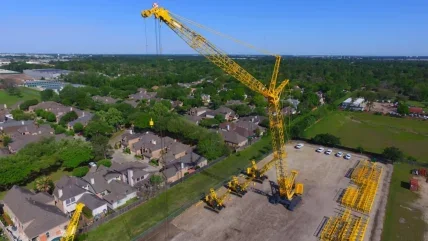
If you want to buy one of the biggest derrick cranes in the world, I know where you can get one. Or actually, two. Bigge Crane and Rigging Company of California have them available. They were purpose-built for the construction of two new nuclear power stations in the southeastern USA. One station is finished, completion of the other has been cancelled, so they are available for other work. They are, as you might expect, massive machines.
Their capacity is 1,500t at 165ft (50m), or 1,000t at 400ft. They are not mobile, but rotate on a 360° ring around a fixed point such that they can cover an area of 28 acres (11ha). “These derrick cranes were configured to carry every load on the projects they went on and have an immense reach,” says Thom Bostrom, senior vice-president at Bigge. “No other crane has the capacity of serving multiple locations the way this A-frame ring derrick can.” Bostrom should know. He led the team that designed and built the machines.
The Bigge cranes are A-frame ring derricks. “They were designed in-house for the nuclear projects,” says Bostrom. “Basically the design objective was: ‘If you were using conventional cranes, you would need some of the largest ones in the world and you would need several of them at each site, and you would need to move them about. We wanted one machine that could do all that from one location. That concept drove the design, which is how we ended up with a derrick. 1,000t capacity at large radius was the concept that we tried to solve, and we did it. I believe they were the largest in the world at the time, though they are not now.
“We had a number of other criteria which made it a challenge. They needed to be able to stay in service in high winds, and to stay up in even higher winds. Nuclear stations tend to be built near coasts, and these were in the south-eastern US, which is hurricane country. So they needed to be able to withstand a Category 4 hurricane, and they have been tested in some pretty severe-event hurricanes since then. That drove a lot of the consideration.
“Each of these can slew 180° in ten minutes, which is quick. That was a design challenge. They are computer controlled, and since they were built for nuclear projects, safety demanded a lot of redundancy features, in braking and the like. For that reason, we installed traction winches, made by Timberland in Canada, rather than drum winches. You can make a derrick so simple that it does not have a lot of safety features, but these two are at the high, sophisticated end of the spectrum.
These are not simple derricks that you would put on the top of a highrise to dismantle your tower crane but the geometry is the same.”
The exact definition of derrick cranes, and what separates them from other cranes, is hard to pin down. Typically, they have a vertical kingpost, or else an A-frame, with bracing struts behind it. Perhaps their most particular characteristic is that the mast and struts are fixed directly to the ground, or to the structure they are working on, rather than to a superstructure or a tower or a set of crawlers or wheels.
The geometry of their struts and booms tends to be uncomplicated and, more to the point, practical: it works. Which are reasons why they have been used since the very earliest times. “Conceptually the derrick is old. It has been around as long as machines and gantries have been around” says Tim Kittle of derrick specialists F&M Mafco.
Early industry, big and small, used them; you can still see examples, rusting or otherwise, at disused rural sawmills, workyards or quarries. They are also involved in the building of some of today’s most iconic buildings; so it is a design worth looking at.
“The geometry is simple – a vertical and two bracing struts or cables, making a triangle,” says Kittle. “The simple geometry makes it simple to install. A big advantage of the derrick is that the mast and the two back legs are tied to the ground or the host structure, so they pass the vertical loads down into it. It means that a properly-installed derrick cannot tip. A large mobile crane needs counterweights, sometimes very heavy counterweights, to prevent tipping. Indeed, it is most often the tipping limit that restricts their capacity.
"A derrick, on the other hand, cannot tip. The host structure itself becomes the counterweight. That host is often a building or part of a bridge and is generally very much heavier than whatever is being lifted. So a derrick can be rated by the vertical load, not by the load moment.
“You do not need to add much to the mast and the stifflegs to make a derrick work.
The simplicity and the lack of counterweight and undercarriage means that derricks are immensely strong for their weight, and therefore cheap.
