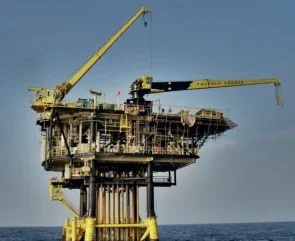
There are 12,000 oil and gas platforms dotted around the world and many of them are nearing the end of their useful life. They need to be decommissioned, and removed, and their materials recycled. The North Sea alone has more than 1,500 such installations; their average is 25-years-old. Another 1,500 oil and gas platforms in the Gulf of Mexico are more than 30-yearsold. And in the Asia-Pacific region more than 2,500 platforms will need to be decommissioned in the next decade. So says the World Economic Forum. Decommissioning is big business.
And not only in offshore energy. Infrastructure everywhere ages and needs to be replaced. Bridges, buildings, plant machinery, even cranes, become redundant and outlive their usefulness.
Removing them presents difficulties. They are old, and possibly corroded; so their strength is not known. Their weight may not be known either; original plans, even if they can be found, might allow their original weight to be calculated but years of use, say of a steel tank in a chemical plant, may have added deposits that increase its weight, or brought corrosion that reduces it; and both of those can move the centre of gravity to an extent that can only be guessed at. And in the years that have intervened since the thing was erected other structures – buildings, roads, more industrial plant – may have been put up around them, making access tight or close to impossible.
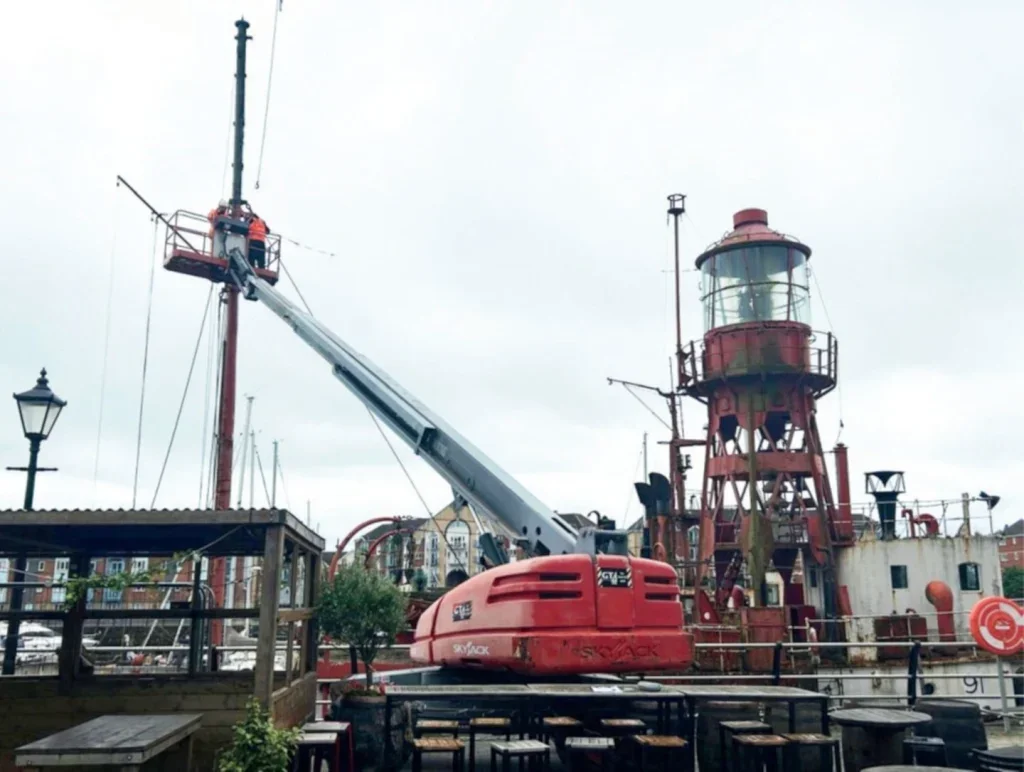
All of which makes decommissioning an art every bit as much as a science. Experience will count, even more than it does on new-build projects. Difficulties will emerge, sometimes partway through the job, that will call for ingenuity as well as expertise. And, as ever, planning is paramount.
