this configuration it can lift 140 tonnes. To improve its stiffness, the width of the base crane has increased from three metres on the CC68.1250-1 to 3.5 metres.
Two crawler shoe widths are available, 2.0 metres and 2.4 metres, to accommodate varying ground pressure requirements.
Despite the wider crane base width the CC 78.1250-1 has been designed for ease of transport and Tadano has reduced the weight of each crawler track by ten tonnes – going from 70 tonnes down to 60 tonnes. This means that the complete crane can be transported using just 42 flatbed trailers, with the heaviest load being the tracks.
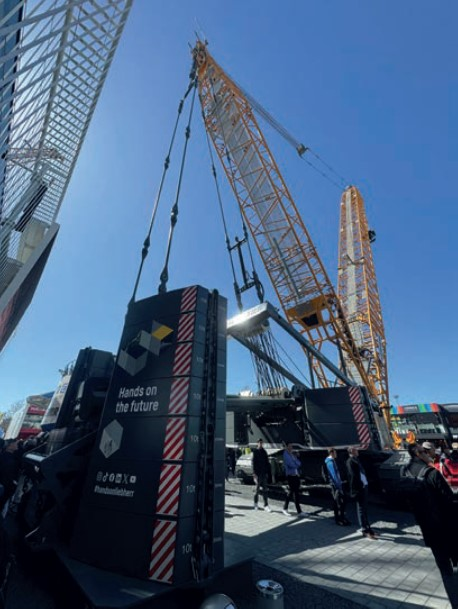
The Boom Booster system, which can be used on both the CC 78.1250-1 and CC68.1250- 1, can also be collapsed for transportability. It goes from six metres wide in use to just three and-a-half metres wide for transport.
Lifting points on various components are designed to make assembly safe and efficient, plus also facilitate ease of transport.
The crane is manufactured in Zweibrücken, Germany, Tadano says the crane adheres to worldclass safety standards and utilises high-quality components.
The crane has been designed to offer multiple redundancies. It has, for example, a dual-engine arrangement with an optimised hydraulic system, allowing for single-engine operation at reduced speeds. The crane’s twin Mercedes-Benz engines are also compatible with HVO fuel.
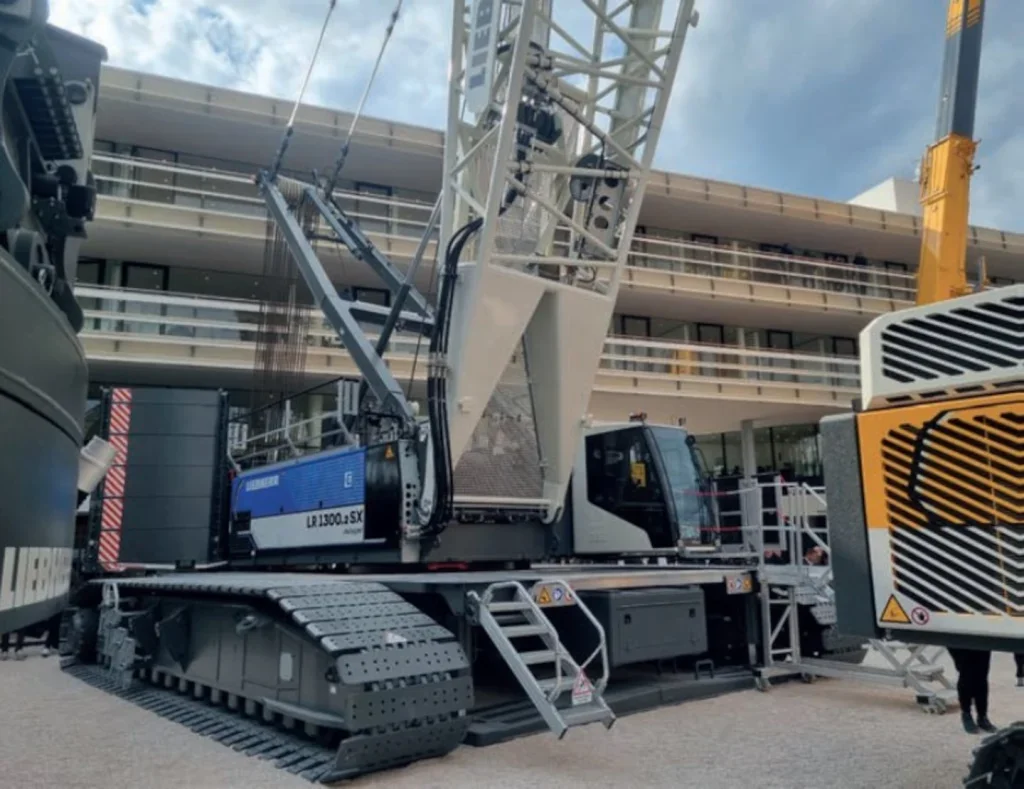
Flexible user-friendly interfaces and an optional dual CAN BUS system also contribute to increased reliability and operational flexibility, says Tadano. An optional auxiliary power unit enables cab systems, HVAC, and lighting to operate using a compact 22.8 HP diesel engine, reducing fuel consumption and emissions during standby operation.
