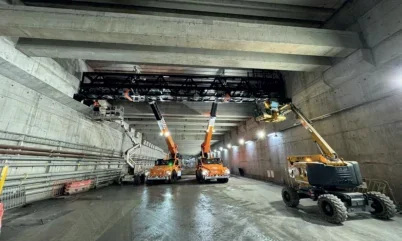
Terex’s Franna pick and carry cranes and the Australian market have a long history together, and their relationship is as strong as ever. From the versatility of the cranes providing invaluable at the country’s many mining sites, to the roadworthiness of the vehicles being put to good use during longdistance drives between job sites, they enjoy enduring popularity ‘Down Under’.
There are around 10,000 cranes active in Australia, says Franna sales director Andrew Pritchard and, of those, around 5,000 are Franna pick and carry cranes. “I drive 70km each way to work every day, and I’ll pass at least three Frannas,” he says.
That requirement to travel on roads was part of the motivation behind the cranes’ latest upgrade. As per the Australian Design Rules (ADR), up until 1 July 2024, cranes running on Australian roads could have a Tier 3 engine but after that date were required to meet the next level up.
While Franna’s AT40, AT22, and MAC25 models previously used a Mercedes-Benz OM906 engine, the cranes – redesignated the AT40 Series 2, AT22 Series 2, and MAC25 Series 5 – now come with an OM936 engine that complies with Stage V and Tier 4 Final regulations regarding emissions.
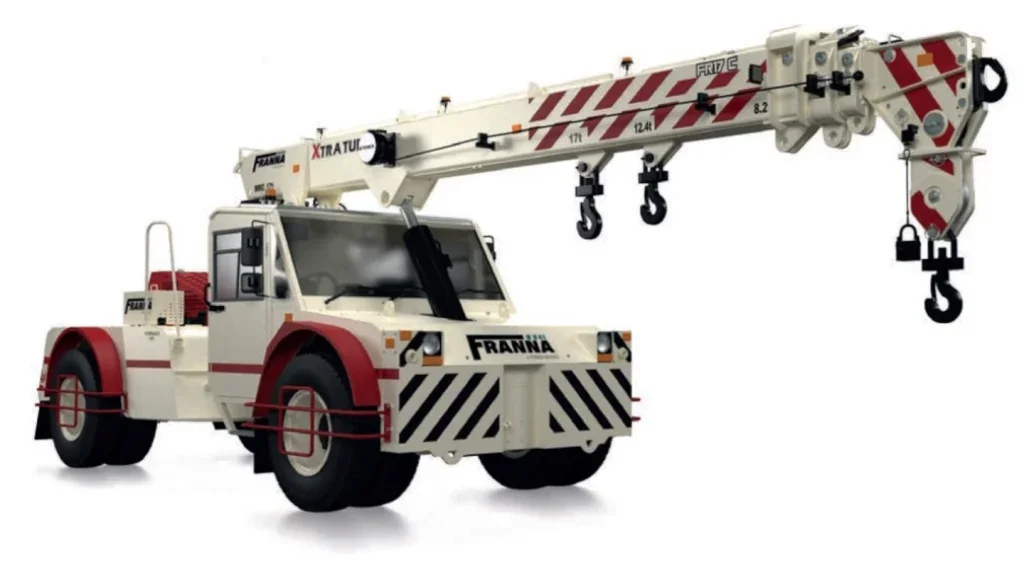
By surpassing the updated ADR compliance standards, the cranes have been future-proofed against further tightening of the rules, adds Franna. This covers not just engine emissions but requirements relating to headlights, visibility, noise levels, and ABS, as well as various safety standards.
“The cranes feature so much technology, and much of that is based around safety,” says Pritchard. A recent innovation is Franna’s Radar system, which deploys real-time load calculations to alert operators, using ‘traffic lights’ indicators, if they are potentially approaching a dangerous situation due to articulation, the position of the load, and so forth. This comes as standard on all new cranes, while a 360-degree camera give visibility all around the crane – similar to today’s modern cars, notes Pritchard – with the addition of a camera on the hook.
Such high safety standards are particularly important at mine sites, where Franna cranes are popular, says Pritchard. “On any given day there will be multiple pick and carry cranes operating at each mine site in Australia. They’re versatile and can travel up and down gradients with the load on the hook.”
Mining operations are just one of many examples of where Franna’s cranes are used in the Australian market.
