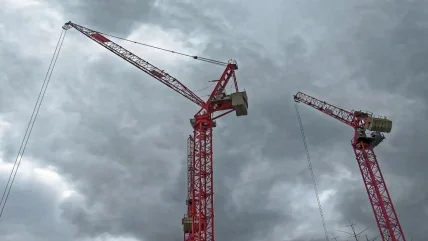
There are several reasons for the recent trend towards using luffing jib cranes on inner city sites. Cranes may not be allowed to overslew, even with no load; nearby areas may be banned due to safety reasons, like railways and high voltage power lines. This can make it hard to find a suitable set up area for a conventional hammerhead crane.
Luffing jib cranes which can raise their boom for minimum out of service radius are also the first choice when serving cramped construction sites surrounded by high rise buildings. Furthermore, when a number of hooks are needed to raise a super high tower (for example) the working space for each tower crane is restricted, and a luffing jib design appreciated in order to avoid collision with neighbour cranes.
When the top slewing European luffing jib climbing crane was rediscovered in the late 1980s, the main design aim was to provide a crane which could raise its boom to about 65° in the out-of-service position. When free slewing under wind conditions— weathervaning—the counterweight radius could remain relatively long, measuring 8–12m in the 160–400tm crane class size. Even so, this was an improvement on saddle jib crane designs, where the boom length remained the same no matter at what radius the crane is working.
However, as users saw the benefits of the luffing jib principle for narrow site conditions, demand rose for more compact designs.
The need for a safe steeper outof- service position, and a small tail radius, became evident to cope with today’s cramped city construction site conditions.
Shrinking the tail
The development of luffing jib climbing cranes with small tail radius can be traced back to 1958 when Liebherr developed the widely used HB series of “universal” tower cranes. For example, the 50HB provided just a tail radius of 4.5m and the hydraulically moved 30m boom could be raised to just 3.5m minimum radius. Still amazing in comparison to today hydraulic luffers is the fast derricking speed of 50 seconds of the 4t capacity crane.
For years the hydraulic luffing mechanism was abandoned in the European construction industry after the Liebherr HB series ceased production. One reason may have been the need for specialized skilled service personnel; another the possible leaks of hydraulic systems, which risked both problems of environmental pollution and the risk of uncontrolled boom lowering when the crane is out of service.
With the growing application of luffing jib cranes under cramped site conditions the question arose how to develop more compact cranes. One way is to minimize the rear radius. For example, the original Wolff Hydro had a 10.3m rear radius while the last generation of the 320B reduced this to 7.2m.
In many cases manufacturers of modern rope luffers with fixed ballast arrangement offer a short tail radius version by changing from standard concrete ballast versions into more compact steel ballast versions of the same crane type. One recent example is the Liebherr 710HC-L with 9.3m back radius when concrete ballast is used, and only 7.9m when the ballast is made of steel. The US market in particular looks for high capacity luffers with short tail radius. In response to this, Wolffkran developed a US-Version for its 700B with 7.4m tail radius, in contrast to the standard version with 8.9m counter radius.
For small to medium sized luffers the trend of short counter jibs is as well obvious, especially in Asia. One example is the Zoomlion L80-6S with a maximum capacity of 6t and a tip load of 1.5t at 40m radius. The new generation rope luffing crane has a tail radius of just 4.5m.
In recent years Japan has been home to the shortest available luffing jib crane machinery decks. For example, the Kitagawa JCL105SK is a city luffing jib crane free standing on a 41.6m high tower with 1.17m square mast sections and 2.5t capacity at 30m radius with just a 3.8m counter radius. Maximum capacity is 8t up to 11m radius.
The newest addition to these Japanese compact luffers is the JCL055SK with an all new strengthened tower system just 0.85m x 0.85m wide. In 35.3m free standing mode this climbing luffing jib crane provides 1.2t tip load at 31m radius while the counter radius is restricted to just 2.6m.
Safe steep slewing
While the influence of a short counter jib radius may gain importance for in- and out-of-service conditions, most important is the safe out-of-service condition for luffing jib. The minimum out-ofservice radius determined by the jib position of a free slewing luffing jib crane is not only related to its jib length but also to the chosen crane design. The radius needed declines from the conventional rope luffing jib crane with fixed ballast, to the luffing jib crane with moving ballast, to the folding jib crane type.
A special upcoming application is the customised crane installation arrangement where the jib is raised in fixed position and the crane is left in out-of-service position without the need to slew its jib into the wind. Generally movable ballast systems like the ones being used on the Jost, Potain and Terex Comedil rope luffers create pressure on the boom against wind coming from the front and therewith reduce the risk of the jib being overblown. However, such ballast features generally add to the tail radius of the crane when the boom is lowered to maximum radius in comparison to rope luffers with fixed ballast.