Having no undercarriage means there is far less to go wrong. You do have to be specific about where on the host structure you attach the kingpost and legs, since those points will take the load reactions.
A derrick can slew, but generally not through 360°. It is constrained by the stifflegs, which are normally at 90° to each other behind the crane. That still gives you 270° of possible rotation; the boom cannot go directly behind the crane but it can go almost anywhere else. We take that into account when we work out where to site it.”
Kittle is a great fan of the derrick—not surprisingly, since his company owns what may be the largest fleet of derricks in the world. “We’ve found that for us, for every ten jobs that lift an object from A to B, a derrick is best for one of them. They are good for marine applications, for unloading barges for example, and for general construction and building where air rights are expensive.
“Typical for us is bridge building. We mount the derrick on a slab or a structural steel carrier on the outermost completed deck section; use it to lift the next deck section into place; and then push the whole slab and derrick forward onto that section to begin lifting and mounting the next one.”
“The derrick is a good concept,” says Bostrom of Bigge.
“It is greatly applicable at the heavy end of construction, for large industrial builds and dockside and other large industrial facilities. The key word for these types of bespoke derricks is ‘large.’ It is a large capital investment and needs the right large project to justify it.”
Up On the Roof
But the geometry being simple means that is also easily scalable, and the most frequent use of derricks today is at the smaller end of lifting; here light derricks have established a particular niche application. “For roof work it is far cheaper to put a derrick onto a roof than to use a huge mobile on the ground for the job,” says Kittle.
Tower cranes build high-rises; but when the buildings are at full height the tower cranes need cranes to dismantle them, and the light, easy-to-carry cranes that frequently do the job are derricks.
The tower crane lifts them to the top of the building; they are secured to the concrete or steel of the roof; and they lower the tower crane components piece by piece. At the end of their task they are light enough to be dismantled by hand, into components that are small enough to fit down the lift-shaft of the now-nearing completion building. Sometimes there is an intermediary size of crane in the process as well, making a two-or three-stage process.
This is the concept behind Jaso’s DC series of derrick cranes, which can be used in conjunction with their larger RC ‘recovery cranes.’ These latter are derricks in the sense that they are fastened down to a surface directly with no substructure, though their geometry more resembles a conventional crane.
Marketing manager Dick Huitema describes one procedure for recovery of a tower crane: “The tower crane lifts a Jaso J80PA recovery crane and a smaller Jaso J1125 DC Derrick crane to the roof. The recovery crane dismantles the tower crane and lowers its components to the ground. The derrick crane dismantles the recovery crane; and the derrick is dismantled by hand and is lowered by hoist down the building’s elevator shaft.” Huitema outlines the design criteria for these light derricks.
“The main and vital criterion has been for easy dismantling into smaller pieces, keeping the weights of separate elements to a minimum. These are typically manhandled down in man hoists or in elevator shafts. This applies not only to the steel parts, but in particular also to the mechanisms.
And drum capacities must be in line with the increasing height of high-rise building, so that rope length is adequate to reach to the ground.” Jaso offer two derricks in their range. The simplest and smallest, the J112DC, has a maximum boom length of 11m and capacity of 2.5t at 11m, which is the maximum boom length.
The longest boom on their larger J1920 has 19m reach, at which radius the crane can lift 2t. Other options are a 17m boom, with 3t capacity at the tip, and a 15m boom which again at the tip can lift 4t. They now offer two versions of their recovery cranes also.The J80PA-RC is the original, with maximum load of 4t direct pull or 8t with double reeving. The new J88PA can work with eight reeves to lift 16t.
“Our recovery cranes have drum capacity of up to 800m, and the J1920DC derrick can reach 478m in direct pull configuration.
“Although our derricks have not been designed to work as construction cranes they can be used as auxiliary cranes for other purposes within the load spectrum, mainly thanks to that ability to be dismantled into small components.
That makes it easy to mount derricks in sites where few other options are available.
“Similarly, since the number of pure recovery operations is rather limited, both our recovery cranes can be used also as normal construction cranes with a 40m boom and 5t maximum lift. This increases the feasibility of the investment from an economic point of view.”
