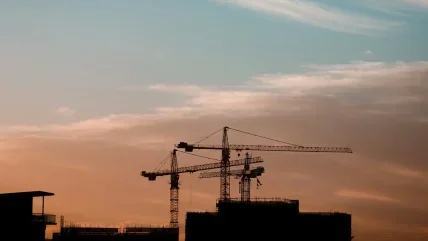
COVID, and the lockdowns that accompanied it, sometimes feel like it has disappeared into a memory hole. For those of us lucky enough to have got through the pandemic with our health – and that of our loved ones – unimpacted, those couple of years can sometimes seem unreal and dreamlike, a boring blur of awkward working from home, isolation or enforced family time, and shopping trips planned with all the care of a polar expedition.
It seemed for a while like nothing would be the same. Once we’d learned – or shown our parents and grandparents – how to use an online store, it seemed like no one would ever need to visit the high street again. And for those engaged in knowledge work, selecting interview quotes, making sales pitches, or analysing business performance on a spreadsheet, it seemed like no one would ever go into the office again.
Now, with the perspective of time, we are gaining a clearer idea of the longer-term impact of this period on both city centres and the wider construction sector. Things have changed… it probably doesn’t make a lot of sense to open a sandwich shop on a Monday in the city now. Many of those knowledge workers now come into the office for just a couple of days, in the middle of the week, if at all.
But even home workers need to clear their heads, buy a few groceries, and grab a lunchtime treat. So while city centres may still feel the impact, commerce may have seen a boost in the suburbs where these workers now spend most of their week.
Although the sector has changed it has not been decimated in the ways that only a few years ago looked likely. And in many parts of the broad commercial construction sector, crane owners can still find opportunities.
SPEED RULES
One thing has changed since COVID: inflation has soared and, with it, interest rates. That means the impact of project delays are more keenly felt by developers. The longer you’re building, the more interest you’re on the hook for before you can start earning from your new project opening. Speed is key. And the commercial sector is all about getting buildings up fast: techniques like tilt-up, steel erection, and prefabrication all contribute to this pace.
Liebherr Nenzing’s LR 1400 SX squarely targets jobs where speed, rather than multiple lifting configurations, is key. The crawler is the biggest ever built by the Austrian factory: its German counterpart, Liebherr Ehingen, builds much bigger cranes with more configurations available, but these can take more time to transport and erect.
Appropriately, the new crane was first to put to work on precisely the sort of job where speed is key: the tilt up construction of a new film and TV studio, Electric Owl Studios, in Atlanta, Georgia. The work was carried out by local specialists, Full Tilt Crane Services. The company used on-site cast panels, measuring up to 34 metres high.
“We bought the machine to meet the needs of our customers: to lift larger and heavier pieces,” explains managing director Jason Richardson. On site casting and tilt up eliminates the need for costly transport, and offers customers flexibility. Full Tilt Crane Services aims to support contractors in the sector, like Martin Concrete Construction, who supplied the panels for this project, by getting to work fast and getting the job done quickly. Often, the company completes its role within a couple of weeks.
The ease of setup of the LR 1400 SX, along with its 400 tonne capacity, is a boon on a job like this. “The self-assembly system of the crane is very important to us,” says Richardson, “We don’t need an assist crane. Right now, we can fully assemble our LR 1400 SX in under 12 hours.”
The crane has been designed around this sort of use, with care taken to eliminate any source of delay. Platform and railings remain attached to the uppercarriage during transportation and only need to be folded down. Thanks to the self-assembly system, Liebherr says, the boom sections, carbody counterweight, crawlers and hoist winches can be easily assembled and disassembled without the need for an auxiliary crane. The crane can even hydraulically lift, lower, and secure the 150-tonne rear counterweight without assistance. The rear counterweight itself is modular and can be equipped with 5 or 10-tonne counterweight slabs, depending on requirements.
Full Tilt was so happy with its first crane, that it has now ordered a second.
For taller buildings, where you are not just assembling a big box for a customer to fill, fast steel erection is equally important. Stevenson Crane & Rigging supplied a 150USt Link-Belt 238 HSL crawler to Ben Hur Construction for a project like this: a new seven storey hospital in Crown Point, Indiana, constructed using more than 4,600US tons of structural steel, supplied by Lenex Steel.
Ben Hur Construction is aiming to complete the structural steel on the project in six months. “We are able to set 40-50 pieces of structural steel per day, and once we get in a nice rhythm we can safely set up to 80 pieces in a day,” says Frank Hiatt, senior project manager for Ben Hur Construction, Central Division-Indianapolis.
Key to this pace of construction is the HSL 238, and Ben Hur’s careful site logistics. Steel pieces, and other building materials, are staged nearby to ensure steady work. The crane can then pick multiple steel elements at a time. “More speed and less distance to travel to place the Christmas tree rigging allows multiple steel beams per lift and expedites each hoist. The crane still has the reach needed to place up to five beams, spaced seven feet apart in one lift, to the far top reaches of the structure which saves the crew time in placement of each beam,” Hiatt explained.