For enhanced operator confidence and job site security the crane is equipped with the Tadano Fall Protection System and incorporates protective access to the superstructure and the undercarriage including improved handrails, catwalks, and access ladders.
The cab design provides an expanded field of view, while an array of cameras and mirrors help the operator see the hoist drums and other blind spots around the crane.
“The cab is the one we developed for the CC 38.650-1,” says Rydbom. “Its cab is a twoperson can and is wider than the one used one the CC68.1250-1. It has a jump seat next to the operator’s seat – so there’s plenty of room in there.”
For job sites with uneven terrain an optional Pedestal Crane (PC) kit replaces the crawlers on the undercarriage with outriggers enabling levelling at three different outrigger bases (39.4 ft x 39.4 ft, 45.9 ft x 45.9 ft, and 52.5 ft x 52.5 ft) offering compatibility with existing foundations.
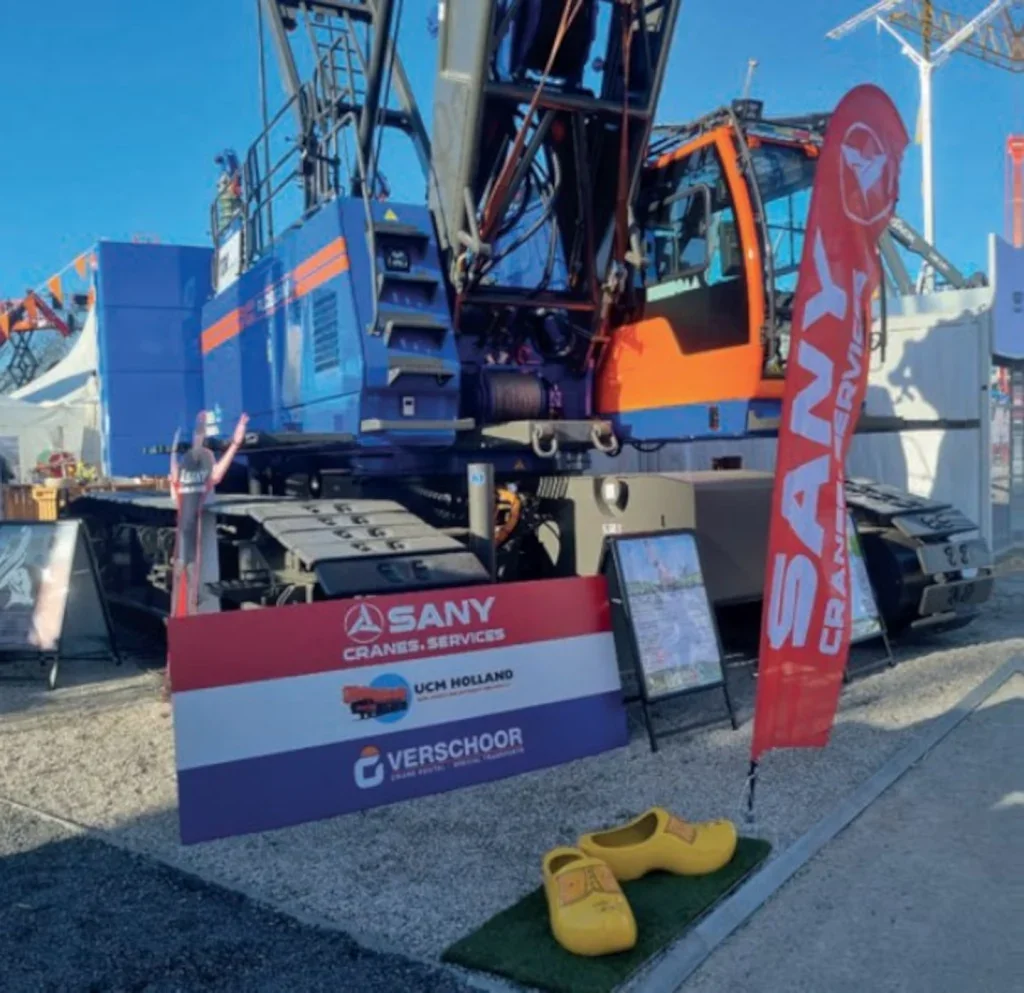
The CC 78.1250-1 utilises Tadano’s IC-1 control system which also gives the operator real-time ground pressures on the rigging aids when erecting long boom systems, plus remote telematics for real-time diagnostics and remote troubleshooting.
The crane’s counterweigh system is a new design for Tadano. “Instead of a single stack we have used a double stack counterweight on the superstructure,” explains Rydbom. “This is the first time we’ve done this. The primary reason was safety. When you’re stacking up two hundred or three hundred tonnes of counterweight it’s going to get pretty high, around 15-16 pieces high. With the double stack design we’ve reduced this so that the maximum stack is seven pieces high.”