As an example of some of the complexities involved, consider the decommissioning of an oil platform completed in August this year by Thunder Cranes. Thunder Cranes is based in Labuan, Malaysia, and specialises in lifting solutions for the offshore oilfields of Asia.
Modular rental cranes are a speciality; its rental division employs a proprietary crane technology with a unique selflifting system that allows its cranes to be rigged up on platforms without assistance. Decommissioning offshore oil platforms is a major area of its work. Such platforms have their own mounted cranes, of course, and it might seem logical to use these for lowering modules to strip the platform before removal.
But as offshore platforms near the end of their life their fixed cranes may no longer be operational or may lack sufficient lifting capacity for removing topside modules in the decommissioning stage. Hence the solution of rental cranes, temporarily installed on the rig to be decommissioned, for topside preparation works such as ‘weight shedding prior to topside removal by a heavy lift vessel.
Global energy company Chevron Thailand engaged Thunder Cranes to assist with the decommissioning preparation work on a topside installation. The requirement was to remove equipment and associated modules and installations totalling some 300 tonnes from the main deck of the platform. This weight shedding was carried out to bring the topside weight to within the heavy lift vessel’s lifting capacity for topside removal.
The ‘reverse-installation’ process consisted of isolating and disconnecting all lines connecting to equipment and disconnecting equipment skid bases from the deck plate. The equipment modules could then be lifted from the main deck to a supply vessel for later disposal or recycling.
Located on the top deck there were 14 large components weighing between 10 to 40 tonnes, as well as a number of smaller components of various weights below 10 tonnes. Since the existing platform crane capacity and reach radius was not sufficient for the project Thunder’s TC90 modular rental crane was proposed, which has a maximum capacity of approximately 60 tonnes for offboard lifts.
The client had explored other options for module removal; one such was to hire a barge crane. However, Thunder Cranes’ modular rental crane was the best solution from the viewpoint of ensuring safe static lifting, as well for cost and time savings.