A luffing jib crane design with fixed ballast version can be adapted to steeper out of service position of the boom above 70° if the overall structure is rigid enough and at the A-frame separate boom stops are installed at which the jib is resting in outof- service position. In this way,
Jaso developed together with its UK representative Falcon Tower Crane Service an additional mechanical boom stop which is lowered from the A-frame when the crane is parked into out of service condition. This keeps the boom from moving into an uncontrolled steep position. In this way, for example, the out-of-service radius for the conventional rope luffing crane J180PA with 55m boom can be reduced from 20m to 11m.
Falcon Tower Crane Services technical director Nick Hurrell says, “For short jib lengths used with this system additional wind sails may be required in the jib.
A short parking radius can be essential for busy city centre jobs where multiple cranes are in use, enabling them to be positioned closer to each other. It also allows the cranes to be positioned nearer to the site boundary without oversailing adjacent property or restricted areas, giving the user more flexibility to the crane position and its impact on site.
“We also have a number of Jaso hydraulic luffing jib tower cranes, these models are the J118HPA and J168HPA with jib lengths up to 50m and maximum safe working loads of 6000kg.
These machines have a short out of service radius from as little as 7m as standard without any additional device, as well as a low electrical power requirement due to its hydraulic luffing mechanism.
ue to their popularity, we have 29 x J118HPA’s and 30 x Jaso J168HPA’s in our fleet.” Favelle Favco chooses a similar approach for its new range of luffers, which can be equipped with second boom stops on which the boom rests in a steep outof- service position. They allow variations of the minimum out-of-service radius up to the minimum outreach of the crane and have so far being used for the M220DX, M380, M390, M440 and even the massive M600 Favelle Favco luffer.
In contrast to Jaso’s design, in this case hydraulic rams are used, creating a pressure on the boom head instead of a folding down framework. The hydraulic buffers from Favco allow not only a rest of the boom in out of service position, but also help the boom to be moved out of the minimum working radius when being caught by heavy wind from the front of the crane.
When the wind blows
A typical risk for a rope luffer is the jib bending backwards over the A-frame, if it is caught by gusting winds from the front. This risk can be reduced by hydraulically operated luffing jib cranes. On a rope luffer, raising the boom angle steeper than 70° raises the risk of a lack of tension to the flying sheave block which can cause damage to the crane. On a hydraulic luffer, safety in a steep out-of-service position depends on the strength of the hydraulic ram connection to the jib as it must take both pressure and tension forces.
For the popular topless jib design, there can be severe side loading affecting the stability of the raised boom when in a 70° out-of-service position. The steeper the jib is parked, the more uncertain is the weathervaning of the crane. Most manufacturers prefer a hydraulic luffing jib design, where the counter jib with ballast moves down and narrow to the centre of the crane when the jib is raised. This feature adds to the capacity of weathervaning, especially when combined with windsails in the jib.
In some cases, the jib must be parked in an extremely steep position above 75°. This will normally be necessary to benefit from a short counterjib at the rear for crane installation. Here, special means must be added for safe out-of-service condition.
Jost has recently designed its JTL 68.4s as an answer to the Artic Raptor 84 with its unique articulated jib design. In the new design, the Jost hydraulic luffers are equipped with just a 4m short counter jib. In order to raise the boom to 4m minimum out-of-service radius it is necessary to park the crane with its counter jib leaning against the tower head. The whole crane including crane tower and base is designed in a way that is uncommon for European design principles, as the upper crane does not weathervane. On a slim 1.13m square sized tower system and 30m freestanding height, the new Jost JTL 68.4S fits in any elevator shaft. Maximum capacity is 4t, while at 35m radius 2t can be lifted. Four units have already been delivered in 2017 to London Tower Cranes. In order to cope with the limited space in the ballast frame, a mixture of steel and concrete ballast is used.
New and improved
Since 2006, Jost has developed the most comprehensive line of hydraulic luffing jib cranes, from 80tm to 300tm class.
More than two hundred JTL series cranes have so far been delivered. The Topless jib design facilitates mobile crane erection. The overall height of the load to be lifted is reduced. In addition, the jib section length can be adapted to the available hook load of the assistant crane.
But there are limits to this design. Without pendants to support the jib, bigger and heavier jib sections must be used, increasing the load to be lifted in installation. This sets a limit to the use of hydraulic luffing above a 350tm class.
The MTL220-10 developed by MTI Lux followed the main Jost design principles, but the hoisting unit is located on top of the boom head. This makes for easy hoisting rope installation at ground level, rather than besides the cabin at the slewing unit as is found on the Jost JTL series.
The trade-off is that while the MTI Lux cranes offer easier rope installation, the Jost cranes give the operator a better view of the working hoisting winch. As an upgrade of the original Jost JTL series, the new cranes are coming with two- and one-fall operation mode, in contrast to the original two- and four-part reeving. For easy installation, the improved Jost JTL models combine basic jib section, hydraulic ram and tower head in one pre-installed transport unit.
