In the October 2001 issue of Cranes Today Bill Cakebread presented an overview of the development of load moment indicator systems (LMIs) on cranes during the last 70 years of lifting history. It is always interesting to study the details of another of mankind’s efforts to advance beyond the use of the spear and the club. While the development history of LMIs has been a rather amazing story, it has, at the same time merely been a response to the nearly geometrical increase in crane lifting capacity over the same period. From a maximum capacity of a few tons, to the ability to lift many thousands of tons on a single crane, the need to provide the crane operator with information to safely control this new-found power has risen proportionately. The two most basic questions which must always be answered to carry out any lifting operation safely are: 1) What does the load weigh?, and 2) Can this crane safely lift that weight? The development of the monitoring systems chronicled by Bill Cakebread represents the ongoing efforts to apply the most current technology to the search for answers to these questions.
The term ‘load moment indicator’ is a carryover from the earliest engineering jargon surrounding the development of such systems. Over the decades, this label has come to be generically applied to almost any type of load monitoring system on a crane. Most remarkably, it has clung on tenaciously in the industry lexicon in spite of the fact that it has real meaning only to relatively few engineering types. Today’s terminology of ‘load monitoring system’ or ‘capacity monitoring system’ is far more descriptive of the inherent function of these devices.
The earliest mechanical/hydraulic systems referred to by Bill Cakebread offered simplicity in the function of weighing a load but were awkward to deploy, limited in accuracy, and notoriously unreliable. These same issues remain a challenge today. Significant progress has been made in the ability to determine accurately the amount of lifting force being applied to a load on a real time basis. This progress has moved toward a better answer to ‘What does the load weigh?’ In light of this progress designers began to address the second, more difficult question of whether a particular crane can SAFELY lift the load weight which is being measured. From an incredibly simplistic viewpoint, this technology involves the use of computers to compare the pulling force being applied to a load by the crane with the allowable capacity determined for the crane by its manufacturer. The various electronic systems which now address this problem have brought the lifting industry to today’s state of the art for LMI systems.
Load and capacity monitoring system technology has in fact progressed to the point where most new cranes are supplied with some type of electronic monitoring system as standard equipment. At least one crane manufacturer has gone so far as to instruct the crane operator to rely on the crane’s computer rather than the venerable printed capacity chart which has so long been a mainstay of safe crane operation. This last move toward total reliance on electronics to direct the crane operator’s lifting efforts demands that the question of system accuracy and reliability be revisited with utmost scrutiny. It is at this point that intense polarisation of opinion abounds despite Bill Cakebread’s counsel that rumours of unreliability are mythical and outdated.
His analogy to motor car advancements is a good one and can provide an everyday comparison to which most laypeople are able to relate. It is nearly unheard of for the current generation of automotive on-board diagnostic computer controlled ignition systems (OBD2) to fail. When is the last time anyone can remember turning the key of a recent production automobile and not having it spring to life and run well under the control of a computer system which continuously adjusts fuel and spark to provide optimum engine performance in response to varying environmental conditions which are monitored by inputs from a system of sensors. Malfunctions are rare.
Is this then the reliability standard by which LMI systems should be judged and has this level of reliability yet been reached in crane systems? Bill Cakebread implies that it has not. Discussing reliability he wrote: ‘The real problem is the price that we place on safety…’ In comparing monitoring systems for cranes to electronics in the airline industry, he points out that ‘essential circuits are duplicated or triplicated, to ensure back up continuity in the event of failure’ and he goes on to say, ‘LMIs could have duplicated circuits if we were prepared to pay for them. It need not be excessively expensive and would allow continuous safe operation while providing the facility to carry out repairs at relative leisure.’
The clear message here is that systems do not currently provide the level of reliability which he feels is appropriate. Even if and when the desired ‘failsafe’ circuitry is incorporated as standard practice, this absolute most current system technology will not reach a majority of crane users for several years.
One need not look far in the crane user ranks to find ample proof that LMI systems still malfunction with frustrating frequency. As recently as 1998, the US based Specialized Carriers & Rigging Association surveyed its crane user membership on the question of accuracy and reliability experience with monitoring systems. The reported responses reflected everyday experience with a population of some 1,850 mobile cranes of varying type and age. It is reasonable to assume that monitoring systems were divided between standard crane manufacturer supplied devices and user installed units. Tabulation of the survey results showed that at least once a month 57.5% of the users experienced some sort of malfunction or observable variation between known weights and radii and the information displayed by a monitoring system. What is the crane operator to do when faced with such a situation in the framework of a statutory mandate for system use – stop the project until a repair or replacement crane can be obtained, or bypass the system and risk violating the statute? The lifting industry has been quick to embrace the safety potential of load and capacity monitoring systems on its cranes. This fact is clearly demonstrated by the robust aftermarket sales of user installed units. Unfortunately in too many cases this potential has fallen short. The frustration of electronic service problems beyond the ability of typical crane service personnel to correct is still too prevalent. While lifting operations with mobile cranes on construction sites create a certain level of inherent risk, it is difficult to compare this situation with the fate of airline passengers faced with an equipment malfunction. Nonetheless, the lives of workers are at risk. How can this situation best be addressed? A reasonable person would look for guidance to the successes of the past. Continue to refine the product. Work with users to achieve an acceptable level of accuracy and reliability, even if at greater cost. Proceed with caution in statutorily mandating devices whose manufacturers generally present prolific warnings NOT to rely solely on their system for crane operation. Human nature is inclined to believe that a government mandate carries with it the implication of functional reliability. How can such a mandate be logically justified in light of the pining of industry insiders for product reliability improvements? Bill Cakebread is dead-on to document the advances which load and capacity monitoring systems have brought to the heavy lifting industry, yet his own words reveal the fact that there is still a measure of necessary reliability to be achieved. Is it right to turn the ultimate potential of these devices into a safety minefield of statutory mandates based on our wishes for the ultimate failsafe system? History teaches that the road to hell is paved with good intentions.
Can cranes be used safely without LMI systems? They have been for decades.
Do load and capacity monitoring systems offer the potential for even greater safety? You bet! One can only hope that manufacturers and crane owners will continue to work together to advance reliability and accuracy to a level acceptable to everyone before the cold stake of government mandate is prematurely driven between them to highlight any shortcomings which may still exist.
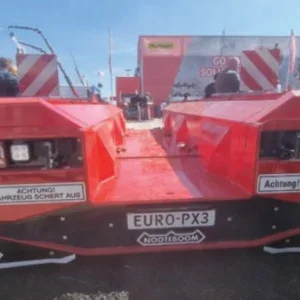