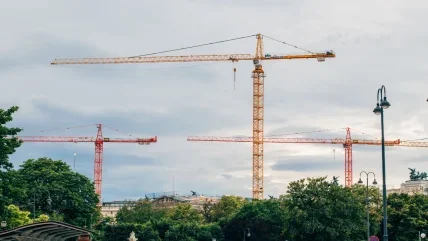
Tower cranes, in one form or another, have been building our world now for around 120-years. Of course other types of crane, particularly mobile cranes, have also made very substantial contributions but there can be no doubt that tower cranes have dominated, and since the mid-twentieth century become an increasingly significant player. According to Chortsey Barr Associates analysis, over the years tower cranes have been manufactured in some 40 countries by more than 400 companies. The number of units produced and sold since the early 1900s is basically incalculable but most certainly runs into the millions.
Predictably, the tower crane industry and its markets were quite slow to develop. Technical challenges, principally concerning safety and stability, have remained major concerns to both potential buyers and crane manufacturers.
By 1920 there were already over a dozen European manufacturers, the majority based in Germany, plus France and the UK.
There was limited industry and market expansion during the depressed 1930s and the WWII years when the munitions manufacture took precedence. Much manufacturing capacity was destroyed by bombing during the war but revived quite quickly.
POST-WAR BOOM
The post-war rebuilding boom that enveloped most of Europe propelled a great boom in tower crane production with over 30 new manufacturers entering the market, including around a dozen German companies, most notably Liebherr, as well as Potain, a strong group of French companies, plus numerous new Italian manufacturers.
The internationalisation of the production of tower cranes also extended to new markets as local companies sought to acquire the necessary technology via licensing agreements with established makers. Amongst these were Fritjof Berg Kroll’s company based in Lynge, Denmark, who acquired the domestic sales rights to the Swedish Linden line, while in Southern Italy, Edilmac, based in Rome, acquired tower crane technology from France’s Pierre Joseph Pingon. Indeed during the 1950s and 1960s over 70 new European companies joined the ranks of tower crane producers, most of them focussed on small ‘fast-erecting’ (self-erecting) cranes primarily for residential construction.
Even as competition intensified and the weaker companies were thinned out, the technology advanced thus attracting new companies to join the business. In addition to increasing lifting capacity and reach, speed and ease of erection and handling became of increased importance.
TURNING POINT
Until the turn of the 21st century the tower crane, in all its varieties, was a ‘European’ crane – predominantly designed and manufactured to meet European building needs. It was the brick, block and concrete two-and-three storey types of European residential construction that defined the reach and capacity specification requirements of the small, fast-erecting tower cranes largely-built by the leading French, Italian and German crane manufacturers since the 1940s.
Certainly, some ‘off-shoots’ such as tower versions of lattice boom mobile cranes took root in the Americas and Japan and found markets globally, but, compared to purpose-designed tower cranes their production numbers remained relatively limited and, in fact, were never a challenger for mass urban building construction.
However, over the past 20 years, the landscape has inexorably changed. As seen in our table of statistics, this business that for so many years remained largely the domicile of European manufacturers, is now increasingly dominated by China. Fact. It is not that the traditional French, German and Italian market leaders have necessarily receded but rather that on the basis their huge domestic market and burgeoning international sales, the Chinese have grown.
DOMESTIC DEMAND
By the early 1960s within China’s financially-restrained and tightly-structured manufacturing sector, tower cranes were being manufactured by only a handful of companies – several of which would ultimately become dominant players. In old and often-unsuitable factories, cranes were being designed and manufactured without the benefit of modern technical aids and machine tools. Such factories were massively over-manned and often cramped for space. But, even then there was a clear plan.
Naturally in those days, domestic Chinese demand for tower cranes was extremely limited with indigenous production offering very limited reach and capacity. In 1959 just seven cranes were produced – rising in the early 1960s to an average ranging up to 20 cranes per year.
Amongst the first manufacturers were Sichuan Construction Machinery (SCM), Shanghai Construction Machinery Co., Fushun Construction Machinery, Beijing Building Machinery Plant, Shanghai Construction Machinery Plant and Harbin Construction Machinery Plant. Most of these enterprises built cranes of just two to six tonnes capacity although the Beijing plant built cranes of up to 16 tonnes capacity. But even then the Chinese were already looking overseas with Fushun exhibiting at the 1955 Leipzig Fair in East Germany. However, significantly, in 1957 those pioneers were joined by what would become China’s dominant maker of cranes and construction machinery – XCMG – who that year built their first saddle jib tower crane.
TECHNOLOGY TRANSFER
By the end of the 1960s these Chinese manufacturers had produced a total of some 900 tower cranes primarily ‘based-on’ the Potain designs.
