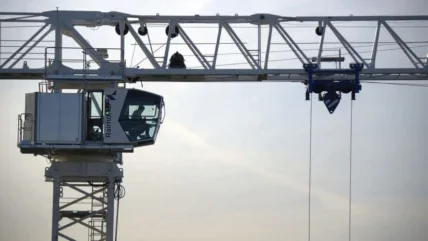
We start with Manitowoc’s Potain brand. In April 2025 Potain launched, from its factory in Zhangjiagang, China, the highcapacity MCR815. Its maximum capacity of 64t is double that of the plant’s current largest luffing jib crane, the 32t capacity MCR 625. The reasoning behind the development came from Manitowoc’s Voice of the Customer process which indicated growing demand for large luffing jib cranes on high-rise buildings and infrastructure projects.
The jib is 70m and can be luffed to an out-of-service radius of just 16m, making it ideal for congested jobsites. The winch is a new design, and powerful, giving line speeds of up to 185 m/min with a 2.3t load.
When the MRC 815 is fitted with a 30m jib and rigged in threefall reeving, that 64t maximum capacity can be lifted at between 4.5m and 18 m working radius. With 60m of jib it can lift that maximum at between 7m and 19.5m working radius; in this configuration it can still lift 7.5t at the jib end. When all nine jib sections are fitted, to create a 70m reach, the crane will lift tip loads of up to 7t with single-fall reeving. For heavy-duty lifting, such as handling large precast elements, the crane will raise 34t at the end of a 30m jib in two-fall reeving.
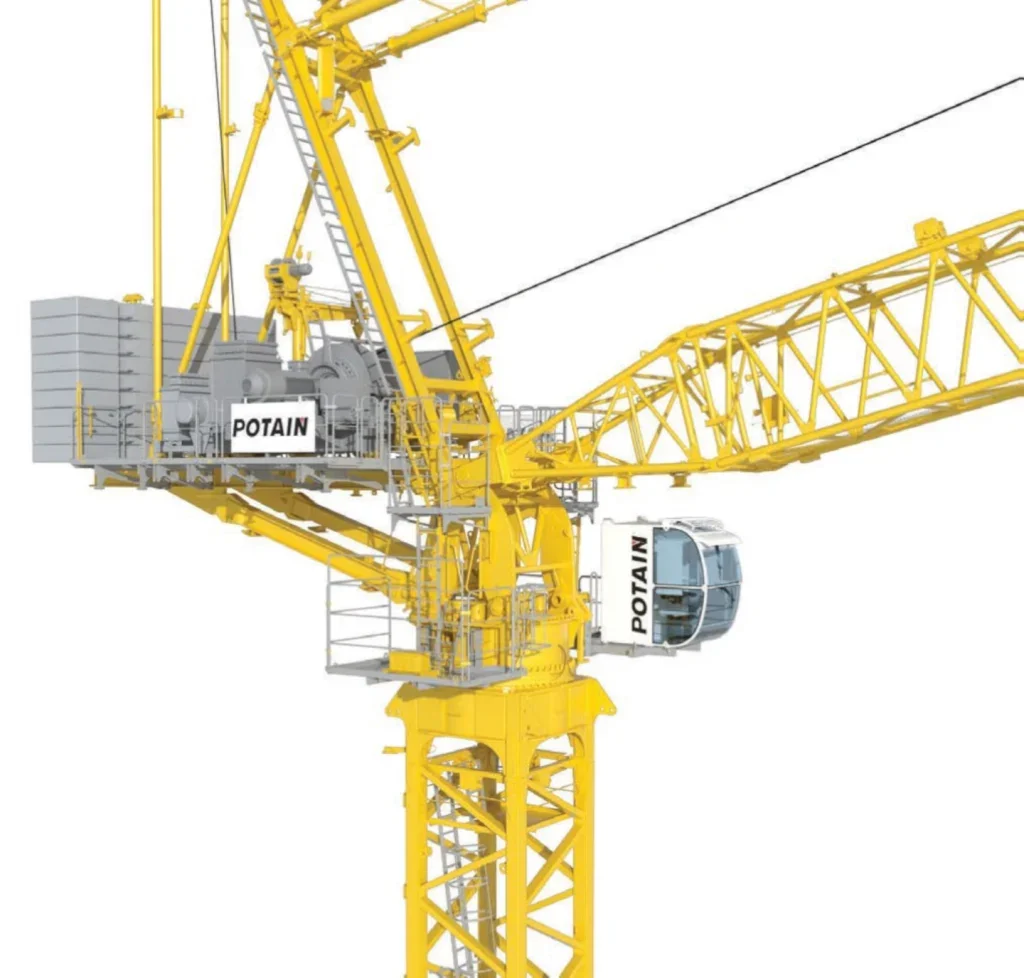
These strong lifting duties necessitated a new and precise (and rapid) hoist winch. The 280 LVFC 213 can accommodate up to 831m of rope and has a 212 kW motor, producing line speeds from 62m/min with a 6.9t load in three-fall reeving to 185m/min with a 2.3t payload in single fall. There