“The CC 78.1250-1 represents a significant step forward in Tadano’s crawler crane development,” says Andreas Hofmann, Executive Vice President of Research & Development. “Customer feedback played a crucial role in its design, ensuring that this crane delivers not only superior lifting capacity but also transport-optimised components and efficient assembly sequences.”
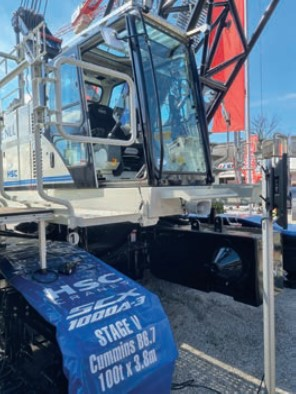
The first company to buy a Tadano CC 78.1250-1 is Maxim Crane Works, one of the largest crane rental companies in North America.
The purchase was concluded with a signing ceremony at Bauma 2025. “At Maxim Crane Works, we are committed to providing our customers with cutting-edge lifting solutions,” says Paul McDonnell, CEO of Maxim. “The specifications of the CC 78.1250-1, including its exceptional lifting capacity and transport efficiency, made it an easy choice for our fleet.
“We can’t wait to have this crane available to work on critical projects.”

A video of the crane at Bauma, and an interview with Lance Rydbom, can be seen here: https://shorturl.at/lapVt
COUNTERWEIGHT CULTURE
In the middle lot of the outside area at Bauma 2025 was Liebherr, which had two lattice boom crawler cranes on its stand: the LR1400.1 SX with derrick system, and the LR1300.2 SX Unplugged.
The 400-tonne capacity LR1400.1 SX was presented for the first time with derrick equipment, and suspended counterweight, designed to increase crane’s lifting capacities for particularly heavy lifting operations and long boom and luffing jib configurations. Liebherr’s aim in doing this is to expand the range of applications available for the LR 1400.1 SX.
