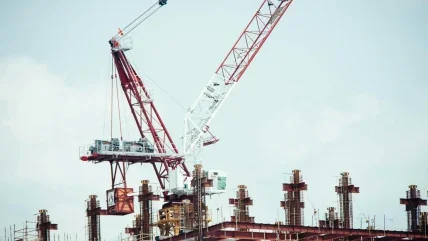
The development of fibre rope in the lifting industry has been a gradual process, over a number of years. Initially, fibre rope manufacturers focused on the offshore sector. In the oil and gas industry cranes are often used to lower heavy loads, such as blow-out preventers, to the seabed. When you are working deep underwater, the weight of steel wire rope can quickly surpass the lifting capacity of cranes and winches. Fibre ropes, designed to be neutrally buoyant in water, allowed these contractors to lower and lift loads, to any depth.
Adopting fibre rope on construction applications took longer. Early ropes were prone to stretching, and could be pulled out of shape under tension. That meant that they could not be easily spooled onto a Lebus-style drum. On a boat, where rope could be stored in loose loops on or under the deck, this was not a problem. On a tower or mobile crane, with limited space, this was a major challenge.
Manufacturers initially considered approaches that would control the tension of rope on the drum. A tensioning device would sit in front of the drum, maintaining a consistent tension, ensuring that the rope maintained its shape and spooled correctly.
This approach never went into production on an onshore crane. Instead manufacturers like Manitowoc and Liebherr worked with suppliers like Samson and Teufelberger to develop fibre ropes with similar spooling capabilities to wire. This research helped solve another problem faced on land: that ropes would stretch, making it more difficult for operators to position loads.
Another challenge was developing discard criteria for fibre. The process of inspecting steel rope requires expertise but is well documented. Technicians and inspection specialists can examine a rope for ‘bird caging’, or count the number of broken strands on the outside of the rope, among other checks.
The differences between steel wire and fibre meant that the same criteria could not be applied. And the rapid development of the ropes meant replacement criteria differed between manufacturers.
This changed in 2017, when the European equipment manufacturers’ group the FEM introduced FEM 5.024 Safe Use of High Performance Fibre Ropes in Mobile Crane Applications. In 2021 ISO used this best practice paper as the basis for a new international standard, ISO/TS 23624:2021(en) Cranes — Safe use of high-performance fibre ropes in crane applications.
Gerhard Kaupert, Manitowoc’s representative on the FEM, and one of the developers of the original guidance, said, “The new ISO Technical Specification gives state-of-the art guidance on modern high-performance fibre ropes. It replaces the groundbreaking FEM document, [which] for the very first time provided guidance on design and discard criteria for high-performance synthetic fibre ropes.
“The new ISO specification builds on the experience made with the FEM guidance document and expands the scope to cover different crane applications. It incorporates the knowledge of the worldwide crane industry of the ISO TC96 Cranes standardisation group. This is a further key step supporting the use of modern high-performance fibre ropes in cranes.”
The development of the guidance and subsequent technical specification may give crane owners more confidence that they can take advantage of the additional lifting capacity of fibre rope, safe in the knowledge that their maintenance staff and third party inspectors have a welldocumented means of confirming a rope’s condition.
LIKE-FOR-LIKE
Wolffkran invested in fibre rope manufacturer Trowis in 2019. The fruits of this collaboration were on display in Munich in October, when the tower crane manufacturer demonstrated the Chemnitz rope specialist’s new product, chaRope, at Bauma on its new 6021 FX flattop. When the rope goes on sale in August, it will be offered as an option on Wolff Clear cranes, the new Wolff 21 FX cranes and the Wolff 8033.16 Cross.
The new rope is designed to replace steel wire ropes of the same load-bearing capacity and diameter. This means it can – in general, Trowis say – be fitted on standard equipment, with no changes of sheaves, hoists, or load capacities. The fibre rope is designed in a similar way to wire counterparts. Layers of rope are packed together, for maximum density, using a hightech fibre material. These layers are separated by inner and outer plastic sheathes.
The outer sheath protects the load bearing core rope. It prevents damage from abrasion, UVradiation, dirt and moisture, and prevents lubricant leaking out of the rope. The sheathes essentially separate the load bearing core from the surface. That means that any damage occurs to the surface, where it is visible and will lead to the rope being discarded, well before the rope loses its loadbearing capacity.