is a power control option that links to the hoist and other mechanisms and enables the crane to operate with lower power for greater efficiency. This option is particularly well-suited to the early stages of a project when less heavy lifting is required. The 110 kWrated 150 VVFC 90 luffing hoist can raise the jib from its minimum to maximum angle in just two minutes and 20 seconds.
CONTROL IS SPEED
In January 2025 Terex also introduced a new luffing jib tower crane. The design emphasis of the CTL 702-32 is on control, safety, and efficiency. At its core is the philosophy that control is speed. Every movement of the crane is precise and swift.

“The more precise the control, the safer and smoother the operation, minimising downtime and maximising efficiency,” says Angelo Cosmo, product manager for Terex Tower Cranes. “We embedded this philosophy in the design and functionality of the crane to provide a more seamless experience for operators and crews alike.”
The CTL 702-32 has a 70m jib length; the maximum lifting capacity of 32t is available up to 28m of jib. At the full 70m jib it offers a lifting capacity up to six tonnes. Its free-standing height, says Terex, is highly competitive to give versatility for high-rise and large-scale projects.
The luffing motor is electric and powerful so that the CTL 702-32 can deliver speed as well as reliability.
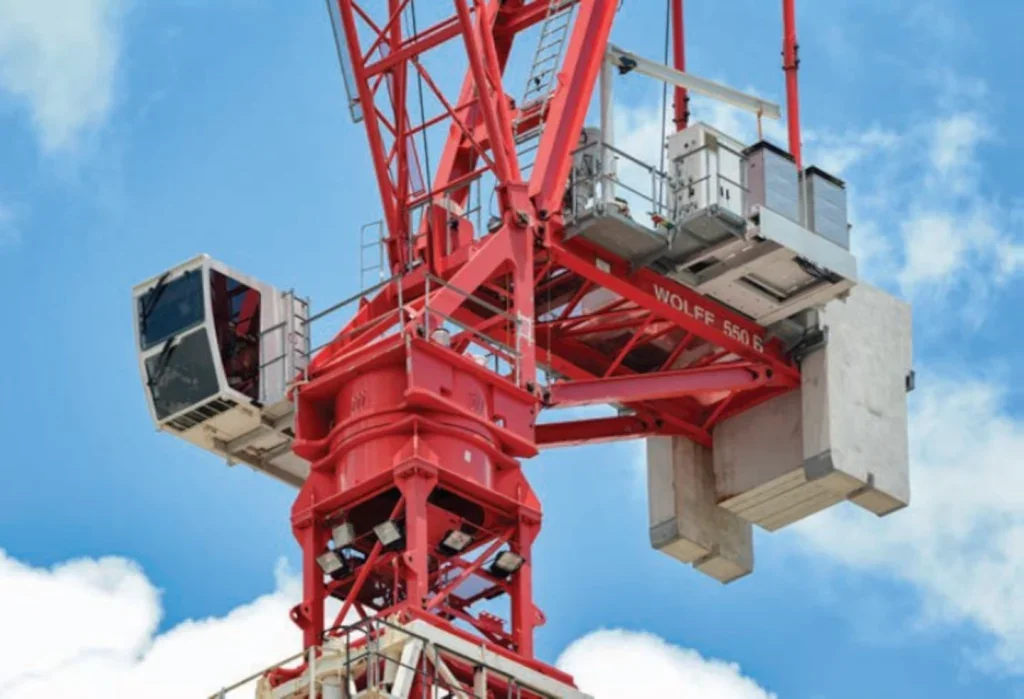
The crane features a slack rope system designed to provide a smooth, uninterrupted lifting process by preventing slack rope conditions that could compromise crane stability and load security.