With the derrick system the crane has a maximum boom length of 220m and a maximum pulley height of 217.2m.
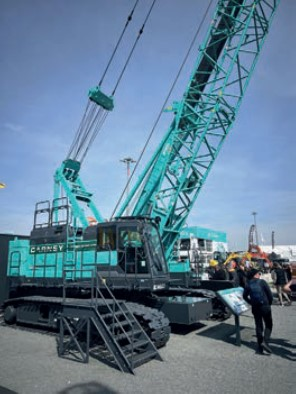
The suspended counterweight consists of a main and an additional counterweight and can be adjusted using an infinitely variable hydraulic extension device. With Liebherr’s VarioTray, the additional counterweight can be increased or reduced with counterweight slabs weighing 10.1 tonnes each, depending on requirements – without an auxiliary crane.
The position monitoring of the suspended counterweight is designed to provide maximum safety during operation. If this is set down on the ground, it is not possible to turn or travel with the crane or move the counterweight.
To help the operator determine the best boom combination for the respective jobsite requirements, and to simulate the lift in advance, Liebherr’s Crane Planner 2.0 lift planning software can be used.
Other operator assistance and control features on the LR 1400.1 SX include a gradient travel aid for the safe negotiation of slopes. The crane’s control system automatically calculates the centre of gravity and warns the operator before the crane leaves the safe area.
Ground pressure is also calculated in real time and the crane’s control system compares this with predefined safety limits for the respective jobsite. The ground pressure is displayed in the operator’s cabin.
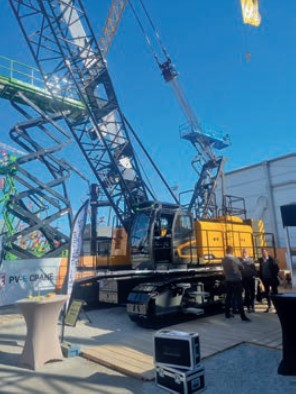
The ground pressure of the crane can also be reduced using the ground pressure reduction plates. During lifting work, the operator can lower these plates to increase the crane’s ground contact area. By doing this the ground pressure under the crane can be reduced by more than half. This is also particularly useful when lifting long booms from the ground, says Liebherr.
Another safety enhancement is a boom up-and-down assistant system. When erecting or lowering the boom the assistance system indicates the approach to the tipping border and automatically stops operation before the operator unintentionally enters an unsafe zone.
Controlled folding of the jib is activated simply by pushing a button. The speed of the laying down procedure is controlled with a single joystick. In the process, the boom-up-and-down assistant chooses the safest method for laying down the boom.
EMISSIONS-FREE
Liebherr also used Bauma 2025 to debut its 300-tonne capacity battery-powered LR 1300.2 SX Unplugged – a fully electric version of the LR 1300 which Liebherr launched almost 18 years ago.
The LR 1300.2 SX Unplugged is powered by a 438kW electric motor and, depending on the application, can be operated for up to 13 hours without a mains connection thanks to a 392kWh battery.
Subject to the available infrastructure on the job site the complete battery-charging process lasts between 4.5 and 8.5 hours. Whilst charging crane operation can continue as normal. Whether attached to the electric supply or not, the performance and range of applications remains unchanged.
The derrick counterweight system on the LR 1300.2 SX Unplugged also extends the crane’s range of possible applications – especially for heavy lifting and long boom combinations. Adjustment of the suspended counterweight is possible without an auxiliary crane.
The LR 1300.2 SX Unplugged can be equipped with seven different boom configurations up to a maximum boom length of 169m. At Bauma 2025 it was shown with a 20m main boom and an adjustable 20m jib.
The LR 1300.2 SX Unplugged comes with many of the same digital assistance systems seen on the LR 1400.1 SX including Crane Planner 2.0, gradient travel aid, boom up-and-down assistance, and ground pressure monitoring.
Like the LR 1400.1 SX, ground pressure reduction plates, mounted at the front and rear of the crane, reduce ground pressure by up to 56 percent.