The option of using the platform’s own cranes for topside preparation and clearance was also considered. This would have involved 150 days of removal work by the platform crane. Since its capacity was limited, many lighter lifts would have been required, and modules would have had to be sectioned and removed one part at a time; this would have also involved the extra work of isolating and disconnecting all lines connected to equipment. 15 lifts over seven days by a heavy lift vessel would also have been needed; the total decommissioning would have taken 157 days.
The alternative was to instal a rental TC-90 crane to be used in addition to the platform’s crane. With this option the schedule would reduce to: 30 days of removal by platform crane alone; 90 days of removal by the platform crane and the TC-90 working together; and three lifts, over two days, by the heavy lift vessel. The total decommissioning would then take 122 days. The saving in time is therefore over a month; the saving in heavy lift vessel time (and associated costs) is a not inconsiderable five days; and the total cost saving was in the region of $USD 1.5-2.0 million. Not surprisingly, this was the option that was adopted.
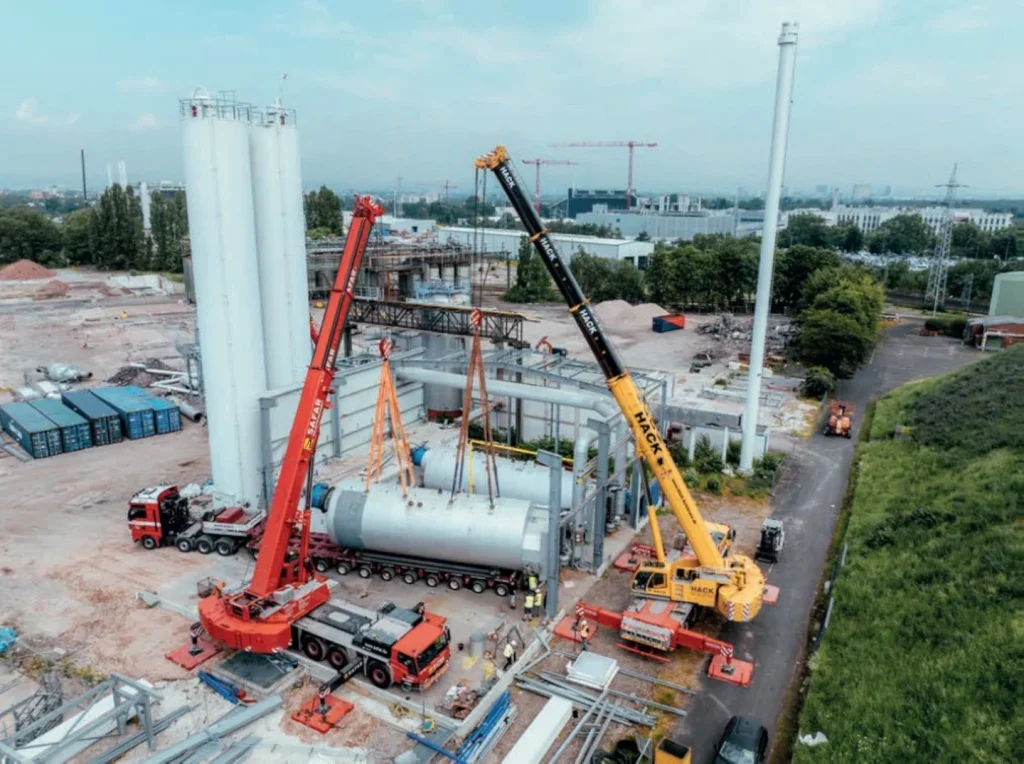
Performing the operation was not straightforward. The platform had very limited space for rigging up and no exposed beams on which Thunder Cranes could apply its TC90 clamping system. Therefore welding with dog plates was required to tie down the modular crane. This was implemented safely and without any issues with one shift of welders within three days. Due to limited space on the platform deck the supply vessel was on standby within reach of the platform crane during this time allowing the rig-up and rig-down of the TC90 crane on the fly.
Another challenge was that some of the larger modules at the limit of the TC90 reach radius did not have verified weight information. A decision had to be made on whether to reposition the crane for those lifts or whether to disassemble and breakdown down those modules into smaller components. It was concluded that the best way forward was to break down some of the modules. In addition, Thunder Cranes deployed its most experienced lifting superintendent on site to supervise the most critical lifts.
By removing the production modules the overall platform weight was reduced to be within the capacity of the heavy lift vessel which was able to remove the topside and structure in one lift. Approximate costs savings from the chosen option with the TC90 crane was estimated at $USD 1.5-2.0 million from savings in preparation time of one month, and in heavy lift vessel time of five days.
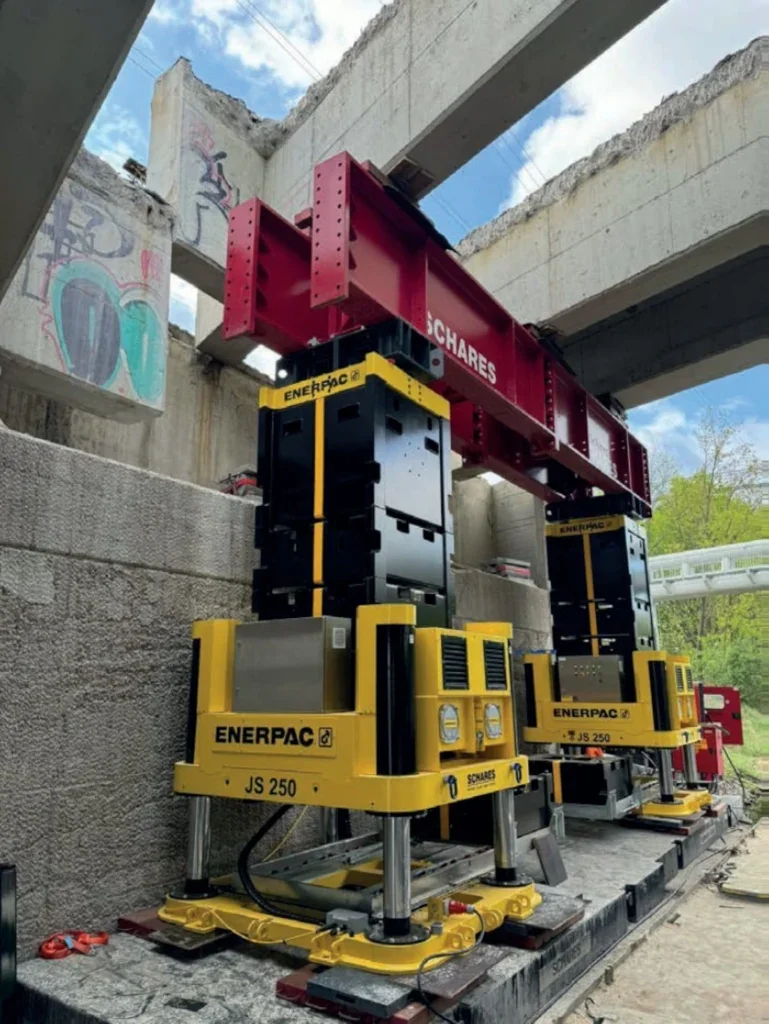
MAST REMOVAL
A similar maritime uncertainty concerning load weights, though on a smaller scale and at a quayside rather than at sea, was encountered by Gemmak Engineering, who this summer removed two masts from a historic vessel docked at Swansea Marina, Wales.
