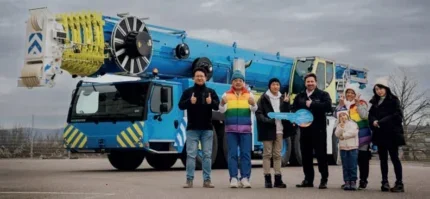
Semiconductor demand is bolstering American manufacturing and boosting the construction industry, claims US crane manufacturer Manitowoc.
It says projects to build the next generation of microchips in the US are in full swing. Across the country funding is being directed to construct new manufacturing plants that will produce the components required for things like smartphones, appliances, cars and military equipment.
CHIPS ACT
Fuelling this is the CHIPS and Science Act which congress passed in 2022. It set aside $280 billion to invest in the semiconductor industry. Of this, $39 billion is earmarked for the construction of microelectronic factories, along with a 25% investment tax credit for the cost of manufacturing equipment. New plants are either planned or already being built in Arizona, Texas, Florida, Ohio, Pennsylvania, Indiana, and New York, with the potential for more in the future.
These construction projects are having a noticeable effect on the construction industry, says Manitowoc. One recentlyannounced project with Intel, for example, estimates the creation of 30,000 new construction and factory jobs. And that is only one project, says Manitowoc; it represents a sliver of what is anticipated to be the total of all the projects combined.
These investments are already driving demand for the lifting industry, it says. According to Kevin Blaney, VP of North America crawler crane sales at Manitowoc, there has been an immediate shift in resources to accommodate new microchip plant builds.
“The impact of semiconductor factory construction on the lifting industry is 100% noticeable. It is pulling many cranes out of the market and redeploying them to these projects. There are a handful of ‘megaprojects’ that require many, many cranes,” he said. “Meanwhile, the rest of the market is still strong. There is also all the other lifting work out there, too.”
SEEING ACTION
Microelectronic manufacturing facility job sites require a variety of cranes to complete the wide range of lifting applications underway. According to Manitowoc, however, crawler and rough-terrain cranes are seeing the most action on these projects in the USA.
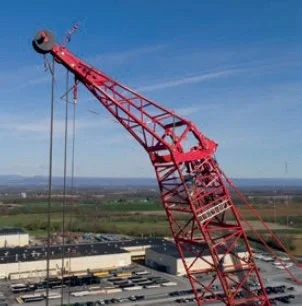
Most of the lifting work in the US is being funnelled through construction companies that are winning project bids. They, in turn, are hiring the crane rental companies, says Manitowoc. Nearly all the work is on a rental basis, with both operated/maintained and bare rental fleets being deployed.
“It’s a very competitive process to win this lifting work,” Blaney explained. “It’s not just about having the lowest bid. There is an interview process and a lot of criteria considered, such as safety and performance.”
The 300-t capacity class of crawler cranes is experiencing the highest demand, followed by 600-t capacity, Manitowoc outlines, with several of its crawler models, like the MLC300 (386 USt) and MLC650 (716 USt), already working on microelectronic job sites.
Rough-terrain cranes play supporting roles, such as erecting crawler cranes and moving materials. Those in the 100 USt (910 t) and above classes, such as the Grove GRT8120 and Grove RT9130-2, are seeing the most action here, Manitowoc reports.
These cranes offer excellent manoeuvrability, strong reach and high capacities, which give them the ability to be used in a variety of applications around the job site.
“These are real workhorse cranes that offer companies a lot of versatility,” Blaney said.
TAIWANESE EXPERTISE
It’s not just the US that’s seeing a boom in microchip related construction. On the opposite side of the globe, in Taiwan, crane rental firm Xin-Hong Crane Engineering Co., has just bought a Liebherr LTM 1300-6.3 specifically to handle the increasing size of production facilities for new semiconductors and microchips production in the Taiwanese IT industry, which are becoming increasingly taller. The crane’s 90-metre boom and compact ballasting options are well-suited to such applications.
