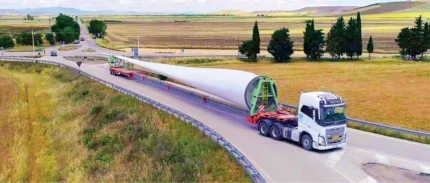
Of all the transformative energy sources wind power is the most visible. It is transforming landscapes onshore and at sea. It is successful: last year wind generated 7.8% of the world’s electricity; for the UK, in October 2023, the figure was 33%. Wind does not carry the waste disposal problem of nuclear, nor its huge decommissioning issues and costs. The long lead-in times that have bedevilled the UK’s Hinckley Point C station are unknown to it. (Construction of Hinckley Point C began in 2017; current estimated costs are over £41 billion; and the project is still not forecast to generate power until 2029.) Wind towers can go up far faster; not exactly overnight but they are built within months or a few years of construction beginning. What is there not to like?
But they do have one problem: height. Hub heights of current onshore wind towers are about 98m metres (2022 figure). Next generation towers of 199 metres have already been announced by Danish wind company Vestas.
Offshore towers in their latest iteration are taller: 260m for seabed farms, and still taller for projected floating windfarms.
There is a simple, unavoidable reason for this: efficiency. A large rotor catches more wind; and the higher above the ground you go the harder and more consistent the wind is. The power produced by wind turbines scales with the square of blade length and increases with height.
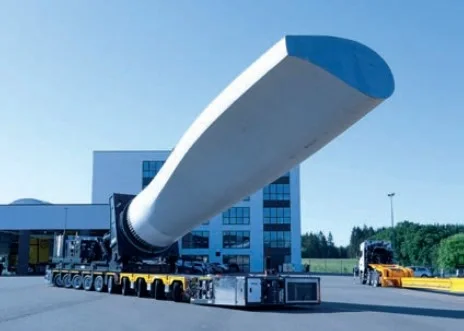
So taller towers and longer blades are the future – and, indeed, the present – of wind power. Which means that building the ever-taller towers, transporting the everlonger blades from their factory to that tower, and lifting those blades to ever-greater heights to attach them to their turbine, become ever more of a problem.
Transport experts and lifting experts are working on it and finding solutions. These solutions range from standard machinery built bigger, via engineering masterpieces of design, to flights of imaginative ingenuity or even fancy.
Onshore problems are very different from offshore; and the solutions are very different also.
Here we shall consider land-based wind farms and cover offshore wind in its own dedicated feature later in this issue (see page 30)
For land-based construction some crane companies are investing in very large crawler machines for lifting, as the example of Verschoor (see box p20) illustrates. Others are going for rough terrain cranes, such as the Terex TRT35 at work in South Africa (see box on p25).
But on-site erection of components is only one challenge: getting those components to an onshore site is another. Collett’s experience in Ireland – see box on p26 – is an example of the effort and ingenuity required for today’s sites and scales.
CONVOI EXCEPTIONNEL
Specialist equipment is being designed for carrying blades – and since current blades can be 70 metres long the equipment needs to be exceptional to say the least.
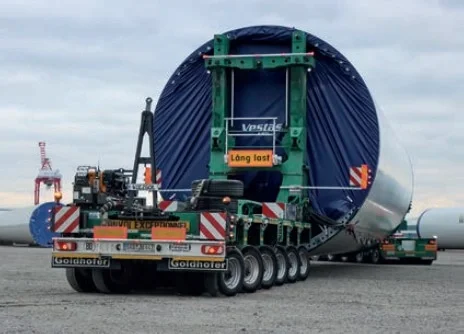
The blade lifter design is an example. It holds the blade at just one end; the tip sticks up in the air supported only by the strength of the blade. Hence it is easier to negotiate corners – and indeed hairpin bends; the blade tip can hang far over the edge of the roadway.
An added complication is that blades are designed to catch the wind – so the precise angle of rotation along its axis at which the blade is held matters a lot.