We have mentioned precision and control. The CTL 702-32 aims to deliver this through its brand-new T-Line system: during jib luffing it ensures a consistent load height is maintained. T-Torque inverter technology provides torque control for precise and operator-adjustable crane slewing. Together these tools allow operators to accurately control and fine-tune the crane’s movements to precisely place loads.
It also makes the crane suitable for a wide range of complex lifting tasks.
The control ethos extends to the erection and dismantling process of the CTL 702-32, which has been significantly improved. Streamlined procedures include standardised pins and bolts and smart assisted assembly solutions. Fewer tools are required and the crane is quicker to assemble and dismantle, reducing on-site time. The design optimises the use of connectors, making maintenance simpler and more efficient by reducing the number of cables and connectors that need to be managed.
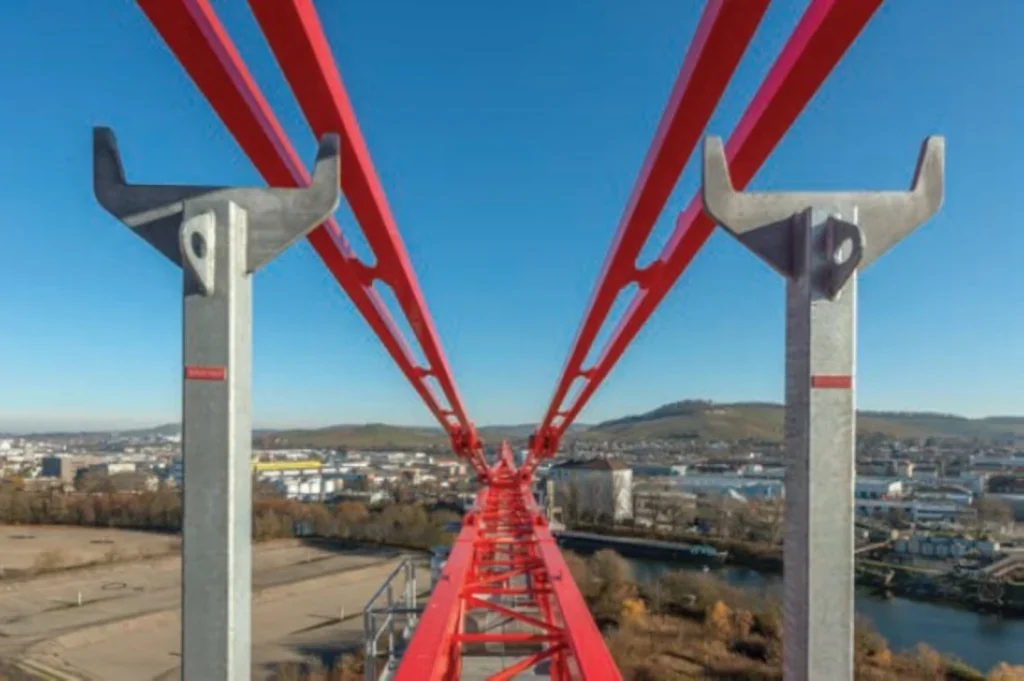
The crane’s main assembly is completed on the ground, further improving safety and ease of setup.