The 238 HSL was set up with 200ft (60.9 m) of main boom, with 50ft (15.2 m) of jib offset at 25 degrees. The heaviest loads are the 40ft steel columns that weigh more than nine tons each.
Fast paced permanent construction techniques are key for business and for the health sector. Schools face another set of deadlines: kids can’t wait for months to go to school, and when the young population of an area soars, the first task is to make sure there are enough classrooms for them to learn in. The approach used here – of modular, temporary, buildings – will be familiar to anyone who’s spent time in site offices; it is also increasingly used for leisure facilities, like ‘pop up’ street food markets.
Orange County, Florida, has one of the largest school districts in the USA. Recently, Beyel Brothers supplied two all terrains, a Tadano Demag AC 220-5 and a Manitowoc Grove GMK 5225, to Dynamics Group, for a school expansion project.
The job saw temporary classrooms moved from two local elementary schools, to a nearby high school. The 16 buildings were transported from Avalon Elementary and Orange County Virtual School in Orlando, to Apopka High School in Apopka, Florida. The Demag was used to lift each of the 32 component pieces onto trailers, which were then transported to Apopka and unloaded by the Grove. Both cranes used a custom rigging configuration with multiple slings and spreader bars.
“Enrolment at schools in the district has soared with an extra 3,300 students entering the system. We are happy to be able to play a part in the growth of the school system to better serve teachers, students and their families,” said Joe Beyel, president of Beyel Brothers. Dynamics Group Inc and Beyel Brothers are already scheduled to move additional classroom buildings over the summer.
RETURN TO WORK?
While many knowledge workers no longer regularly attend the office, city centres are still the beating heart of the economy.
Employers who now struggle to get their staff to spend hours commuting to do work in the office that they could do equally well at home must find other ways to encourage them to come to the office for those collaborative and mentoring tasks that benefit most from face-to-face interaction.
One way to do this is by offering the chance to combine work and leisure time. In London, for example, HSBC has announced that it will give up its lease on its premises in Canary Wharf — a purpose built, soulless, financial services district, in the former Docklands — for a smaller site in the heart of the city.
Many of the vast open plan skyscrapers of the past will see dropping demand. But this may be replaced by a new type of working environment of smaller offices, suitable for daily use by a fraction of a company’s total workforce, in locations closer to leisure and shopping facilities.
At the same time shops find themselves competing with Amazon, Ocado and Shein. Like employers, they must offer the opportunity to do more, in a buzzy and exciting city centre. Buying a new piece of cookware, getting your weekly shop in, or finding a new outfit for the weekend, no longer requires a trip into town. But a good meal between shops, or a hotel where you can make a weekend of the trip, might get you out of the house.
Tower cranes are the tool of choice for high value buildings in constricted city environments. In Vienna, Austria, Wolffkran has supplied three cranes for use on a new department store, which will also boast a hotel and restaurants, called Lamarr. Hedy Lamarr, for whom it is named, was both a glamorous star of Hollywood’s golden age and the co-inventor of radio frequency hopping technology which laid the ground for today’s wireless world. In this mix of talents one might see inspiration for today’s world, where shopping and relaxation, work and play, live side-by-side.
The mixed use project on Vienna’s Mariahilfer Straße, in the heart of the city’s downtown, required careful selection and planning of cranes. Contractor Habau Hoch- und Tiefbaugesellschaft purchased a Wolff 8033.16 Cross for the project. It is being used alongside two more Wolff cranes, a 7352.16 Cross and a 6023.8 Clear, to construct the building shell.
Wolffkran planned the job so that only the largest crane needed to be erected with a mobile crane. The 8033.16 Cross was then used to erect the 7532.16 Cross, which was itself used to erect the flat top. It took some careful planning. "For the assembly of the roughly 14t jib of the Wolff 7532.16, our team had to calculate an overload hoist for the Wolff 8033.16 since the crane was statically reaching its limits at this point," says Zeljko Tenjovic, managing director of Wolffkran Austria.
Space and overflight limits made placing the cranes equally tricky. The larger crane was placed on the edge of the site, with the smaller cranes in the middle. Since 2022, they have been used to lift concrete, formwork, and reinforcement across the 6,500 sq m site.
The cranes will help get the building shell completed fast, by the end of the year. But the Wolffkran team have set themselves up for another challenging set of lifts at the end of the project: once the building is complete, there will be no way to get a mobile crane close enough to the cranes to dismantle them.
The Wolff 7532.16 will first dismantle the Wolff 6023.8, and afterwards, it will be dismantled by the 8033.16 standing some 60 metres away. The 13-tonne heavy counter jib of the 7532.16 will have to be split into two parts. “To handle this, we need to release the bracings of the counter jib at the tower top and support the remaining jib section with special supports towards the crane tower before this component can then also be taken down," says Tenjovic.
ECO DISTRICT
In Switzerland, Potain dealer Stirnimann supplied four cranes to real estate and construction company Implenia for work on another mixed use project, Central Malley, in Lausanne. The new ‘eco district’ on a brownfield site on the edge of the country’s fourth largest city, will combine offices, housing, and shops, and seeks to promote energy autonomy.