Gemmak is the engineering division within Rope and Sling Specialists (RSS). The work was aboard Helwick Light Ship LV91, a historic vessel belonging to Swansea Museum. Designed and built as a floating lighthouse her hull shape and form were specifically developed to remain anchored to mark a navigation hazard in all weathers and sea states.
Following a site survey by RSS to inspect the mast tensioners it was discovered that both the 87-yearold masts were in poor condition, so replacing the mast tensioners might have caused undue stresses and strains. Due to the proximity of the boat to a pedestrianised area, it was noted that the likelihood of failure and potential collapse onto that area would greatly increase with new wire tensioners acting on the masts.
Matthew Edwards, engineer at Gemmak Engineering, said: “We were then contracted to undertake thickness testing on the masts, to estimate the material loss due to corrosion and the effect that would have on the stability of the masts.
“Sections of the masts were tested and found to be in some locations to be between 40% and 60% of the assumed wall thickness. The recommendation based on health and safety was to remove the masts and to land them both on the ship so that any possible future works will still have the original equipment in one place.”
The masts were estimated to weigh between 900kg and 1000kg; they were approximately 12m tall and measured 270mm in diameter. Pipework was estimated to weigh 700kg, but during the lift the crane was reporting near 900kg for the front mast and near 1,000kg for the rear mast.
A local rental company provided a 35-tonne capacity Terex AC 35 L all terrain crane and led on the lift plan and selection of below the hook equipment; a 22-metre Skyjack SJ66T telescopic boom was also used to fit one-tonne capacity, one-metre-long slings to the masts.
Despite the length of the masts, centre of gravity wasn’t a concern because the masts were landed on the boat, then re-slung to create a horizontal lift.
“The existing mast tensioners were kept attached to the masts and tied to each mast during the lift,” explained Edwards. A safe working area was created for the one-day duration of the work.
TANDEM TEAMWORK
A decommissioning assignment that involved a tandem lift was recently undertaken in Germany by Frankfurt-based crane service provider Auto-Service Safar.
It decided to use its Tadano AC 5.220-1 all terrain crane to handle a boiler that had been removed from service at the old industrial park in Griesheim, near Frankfurt, and to do it together with Neuwied-based Hack Schwerlast which brought its very own Tadano AC 5.220-1 to help.
According to Safar the only way to lift the boiler, which weighed 120 tonnes and had a length of 11.60 metres and a diameter of 3.50 metres, was via a tandem lift and it says Hack Schwerlast was a solid partner in the endeavour.
The plan was for both cranes to lift the boiler to a height that would make it possible to move a lowbed trailer underneath it so that the load could then be lowered onto it. After that, the boiler would be transported to its destination in Turkey.
“To do this we started by optimally positioning both cranes after measuring the required radius of 13 metres and then rigging the load,” reports Safar’s heavy load and crane manager Detlef Precht, who also operated the Tadano AC 5.220-1. Together with the corresponding slinging gear the boiler came in at a gross weight of 122 tonnes, which was split evenly by having each crane handle 61 tonnes.
Set up with a counterweight of 71 tonnes and a boom length of 21.56 metres the two cranes lifted the boiler to a height of one metre in synchronisation.