The BladeMAX1000 blade lifter from Cometto, part of trailer specialist Faymonville, has a load moment of 1000 metre-tonnes. This, the company claims, is the highest value on the market.
The manoeuvrability allows blade transport through winding mountain passes, challenging urban areas, and densely forested regions.
Adrian Zingan, product manager at Cometto, explains what is important in use. “The rotor blades can be raised by up to 60 degrees if necessary and also rotated by 360 degrees around their own axis. It all depends on the obstacle on the road section and the prevailing wind direction. Optimum handling stability is guaranteed by the similarly patented stability control system. Several sensors transmit data in real time, which is processed by a central control unit. In this way, all safety-relevant information is constantly monitored.”
In June, the Faymonville Group (which also owns the MAX Trailer brand) recently held a ‘WindMover Days’ event, covering four days and devoted entirely to wind energy transport.
Around 250 industry experts from the wind power sector came together to get a close look at the latest high-tech material on the factory premises in Luxembourg.
At the event the company showcased its four-axle WingMAX flatbed trailer, designed for the longest, XXL sized, blades.
“The enormous stroke at the gooseneck and the longest available four-fold telescopically extendable loading platform, as well as the gooseneck length, which is compatible with five-axle tractors, and the 19.5” pendle axles are real assets for the wind power industry,” says Julian Thelen, Faymonville’s head of sales Europe. “The sliding load support for the blade tip frame permits shortening of the flatbed trailer even under load. This refinement is a real help when passing through winding stretches of road.”
Faymonville also showcased at WindMover Days: a two-axle dolly and a four-axle self-steering trailer with a blade adapter; a Cometto BladeMAX1000; a ten-axle Faymonville ModulMAX AP-M heavy load module; a 4+7 self-steering trailer combination with a tower adapter; a 3+5 VarioMAX low loader; a MultiMAX 6-axle semi low loader; a 12-axle Cometto MSPE 48T; and a fouraxle MAX410 ballast trailer from MAX Trailer.
A video showcasing Faymonville’s wind portfolio as seen on display at WindMover Days 2024 can be seen here
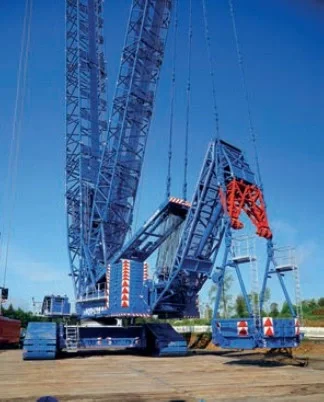
Goldhofer has been equally innovative its tower transporters. Its latest, the RA 2-110, can now transport tower sections with weights up to 110 tonnes and diameters up to 6.8m. The increased payload comes from the combination of a front bogie in the form of a four-axle dolly with pendulum axles and a heavy-duty THP/SL-S (285) module as the trailing dolly.
This vehicle concept meets the additional safety requirements specified by the Danish wind turbine manufacturer Vestas.
Instead of the usual configuration with two free-turning devices – that is, goosenecks at the bogie and at the trailing module – the new system has only one freeturning device, which is located at the front of the unit, between the front tractor dolly and the tower adapter. The rear tower adapter is mounted directly on the heavyduty module.
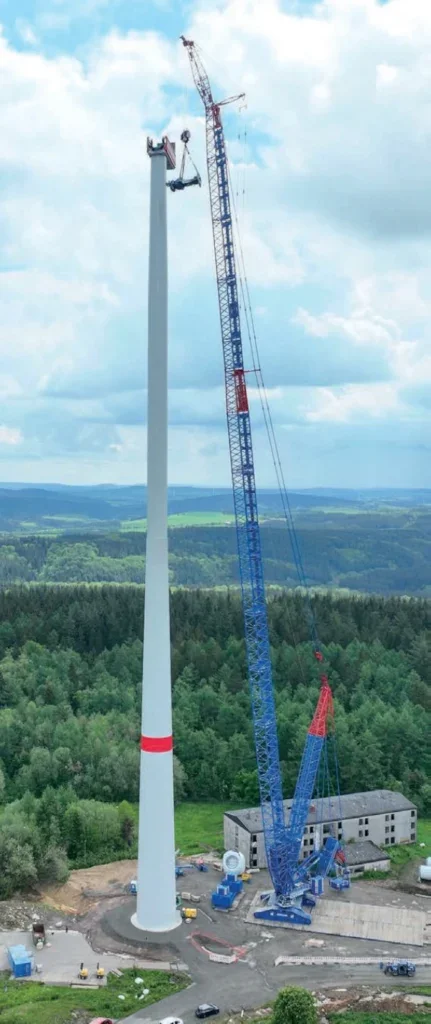
Compared with a completely free-turning system Goldhofer claims this solution delivers improved lateral stability for greater safety, even at high tilt angles.