For larger tower cranes offering greater reach, China was totally-dependent on imports. Even by then in China the name of Potain was widely-recognised but economic restraints and the international valuation of the Chinese currency made all imports very-expensive.
Following the sale of six Potain cranes in 1979, the French organised a mission of leading construction companies that also included Potain representatives led by Pierre Perrin, deputy director of operations and director of international development.
The trade links established during that mission nurtured further contact and, following the supply of another six Potains to Beijing in 1982, negotiations for the local manufacture of Potain tower cranes were initiated by the Chinese. After several meetings, on June 6th 1984, Potain signed a technology transfer agreement with the China National Construction Machinery Corp. That agreement 84MGS161015CF licensed the local manufacture of two models of Potain saddle-jib tower crane – the Potain FO/23B of 10t capacity @ 14.5m and 2.3t @ 50m jib tip and the Potain H3/36B rated 12t @ 21.7m and 3.6t @ 60m jib tip would ultimately become the bedrock of the Chinese tower crane industry.
Three Chinese enterprises were nominated as manufacturers: Beijing Building Machinery Works, Shenyang Building Machinery Co. Ltd, and with Sichuan Construction Machinery Group (SCM) in Chengdu. However, within a few years, cranes seemingly-based on these designs were being manufactured by numerous companies all over China.
Although from the early days Potain was extremely well-placed, by no means did they have the Chinese market all to themselves. The late 1960s and the 1970s were economically challenging for China with several years of negative growth. Even so, other entrepreneurial European manufacturers including Peiner, Kroll and Italy’s Alfa and Milan-based Simma were active in China – the latter selling 200 saddle-jib cranes. Nevertheless by the 1980s Potain’s ‘Topkit’ trademark was being widely ‘used’ across China and had come to represent the hallmark of quality and technology. By 1980 annual Chinese tower crane production had reached around 1,000 tower cranes, climbing to over 1,500 by 1986 before falling back to around 1,000 in 1990.
In 1985 a delegation of 27 Chinese visited Potain in France to study the designs and manufacturing techniques of the world’s leading producer. Potain also began delivering component kits and spare parts to China. That year the first ten Potain tower cranes were built at plants in Beijing, Shenyang and Chengde.
POTAIN LICENCE PROGRAMME
Starting in the 1970s Potain developed an overseas manufacturing licence programme as a reaction to diminished sales opportunities in its main European markets where local competitors had emerged and were flourishing.
The programme was seen as a means to opening-up remote markets as well as markets protected by tariff or regulatory barriers. Typically in these ‘emerging’ markets the demand was for small cranes and the Potain FO/23B was a natural candidate.
Within a well-supported plan such agreements, typically of five-years duration, were offered under strict terms and with clearly defined phases. Companies entering license contracts gained access to Potain technology in a series of steps such as (Phase I: Tower and jib; Phase II: counter-jib and cathead or A Frame; Phase III: Crane base; and Phase IV telescoping accessories). The other more challenging elements (hoists, slew systems, trolleys, travel systems, cab, electrical switchboards and controls) were generally not automatically included in the agreements.
Agreements were signed with Noe Pereira, a Portuguese manufacturer (1972), and with manufacturing companies in the former Yugoslavia and Iran (1974), Poland (1975), Venezuela, Argentina and South Korea (1976), Turkey (1979), Egypt and Singapore (1980), Mexico and Morocco (1981) and India (1983).
The Korean agreement was with Hyundai Heavy Industries which produced two top-slewing and one bottom slewing model and under which Hyundai produced a total of 97 top-slewing and 11 bottom-slewing cranes. The Singaporean licensee produced three different models of top-slewing cranes, making a total of 80 units until 1985. Such was the international reach and success of their international activities that by the early-to-mid 1980s some 70% of Potain cranes were being manufactured outside of France. Such deals were also pursued by other French manufacturers. Braud & Faucheax (later Manitou) licensed its line of self-erectors to the Algerian state-owned enterprise ENMTP while on the other side of the world, in 1959 Pingon Brasil, in cooperation with Industria Villares, began building its tower cranes in Sao Paulo and would eventually manufacture over 700 units.
Potain’s global business strategy also included the acquisition of competitors such as Cadillon, the French self-erector manufacturer in 1968, followed by Milan-based Simma in which Potain had invested a 51% share in 1972 and completed the acquisition in 1988.
Meanwhile, in 1982, Potain acquired its domestic competitor Richier. Richier had a line of larger-sized saddle jibs and had developed a strong sales base with the French Government and particularly the Navy. In addition, they developed a very strong relationship with the powerful UK dealer, Babcock which manufactured large Weitz and later Richier saddle jib cranes at its plant in Dalmuir, Scotland. For many years Babcock enjoyed broad international success with its British-built French cranes that they had modified to employ British electrics and components to meet the needs of far-flung export markets.
