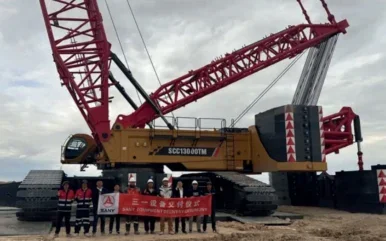
Lattice-boom crawler cranes are designed to combine strength with mobility. Increase that strength, and the crane offers more versatility – as well as potential time savings on certain lifting jobs.
A new standard was set earlier in the year, says China-based manufacturer Zoomlion, when its 3,600-tonne ZCC89000 crawler broke two world records: for the heaviest single lift, and the fastest lifting speed.
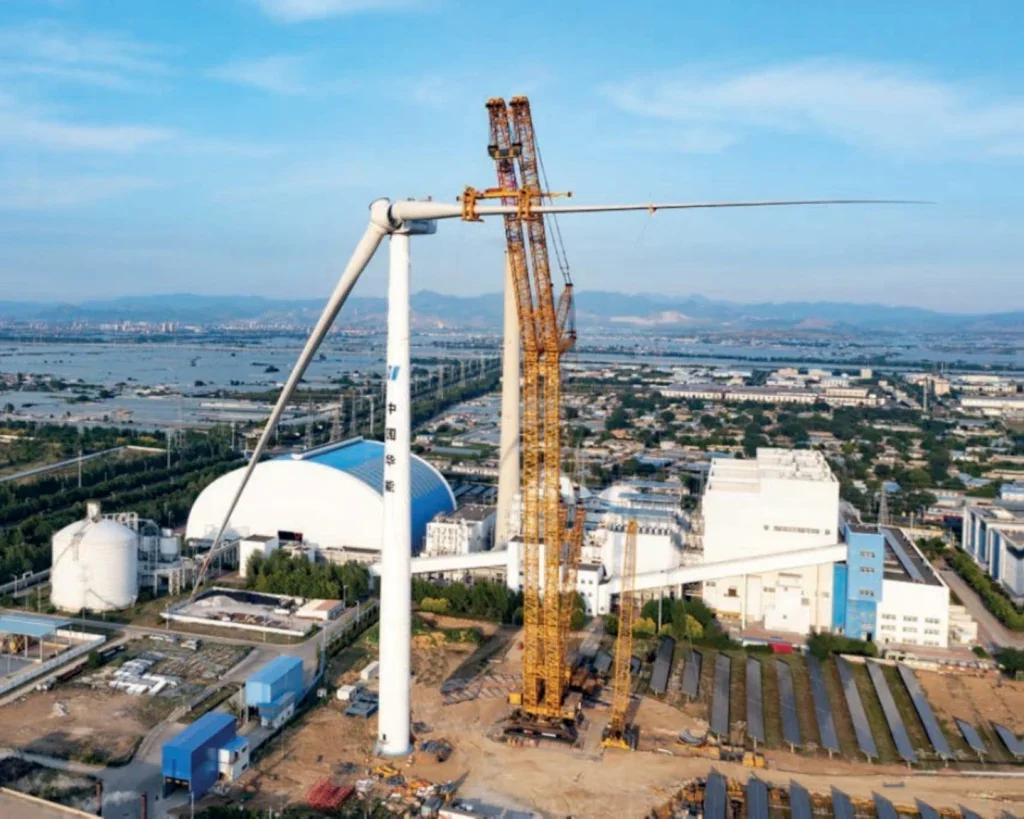
The capacity of the crane mirrored the scope of the project. The records took place during the installation of three slurry bed reactors in Zhejiang Province, as part of the construction of a slurry bed residue hydrogenation plant forming part of Zhejiang Petroleum & Chemical Co. Ltd.’s No.3 New Material Engineering Project.
The project is the largest of its kind within the Chinese refining and chemical integration sector, says Zoomlion, and also the largest investment in a single industrial development of any kind.
Once complete, the petrochemical facility will have an annual refining capacity of 40 million tonnes of oils, 11.8m tonnes of aromatics, and 4.2m tonnes of ethylene.
Big numbers, which require big equipment – which required a big crane. Each slurry bed reactor – the largest single-weight forging and welding hydrogenation reactor – has a net weight of 3,037 tonnes, and a net height of 67.57 metres.
Zoomlion completed the installation of the three reactors in six days, advancing the construction schedule by two months. The lifting moment of the crane reached 92,800tm with a counterweight of 3,160t.