“Our goal is to deliver not only cutting-edge technology but also a real solution to the challenges faced by construction teams on the ground,” says Lee Maynard, global sales director, Terex Tower Cranes. “The CTL 702-32 exemplifies our dedication to providing the highest level of control, which we believe enhances safety and efficiency.”
“Every feature – from the advanced slack rope system to the precision torque control and faster assembly process – has been meticulously designed with the end user in mind,” added Cosmo.
FLAT-TOP FOR GCC
Raimondi also introduced a new tower crane, the T577, though this is a flat-top rather than a luffer. The launch took place at the Big 5 Construct Saudi exhibition, which took place in Riyadh, Saudi Arabia in February.
It is another large crane – the largest, in fact, in the Raimondi portfolio – and its introduction has a similar rationale. It aims to support the international – and particularly the Middle Eastern – increase in demand for machines with greater lifting capacities combined with high efficiency, precision, and ease of operations.
“We launched during Big5 Construct in Riyadh to allow our regional clients first-look at the specifications, as this crane is designed to support large infrastructure projects – specifically those in Saudi and the wider Gulf Cooperation Council (GCC),” says group CEO Luigi Maggioni.
Wael Hasan, general manager of Raimondi Middle East, adds: “High-capacity flat-tops remain in high demand in the GCC. This is particularly so in Saudi Arabia where developers prioritise topless tower cranes with 24-tonne capacity and above as essential for large-scale projects. The increasing use of precast and steel structures, especially in fast-track projects, is further driving demand for efficient lifting solutions shaping the region’s construction landscape.”
The new flat-top is part of the T series. It has a maximum jib length of 80m and a tip load of 3.14t in Ultralift mode. Maximum lifting capacity is 24t in four falls configuration. Ten different jib length combinations are possible, from 80m to 36m; the last three configurations offer shortened jibs and counter-jibs which give improved crane stability. This, with the enhanced versatility in tower configurations, allows for greater flexibility in terms of freestanding heights and can satisfy a broad spectrum of jobsite requirements.
Maximum lifting speed is 21.88m/min with 110kW hoisting gear; drum capacity is 1,030m; these again are designed with large-scale development jobsites in mind. The hoisting winch is fitted with an emergency hydraulic brake to further enhance safety.
Like other cranes in the series the T577 is equipped with Raimondi’s ConCore control system. Electronic sensors combine with dual control, which allows for swifter commissioning, precise calibrations, and instant troubleshooting during operations. The effect is that site downtime is minimised.
CONTROL AND FLEXIBILITY
Control also features heavily in new offerings from Wolffkran. At the recent Bauma it launched the Wolff 550 B luffing jib tower crane which fits into the company’s portfolio between the Wolff 355 B and the Wolff 630 B.
The Wolff 550 B is powerful, has a high lifting capacity, and offers flexibility. The crane has a hook path of 920m in singlefall or 460m (two-fall), and a lifting speed of up to 200m per minute.
It comes as standard with a 2.3m tower connection. This allows freestanding heights of nearly 52m.
When mounted on a 2.9m tower, though, it can reach up to 82.2m without additional support, making it an excellent choice for high-rise projects. And the Wolff 550 B is compatible with Wolffkran’s KSH 23 internal climbing frame, enabling the crane to climb nearly 27m in a single phase – significantly more than the 15.5m achieved by the standard climbing system. The KSH 23 reduces time considerably and lowers costs.
Initially the Wolff 550 B is being launched with a 110-kW hoist winch, giving a maximum lifting capacity of 30t in two-fall operation and 15t in single-fall mode. At the tip of its maximum 65m jib it can lift five tonnes.