VERTICAL REACH
After transport has been accomplished, on-site construction, and then on-site maintenance, follow. Both require extremes of high lifting, and therefore cranes with exceptional vertical reach.
As an example, at the end of May 2024 crane company Hofmann, based in Paderborn, Germany, used its brand-new (and very large) Liebherr LR 1800-1.0 lattice boom crawler crane to erect two high-performance 5.7 MW Nordex wind turbines at a hub height of 160 metres.
The site was a former military radio station. The crane had been purchased with wind projects especially in mind, and this was its first assignment. It has a lifting capacity of up to 800 tonnes and hook heights of over 200 metres: the rotor diameter of the Nordex turbines was 163 metres.
In April the crane system was transported from the Liebherr plant in Ehingen to Prüm and assembled there for the first time. It weighs around 900 tonnes and was moved on 60 low-loaders. To reduce the number of transport vehicles the six- and 12-metre long segments of the main boom, luffing jib and fixed jib can be pushed into each other three times.
The crane was assembled in the HSL4 boom configuration with a 165-metre main boom and a 12-metre lattice type fixed jib. The HSL4 is currently the most powerful system available for the LR 1800-1.0 for wind power installations. With a 174-metre main mast and 21-metre lattice type fixed jib, it can erect wind turbines with a hub height of up to 179 metres.
The crane was ballasted with 170 tonnes on the slewing platform, 70 tonnes in the undercarriage, and a further 400 tonnes of suspended ballast. The total ballast is only required for erecting the boom, after which the crane was able to carry out the lifts with only a small amount of ballast on the VarioTray.
A 68-tonne nacelle, a 74-tonne drivetrain, and 63-tonne hub had to be lifted to a radius of around 28 metres for each wind turbine. These comparatively easy-toassemble tower elements weighed 76, 73, and 51 tonnes respectively.
Once the first turbine had been assembled the team had to completely dismantle the LR 1800-1.0 and reassemble it near the second system 300 metres away. The task took six people and a 100-tonne auxiliary crane and was accomplished within a week. The heaviest components were the two 60-tonne crawler carriers. The slewing platform could then be quickly connected to the centre section of the chassis using Liebherr’s Quick Connection.
MOBILE MANOEUVRES
it is not only crawlers being used. Bremen-based Sommer Kranverleigh has added a Liebherr mobile crane, an eight-axle LTM 1650-8.1 equipped with 54 and 80 metre telescopic booms, to its fleet.
Sommer is planning to use it for the construction – and the dismantling – of wind turbines, as well as for industry and infrastructure projects. Its first job was to dismantle six old wind turbines in Schleswig-Holstein.