The model also offers six travel modes, notes Zoomlion, including its ‘T-shaped’ travel path innovation that allows the crane to achieve greater pick-up range in a narrow operating area.
GROWTH MARKET
The wind energy sector is currently growing – not just in investment, but also in the size of the turbines used to harness power. As a result, bigger crawlers are being deployed.
A crane from Chinese manufacturer XCMG assisted the installation of another world record – this time the world’s longest wind turbine blade – in the city of Yingkou, in Liaoning Province in north-eastern China.
In the city’s shipyard a 4,000t-capacity XGC88000 crawler with luffing jib – operated by XCMG subsidiary XCMG Crane – lifted an 18MW offshore wind turbine weighing almost 800 tonnes. With a hub centre of 145m and a blade tip height of almost 270m, the turbines produce 44kWh of power per revolution.
The project wasn’t all about lifting strength – it also required accuracy, to install the giant blades. Requiring the insertion of more than 170 bolts at a height of around 150m, the XGC88000 completed the task with support from auxiliary cranes.
Heavy lifting and transport specialist Mammoet recently took delivery of its first Liebherr LR12500, which has a capacity of 2,500t and a 200m hook height.
‘Offshore wind turbine components are growing at a fast rate, with nacelles of 1,000t, tower sections of 2,000t, and jackets and monopiles of 3,000t in production,’ says the company.
Higher-capacity cranes also help to expediate other energy projects, adds Mammoet: ‘Energy projects in both the nuclear and oil and gas sectors will rely heavily on high-capacity lifting equipment to bring forward the date of first power, while increasing the costeffectiveness of the build phase in the case of new construction, and reducing downtime in the case of turnaround projects.’
Wind energy is also receiving investment in the USA. In Maine, for example, Manitowoc cranes being used to handle turbine components that the crane manufacturer describes as ‘massive’. The project, being overseen by Sprague Energy, will create enough onshore wind energy to power more than 62,000 homes across the state, with work due to have conclude in October.
Sprague worked with local dealer Shawmut Equipment to source five Manitowoc crawlers: three MLC150s; one MLC250; and one MLC300 VPC-MAX – all of which performed up to 30 lifts each day. Loads ranged from 24.2 US tons to 101.4 tons, with some of the larger components – such as blades measuring up to 250 feet long – requiring two cranes working in tandem.
The cranes were used to unload and transport the turbine components from vessels and rail off the coast of Searsport into holding yards, then on to trucks for transportation to a number of wind farms.
Also in the onshore wind sector a Sany SCC13000TM crawler played a key role in erecting turbines in the Mangystau Region of Kazakhstan. The turbines have a tower height of 112m, with a 127t nacelle, 43t hub, and 30t blades.
The crane, assisted by two auxiliary STB1600T6 telecrawlers, was configured with a 126m main boom, 9m E-jib, and a total of 440t of additional counterweights, helping the crane to move components weighing up to 239t at a 20m radius.
The wind farm is located around 75km from the city of Aktau, located in the south-west of Kazakhstan, near the Caspian Sea. The project comprises eight turbines, each generating 6.25MW, are designed to withstand the region’s strong winds, says Sany.
POPULAR CHOICE
Sarens recently purchased its third Liebherr LR12500-1.0, a crawler with lifting capacity of 2,500t. It’s equipped with a unique wide boom and a T-shaped turntable, explains Sarens, making it very suitable for handling large monopiles and other major wind turbine components.

One of the company’s fleet of LR12500-1.0 cranes was deployed at the Port of Rostock in Germany, to lift monopiles for the Baltic Eagle offshore wind farm.
“We are particularly focusing on jobs in the renewables sector with our new 2,500t crane,” says Sarens. “Handling offshore wind turbines and their foundations at ports is becoming an important business segment as the weights of components continue to rise. The LR 12500-1.0 is perfectly suited for these tasks, along with lifting large components for the petrochemical industry and general port handling work.”
Sarens added the third LR12500-1.0 to its portfolio due to the amount of demand from clients for the crane. The cranes also seem popular within the company, as the first two have both been given names.
‘Strong Steve’ is named after Steve Sarens, the company’s managing director of technical solutions in the US, and is currently serving on an offshore wind project in Norway. And ‘Straffe Hendrik’ was named after Hendrik Sanders, an engineer who has worked at Sarens for more than 40 years. That crane was, until recently, stationed in Eemshaven, The Netherlands, engaging in loading and unloading transition pieces and monopiles.
Sarens has now deployed that crane in the construction sector, transporting it to North America to assist on a major semiconductor plant project.