After this a team from transport specialist Max Goll moved a 12-axle semi-trailer with a fouraxle tractor underneath the boiler and the two Tadano cranes lowered their load onto the semi-trailer.
“Thanks to preparation and perfect teamwork when carrying out the tandem lift, everything went exactly as planned,” reports Precht. He listed the prerequisites for a successful tandem lift. “The things that are absolutely crucial for us as crane operators are having a direct line of sight, being able to communicate smoothly with each other at every phase of the lift, and having experienced signal people that we can rely on one hundred percent.”
Abuzer Colak, managing director of client Colak, summarised the lift: “They carried out the job with professionalism and without issues within the scheduled time-frame.”
PRECISE OPERATION
German heavy lift contractor Autokrane Schares used its new Enerpac JS-250 jack-up system to assist in the challenging removal of a bridge.
The Marggraff bridge over the Britzer Verbindungs canal in Berlin was built in 1965. It consists of three bridge sections built adjacent to each other. Autokrane Schares was responsible for removing the first 60m long bridge section weighing 1500 tonnes. Overhead power lines and lack of space at the busy road intersection were severe constraints and meant that an Enerpac jack-up system was the preferred lifting solution. The close proximity of a busy highway meant that precise operation of the JS-250 was critical.
To position the JS-250 jack-up tower bases on the narrow canal towpath a section of bridge deck was removed at each end of the bridge and the jack-up bases lowered onto the path, followed by the header beams.
Once those were in position additional jack-up tower barrels were added from a pontoon. Synchronous lifting of the bridge section was achieved using two interconnected split flow pumps.
The bridge deck was removed in three stages, each 60m long and weighing between 450 and 630 tonnes, over a two-week period. For each stage the JS-250 raised the bridge deck three metres clear of the bridge abutments. Two pontoons were positioned underneath, and the bridge deck lowered onto steel frames resting on support structures. The bridge was then floated to the side and lowered on to SPMTs for transportation by road to a nearby site for dismantling.
“Space restrictions at the site made this a very challenging project,” said Max Boere, team leader SPMT, Autokrane Schares. “The compactness and ease of set-up, together with accurate synchronised lifting, made the Enerpac JS-250 a perfect fit for this project.”
GANTRY CRANE REMOVAL
Sarens was asked last year to remove two redundant overhead gantry cranes from within a warehouse in Teesport, UK.
The challenge was to remove the gantries without modifying the warehouse structure while allowing site operations to continue at the opposite end of the warehouse. The overhead gantry cranes had to be lifted from elevated rails 15m above ground level and placed on the ground to allow the demolition. The two cranes weighed 122 tonnes each and measured 30.7x12x7.8 metres.
Sarens crew decided to use four Sarlift Gantry Towers, with a capacity of 250 tonnes per tower, along with a ten-metre-long lifting beam, to raise the gantries. 20 K24 SPMT axles with two PPUs then moved them once on the ground; and three mobile cranes, of 400t, 500t and 100t capacity, were used to assist. Bracing steelwork, a spreader beam and tackle and a telehandler were also utilised.
Sarens engineers worked out a customised solution for the client. The trolley and cab were positioned on the overhead gantry crane as per Sarens’ specifications and parked in their pick-up position.