“These lifting capacities are market-leading in this crane class,” says Mohamed Abouelezz, Wolffkran’s head of business development and product management. “By the end of the year, we’ll be raising the bar even further by offering the 550 B with a more powerful hoist winch, with which the luffing jib crane can lift up to 36t in two-fall operation.
“Additionally, there will be a US version with a 132-kW hoist winch.”
Adding to its suitability for highrise construction is the Flex Cab cabin, which can be mounted on either the right or left side of the crane. It was previously available only as a special customer request but is now standard equipment on the Wolff 550 B.
Being able to select which side the cab is mounted simplifies construction site planning and is particularly beneficial for cranes that need to be climbed down after construction.
The new luffing jib crane will be available for order starting in June and is expected to be launched in Europe, the US, and the Middle East later this year.
Wolffkran also showed another new tower crane at Bauma: the Wolff 8095 Compact. It is the company’s first trolley jib crane in the 900mt class.
It comes in two variants and a key feature is its automatically couplable double trolley.
Although high capacity, the crane is compact – making it well-suited to city centre work. “Its tower top section is about six meters shorter than the crossjib version, which makes it very compact and economical,” says Dr Abouelezz.
The two-fall model Wolff 8095.25 has a maximum lifting capacity of 25t and a tip load capacity of 10.5t (with Wolff Boost at an 80m jib length); the convertible two- and four-fall model Wolff 8095.40 has a double, automatically couplable, and separable trolley.
In four-fall operation, the crane can lift up to 40t with the double trolley and still achieve a lifting capacity of 7.8t at the tip at maximum jib length (or 8.6t if using Wolff Boost).
If a higher tip load capacity is needed the trolley can be split at the push of a button. The advantage is that crane personnel no longer have to climb onto the jib to manually separate the trolley.
In two-fall operation with a single trolley the Wolff 8095.40 achieves a tip load capacity of 9.4t (10.3t with Wolff Boost).
The high capacity is due not only to the lighter individual weights of the separable trolley but also to the design of the first three jib parts as a four-chord instead of a three-chord version.
“This optimises force transmission in the jib and makes individual components lighter, enabling significantly higher lifting capacity than with a three-chord design,” explains project manager Markus Richter.
The compact tower top means that multiple cranes can be positioned close together while keeping the overall height of the cranes low.
A hoist rope support on the jib reduces rope sag from seven metres to just 1.5m, minimising the risk of collision with another crane’s hoist rope while slewing.
The jib length can be adjusted in five-metre increments between 30m and 80m.
The crane features a tower connection for the 2.90 x 2.90m TV 29 tower element, which, when combined with the next larger Wolff tower element TV 33, enables freestanding tower heights of up to 100m – ideal for high-rise prefabricated structures where tieins are not possible.
The above examples show how the latest generation of cranes are engineered for the realities of high-rise construction, with each crane model demonstrating advancements that directly respond to the evolving needs of builders working at height.
These cranes aren’t just construction tools – they’re really strategic enablers of vertical growth, helping redefine what’s possible in the skylines of tomorrow.
ELEVATING AND INNOVATING IN DUBAI
In Dubai, UAE, Raimondi Middle East has marked a region-wide milestone by deploying the highest-climbed luffing jib crane to date. A Raimondi LR213 has been operating, with a 50m jib and a tip load of 3.30t, at a remarkable height of 322m. It is constructing a 75-storey premium residential building.
The confined jobsite location, coupled with intricate technical challenges and contractor requirements, demanded a precision approach for machine deployment. Tasked with replacing a previously installed crane after the building had already reached a height of 100m, the Raimondi team faced the complexity of working with a pre-existing foundation.
