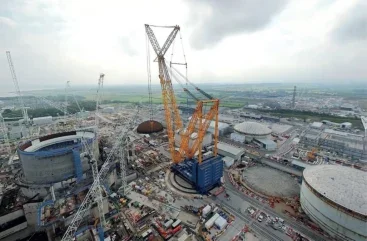
Loads are getting heavier. Cranes are getting bigger. And the market for big cranes and heavy lifting is getting bigger, too.
Consider for example two market-leading names: crane manufacturer Liebherr and heavy lift and transportation specialist Sarens. Liebherr’s latest heavy-lift crawler crane is its LR12500-1.0 which can lift 2,500 tonnes. It is not quite its biggest crawler – it has its LR13000 which Liebherr claims as the most powerful conventional crawler in the world. It has, as the name suggests, a capacity of 3,000 tonnes. Even so the LR12500-1.0 is a giant of a beast. It has been designed, says Liebherr, as ‘an economical crawler crane for global projects’. Sarens bought its first one last year, not long after it was introduced.
This year Sarens bought two more. Given the huge size of the crane, two immediate questions arise: why does Sarens need three of them, and what will they be used for?
“We see a significant need for this type of crane and the type of job it can perform,” says Yannick Sel, Sarens’ group commercial director of projects. “This is why we decided to increase our arsenal.”
And their uses? “We are particularly focusing on jobs in renewables for these new 2,500 tonne cranes. Handling offshore wind turbines at ports is also becoming an important business segment as the weights of components continues to rise. Apart from lifting large components for the offshore wind sector, the LR12500 -1.0 is perfectly suited for the petrochemical industry and port handling work. The crane is easy to transport thus reducing the rigging and transportation cost and time when deployed for global projects.”
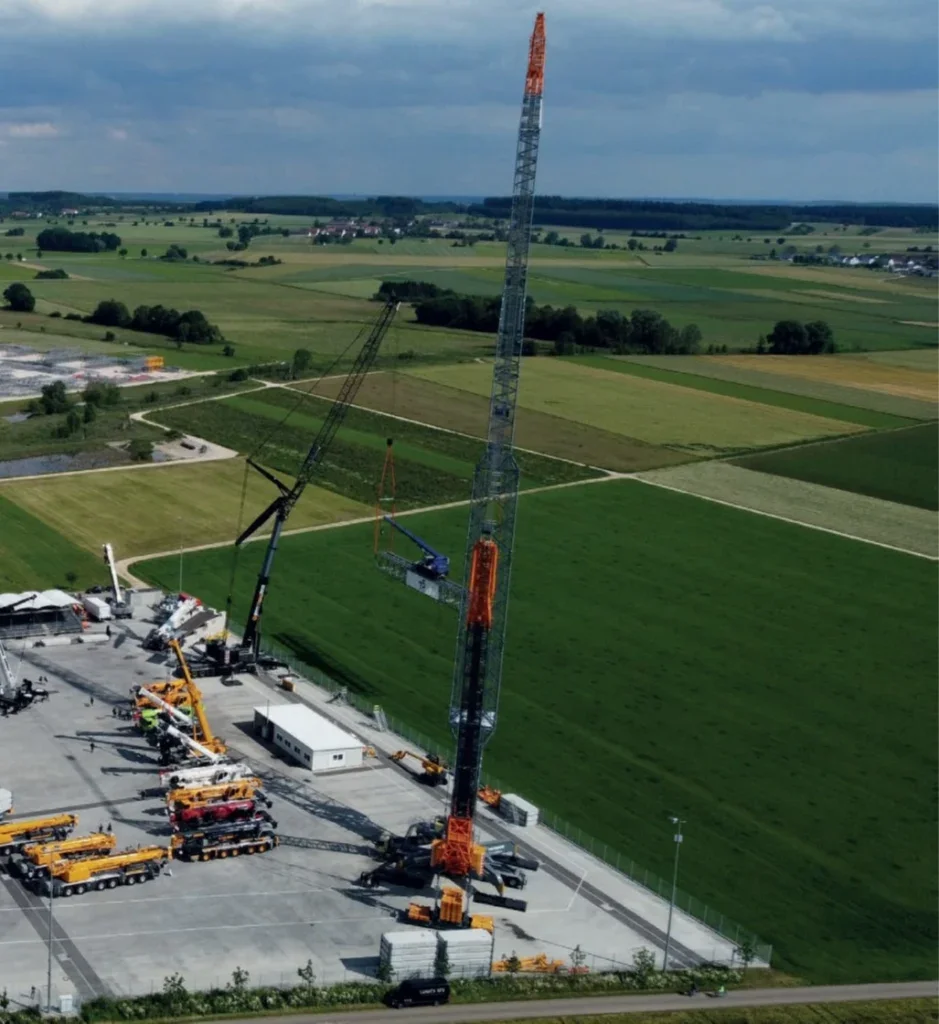
Another customer for the LR12500-1.0 is Denzai in Japan. Since its foundation in 1972 the Denzai Group has become one of Japan’s largest heavy lifting and specialised heavy transport companies. And it is one with ambitions claiming its aim is ‘to become the world’s premier company in heavy lift and specialised transportation engineering’.