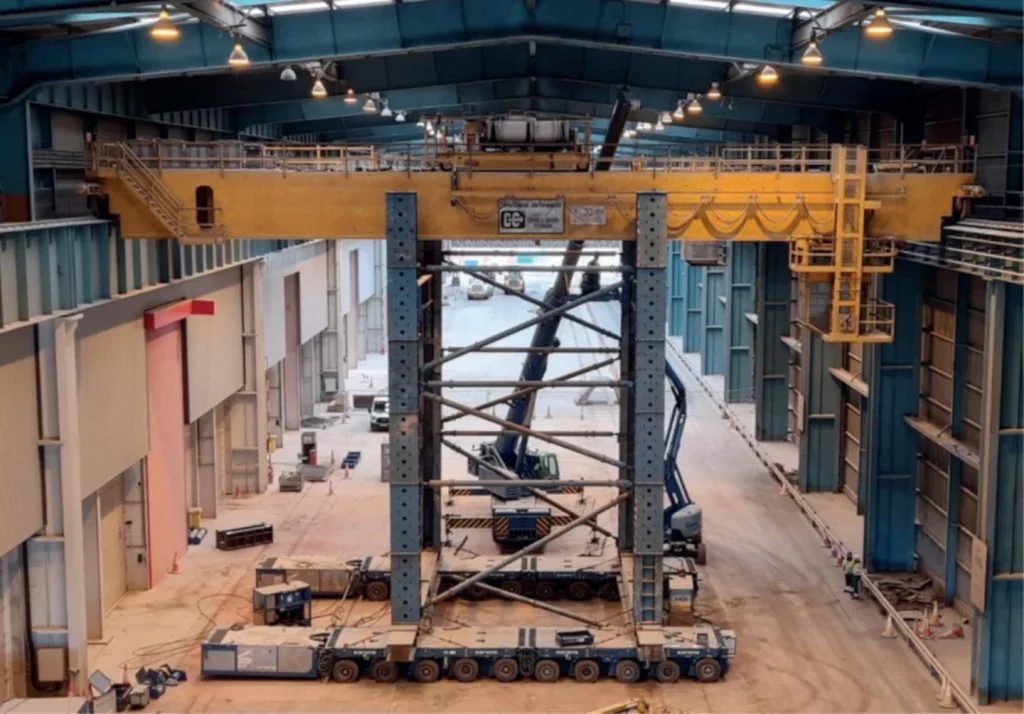
The 100t mobile crane assembled the SPMTs and Sarlift gantry within the warehouse adjacent to the gantry crane which was then driven into position. It was lifted 800mm using the Sarlift Gantry until the underside of the girders were above the rails. The SPMTs were then used in carousel mode to rotate the overhead gentry so that it could pass between the rails and lowered. Once lowered the crane was tandem lifted to the ground using the 400 tonne and 500 tonne mobile cranes.
The customised solution by Sarens provided considerable cost savings. This was because there was no requirement to remove roof sections from warehouse; no strengthening work was required, as supports were provided to the overhead gantry crane; and there was minimal disruption to port operations. There were safety benefits as well, from avoidance of working at a height, a reduction in project man hours, and work being undertaken within the warehouse so reducing exposure to the elements.
MAMMOET DISMANTLES TWO TUNNEL BORING MACHINES USED ON HS2 PROJECT
Netherlands-based heavy lift and transportation specialist Mammoet has dismantled two tunnel boring machines used on the HS2 (High Speed Two) rail project in the UK.
Having previously supported Align JV (a joint venture between infrastructure companies Bouygues Travaux Publics, VolkerFitzpatrick and Sir Robert McAlpine) with the assembly of two TBMs, Mammoet was well-placed to assess the requirements of the job.
Assembly of the TBMs took place at Align’s South Portal site, a large purpose-built site that included two factories that manufactured the segments required to line the tunnels, and a slurry treatment plant to process the spoil excavated from the tunnels. The dismantling of the TBMs was to take place at its North Portal site, near Great Missenden.