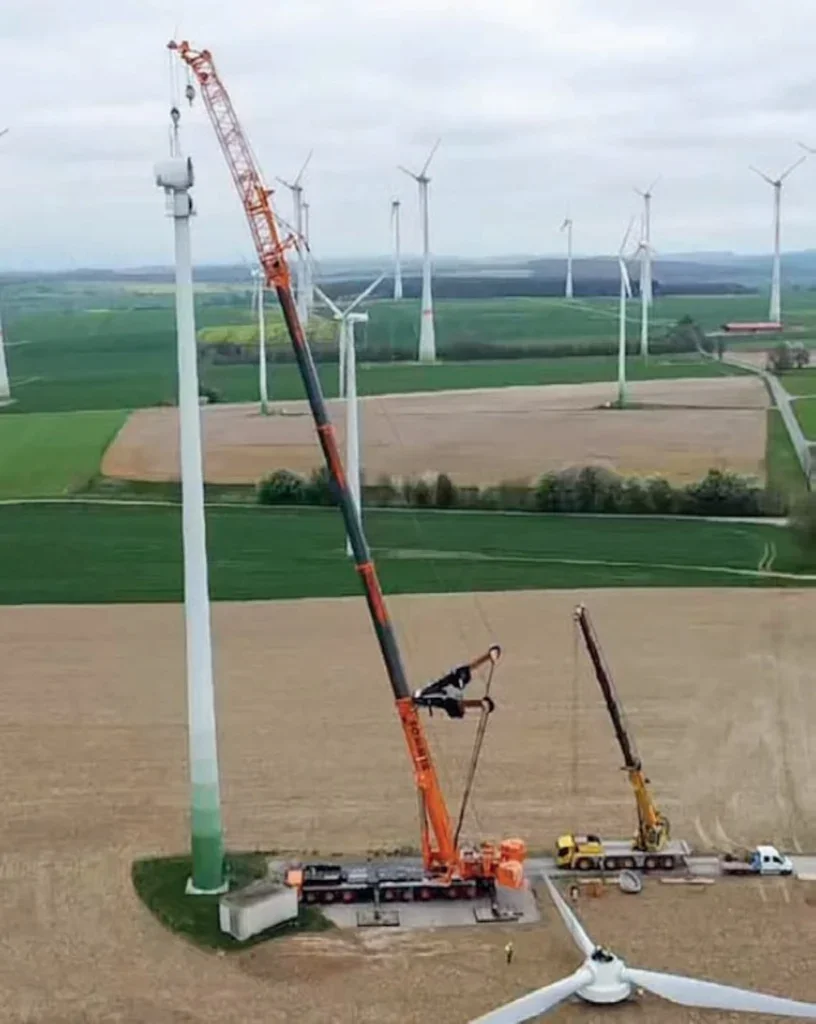
(They are to be replaced with eight higher, more powerful ones, quadrupling the capacity of the farm). “We were able to use the T5 configuration – the 80-metre telescopic boom – right from the start,” says managing partner Björn Sommer. “This has huge advantages, because with our LTM 1500-8.1 we would have had to build a luffing jib or at least a lattice type fixed jib. We also managed with just 75 tonnes of ballast. This reduces set-up and conversion times. Our staff are delighted with the simplicity of the LTM 1650-8.1.”
The rapid evolution of onshore wind power technology underscores the critical role that innovative lifting and transportation solutions play in the sector’s success. If onshore wind power seems to exhibit fewer construction challenges than offshore farms, they are still very far from easy. To compare their challenges with those of offshore windfarm construction turn the page to see part two of this article.
A GOLDHOFER FTV 870 TRAILER MOVES A 77M BLADE IN THE PERUVIAN ANDES
In mid-2023, Peruvian heavy haulage specialist Transportes Acoinsa S.A.C. transported wind turbine components for the Wayra II wind farm in the Ica region. Two Goldhofer FTV 850s were used to transport the 77-metre rotor blades for 31 wind turbines to their destination, making a total of 93 blades. To transport the blades Acoinsa opted used two Goldhofer FTV 850s mounted on 12-axle Goldhofer THP/SL modules.