The LR 1300.2 SX also has Liebherr’s safety system for crawlers working on floating units.
Liebherr also enjoyed sales of other lattice boom crawler cranes at Bauma. Czech company AG Transport, for example, ordered another LR 1800-1.0 – this time with the new X3A boom system, while Houston, USA-based Bigge Crane and Rigging bought three LR 1700-1.0 and three LR 1500 crawler cranes (plus 20 LTR 1220 telescopic crawler cranes!).
ELECTRIC AVENUE
In the north lot of the outside area at Bauma 2025 was Chinese manufacturer Sany which was showcasing its flagship lattice boom crawler: the fully electric SCC2000A-EV.
The 200t capacity crane has an 86m main boom, a 30m fixed jib and a 63m luffing jib.
The crane has a maximum lifting moment of over 1300 tonne metres and a wide range of possible jib configurations to suit a range of different working conditions.
The crane is powered by a 422.87 kWh high-capacity battery and a motor with a rated power of 234 kW, a rated torque of 1118 tonne metres, and a peak torque of 2125 tonne metres. This, Sany claims, offers powerful performance and a run-time exceeding eight hours.
It supports AC/DC multi-mode charging with real time monitoring and protection against overheating, overcurrent and leakage. It also enables European standard doublegun DC fast charging and can be fully charged in just two hours.
The eco-friendly electric drive also eliminates engine maintenance, adds Sany.
The crane has a working width of 7.5m to provide enhanced stability. The crane’s chain type flat track pads are designed to handle sandy, muddy and gravelly conditions, Sany says.
The crane has been made using premium brand components.
The battery, for example, is from CATL. The hydraulic motor and reducers are by Rexroth. And the electric motor and main valve are from Danfoss.
The crane is equipped with a centralised lubrication system designed for easier and more efficient maintenance.
The SCC2000A-EV can be operated via a wireless remote control system, enabling operators to control crawler travel, lifting operations and outrigger positioning, and rear counterweigh self-assembling.
This machine features a newly-designed cab equipped with a suspension seat and a dual 10.1-inch smart touchscreen. The screen can supply split views of the surrounding area, winch monitoring, and zoom camera of the boom or jib head (allowing real-time awareness of the equipment’s surroundings).
For enhanced transportability, the boom segments have a ‘threein- one’ transport feature which Sany says greatly lowers transport costs. A YouTube video of the crane can be seen here: www.youtube.com/watch?v=jr5jlhhjxVk
The model on display on Sany’s stand at Bauma, the first in Europe, has been bought by Nederweert, Netherlands-based crane and transportation company Herpertz. It was sold to them by Sanycranes. services/UCM Holland – which is Sany’s dealer for Europe and is also located in The Netherlands.
Sanycranes.services/UCM Holland also had a stand at Bauma, in the outside south lot. “We’ve sold 60 new Sany crawler cranes (lattice and telescopic boom) in the last five years,” says Jack Donker from Sanycranes. Services/UCM Holland. Donker has multiple roles at the company encompassing sales and customer liaison to ensuring all paperwork is EU compliant. “We have Sany customers across Benelux, UK, and Poland – those are the main countries we serve,” he continues. “Being in Western Europe our market is mostly electric these days. In the last two years we’ve only sold one diesel model for a customer who wanted to upgrade his Sany Stage 5 diesel crane to an electric model.
“The cranes we have here on the stand are all electric. It’s our main market and being able to supply a portfolio of electric cranes really helps us stand out in the market.”
On the Sanycranes.Services/ UCM Holland stand was a 50t capacity electric telecrawler (bought by foundation specialist Van Thek) and a 200 tonne electric lattice boom crawler (which, like the SCC2000A-EV, had been bought by Herpertz.
“Most of our customers are already on their fifth, or sixth Sany crane – that’s really nice to see,” concludes Donker. “And because there’s not been many electric options in the all terrain crane sector we’ve seen crane companies using electric crawlers instead. In this way the electric crawler market has cut into the mobile crane market a bit.”