To that end it bought its LR12500-1.0 in April this year, to be delivered in October.
The purchase makes it the only owner and operator of the machine in Japan and the Asia-Pacific region. It will start operation in October at S-OIL’s Shaheen Project in Ulsan, South Korea. After that, Denzai plans to operate it in Japan and overseas.
Sarens’ Yannick Sel mentioned above that the crane is well-suited for port handling work. That would appear to be especially true for Denzai, who plans also to use it in the offshore wind sector. ‘As the amount of electricity generated by offshore wind increases, the height and weight of offshore wind turbines are becoming larger and larger,’ says the company.
‘The construction of even larger offshore wind turbines is expected to become impossible with the 1350-tonne crawler crane, which is the largest crane we currently own. In the Round 1 and Round 2 offshore wind turbine construction projects currently underway in Japan, the weight of the towers will be different from the European specifications, and the Japanese specifications are expected to be even heavier.’
Another factor adds to that suitability: ‘The working radius of cranes [for offshore wind] is expected to be larger than in Europe, because some Japanese ports have less strong wharves than those in Europe, and the cranes must be installed further away from the wharves,’ Denzai explains. ‘Furthermore, if the nacelle weight exceeds 800 tonnes it will be impossible to lift the nacelle from the far side of the vessel with a single 1350-tonne crane; and we estimate that two 1350-tonne cranes will be required. On the other hand, the LR12500 to be introduced at this time can lift up to 951 tonnes with a working radius of 48 metres; that means it can satisfy the requirement with only one crane. The decision was made to install the crane to meet the height and weight requirements for offshore wind power in Round 1 and Round 2, and to assemble and construct offshore wind components with the crane for the floating offshore wind farm that is expected to follow.’