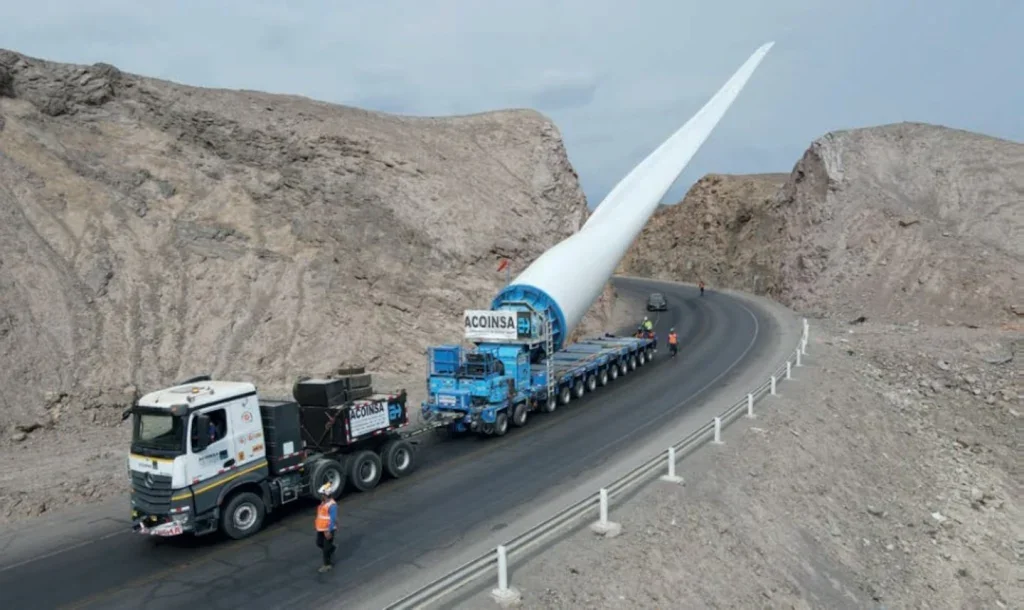
The 129 km route from the port to the Wayra II wind farm was demanding and involved narrow passages, built-up areas, power lines, roundabouts, trees and hairpin bends. These obstacles meant that the rotor blades were raised for 50% of the journey, with the FTV 850 offering a lift angle of up to 60°
LIEBHERR CRAWLER FOR VERSCHOOR IS NOW MOST POWERFUL IN ITS FLEET
Dutch crane and transport specialist Verschoor has expanded its fleet with the addition of a Liebherr LR 11000. It is the most powerful crane in its fleet and will primarily be used for wind work. The company has already used the crane to install two wind turbines at the Vanikum wind farm near the Dutch border.
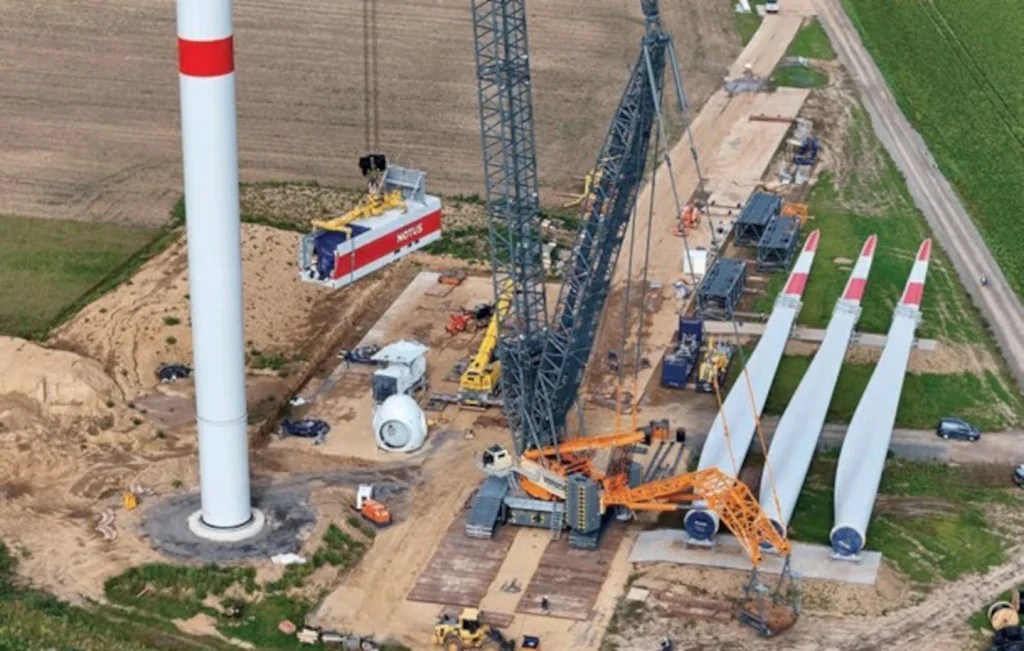
Verschoor purchased the crane in order to futureproof its capability to instal increasingly taller wind turbines with corresponding hub heights and heavier nacelles. For the work at Vanikum the LR 11000 assembled various components, such as the tower sections, nacelle and rotor blades, at a height of 169 metres.