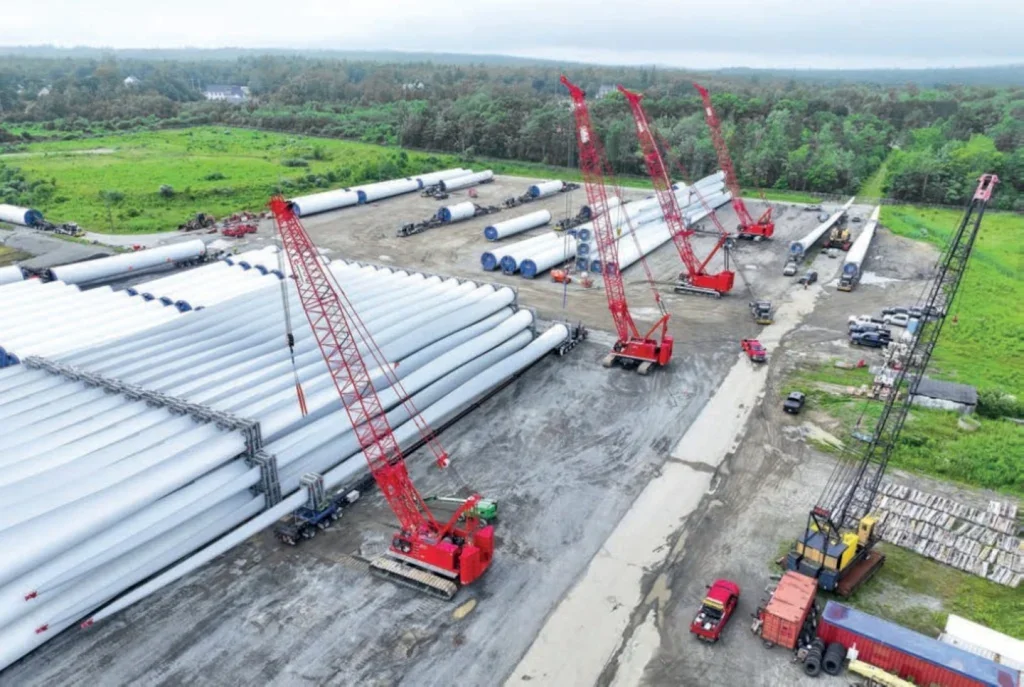
“The LR12500 will be operating in HDWB2 configuration, with 90m of main boom and 84m of luffing jib and full 1,400Te Superlift ballast,” says Steve Sarens. “This crane was selected for the high lifting capacities in this configuration as well as for the wagon availability. Very few cranes in this category are capable of using a wagon/ carrier for the Superlift.
“The LR12500, as a first in the industry, is using SPMTs as ballast wagon. Using a ballast wagon allows for faster and more efficient working as there is no need to handle the counterweights during and in between the lifting operations. There are various advantages of using SPMTs as ballast wagon, the most important being the low ground load applied.
“Our fleet of LR12500s is currently planned for projects in offshore wind, semiconductor plants, nuclear plants, the steel industry, and shipyards.”
Japan-based heavy lifting and specialised heavy transport provider Denzai also purchased a Liebherr LR12500-1.0 earlier this year and has put the crane to work at S-Oil’s Shaheen Project petrochemical plant in Ulsan, South Korea.
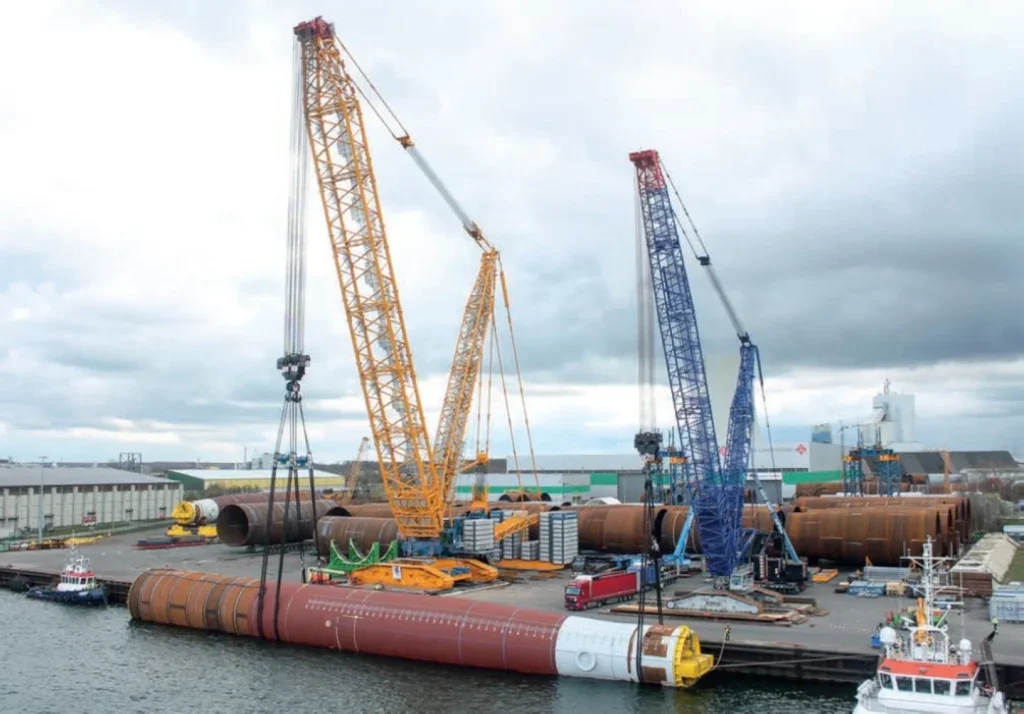
The company already owned a 1,350t-capacity Liebherr LR11350, but purchased the larger model in part due to the increased size of wind turbine components.
