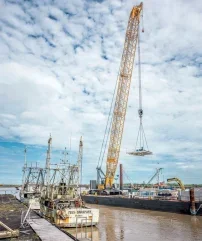
In the wider context, the use of cranes at docks around the world isn’t confined to simply the loading and unloading of cargo. The docks themselves, for example, need to be constructed – often using crawler cranes based on floating platforms, or barges, which install pilings and foundations into the ground under the water. There is bridge work, too, and other dockside infrastructure where often the only way for a crane to access the site is by floating it.
In an industry based upon eliminating variables, however, a floating (i.e moving) base is not ideal as the crane operator has to take into account not only the lifting movements of the crane but also those of the floating unit.
Add to the equation, says crane manufacturer Liebherr, usually only load charts on paper are available for operation on floating units. That’s right, there’s often no load moment limitation integrated into the crawler crane’s control system. This makes a possibly dangerous situation potentially even more perilous.
LISTING CHALLENGES
Safe operation based solely on printed load charts is extremely difficult, says Liebherr, as different load moments of the crane result in different listing of the barge. This effect is amplified when the crane slews because the barge normally has different listing angles longitudinally and transversely with the same load moment.
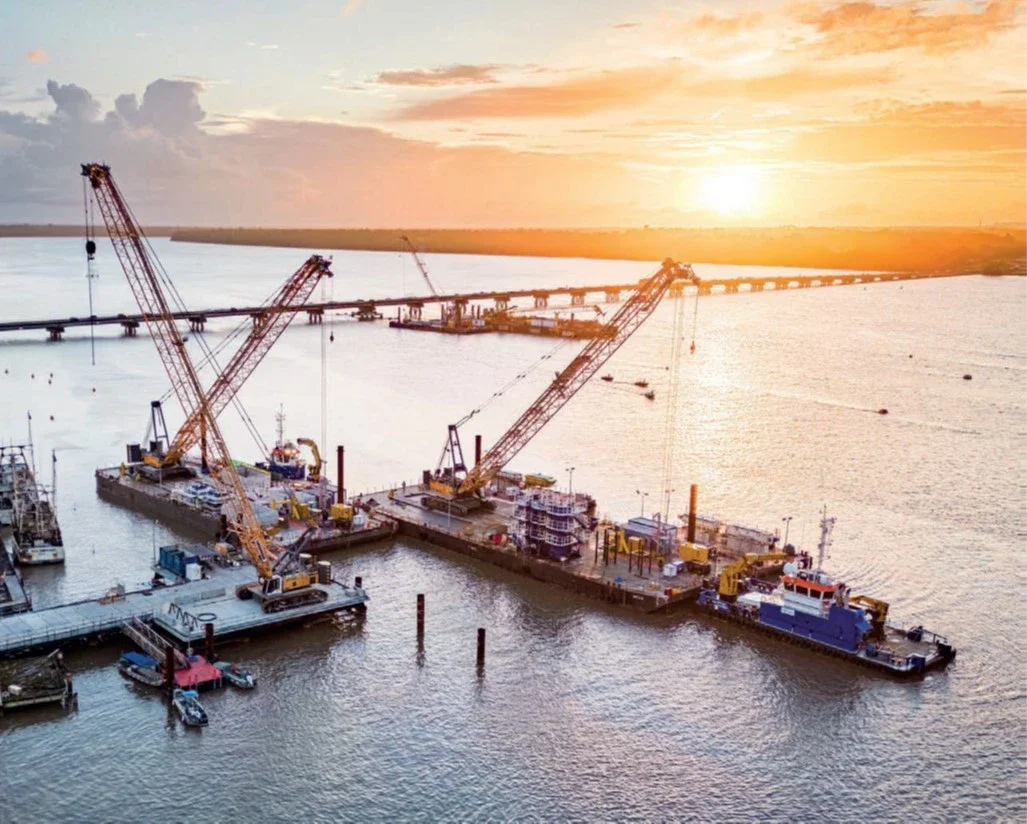
When the crane slews the inclination of the barge usually changes. This means there is a danger that the load moment limitation will react while the crane is slewing, so there is a risk of the crane toppling and/or overloading.