The heaviest single component it lifted was the gearbox which weighed 117 tonnes. The crane was set up for the lifts with a 168-metre-long main boom and 15-metre lattice type fixed jib.
According to Liebherr, the LR 11000 is characterised by its economical transport concept and is designed for a transport width of 3.5 metres and a transport height of 3.2 metres. The V-frame with its adjustment distance of 17 metres moves the derrick ballast into the required position and reduces the workload for ballast handling.
“The lifting power of the LR 11000 is enormous,” said Maarten Verschoor Jr. who manages the company.
The ability to transport the crane within the weight limits also played a role in the company’s purchase decision. “It was also important for us to have crawler cranes in our fleet in addition to jib cranes,” added account manager Peter Verschoor.
HARSH CONDITIONS NO PROBLEM FOR TEREX RT AT SOUTH AFRICAN WIND FARM
Difficult terrain and extreme climate has lead South Africa-based Concorde Cranes to use a Terex TRT 35 rough terrain crane on a windfarm project in a remote, rugged and mountainous part of Northern Cape, South Africa.
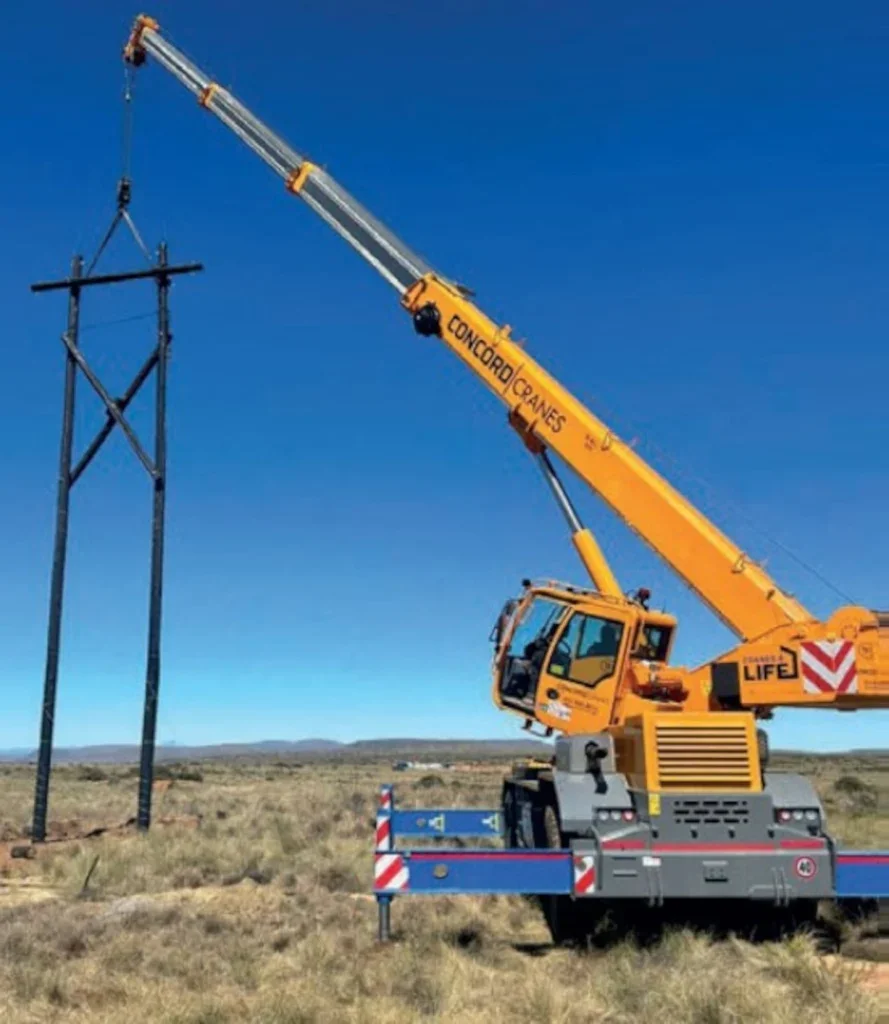
It took Midrand-based Concord Cranes 15 hours to transport the crane from Cape Town to the Coleskop Wind Farm site in Noupoort using a three-axle lowbed.