As the amount of electricity generated by offshore wind increases, the height and weight of offshore wind turbines are becoming larger and larger, says the company. As a result it expects the construction of even larger offshore wind turbines to become impossible with its 1,350-tonne crawler crane.
In the Round 1 and Round 2 of offshore wind turbine construction projects currently under way in Japan the weight of the towers will be different from the European specifications and the Japanese specifications are expected to be even heavier.
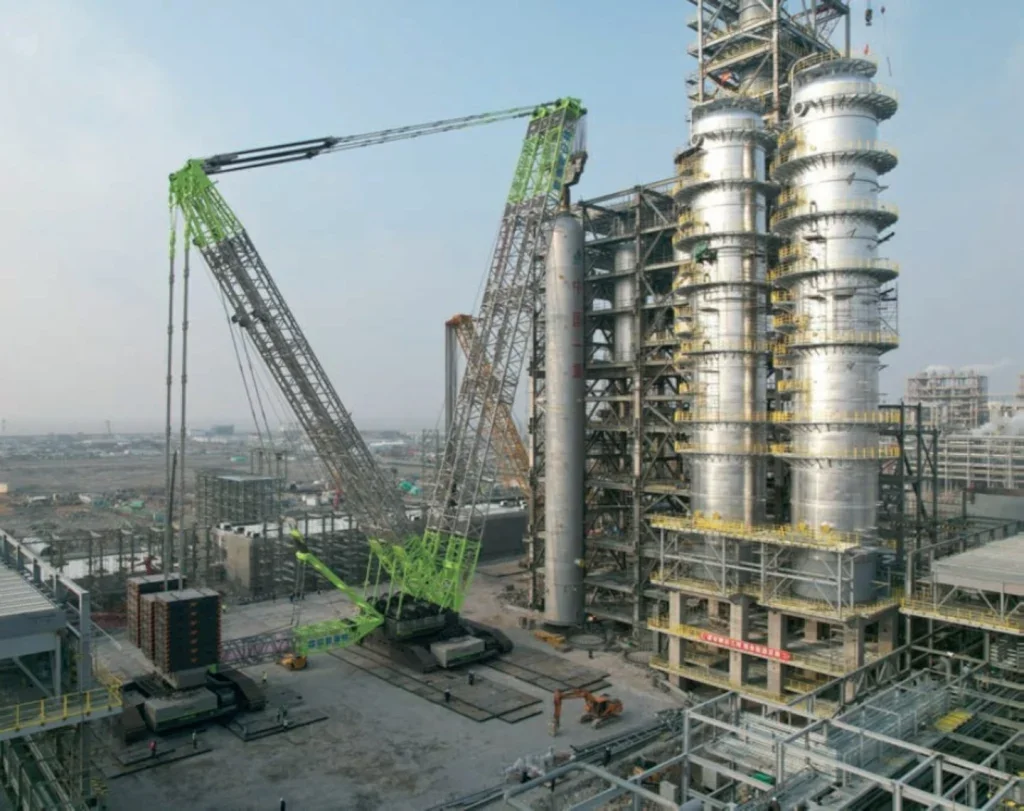
In addition, the working radius of the cranes is expected to be larger than in Europe because some Japanese ports have less strong wharves than those in Europe, and the cranes must be installed further away from the wharves. Furthermore, if the nacelle weight exceeds 800 tonnes Denzai says it will be impossible to lift the nacelle at the far side of the vessel using a single 1,350-tonne crane. It estimates that two 1,350-tonne cranes will be required.