Liebherr have their 200 DR 5-10 derrick crane, designed specifically as a dismantling crane for stripping down tower cranes from high places. “That is why the dimensions and weights of all the individual parts are designed to enable them to be dismantled solely with the aid of a very small hoist and removed via lift shafts,” says Hans-Martin Frech.
This crane can also be used as a standard construction crane for very high bridge pylons or telecommunication towers. “The crane breaks down to parts with maximum dimensions of 2.2m x 1.1m x 1.1m, with a maximum weight per package of 1,000kg.
No additional crane is needed to dismantle it – just simple hoisting equipment.” For this, Liebherr supply a complete package consisting of a high-lift truck, a fork-lift truck with weighing equipment, and a collapsible workshop crane. “And the equipment is particularly easy to assemble and disassemble, aided by accessibility of the jib sections and tower and drive platforms and the fact that only plug-and-socket connections are used for the electricity lines” says Frech. “This makes it possible to fully dismantle the derrick, given suitable building site logistics, in only 3 to 4 days.
“The 200 DR 5-10 has no trouble dismantling tower cranes in the 300tm-plus payload category” he says. “Since dismantling machinery is generally used at very great heights, its standard construction includes hoisting drum for heights of 630m in single- and 315m in double-reeved operation.
“The Liebherr derrick can be configured with load moments of 100tm or 200tm. The maximum radius can be set to 20m or 25m.
The jib for 25m radius can hoist 8.1t at the tip, and 10t at 19m radius. This ensures that the crane can lower heavy parts from great heights while preserving a safe gap between them and the building.” City Lifting have an interesting variant in their Artic CL125 crane.
Recently introduced, its jib is that of a light tower crane; “but it can be mounted in many different ways”, says owner Trevor Jepson It can go on a normal or a small tower, or on a base cross that is bolted directly to, for example, a high rise roof. Alternatively it can be put on custom steel grillage, which could act as skids. He will have five of them by the end of May so he is hoping that there will be a good market for their services. The company also has a Vanson LCL 20.1L, a luffing crane which in floor-mounted configuration can lift 1t at 20m radius, and 3.5t at 3m, giving it abilities similar to a small conventional derrick.
ALE also has a light derrick, the LSC or lightweight service crane. “Due to its lightweight construction and its capacity, the LSC’s primary capability is for lifting equipment onto high-rise buildings” says sales director Richard Verhoeff. “This typically means air-conditioning units, air handling units, or building maintenance units.” But as with the other small derricks, he says, it can also be used for tower crane disassembly.
Unusually for this category, the height to which it can lower is not limited by the size of a winch drum. “It does not use drum winches but tirfor winches, so it pulls cable through a winch instead of rolling it around a drum.” In a tirfor winch jaws grip the rope and pull it; at the end of the stroke a second set of jaws hold the rope still while the first set moves forward for the next stroke. This is conceptually similar to the friction winches used on Bigge’s giant derricks. “Because of this you can use it with different cable lengths” says Verhoeff. The excess cable is simply stored suitably behind the crane.
Once again it is easily assembled. “It does not need bolting together as all the connections are pin joints. The heaviest component weighs 90kg, and this can be carried with a special trolley, even up stairs. Two people can assemble it in two days and disassemble it in one. We have used it for building maintenance installations, putting solar panels on a train station roof and air-conditioning units atop high-rise buildings. The maximum weight it can lift is 6t. It is a versatile machine that can work in a lot of difficult-to-reach areas. For mobile or crawler cranes you often require permits for road closure and the like, which you do not need for the LSC.”
“We have to teach engineers that this great concept still exists” says F&M Mafco’s Kittle. “One problem we have experienced is finding capable operators. So now as we are expanding our fleet we are outfitting them with joystick controls like on a standard crane, so they are operated exactly the same as any other crane.
“Any crane has advantages and disadvantages” he says. “Tower cranes and mobiles took over many of their tasks in the ‘70s and a lot of companies forgot about derricks. Now awareness is coming back. People we lost a generation ago are returning. It is not quite a resurrection but we’ve seen a definite increase in interest.”