Should the slewing gear ‘stop’ be triggered there is also the potential for uncontrollable swinging of the load.
While lifting or setting down the load a further change in the barge inclination is caused due to the change in the position of the centre of gravity and the total weight (i.e crane plus load). This causes diagonal pull which can lead to additional strain on the crane as well as uncontrolled swinging of the load.
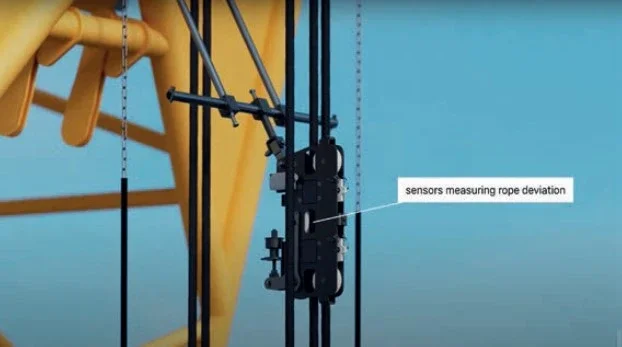
When setting down the load with a small radius the maximum angle of the boom may also be exceeded due to the shift of the crane’s centre of gravity to the rear, resulting in a risk of the boom toppling backwards.
As you can see, there are multiple potential dangers that need to be considered.
SAFETY SOLUTION
Liebherr’s solution? It’s a digital, real-time control system mode for its crawler cranes called ‘floating unit operation’ which, as you might expect for such complex scenarios, is multifaceted.
It starts with monitoring. Once the floating unit operation mode is activated sensors monitor the barge or pontoon’s inclination during the entire operation and this information is displayed to the crane driver.
Based on this information, the operator can simply select the most appropriate floating unit operation settings. The operating mode includes load curves for different lists (0°, 1°, 2°, 3°) with appropriate protection via the load moment limitation. If the permissible limit value is exceeded, a warning is issued. Additionally, it prevents the maximum boom angle from being exceeded when the load is set down.
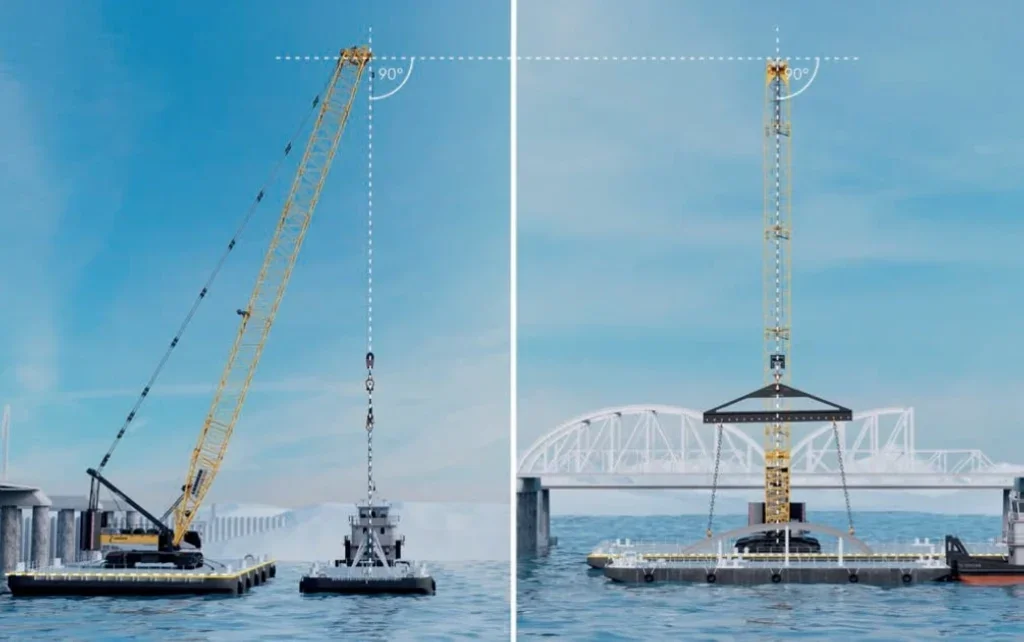
Another aspect is Liebherr’s ‘Vertical Line Finder’ assistance system. This enables the crane driver to avoid all inclined lifts at the touch of a button – especially those caused by changes in the barge inclination as a result of the shift in the centre of gravity when lifting and setting down the load.