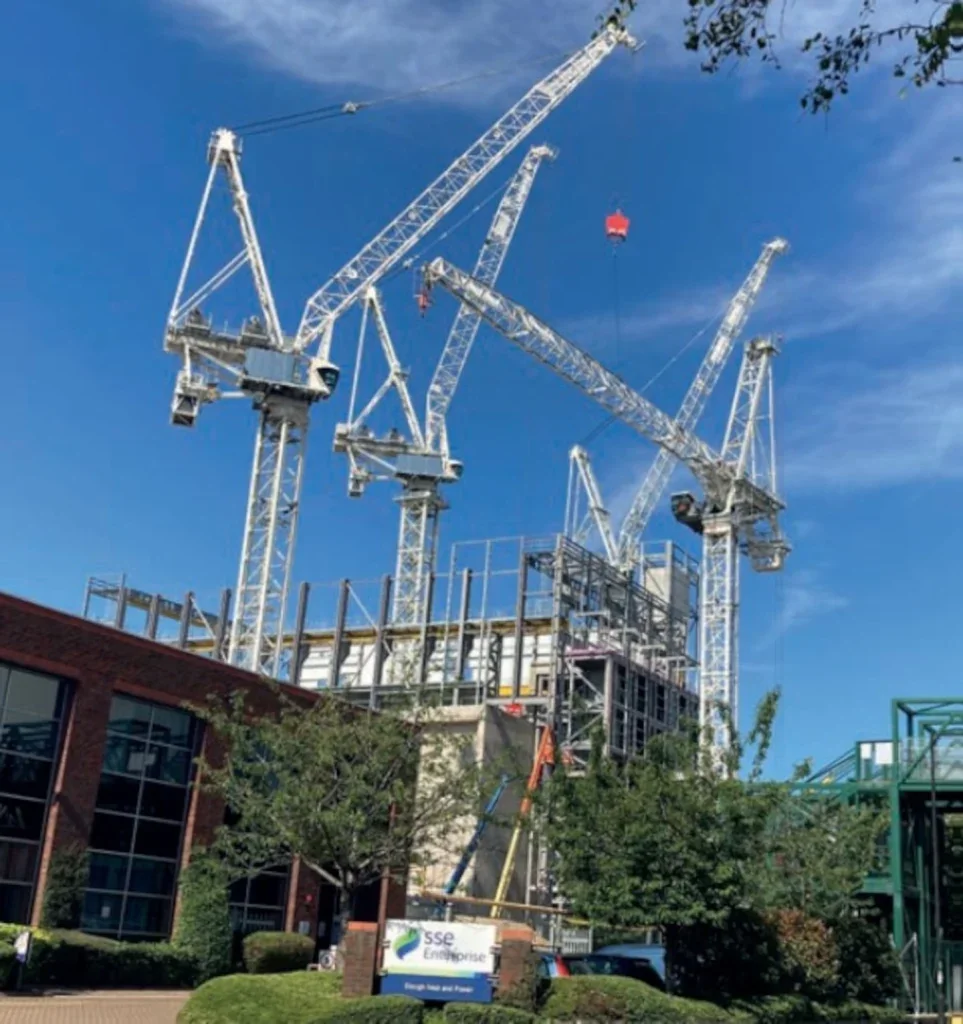
“The LTM 1300-6.3 is particularly suitable for our planned operations in science parks,” explains Chien- Min Wu, owner and CEO of Xin- Hong. “It’s a versatile six-axle crane with an excellent telescopic boom and outstanding capacities.”
DATA DRIVEN
It’s not just microchip factories being built; related tech infrastructure needs construction, too; and this is around the globe.
In London, UK, for example, Clare Rodgers, business stream leader for construction equipment provider Select Plant Hire identifies the data sector as being a driver of demand for its tower cranes. The company recently purchased three Terex CTL 1600-66 luffing jib cranes to add to its fleet, meaning it has the largest fleet of the CTL 1600-66 globally, now totalling 12.
“Back in March 2023, we were placing orders for number six and seven of our CTL1600 fleet,” explains Rodgers. “In less than one year this has increased to 12. This is driven by the requirement for heavy lifting tower cranes, which continues to increase, particularly in the energy and data sectors. Our clients, including Laing O’Rourke, see the benefits of these heavy-duty machines when deploying modern methods of construction to deliver projects for clients. We will soon see more CTL1600 machines being installed on sites across the country, including a fantastic project in Oxford and further projects to be disclosed in the near future.”
The Powergate Data Centre, in west London, is an example of a current UK high-tech data centre project. Construction company Mace is using five Wolff tower cranes from crane manufacturer Wolffkran to build it.
The cranes in use are: three Wolff 630 Bs; one Wolff 700 B; and one Wolff 500 B. Four of the cranes have 70m luffing jibs, whilst the fifth has a 60m jib.
Wolffkran is also suppling the eight tower crane operators and two crane coordinators to oversee and carry out all lifting operations.
“We at Mace have been appointed to manage construction of this hyper-scale data centre set in West London,” says Andrew Wiggins, operations director (construction) at Mace. “The sheer scale of this project reflects the demand for an enhanced digital infrastructure.”
For the full jobsite story see
POSITIVE FUTURE
There is a long horizon for the construction of new microchip factories with the work set to continue for many years, Manitowoc believes, with projects still being announced.