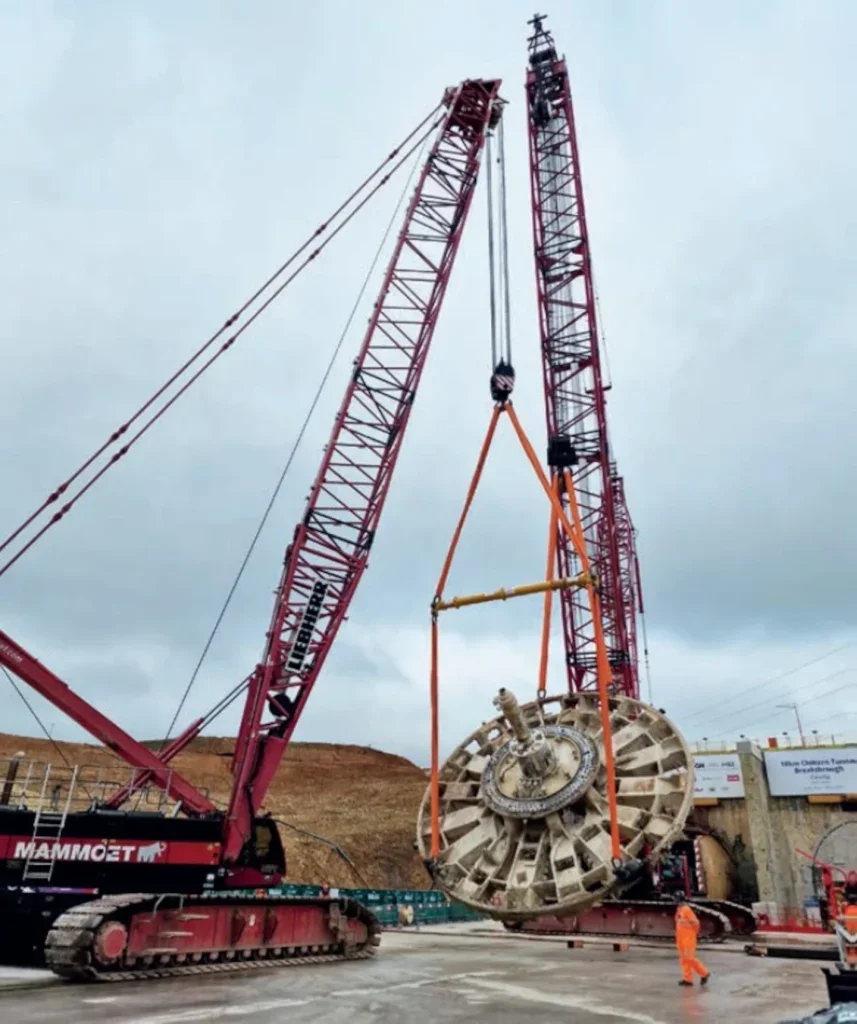
Simon Crawley, senior commercial manager at Mammoet, visited the North Portal site to understand the different limitations relating to the dismantling – which obstructions existed on site and what space was available.
“We determined that the equipment used to build the boring machines wasn’t necessarily the equipment needed for their dismantling,” said Crawley. “There were different limitations at the two sites. Because there were obstructions in the way, a 600t crawler crane was needed at the construction stage. We believed that a 400t crawler crane would be adequate to perform the dismantling.”
To prove a lower capacity crane could do the job Crawley worked closely with Mammoet project manager Rhys Burley and the project engineer Antreas Michail to create a detailed visualisation of the project using Mammoet Move3D software. This included a full animation of the most complex lifts.
Seeing how the job would be carried out using the smaller crane, Align was satisfied with the recommendations that Mammoet put forward and was able to use a more costeffective solution.
With separate TBMs creating the south and northbound tunnels, two machines needed to be dismantled at the North Portal. The 400t capacity crawler crane (a CC2400) was used to remove the biggest components from the TBMs. For the heaviest component, the cutter head, an LR1300SX crawler crane was also used to perform a tandem lift.
The components were lowered onto Mammoet Self-Propelled Modular Transporters (SPMTs) before being taken to one of two laydown areas.
Additional crawler cranes, including the LR1300SX and an LR1250 support crane, offloaded the components onto the ground or supports for further dismantling.
As the cutter head was too heavy for the smaller cranes to lift, climbing jacks were used to offload it from SPMTs to the ground.
A challenging aspect of the project was the fact that the cutter head’s centre of gravity (COG) could not be fully known. The lifts also needed to be performed on a slight incline. This was because the TBMs exited the tunnel at an angle. Typically, challenges such as this this would result in having to create additional drawings and manage changes before performing the lift. This would add unnecessary delays, depending on how pronounced the differences were with respect to the original project planning.
The team instead came up with an engineering solution that would avoid unnecessary changes, and days or even weeks of potential downtime.
“We used air hoists to make pneumatic length changes and keep the components level,” explains Burley. “It took away that manual element of hoisting chain blocks. It was done on a compressor rather than using manual labour, which was safer and more efficient.”
“The key challenge was the large amount of equipment and people needed for the project,” concludes Crawley. “As the biggest global company when it comes to heavy lift and transport, we knew that we could meet these expectations.
“We were able to offer a full turnkey package, by providing all Mammoet personnel, all the crawler cranes, mobile cranes, SPMTs and jacking systems, and we could also adapt to any changes.”