The system positions the hook above the load’s centre of gravity and prevents lateral pull forces and swinging load, thus increasing operating safety and extending the service life of the crane.
This innovative answer could well be a game-changer when it comes to enhancing safety in on-water lifts; and a specific application that is catered for is pile driving. When combined with Liebherr’s pile tilting device, with a maximum weigh capacity of 90 tonnes, the system offers safer operation as there are zero effects from lateral forces, says Liebherr.
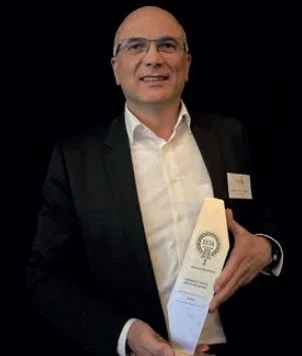
FINDING FAVOUR
Liebherr’s new assistance system for floating lifting operations is fast finding fans. It won the safety award at the ESTA awards in April 2024. “The award is recognition of our efforts to design safe cranes and construction machines,” said Gerhard Frainer, managing director for sales at Liebherr- Werk Nenzing. “As a manufacturer of cranes the safety of jobsite personnel is of the utmost importance to us. Our digital solutions and assistance systems are a result of this commitment.”
The system is also finding favour in real-world applications, too. In French Guiana, for example, French construction company Vinci is building a new bridge, the new Pont du Larivot, across the Montsinery river to help accommodate increased traffic between the capital Cayenne and Kourou – where The European Space Agency’s Spaceport site is located. Once complete the bridge will be around 1.2km long and comprise 19 different piers.
To help build the bridge Vinci has commissioned the help of Dutch marine services provider Neptune Marine. Neptune says it is a one-stop-shop for maritime services and has provided both the barges and the Liebherr LR1300.1 SX crawler cranes that are on them for the project.
The cranes are being used to place piles and lift pre-cast low carbon concrete bridge elements onto them. To place the piles, which are 1.6 metres in diameter and up to 50 metres deep, Vinci is using a technique called Reverse Circulation drilling. To do this, it says, it requires the crawler cranes which, to maximise safety, are equipped with the ‘floating unit operation’ (aka ‘barge mode’).
“Liebherr was able to understand our needs,” says Julian Agostini, business development manager at Neptune. “Liebherr understands that every asset of ours is specific and needs to be customised. Having the barge mode means that the operator is now in syncronisation with the machine and we are doing everything possible to avoid risk, ensuring maximum safety during all the lifts.
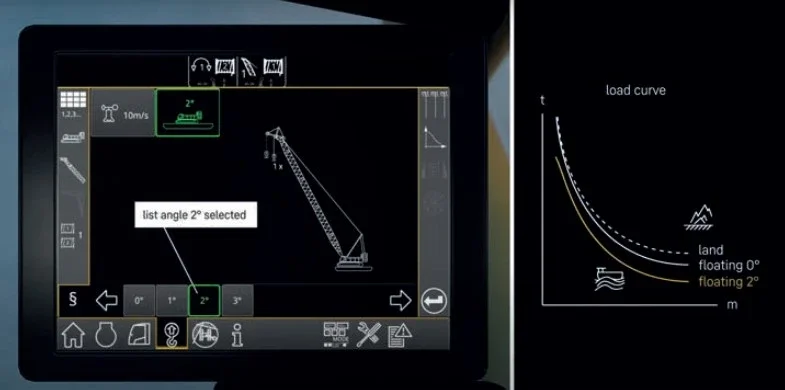
“Even though the investment [in the equipment] was significant, we get this back through the reliability of the machines and their low breakdown rate.”
In such a remote and tough environment it’s heartening to see that safety and reliability are so highly valued