On site the cranes are moving concrete slabs to facilitate the project’s groundwork and then positioning 26 electrical poles required to channel energy from the wind turbines to the power station.
Concord Cranes’s engineers selected the TRT 35 for a number of reasons. Key was its ability to navigate and operate in the tough environment of the farm with its steep gradients and uneven ground conditions.
The crane’s width of 2.5m and a choice of four steering options enable it to tackle rugged terrain where conventional road infrastructure is absent, says Terex.
Being in a semi-desert region the cranes also have to endure an arid challenging climate defined by low rainfall, cloudless skies, and extremes of heat and cold between summer and winter.
For the work the TRT 35 has a 22m main boom and a Cummins four-cylinder engine with Eco Mode function designed to provide high power combined with optimised consumption.
The crane has Terex’s Powershift (permanent four-wheel drive) which can be switched between manual mode (with three speeds forward and three speeds reverse) and automatic mode (with five speeds forward and three speeds reverse) to suit the driver’s style.
Operation is via Terex’s TEOS (Terex Operating System) control system with 10″ touchscreen display.
The manoeuvrability of the crane is also helping Concord overcome challenges such as accessing units and handling the semifragile electrical poles.
“Despite the demanding conditions the crane is exhibiting exceptional reliability with no breakdowns, loose wires, or blown fuses since its deployment,” said Chester Rawstron, sales manager at Concord Cranes. “The TRT 35 boasts a capacity that exceeds our project requirements, ensuring the successful execution of lifting tasks with ease.”
COLLETT SUCCESSFULLY DELIVERS 88 WIND TURBINE COMPONENTS IN IRELAND
Collett Transport, a leading specialist in wind turbine logistics and transport, has successfully delivered 88 wind turbine components for Drumlins Park Wind Farm project in Ireland.
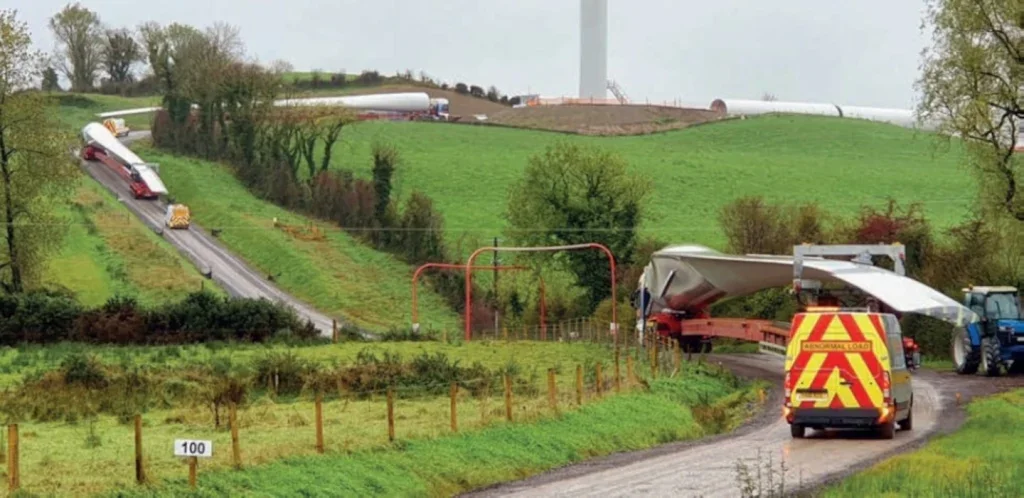
Before the deliveries, Collett undertook a trial run to identify potential challenges along the route for the blade and turbine sections. This practical approach resulted in essential modifications, including tree pruning and adjustments to street furniture.