The LR12500, however, can lift up to 951 tonnes with a working radius of 48m, thus satisfying the requirements with only one crane.
The LR11350, meanwhile, is now being used by Denzai’s South Korean subsidiary Denzai International Projects at the construction of a fertiliser production plant in Port Harcourt, Nigeria – the first of its kind in Africa, says Denzai.
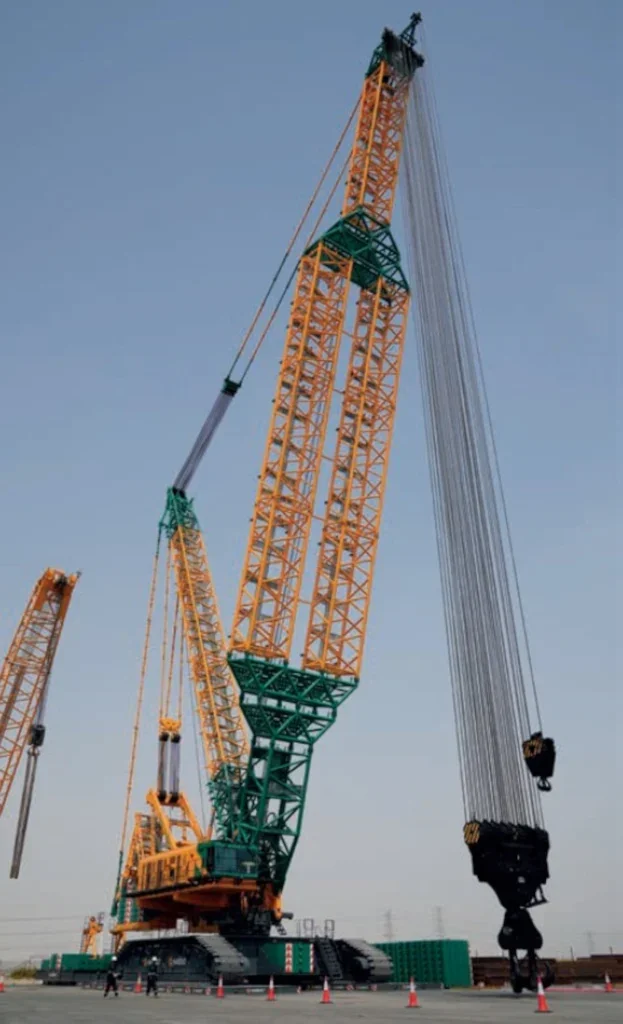
Indorama Eleme Fertilizer & Chemicals awarded the project to Daewoo E&C Nigeria, a subsidiary of Daewoo Engineering & Construction, with Denzai Group providing technical planning, dispatching crane operators, and leasing the LR11350.
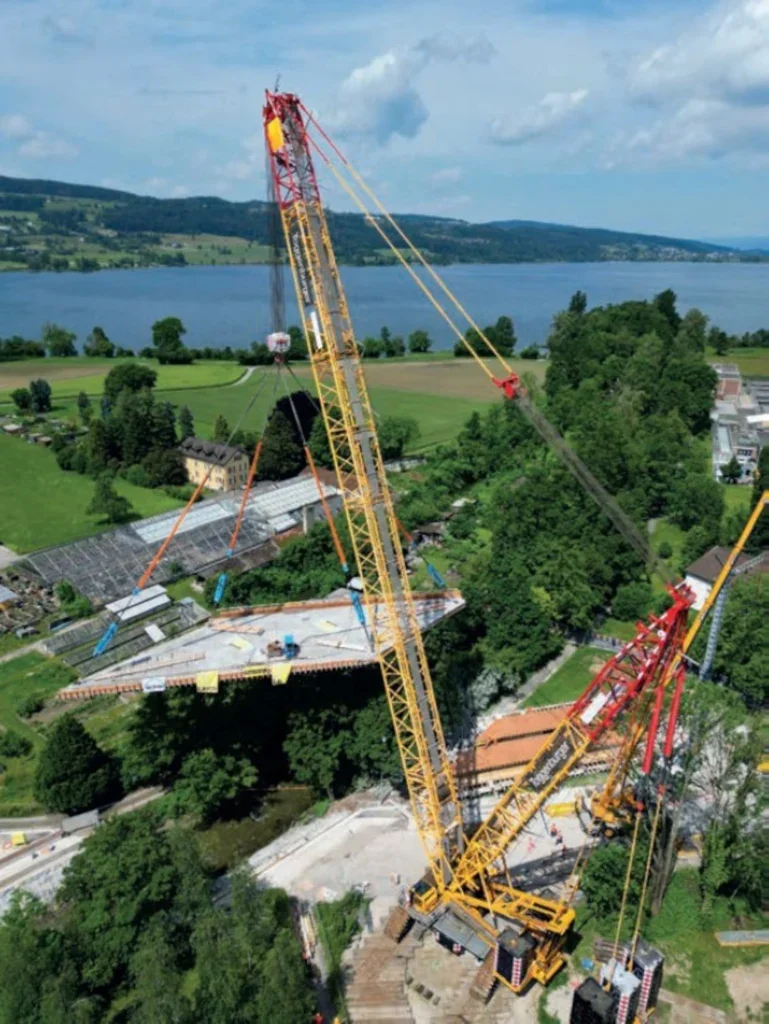
CROSSING OVER
High-capacity lattice-boom crawlers are also being used in the bridge industry, where whole bridges or component parts tip the scales and need careful handling.