The dimensionally-stable rope, which can be spooled on standard drums and over the usual sheaves, can be up to 80% lighter in operation. This means that lighter hook blocks can be used. It has been designed in line with the new ISO technical specification.
The rope was shown at Bauma fitted to Wolffkran’s new Wolff 6021 FX, one of three cranes in a ‘family’ of 141–200t/m class flattops. The crane was shown alongside a Wolff 7021 FX, and the trio of cranes is made up by the Wolff 6521 FX. The cranes can be configured with 60, 65 or 70 metre jibs, and maximum lifting capacities of 8.5, 10.5 or 12.5t, on 1.5 or 2.0m tower connections. They share numerous components, Wolffkran says, speeding delivery times, reducing the number of components that must be held in stock, and simplifying the training needed by rigging crews.
All of the cranes in the 21 FX family can lift 2.1t on the jib tip in normal operation, and 2.3t when the Wolff Boost function is activated. The option of installing them on Wolff’s new 1.5m TV 15 tower system makes them suitable for use in countries with narrower lift shafts: this has been a focus for many tower crane markets, as they build their business in growing markets like that in India.
The cranes promise compact transport and simple assembly, with 40m of jib on one truck, and 30m in a shipping container. Component weights have been kept under 7.9t, allowing the crane to be assembled with a 100t mobile crane, at a height of 40m.
A COMMON THREAD
Liebherr was one of the pioneers of fibre rope lifting, developing soLITE with Teufelberger.
Like the Trowis rope, this solves the problem of discard criteria by using a multi-layer sheaf. The exterior of the rope is made up of multicoloured braided material. A rigger or specialist can easily spot abrasion in this. When the red core is visible the rope should be discarded but still maintains 100% of its lifting capacity.
Liebherr has been demonstrating its confidence in its fibre rope, with a programme called Fibre Care. Prices for the service start at €50 a month.
As well as offering support for users, they come with a six year guarantee that Liebherr will make up any difference between the costs of replacing a steel rope, and those of replacing a fibre rope. For users worried about training and cost, this should help ease their transition away from steel wire rope.
Another sign of Liebherr’s confidence in the technology came at Bauma, when the company demonstrated tower cranes with fibre rope across its range.
The new 1188 EC-H high-top is the largest standard crane in Liebherr’s range. Launched in Munich, it can lift 13.1t at the end of an 80m jib, and has a maximum capacity of 40t. Liebherr says that this helps demonstrate the benefits available when using fibre rather than steel.
RECORD-BREAKING CAPACITY
The fibre crane lifts 2.1t more at 80m, than is available on Libherr’s next largest crane, the 1000 EC-H, with steel wire rope. The new crane also lifts further, with the option of extending the jib to 90m, 10m longer than on the steel rope crane.
“The 1188 EC-H 40 is our first high-top crane with fibre rope technology,” says Markus Kinateder, product manager, Liebherr-Werk Biberach. “We’ve increased the performance capacity of our EC-H series even further with this crane and can now offer our customers even greater support for the implementation of large and custom projects,”
Cranes like this are used for some of the biggest civil engineering projects: they’re suitable for pouring large volumes of concrete on dams, for example, or for handling other building materials across large sites. Increases in capacity, achieved through using fibre rope, should have a real impact on these large, long term, projects.
LUFFING WITH FIBRE
The benefits of fibre rope can be seen lower down the capacity scale. At Bauma, Liebherr showed its first luffer with fibre rope for hoisting (Liebherr and Wolffkran have both experimented with the use of similar materials for luffing pendants, on tower cranes and on crawlers; these, like the rope, can be easier to handle when rigging the crane).
Luffers are typically used on projects which require vertical reach, in constricted urban environments. The luffing jib both removes the need to oversail, and extends the jib end up above the cab, limiting the need to jack cranes.
LONG HOISTING ROPE
The new 258 HC-L 10/18 Fibre demonstrates the benefits of fibre when working with a very long hoisting rope, as is typical for these cranes. Liebherr says it offers 43% more capacity on the jib head, and 25% higher maximum lifting capacity, than is offered on the comparable 230 HC-L 8/16 steel wire rope crane.