Collett used super wing carriers for the 65m long blades, flat-top trailers for the additional 15m long blade tips, and tower clamp trailers for the tower sections. The longest tower section, for the top, was 28m long and the heaviest (base) section weighed 62 tonnes. Altogether 88 components were transported.
All components were loaded at Belview Port in Waterford and transported during night-time to minimise traffic congestion. Covering a distance of 199 miles, the journey took a total travel time of nine hours. Departing at 7pm, the travel time included necessary rest breaks for the drivers and was accompanied by the Collett escort fleet and local Garda escort.
The Drumlins Park Wind Farm is expected to be operational in 2024 and to generate up to 49MW of renewable energy.
COULD LARGEST AIRCRAFT EVER BE THE SOLUTION TO MOVING MEGA BLADES?
As we have seen, wind energy components will only get larger; and the practical limits of transporting them by land may in some cases be being reached already. Radia is an energy company focussed on radically expanding the scope and scale of the onshore wind energy industry – indeed on bringing offshore scales to onshore. The company envisions structures the height of the Eiffel Tower as typical. Components of its GigaWind system would be simply too long, too tall and too wide to transport terrestrially. A 100m-long blade for example would have a hub diameter of around 7 or 8 metres; and overpasses and bridges in most countries are standardised at around five metres. The components, even on the lowest of low-loaders, simply would not fit underneath them.
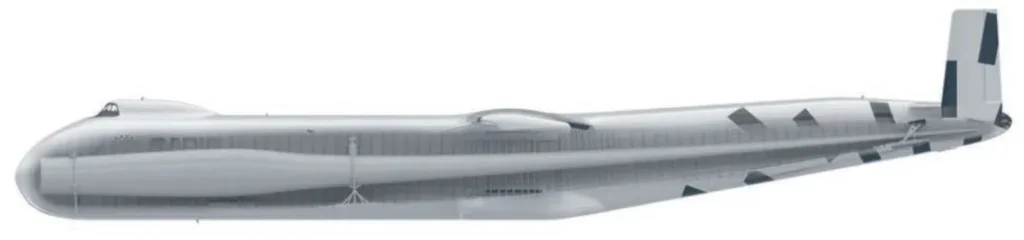
Radia’s solution to this logical (and logistical) dead end is to transport tower sections and entire blades by air, inside the fuselage of a plane. They are proposing to build an aircraft to do so. The only snag is size: these will be the largest payloads ever moved by air, and the plane, called ‘Windrunner’, will have to be the largest aircraft in history. Even so, it will have to be able to land on minimally prepared dirt or gravel runways carved out at the wind farm site and sometimes no more than 1800 metres long.
It is not quite the impossibility it might seem. The cargo is extreme in size but not in weight. So although the Windrunner will have a cargo bay volume of 272,000 cubic feet, 12 times that of a Boeing 747-400F, its wingspan, at 261 feet, would be only 20 feet longer. Its length though at 365 feet, will be 127 feet longer than the Boeing’s. “This is the first time that an aircraft has been designed to optimise on volume instead of weight, and so it’s very unique in that sense. It can still move a lot of mass, 70 tonnes [a Boeing 747 cargo variant aircraft can typically carry around 110 tonnes] but it has a volume that’s about 12 times bigger than a 747,” said founder and CEO Mark Lundstrom. “This means the cargo hold can carry a 100-metre-plus blade – and because wind farms are typically built in remote locations the plane will be capable of landing on short, unpaved airstrips.”