When it comes to pick and carry cranes, Australia ‘gets it’ in a way that not many regions currently do, says Pritchard.
“Other types of crane may offer a longer reach but the capacity is reduced and outriggers are required, making the crane static. To move the load it then needs placing on a separate truck.
“Pick and carry cranes offer a different, more efficient process. Because the load isn’t picked up at a distance, capacity isn’t compromised. The operator can drive the crane with the load on the hook, and because of the short rigging, the load doesn’t swing. And the cranes articulate, rather than slewing the load as on a carry deck crane, so the load is always in front of the operator and easy to see.”
The articulation differentiates the Franna crane from equivalent pick and carry cranes manufactured in Italy – one of the global hotspots for pick and carry crane production – as those mainly use a rear wheel to turn the crane instead.
The distinction between Franna’s cranes and carry deck cranes is something the manufacturer is aiming to exploit in the US market, where it launched a 24t model (the AT24 US) last year, at the Utility Show in Kentucky.
“People at the launch thought it was fantastic,” says Pritchard. “We weren’t just launching the crane, we were launching a process, and had to explain the efficiency the cranes offer, and that the capacity isn’t compromised by reach.”
The target market in the US is those companies currently using carry deck cranes, due to the lack of pick and carry cranes currently in operation in the region.
To expand the versatility of the cranes, the 24t model will soon be followed by the 44t crane in the US market. The range of potential end uses is broad, explains Pritchard: “They’re useful for maintenance, for example in a plant room, where the cranes can pick up a compressor or generator, lift it and go, even with minimal headroom.
“Another common application is installing gantry cranes in factories where you have virtually no headroom.
“In Australia, a swimming pool manufacturer called Plungie Pools uses Franna pick and carry cranes to move pre-cast concrete swimming pools down the side of houses to the back garden, and that company has just started doing business in Texas. Without that method of moving the pre-cast pools, you would need a crane with capacity of at least 250t to lift the pool over the house.”
Another market being targeted by Franna is India, where the brand has a long and interesting history.
Around 20 years ago, Indian company Escorts commissioned Franna with designing a pick and carry crane, which it then manufactured, using the Franna name – which is now synonymous with pick and carry cranes in the country, says Pritchard, in a similar way to the name Hoover is used as a by-word for vacuum cleaners.
As a result, ‘Franna’ is a byword for any pick and carry crane in India, explains Pritchard.
And the pick and carry market in the subcontinent is huge with around 8,000 of the cranes sold into the market each year compared to around 300 new cranes in Australia.
Franna entered the India market directly two years ago when it started producing its 17t-capacity FR17C – the model was chosen as it could be manufactured at a suitable price for the region. While it isn’t as advanced as the models produced for the Australia and the US it meets the demands of the market – including its Tier 3 engine being able to process fuel of a lower purity, as is more common in the region, which could damage a Tier 4 or 5 engine.