In 2014, Wolff entered the hydraulic luffing jib market with its 166B. So far about 30 units have been built, mainly for the British market. In comparison to the conventional rope luffing Wolff 100B, the out-of-service radius is reduced from 20m to 12m. Contrary to the Jost design, the hoisting winch is located on top of the boom and the comparable short counterjib is equipped with a fixed ballast frame, in contrast to the typical free swinging ballast cage used on Jost cranes.
Therefore, specially shaped concrete blocks must be used for the Wolff 166B, while in the Jost ballast cage any kind of adequate ballast blocks can be filled in. Saez chose a similar design to the Wolff 166B for its new 80-110tm hydraulic luffers, which have been developed since 2016.
Already eight units of the SLH 80 with 5t maximum capacity and 16 units of the SLH110 with 6t maximum capacity have been delivered. A larger SLH190 with 3t capacity at 50m radius is under development. In contrast to the Wolff 166B, both Saez cranes can be rigged with central jib section, hydraulic ram, and tower head section, as one erection and transport unit to speed up the installation process.
China Dahan’s new WHl2925 follows the Jost design principle with the hoisting winch located besides the cab and the ballast support frame integrated into the square sized counter jib.
In 2014 Jaso stepped into the hydraulic luffing jib market with another design principle. This time the jib is hold by pendants to reduce structural weight and luffing power consumption. The compact jib sections fit into tower segments during transportation.
After the successful launch of the J168HPA with a tip load of 2.5t at 50m radius, the smaller J118HPA followed. Providing a tip load of 1.6t at 45m radius this crane could be installed on a slim 1.18m tower system to fit into standard lift shafts with 31.6m free standing tower height. In early 2017, Potain launched the MCH 125 hydraulic luffing jib crane. According to Potain the widely used balancing counterweight designs have to be much heavier than a fixed equivalent to ensure the right level of back moment when the crane is in out of service position.
Therefore concrete ballast blocks are traditionally mounted on the back of a 7m long fixed counter jib, which also carries the hoisting winch. Maximum boom length will be 50m. The minimum out-of-service radius is said to be 13.5m at 88° jib angle. Maximum lifting capacity is 8t. At maximum 50m outreach, lifting capacity is 2t. In contrast to the conventional rope luffer it provides a shorter out of service radius and is easier to erect and dismantle thanks to its topless design. Furthermore, the hydraulics are pre-connected at the factory and therefore there is no installation need of luffing wire ropes. Hence the crane can be installed to 40m free standing height in just 6 hours.
Alternative approaches
There have been several attempts to make use of articulated luffing jib designs for the construction industry, but only one was successful in the long run according to the number of cranes being built. This was the original Tornborgs S-46 “jack knife” tower crane that has been revitalized and improved by Artic Crane AB in the form of the Raptor 84.
The system integrated design benefits of the articulated jib are horizontal load movement, twice as fast outreach variation in contrast to standard single boom cranes, and a very stable out of service condition with retracted boom. With short tail radius of just 4m and tip end capacity of 2t at 32m radius the Raptor 84 replaces perfectly the Tornborgs S-46 of the 1960s, but with up to date rigging features and inverter control system. With its 1.2m x 1.2m tower system providing 32m free standing capacity, the crane fits in standard lift shafts. Thanks to the articulated jib device minimum out of service position is just 4m. In 2017 a larger version, the Raptor 184, was launched.
While the maximum lifting capacity is raised from 4t to 8t and tip load to 4t at 36m outreach, the tail radius remains 4.5m. On 1.74m square sized tower system the crane reaches a free standing height of 42m.
With the acquisition of Vertical Transportation, the new owner City Lifting has integrated a number of Tornborgs into their rental fleet. They will be updated soon with modern inverter control systems.
Together with its 12 Raptor 84s and four Raptor 184s, City Lifting is operating the largest rental fleet of specialised articulated jib tower cranes for narrow site conditions in the world.
For small jobsites under very cramped conditions the telescopic loader crane boom installed on a mast climbing system can be a smart solution. For example, the Everdigm ELC-10015F can be mounted on a 10m free standing mast system and does not require counterweight jib. At 3m radius, the hydraulic telescopic boom luffing jib mini tower crane has 10t capacity, while at the full 21m radius still 1t can be handled.
By quick connection device the complete upper crane can be lifted off by an umbrella tower crane and relocated to another mast in the construction field. If the mini luffer is integrated into a self-climbing formwork it can be raised to the next level of construction. An internal climbing system is also available for the compact 0.88m X 0.88m modular mast system in floor climbing mode. Maximum winch capacity of the hoisting drum is 120m. Due to its outer dimensions this mini tower crane can work inside buildings under construction.