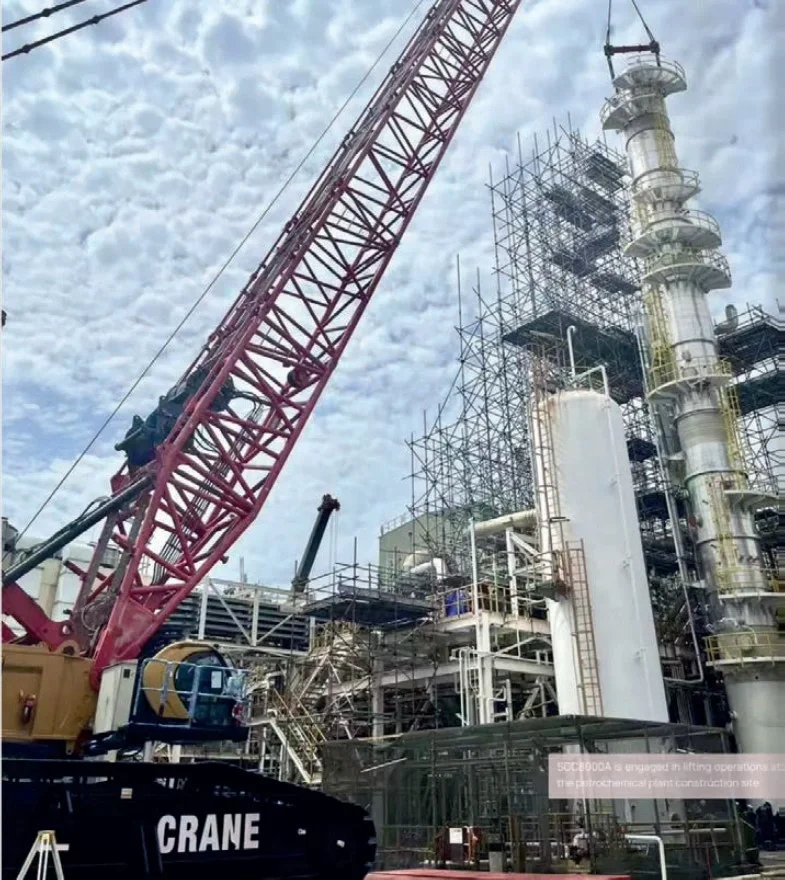
And earlier this month Mammoet announced it, too, has purchased an LR12500 which it will use on future energy and infrastructure developments (see news p10 for further details)
Sany is another global-player in crane manufacture and ports also feature as an application for its flagship heavy-lift crane. The SCC8000A has a capacity of 800 tonnes and it, too, has penetrated the APAC market. It has achieved sales in India, Vietnam and South Korea as well as Saudi Arabia and Australia.
In October 2023 Sany sold one unit to Malaysia’s leading lifting service provider, Public Crane. By early 2024 the same client had placed an order for a second unit. Both will support shipyard operations. Also this year East Malaysian client Harbour- Link received an SCC8000A to support development of a port infrastructure project in Sarawak.
RING CRANES
These giant cranes are all crawlers. There are still heavier lifters. In its fleet Sarens also has a series of ring cranes, such as ‘Big Carl’, the SGC-250 machine currently at work constructing the UK’s Hinckley Point C nuclear power station. It was launched in 2018 and is currently the largest landbased crane in the world. It has a maximum load moment of 250,000 tonnes, allowing it to lift 5,000 tonnes. At a radius of 100 metres it can lift 2,000 tonnes.
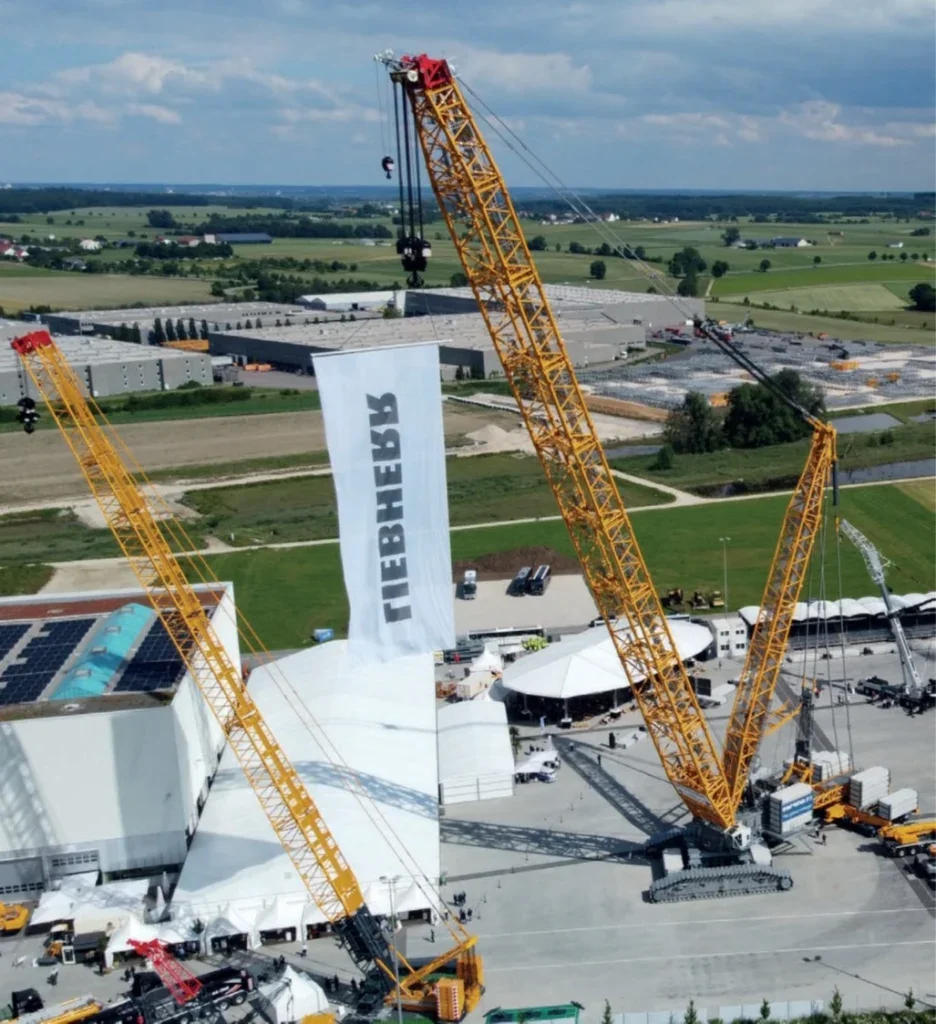
It is the third generation of the SGC series. The first was the 120,000TM ‘Big Benny’; the 140,000TM ‘Big Benny XL’ SGC-140 followed, with 45% stronger capacity. The most recent addition is smaller… but only in comparison: the SGC-90 has a capacity of 90,000TM but is intended for projects in the nuclear, logistics, construction and, again, offshore wind sectors.