The cranes can be set up at virtually any height. The higher they go, the longer the rope, and the more the benefits of fibre can be seen. “When using our Fibre cranes, the greater the hook height is, the more substantial the possible increases in load capacity are,” says Kinateder. The company points out that reduced wear of materials and exceptional durability contribute to the machine’s particularly long service life and, therefore, its cost-efficiency.
FIBRE FLAT-TOPS
Liebherr has also upgraded its flat-top range adding fibre to many models and updating its two first fibre crane models.
The 300 EC-B 12 Fibre has a 70m jib and delivers a lifting capacity at the jib head of 3.25t. The steel rope version, the 270 EC-B 12 with a 70 metre jib, has a lifting capacity at the jib head of 2.85t. Powerful hoist units and pure two-line operation make both machines particularly efficient, Liebherr says. The new cranes will replace the existing Liebherr 250 EC-B and 278 EC-B Fibre models.
At the top of the flat-top range, Liebherr introduced the 520 EC-B 20 Fibre. This crane offers a capacity of 2.9t at the end of its 83m jib, and can reach a freestanding height of around 96m. With a maximum capacity of 20t, Liebherr says the crane will be ideal for applications that use heavy prefabricated concrete modules, an increasingly common approach to the housing crisis that afflicts cities around the world.
Falcon launches modular battery system
UK tower crane supplier Falcon Cranes has launched Northvolt Voltpack, a modular and scalable energy storage system designed to power cranes and other equipment on construction sites.
The Northvolt Voltpack is made up of individual battery modules that can be combined to provide between 281kWH and 1,405kWh of power. The system works by storing energy from a mains supply or renewable sources in a battery. This stored energy can then be used to power cranes and other equipment on construction sites, reducing the need for diesel or petrol generators.
It also showcased Northvolt Voltpack alongside its Punch Flybrid System at recent UK trade show Vertikal Days.
Battery-powered tower cranes in London
Ampd Energy, a player in the energy storage industry, in collaboration with Select Plant Hire, a subsidiary of Laing O'Rourke, has deployed three of its zero-emission ‘Enertainer’ lithium-ion battery energy storage systems at London's high profile Olympia Redevelopment.
Ampd Energy says that its modular lithium-ion battery solution has the potential to revolutionise the industry by electrifying building sites and driving down carbon emissions
The deployment of the Enertainer systems at the Olympia Redevelopment is estimated to save 192 tonnes of carbon over 12 months, reduce operating costs by 70%, and eliminate the equivalent air pollutants of 975 cars when compared to standard diesel generators.
Ampd Energy claims that, over the life of the project, the Enertainer will be more cost effective than diesel generators, as well as saving space and labour time.
According to Ampd Energy, compared to fossil fuel generators the Enertainer reduces carbon footprints by up to 90%, is up to 30 times quieter, emits zero air pollutants, and eliminates diesel handling and usage risks. It requires minimal maintenance and zero refuelling downtime.
Tower crane usage monitoring
London,UK-based software company 1Guava has launched its tower crane usage monitoring program in the UK. 1Guava says the program can increase on-site productivity, promote proactive scheduling, and deliver intuitive reporting to support on-site operations by capturing vital utilisation data on-site while capturing key events such as winding off, maintenance/ breakdowns and idle time.
1Guava launched the program at the Vertikal Days trade show in the UK where it gave demonstrations of the software's capabilities in real-time.
Expansion for BKL
German crane rental fi rm Baukran Logistik (BKL) has expanded its presence in Germany with the opening of a new location in the Rhine/Main area. This strategic move aims to enhance BKL's ability to provide crane services to customers in the south and east of the Frankfurt Metropolitan Region. The new subsidiary is situated on the B26 with easy access to the A3 and B469.
Jörg Hegestweiler, managing director at BKL, emphasised that the primary objective of the expansion strategy was to maintain strong relationships with customers throughout Germany and Europe and that the expansion represents a logical progression in their efforts to broaden the reach of their crane solutions in the Rhine/Main area.
Founded by Jürgen Volz in 1969, BKL is a familyowned company with over 50 years of experience in the industry. It currently employ approximately 330 staff across their seven locations spanning the north-south axis of Germany.
As one of Europe's largest manufacturerindependent, full-service providers of crane solutions, BKL has a fl eet that includes over 500 tower cranes, more than 100 mobile cranes, around 20 mobile construction cranes, and over 70 trucks, loader cranes, and low-loaders. In the previous fi nancial year, the company generated sales of 83 million euros.