In Switzerland, a Tadano CC 38.650-1 was used by Winterthurbased crane service provider Toggenburger + Co to lift and remove parts of the old and demolished Aabachbrücke bridge, each weighing up to 150t.
That was followed up with setting the new bridge – with a net weight of 230t – in place in Niederuster, near Zurich.
As the parallelogram-shaped bridge was classed as a sensitive load Toggenburger had to ensure the maximum permissible forces at the attachment points were not exceeded. This was achieved by integrating strand jacks into the slinging gear, to enable each line to be controlled individually, thereby distributing the load evenly.
In India Sany’s 750t SCC7500A was used in the installation of a steel bridge at Vikhroli Railway Station in Mumbai. As the bridge traversed the existing railway tracks the crane had to lift the 180t bridge at a working radius of more than 40m. The project also had a major restriction: the station is a key transport hub between Mumbai’s city centre and surrounding towns, and the resultant high levels of train traffic limited work time to less than one hour a day.
The SCC7500A was originally developed specifically for the Indian wind power market, adds Sany, with more than 20 units sold in the subcontinent so far.
Istanbul-headquartered Hareket, which provides load engineering, project transportation and heavy lifting services across the Middle East, Africa and Europe, is also enjoying the benefits of a Sany crane – specifically the 2,200-tonne capacity SCE2200A.
Hareket describes the crane, which reaches 216m in full configuration, as ‘a key piece of equipment for mega projects’.

“At Hareket we are opening the doors to a new era in largescale projects with our new crawler crane with a capacity of 2,200 tonnes,” says Abdullah Altunkum, chief executive officer at the company. “We are proud to take this important step to take part in mega projects and use our engineering services more effectively. We aim to have a total lifting capacity of 4,000t with a second 2,200t capacity crane, which is among our future investment plans.”
Lifting capacity is not the only consideration amongst manufacturers and buyers of cranes, though. One key advantage of the 275t-capacity SCX2800A-3 from Sumitomo Heavy Industries Construction Cranes (HSC) is its new-generation Cummins L9 engine, which helps to ensure that the crane complies with EU Stage V exhaust emission regulations.