It is nicknamed ‘Little Celeste’ and is fully electric, fully silent, and the first and only one of its kind. The entire series is the product of Sarens’ in-house engineering and technical teams.
Sarens has a place for both types of heavy lifters. “The high lifting capacity of the LR 12500- 1.0 is the outstanding feature for us,” says Sel. “The new crane will enable us to close the gap between our crawler and ringer cranes.”
How many more LR12500 cranes Sarens will buy – and Liebherr will be able to sell, to them and other customers – is going to depend on demand and need for their use. Is Sarens planning to add more? “We are always open to expanding our fleet as we need to remain the reference point for our clients,” says Sel, not committing himself. But he does say that worldwide demand for heavy lifts is increasing: “The demand is robust and growing. We see a significant increase in requests for our services across various industries. The primary sectors driving demand for heavy lift are infrastructure, energy, and construction.”
Specifically, he says, Sarens is seeing substantial activity in renewable energy projects, including wind installations, large-scale infrastructure projects like bridges and highways, and significant construction ventures.
“The worldwide demand for our very heavy lifters, including giant ring cranes, is substantial and growing. As projects grow in complexity and scale the need for cranes capable of lifting and manoeuvring massive components is increasing. The global shift towards renewable energy and the construction of larger and more ambitious infrastructure projects are key drivers of this expansion.”
Is there a market for five of their huge ring cranes, or ten, or more perhaps, worldwide? “Yes, we believe there is room in the market. Only time, however, will show,” Sel says.