Potain then enhanced its dominant control of the French tower crane business in 1984 when it acquired BPR – the amalgam of Boilot, Pingnon and Richier – formed in 1977. Potain’s Portuguese licensee, Noe Pereira, was acquired in 1989 and over time would be developed as a major element in the company’s international manufacturing operations. In 1990 the Italian self-erector manufacturer Fergru was also acquired.
The visit of a delegation of 27 Chinese to Potain’s French operations in 1985 reflected the strengthening of Potain’s relationships with China. In 1988 Potain curtailed further licensing activities in China. That year the new 39 storey China World Trade Center in Beijing was built with the help of two Potain 85/20 cranes used to skip concrete and lift steel beams. The construction of that prestigious project involved a total of 12 Potain cranes including two locally-made ten-tonne capacity FO/23B (2.3t x 60m) and one locally-made eight-tonne capacity fast-erector GTMR 360B now in full-scale production at licensees in Beijing and Shenyang.
Certainly the number of Chinese manufacturers – mostly small companies – continued to expand. While most domestic production remained focussed on small, low-capacity saddle jib cranes, China National Building Materials (Group) Co., (CNBM) Beijing, a state-owned organisation, started building a range of tower cranes of various sizes. CNBM product brands included CMAX for their QYZ 80 of 10t capacity with 80m jib and 1250tm capacity.
The 1990s proved to be a pivotal period for the Chinese tower crane industry. Production levels rapidly increased to a range of 9-11,000 units per annum. Perhaps most significantly three domestic enterprises that would become world-famous emerged. The company that would rise to become China’s largest crane and construction machinery maker – XCMG – had its beginnings in 1943 and became established as Xuzhou Construction Machinery Group in 1985 adding tower cranes to its broad product line. Further west, in Hunan Province, already in 1989 Liang Wengen with three friends (Tang Xiuguo, Mao Zhongwu and Yuan Jinhua) with just RMB 60,000 had sowed the seeds that in September 1991 would mature into Sany Heavy Industries based in Changsha. Close-by and just a few years later, on September 28th 1992, Changsha Construction Machinery Research Industry was founded by Zhan Chunxin who with seven colleagues took a loan of RMB 500,000 that would lead to the establishment of Zoomlion. And in the North Eastern province of Liaoning in 1996, Fushun Yongmao was established and soon set its sights on foreign markets.
Government pressure to secure ‘hard currency’ via exports has been a factor since China commenced its industrial transformation and the first tower crane exports were achieved as early as the late 1950s. Initially target markets were often countries of similar political-persuasion but over time the net was spread across Asia, Africa and the Middle East. By the early 1990s China was exporting as many as 300 tower cranes per year valued at RMB 10-15m/year.
As the range of sizes and capacity of domestically-produced cranes expanded, tower crane imports began to decline falling from 70-100 per year to as few as 20 per year by 2000. As the size of the domestic market expanded and domestic competition increased in intensity and quality, it became clear that, except for very large or specialized units, the viability of importing cranes from Europe had run its course.
In 1995 Potain established a 64:36 manufacturing joint-venture agreement with a small Chinese tower crane maker named Linhong based in Zhangjiagang, west of Shanghai. It was a bold move that led to the 100% acquisition of the business in 2000 and the development of a new 56,000m2 state-of-the-art facility that opened in 2006.
Meanwhile XCMG had gained access to Liebherr crane technology. All the time, several other Chinese companies were becoming active in the tower crane field. By now, new entrants included Sichuan Qiangli Construction Machinery Co., and Shandong Baimai Construction Machinery.
Product diversification was also developing. In 1995, Shenyang Building Machinery Co (later renamed Shenyang Sanyo SYM Building Machinery) had licensed the production of the 20-tonne capacity/70m reach Potain K 50/50; followed in 1996 by SYM licensing Potain luffing boom tower cranes and in 1999 introducing its first flat top. The range of domestically-produced luffing boom tower cranes available expanded in 1998 when Jianglu Heavy Machinery Tech Co. introduced the 240tm QTD 160. The level of technology was also advancing with Zoomlion introduced its first cranes with frequency conversion in 1996. That year the Government solicited bids for five super-size cranes with concrete pouring attachments for use on the Three Gorges hydro-electric power project (resulting in the delivery of 64-tonne capacity Potain MD 2200s).
UNDER THE RADAR
To an extent, Chinese exports of tower cranes initially flew ‘under the radar’. Once erected, the identification of brands and models becomes more challenging to all but the knowledgeable ‘eye’.