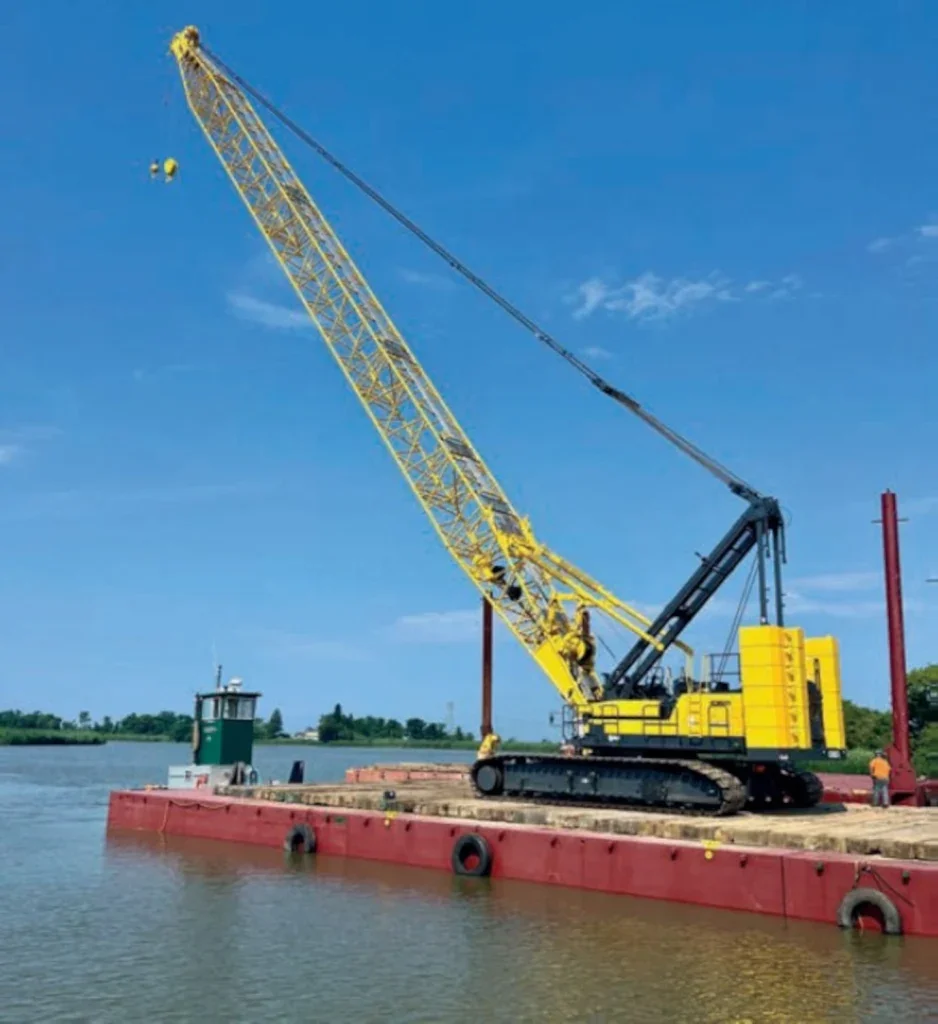
Multiple units of the crane equipped with the Stage V-compliant engine have been sold into Europe and Korea since its launch, says the manufacturer, while the crane is also available with a Stage 3A-compliant engine.
In North America, the ALL Family of Companies has added an order of Kobelco G-3 Series hydraulic crawlers to its fleet, comprising, in varying numbers, the 80t-capacity CK800G-3, the 110t CK1100G-3, and the 160t CK1600G-3.
Rick Mikut, crawler crane division manager at ALL, highlighted the Isuzu Tier 4-compliant engine in the G-3 line, and its reliability, fuel efficiency, and quiet operation.
Kobelco further expanded its presence in North America when South State, a heavy-highway, paving and utility contractor based in New Jersey, purchased a 2024 Kobelco CK2000G-3 crawler. South State purchased the 200t crane – the second largest crawler in the company’s fleet, with 200 feet of boom – through Empire Crane Company, based in Syracuse, New York.
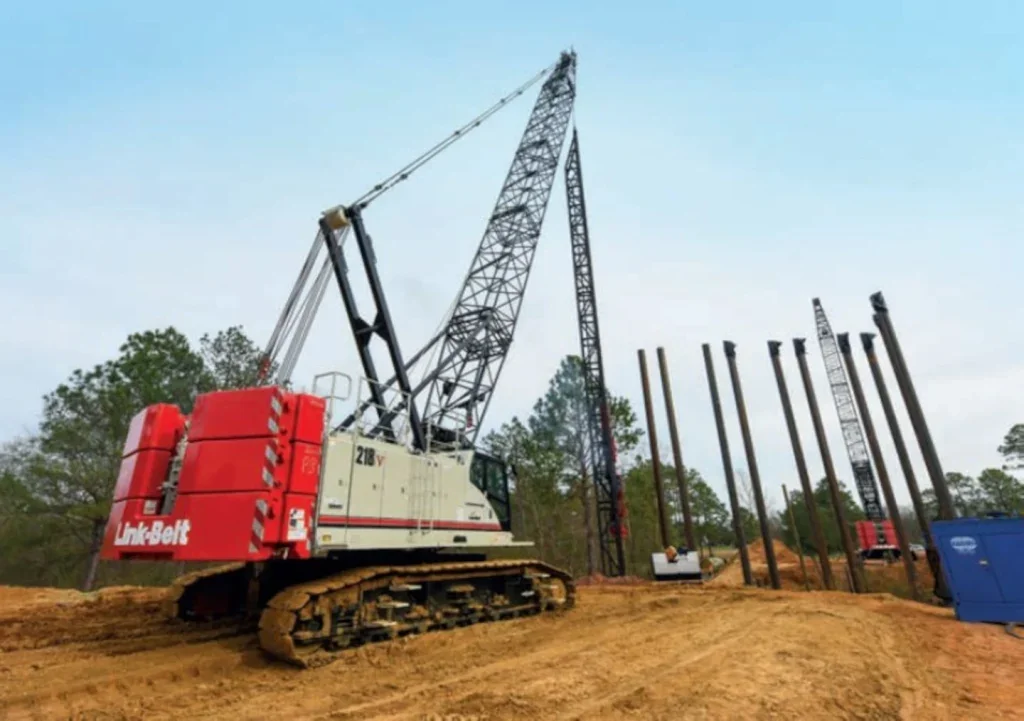
Carlos Cajeira, crane and marine equipment superintendent for South State, cited the crane’s capacity and price point, along with Kobelco’s backing and warranty, as key factors in selecting the crane.