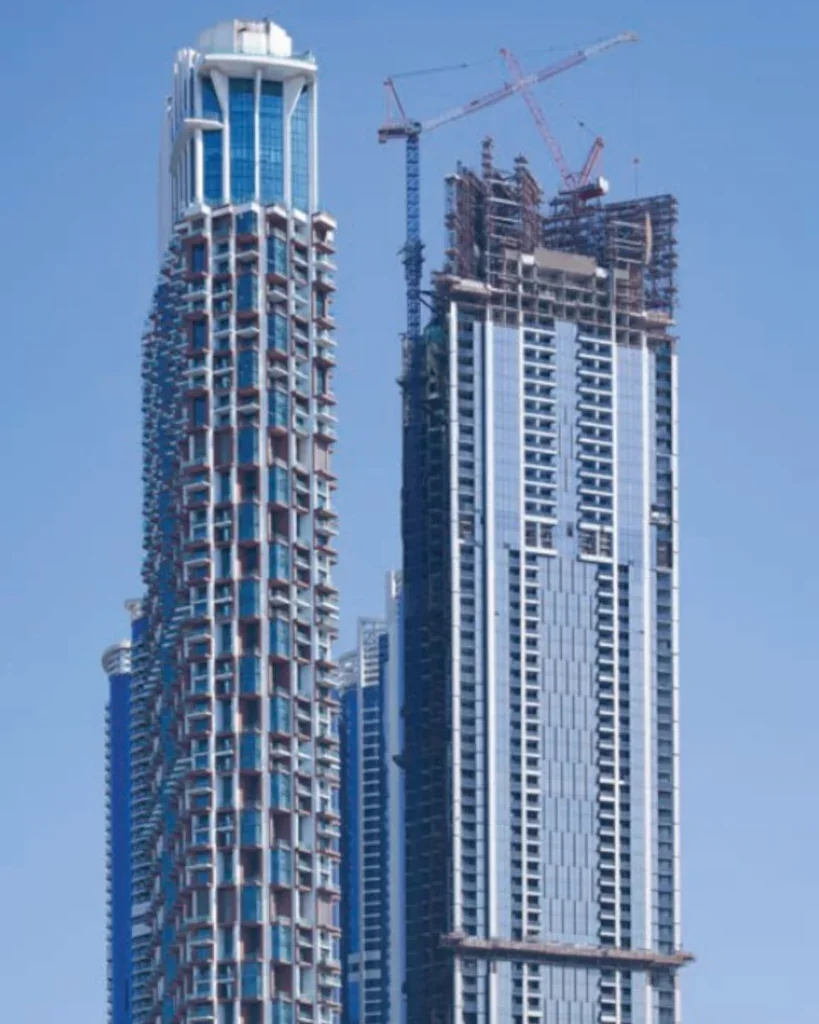
That foundation imposed restrictions on base loads, due to the existing raft and its maximum allowable limits.
Typically, crane foundations are designed based on reaction forces provided by the crane manufacturer; in this case, Raimondi’s engineers had to reverse the process, adapting the crane’s setup to comply with predetermined limits.
“To achieve this, we utilised a 6×6 base and progressively removed ballast blocks at each climbing stage, ensuring the base reaction remained within the studied allowable load limits. This adjustment was critical for maintaining stability while adhering to the site’s structural limitations,” explains Wael Hasan, general manager of Raimondi Middle East.
In addition, to fulfil client requirements and project specifications, the Raimondi Applications Department redesigned the load curve to accommodate lifting needs at a final height exceeding 300m.
Structurally, the crane was assembled using GR5S mast elements, incorporating two longer 11.8m sections and 100 smaller 2.95m segments. To stabilise the crane at its towering height, 12 bracings were installed.
One of the most challenging aspects of the deployment involved collar positioning. Site-specific requirements necessitated several revisions to collar placement, each involving extensive iterative calculations and detailed adjustments. This meticulous process required significant engineering expertise and many hours of precision work.
With dismantling procedures expected to commence in the coming weeks, Raimondi Middle East’s operations team has planned the jack-down of the LR213-14t to 50m, after which the crane will be fully removed with the use of a mobile crane.