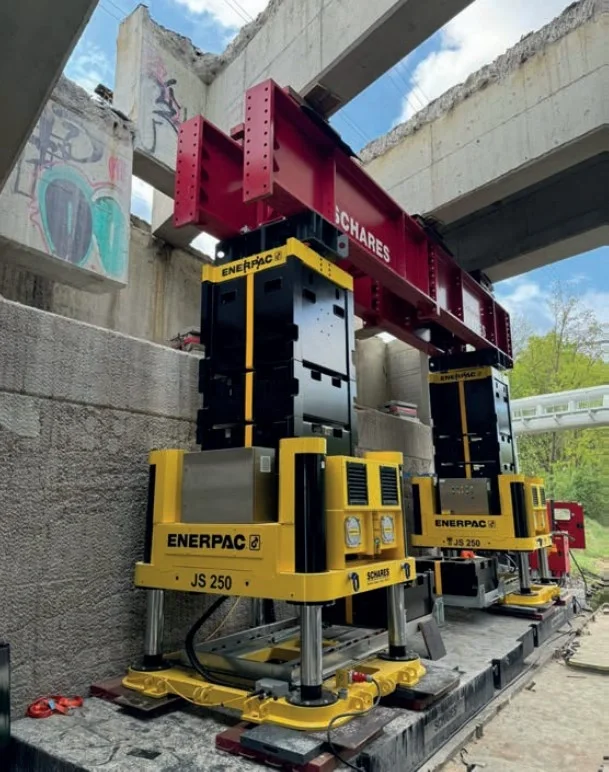
With its SGC-250, Sarens has the largest land-based crane in the world. How much bigger can such cranes get? How much heavier loads can they take? Are we approaching the limits of what can actually be lifted from the ground? Are loads reaching now their practical limits, in terms of weight? Have we reached the point where even greater capacity cranes are simply impractical or not economic – or where ultra-heavy loads can be moved by other means – e.g skidding, jacks, or in several smaller modular pieces?
“Loads are still increasing,” says Sel. “We have not yet reached the practical limits in terms of weight for cranes. However, our industry is constantly evaluating the economic and practical aspects of developing even greater capacity cranes. Alternative methods like skidding, jacking, or modularising loads are sometimes more practical, but each method has its own set of challenges and is selected based on projectspecific requirements.”
BRIDGE LIFT
Neatly exemplifying this was the heavy lift and move of a bridge in Germany carried out by German heavy lift contractor Autokrane Schares. The company recently purchased an Enerpac JS-250 jack-up system and used it in the removal of a section of the Marggraff bridge over the Britzer Verbindungs canal in Berlin.
The move was challenging due to space restrictions. The bridge was built in 1965. It consists of three sections, adjacent and parallel to each other.
Autokrane Schares was responsible for removing the first section, which was 60 metres long and weighed 1500 tonnes. Overhead power lines, and lack of space at the busy road intersection, meant that a jack-up system was the preferred solution.
To position the JS-250 jack-up tower bases on the narrow canal towpath a section of bridge deck was removed at each end of the bridge and the jack-up bases were lowered onto the path. The header beams followed. Once the jack-ups and header beams were in position further jack-up tower barrels were added from a pontoon. Synchronous lifting of the bridge section was achieved using two interconnected split flow pumps.
The bridge deck was removed in three pieces, each 60 metres length and weighing between 450 and 630 tonnes.
For each stage the JS-250 raised the bridge deck three metres clear of the bridge abutments. Two pontoons were positioned underneath, and the bridge deck lowered onto steel frames resting on support structures. The bridge was then floated to the side and lowered on to SPMTs for transportation by road to a nearby site for dismantling. The task was competed over a two-week period.
The close proximity of a busy highway meant that precise operation of the JS-250 was critical. As standard the JS-250 features an adjustable top barrel, including a double-acting lock nut cylinder with swivel saddle, for each of the four lifting towers. The cylinders can be extended, allowing precise adjustment of the starting height of each leg, ensuring safe and stable lifting.
“Space restrictions at the site made this a very challenging project,” said Max Boere, team leader SPMT at Autokrane Schares. “The compactness and ease of set-up, together with accurate synchronised lifting, made the Enerpac JS-250 a perfect fit for this project.”
Engineered Rigging is another company that has added to its Enerpac fleet. In its case the addition was an additional Enerpac SBL500 Hydraulic Gantry. The gantry has a lifting capacity of 500 tonnes and is designed for infrastructure projects at ports, railways, power and industrial plants – basically any civil or commercial construction application where traditional cranes will not fit and overhead cranes are not an option.