And in Colorado and Utah, Bigge Crane and Rigging has been selected by Kobelco as the exclusive representative of its crawler cranes. As the authorised dealer in the regions, Bigge says it has ‘renewed commitment to bringing the latest crane technology to the heavy-lifting and construction industries’.
There’s plenty of demand for lattice-boom crawlers, says Link-Belt’s Brian Elkins: “Since the release of our 110t 218|V lattice crawler crane at Conexpo 2023, demand for Link-Belt lattice crawlers has been strong across the board. Our 130–300t capacities have been in high demand for the last several years, and our newest luffer design has positively impacted larger-model sales, as well, particularly in the infrastructure sector.
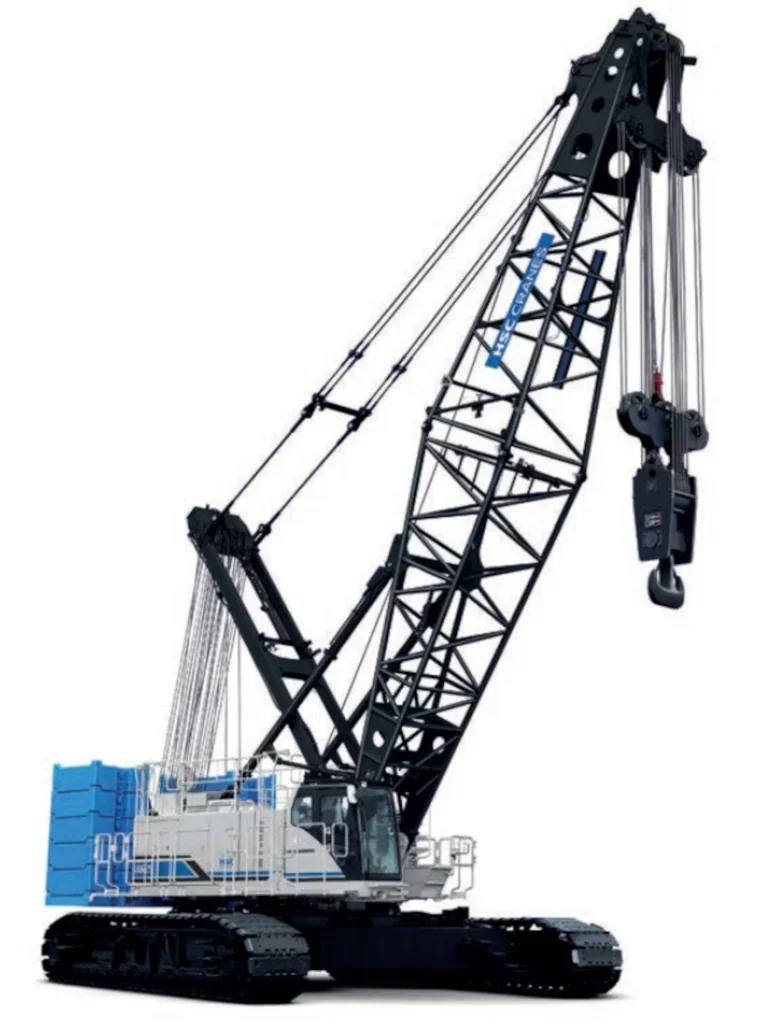
“Customers are seeking crawler cranes that have strong lifting capacity/reach combined with advanced manoeuvrability and reliability.”
From breaking records through to handling the ever-growing demands of giant turbines, while offering the versatility to complete a wide range of other lifts, it’s understandable that lattice-boom crawler cranes are making their mark right across the world.