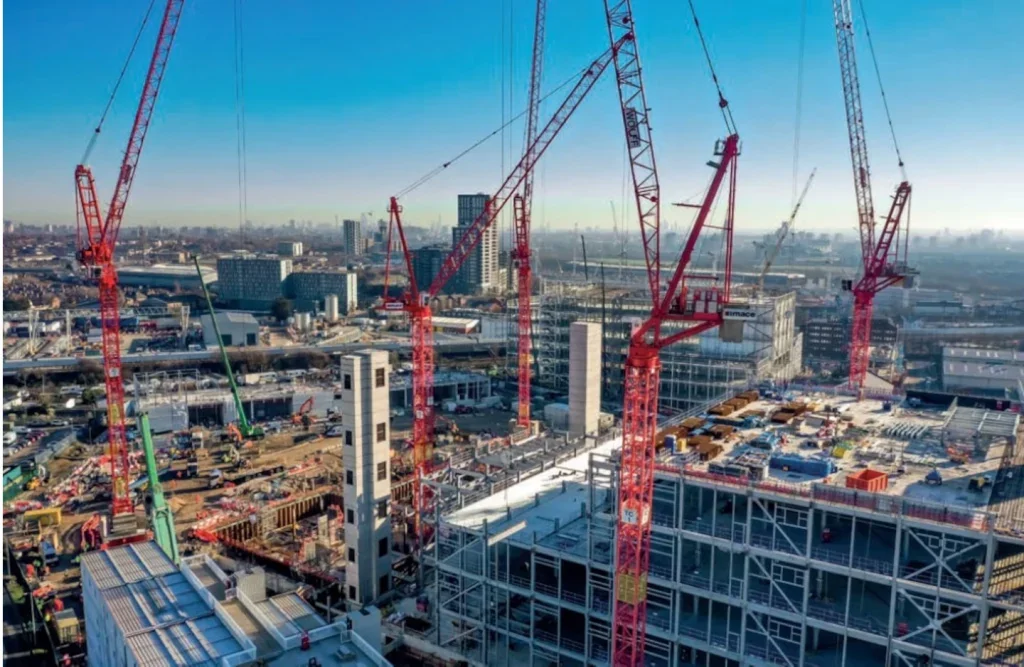
Additional projects are in the pipeline, it says, and they aren’t just factories. This is because a key component of the CHIPS and Science Act is research funding. Universities could build new facilities to accommodate this work, for example. This means that there are even more opportunities ahead for lifting companies to win projects tied to CHIPS and Science Act funding.
“I was just talking to folks in the industry that think this could be a 20-year run of work,” Manitowoc’s Blaney concludes. “There is a chain reaction of new construction work boosting lifting work.”
SMITH ERECTORS USES TWO LINK-BELT TELESCOPIC CRANES FOR FITTING DISTRIBUTION FACILITY ROOF
Smith Erectors of Markle, Indiana, USA, is utilising the reach and versatility of two Link-Belt telescopic cranes – the TCC-2500 and the ATC-3275 – for construction of a new 700,000-square-foot manufacturing and distribution facility in Rushville, Indiana. The state-of-the-art facility represents a $259 million investment. Construction is set for completion by the end of 2024.
“We have the TCC-2500 and ATC-3275 on-site to set all the internal steel structure for this building,” says Jason Moore, crane operator at Smith Erectors. “Then we are lifting insulated metal panels for the walls and insulated metal panels for the roof primarily with the TCC-2500.”
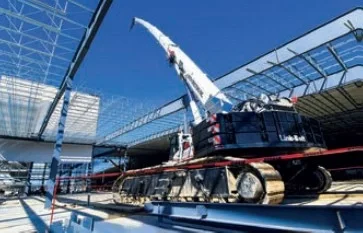
Smith Erectors is utilising the long reach of the TCC-2500 for placement of roof panels of the 600-by-1200-foot (182-by-365-metre) distribution centre. To accomplish roof panel placement of the entire 700,000-square-foot project, Smith Erectors has fitted the TCC-2500 with one or both lattice fly extensions (depending on the radius requirement) when erecting the fly to give the TCC-2500 the greatest reach possible. By inserting one or both 25-foot (7.6-metre) lattice fly extensions, the TCC-2500 is able to place panels up to a 260-foot (79.2-metre) radius by traveling up and down the 600-foot (182-metre) length of the building.
“This TCC-2500 really is a beast. When you add in all of the lattice extensions with the fly, it can work at a really great radius,” Moore explains.
Smith Erectors has broken the roof schedule into three sections, giving the TCC-2500 three locations to work from: both 600-foot (182-metre) lengths of the building and the middle of the building.
“We left a hole in the middle of the building for the TCC-2500 to travel inside on the finished concrete and place panels roughly 160 feet (48.7 metres) in either direction. We’re obviously obstructed with our boom angle, but that lets us do the whole building with the TCC-2500,” Moore says.
The ATC-3275 placed most of the initial steel structure of the facility. Each bay, roughly 60 feet wide, is lifted into place and weighs approximately 60,000 pounds.
“These are both just handy cranes for this kind of work. The computers both set up easily. You can set your limits easily – especially when working with roof obstructions,” Moore concludes.