Each of the gantry’s four legs has internal three-stage doubleacting hydraulic cylinders and selfpropelled steel wheels for travel on skid tracks. Each lifting tower has a counter-balance valve, stroke sensor and pressure transducers.
Technicians can remotely operate the lifting towers either independently or as a group of two, three or four towers – wirelessly with the Intelli-Lift control system or, if site conditions dictate, via a control cable. Additional features of Intelli-Lift include load and height readings for each tower, and synchronised lifting and travel.
As Sel says, even heavier loads may be lifted in the future. There is, though, another possible limit that we may now be reaching: that of size. Large but not necessarily hugely heavy loads are transported; they are moved on skids, or on SPMTs, and sometimes over many kilometres. The physical access required to transport such things – removing street furniture, negotiating low-headroom bridges, raising power cables and the like – must surely impose some kind of limit to what can sensibly be moved? Is this a challenge? What does he think will happen her over the next five to ten years?
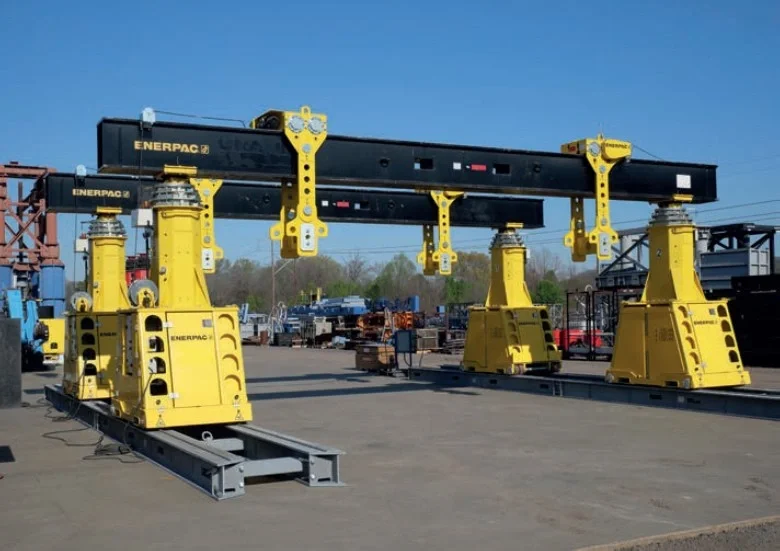
“Size and volume are indeed approaching logistical limits,” he says, “posing significant challenges. Transporting large components often requires extensive planning and infrastructure adjustments. Over the next five to ten years, we expect advances in modular construction techniques, improvements in transportation infrastructure, and the development of more sophisticated logistics planning tools to help address challenges that may arise.”
Transport infrastructure may deliver better roads able to bear higher axle loads, but presumably will deliver with it more in the way of overpasses, overhead traffic gantries, foot- and cycle-path bridges and so on. There will be more obstacles to negotiate rather than fewer. “We also anticipate an increase in on-site assembly to reduce the need for transporting oversized loads,” says Sel, addressing that problem. The cranes themselves are ahead of the game here: “Most of our heavy lifting machines are containerisable, which is a very good answer to the logistics challenges of moving around such giant cranes.”
So, giants will still rule the earth… but they may be giants that can be split into smaller parts.
STRONGEST LAND-BASED CRANE EVER FROM MAMMOET BEING ASSEMBLED
Engineered heavy lifting and transport specialist Mammoet is assembling what will be world’s strongest land-based crane, the SK6000 ring crane, at its Westdorpe facility in the Netherlands. All parts have now been delivered to the site; initial works include assembly of the crane’s base frame, power packs and control room. Mammoet’s auxiliary cranes are supporting the build, including two 250-tonne crawler cranes and a 140-tonne Gottwald mobile harbour crane.
The crane is designed to deliver a maximum capacity of 6,000 tonnes with the capability to lift components up to 3,000 tonnes to a height of 220 metres. It will offer full electric operation. Its intended use is for offshore wind projects: it will be used to lift latest generation offshore wind turbine components, which are getting ever bigger to achieve higher yields.