Chinese tower cranes began to appear in ‘western’ markets around 2003-6, offered with great prices and tempting incentives.
In February 2003 the first known Chinese tower crane – a Yongmao – was imported to Belgium by the dealer Jin Long. Then in October the first Yongmao STT 293-12 was erected at Imperial Wharf, London by its new owners/dealer – London Tower Cranes. The pace quickened further during the 2000s and with the emergence of the Belt & Road Initiative, export-reach accelerated. From the outset, the leading Chinese manufacturers had recognised the merits of exhibiting at Europe’s trade shows such as Bauma, Intermat and Vertikal Days. Slowly, at first, the sales started.
In 2005 Zoomlion built 300 saddle jib tower cranes of up to 210tm capacity at its Changsha plant which, at the time, employed some 460 people. It was a good year for Zoomlion, thanks mainly to a record order for 79 six-tonne capacity models TC 5616 and TC 5015 cranes placed on a government-to-government deal for a housing project in Angola.
That year Zoomlion also expanded its product line with three new models: the TC 5013, TC 5518, and its largest crane to-date, the 13-tonne capacity TC7030B, offering 3.1t capacity on the max 70m jib.
Only a handful of Chinese companies manufacture a few small self-erecting tower cranes, meaning that to date, the Chinese do not compete for the bulk of European market demand. Certainly many Chinese companies have added luffing boom tower cranes but with lower production volumes, these are less of a threat to Europe’s traditional manufacturers. Over the past decade the Chinese have also added flat top tower cranes to their lines but, being more expensive, these are less appealing to their domestic market. Most recently the leading Chinese tower crane producers have sought to out-do each other with ever larger cranes.
EXPORT ANALYSIS
Between 2018 and 2019 exports of tower cranes (to product code 842620) increased over 25% from $321 million to $402 million.
During the same period exports by European manufacturer nations declined. Germany remained the leading European manufacturer and exporter but 2019 exports declined to $288m versus $309m in 2018. Italy is the second largest European exporter with $266m in 2019 versus $302m in 2018. Spain is the fourth ranked producer with $199m in 2019, down from $218m in 2018, while France exported just $140m in 2019 versus $185m the previous year. Total reported worldwide exports declined slightly to $1.75 billion in 2019 versus $1.8 billion the previous year.
From a near-term low of just over 1,500 in 2009, Chinese manufacturers reported tower crane exports peaking at almost 4,000 units in 2015, declining to approx. 2,500 units in subsequent years. In 2020 total global exports of tower crane suffered a decline to approx. $1.3 billion ($1.75 billion 2019) – undoubtedly impacted by the global pandemic. China’s exports peaked in 2015 – reaching almost $450m versus $320m in 2010. Thanks in large part to its strong domestic industry led by Liebherr and Wolff, over the last decade Germany has remained the dominant European exporter nation. Similarly Italy has maintained its position as Europe’s third largest export supplier, well-supported by Terex-Comedil, Potain Italia, Cibin, Catteneo, FM Gru, FB, Raimondi and others.
Even as Spain’s tower crane exports declined by around 9% to just under $200m in 2019, the impressive product developments by their strong group of manufacturers (Liebherr, Comansa, Saez and Jaso) has continued to favourably-impact export markets. While domestic production and exports of French cranes may appear to have declined ($140m in 2019) this distorts the global picture of Potain which has enjoyed substantial international success with its broadened line of Chinese, Italian and Indian-built cranes.
Turning back to China, thanks largely to their Belt & Road Initiative, Chinese tower crane producers are winning substantial business in markets across Asia and the Middle East. Estimating the precise volumes is challenging as in several cases, these cranes are exported in the hands of Chinese contractors rather than sold directly by manufacturers. Therefore, reported export volumes can sometimes be significantly under-stated and possibly reported by their manufacturers as domestic sales. Nevertheless, Korea was reported as the leading export destination in 2019 ($34m), followed by the UAE and Singapore ($27.6m and $27.2m respectively). Other SE Asian markets featuring strongly included Philippines, Vietnam, Malaysia, Thailand and Indonesia.
The fast-growing Indian market registered a strong showing with $12.5m – augmented by the domestic production by Potain, Liebherr, Electromech-Zoomlion, Schwing-Stetter XCMG and a growing list of others. Meanwhile the Chinese reported export sales of over US$9m to Australia. Notably, sales to the US only totalled $1.9m (undoubtedly including Chinese Manitowoc/Potain cranes. The only European nation to make the list of significant buyers of Chinese tower cranes was Finland – at #31 a total valued at $1.23m.