“Several factors make this a complex and unique project, with building heights reaching 80m and the location of two towers close to the SBB railway,” says Florian Lamy-Rousseau, project manager at Implenia.
Stirnimann’s solution included one Potain MDT 308 and three MDT 389 top-slewing tower cranes equipped with cameras, the Potain Top Tracing 3 interference system, the new Potain Connect telematics system, and aviation lighting.
The Potain MDT 389 has a maximum load capacity of 16 t and 3.3 t at the end of the 75 m jib. However, it will primarily handle loads of 11 t at 30 m and 6 t at 55 m. The cranes will operate daily from 7 am to 6 pm, and the project is estimated to last between 24 and 30 months.
TRANSPORT PLATFORMS
Not every task on every office project needs quite as much lifting power as this. For many tasks, on many sites, a material hoist or personnel lift is ideal. Geda’s range of transport platforms are designed to move both people and materials. In Malta, Y&P Cranes is using a Geda 1200Z/ZP transport platform to lift both safely, on a new high rise office building.
The Geda 1200 Z/ZP, in its C configuration, has a capacity of 1500kg. It offers 1.4m x 3.2m of space, with a 2.9m doorway, simplifying loading pallets of materials. For this job, the transport platform needed to serve 17 floors and reach a conveyor height of 85m: well under its 130m maximum.
Geda’s transport systems feature two separate control systems: this allows it to be used for materials alone, at 24m/s; when it is being used to carry personnel, it can work at 12m/s.
Geda’s systems are supported by a range of digital applications via its new Geda Central platform. This includes an installation designer, which customers like Y&P Cranes can use to calculate anchoring and ground forces.
For more complex, BIM-based planning, Geda offers models of its equipment in a range of file formats, suitable for use in building models or to simulate construction processes.
So we see the commercial construction sector has proven to be resilient despite initial concerns about the impact of the COVID-19 pandemic. While the ways of working and shopping have changed, the sector has adapted to the new realities. City centres may have experienced some challenges but commerce has seen a boost in the suburbs and in brownfield sites. The construction industry has embraced speed as a key factor, with techniques like tilt-up, steel erection, and prefabrication enabling faster construction timelines. Crane manufacturers have introduced innovative solutions that prioritise efficiency and quick assembly, while the demand for smaller offices and mixed-use projects closer to leisure and shopping facilities has emerged as a trend.
Additionally, the need for fastpaced construction techniques is evident in sectors such as healthcare and education. Despite the rise of online shopping, physical stores can still attract customers by offering unique experiences and opportunities for leisure. The future of commercial construction lies in creating vibrant city centres that combine work, play, and relaxation.
The lifting industry's ability to adapt and embrace change ensures its continued success in a rapidly evolving landscape.
Two raimondi flat-tops at work on commercial cluster in Toronto
JESS Equipment Inc., the Canadian equipment management company operating under the Straw Construction Group, supplied two Raimondi fl at-top tower cranes, an MRT234 and an MRT294, to an urban redevelopment project in Greater Toronto Area, Canada
The jobsite, situated in North York, part of the Greater Toronto Area, is for the construction of three new rental buildings across the street from the Yorkdale Shopping Centre.
“The decision to utilise these two Raimondis on this important project is based on the superior lifting capacity of the machines, as well as the fast lifting and loading speeds,” said Sante Paglia, director of Jess Equipment Inc.
Paglia added that, due to the dimensions of the site and the project’s tight completion deadline, it was essential to choose high performing machines with signifi cant hoist speeds.
The MRT234 presents a maximum lifting capacity of 12t and is freestanding at a height of 35.6m. The machine has been confi gured with a jib length of 48.4 metres and a tip load of 5.6t.
Equipped with a 55kW winch and a drum capacity of 700 metres, the fl at-top maximum lifting speed is 22 metres per minute.
The MRT294, which freestands at a height of 36.2m, is at work with a jib length of 42.37m and a 7.6t tip load. The 16t maximum lifting capacity crane is fi tted with a 75kW winch and 700-metre drum boosting a maximum lifting speed of 26 metres per minute.
The machines had a staggered installation schedule, in line with the jobsite progress. Both cranes, erected by Total Crane Hoisting & Rigging Inc., will remain onsite for a total of approximately 18 months.
“With the jobsite located in close proximity to Yorkdale Shopping Centre, one of the busiest centres in Toronto, as well as the Highway 401, one of the most traffi cked highways in Canada, the biggest challenges of the project were to ensure smooth operations when accessing the site and to guarantee that the cranes do not swing outside the boundaries of the site,” Paglia explained.
Upon completion, the site will feature three contemporary towers hosting 760 residential rental units, commercial spaces, and several modern amenities.
“Currently, we have seven Raimondi cranes within our fl eet, all at work at different jobsites around the Greater Toronto Region. We are proud to participate in this landmark project by Fitzrovia and have utilised two of Raimondi’s heaviest lifting machines in order to ensure its successful delivery,” he concluded.