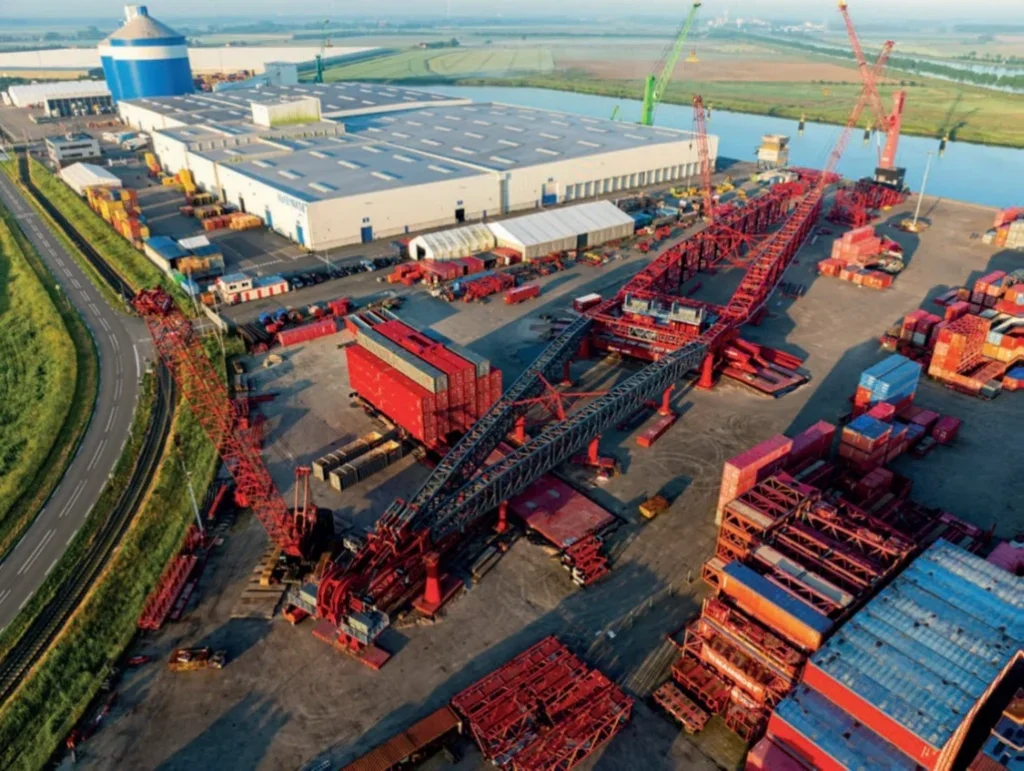
‘Offshore wind farms are moving to deeper waters and reaching higher to find stronger wind flows,’ says the company. ‘As a result, the scale of turbine and foundation components, in both floating and fixed offshore wind farms, continue to grow.’
Bottom-fixed jackets and monopiles weighing between 2,000 and 3,000 tonnes are now common; next-generation turbines will be even larger. Generating 15MW and 20MW, their towers will rise to 150 metres and beyond.
Hence Mammoet’s development of the SK6000. Mammoet says that, with it, customers can build more efficiently in larger pieces, shrinking the logistics, integration and mobilisation phases of projects. ‘In the oil and gas sector the crane helps new builds and expansion projects to benefit from economies of scale on a level never before seen,’ it claims.
The SK6000 builds on the popularity of Mammoet’s established SK190 and SK350 series cranes, and in the construction of new modular nuclear facilities. Koen Brouwers, project manager for the SK6000, said: “This is a thrilling new chapter for Mammoet and modular construction in heavy industry, as we see the SK6000 taking shape. It will offer a hook height, outreach, and lifting capacity far in excess of any crane on the market.”
Cranes Today will be visiting Mammoet’s SK6000 in Westdorpe at the end of August; stay tuned for more on this crane…