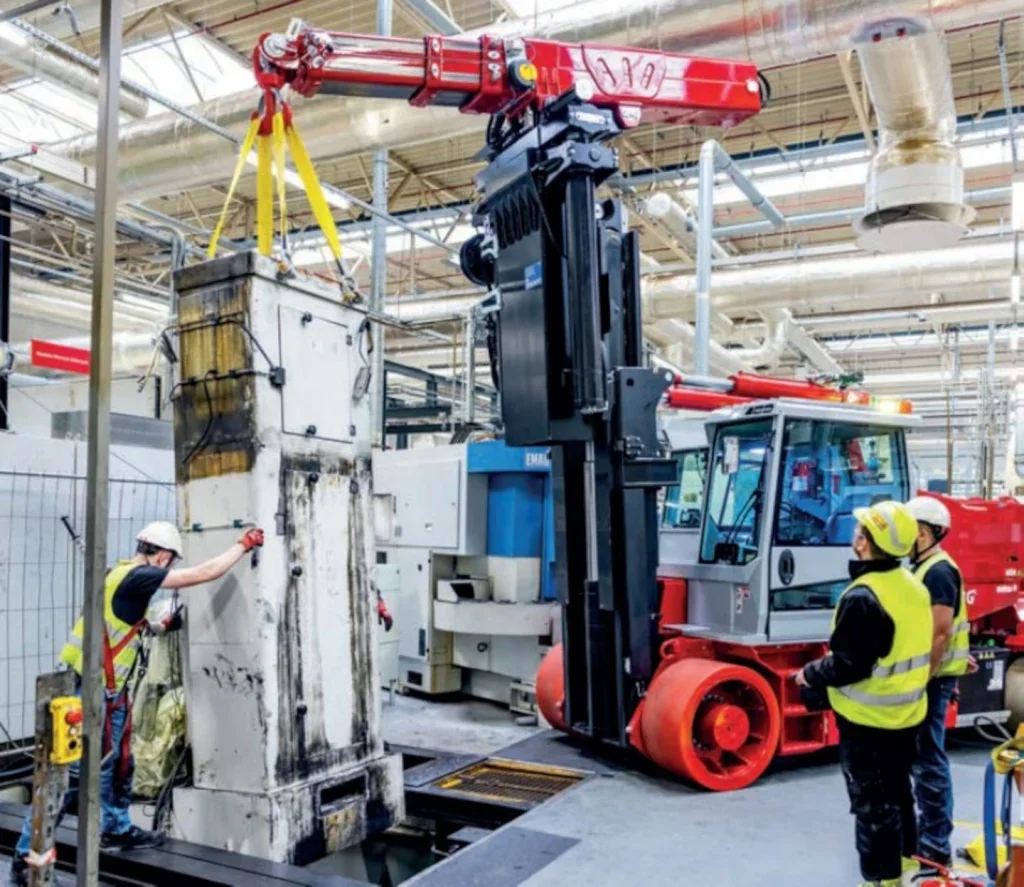
The same model was also launched into the Brazil market earlier this year, with launches into the Middle East and South Africa due to follow.
“The Latin America market is going to be big,” says Pritchard, noting that Franna has had some orders already.
HOME SWEET HOME FOR JMG
In May, Italian pick and carry crane manufacturer JMG Cranes celebrated the opening of its new HQ, which the company calls la Cittadella delle Gru, in Sarmato.
That location – a town in the Province of Piacenza, in the northwest of Italy – was where founder Maurizio Manzini purchased the company’s first warehouses.
The new facility covers 63 hectares, of which 8,000sqm are allocated to production, and 11,000sqm to green spaces. The area was formerly the site of the Eridania sugar refinery, which had been disused since 2002.
JMG is a specialist in electric cranes, and has an 18-strong engineering team. At the opening event, Matteo Montagna, head of the R&D department at JMG, mentioned a new technology that the company is currently exploring: hydrogen-powered cranes.
“We are ready to take the next step towards fuel cell batteries, responding to our customers’ needs,” said Montagna. “It is certainly not a step we will take tomorrow, it requires two years of study, but we believe that fuel cells are the technological destiny of our machines and, more generally, of all operating machines.
“Because it is the only available technology today that can unite all operational needs without compromising an equally important need, called sustainability.”
While hydrogen-powered cranes may be a little while away yet, JMG’s electric cranes are offering benefits to end users today. Shortly after the opening of the new facility, JMG exhibited at the Pipeline & Gas Expo in Piacenza, a trade show dedicated to the midstream sector and distribution networks in the oil, gas, and water industries.
The company used the event to promote the benefits of electric pick and carry cranes in those areas: these include reductions in emissions, which JMG highlights as crucial to the midstream sectors where sustainability regulations are becoming increasingly exacting; and quieter operation, which is important on job sites close to urban environments. Specific focus was given to its 4.5t-capacity MC45SB, and the MC100RE carry deck crane.
Away from the oil and gas industry, JMG recently developed a crane suitable for applications such as warehouses, where narrow aisles and high shelves can prove a challenge for conventional lifting equipment.
Described as a hybrid between a pick and carry crane and a forklift, the MC250.09FL is designed with a low, set-back centre of gravity, and a lift mast similar to that of a forklift, enabling it to lift heavy weights vertically, very close to the body of the crane: it has capacity to lift 25t at 0.9m with an open carriage, explains JMG.
The lift mast can be combined with either a fork carriage or a hydraulic crane jib with a load indicator and tilting moment limiting device.
The crane is fully electric, radio remote controlled, and has a variable wheelbase that can extend up to 1,200mm at the rear, as well as removable counterweights.
UPGRADES TO GALIZIA’S RANGE
Galizia, based in Castello di Annone in north-western Italy, recent updated its GF600 pick and carry crane to improve operator visibility.
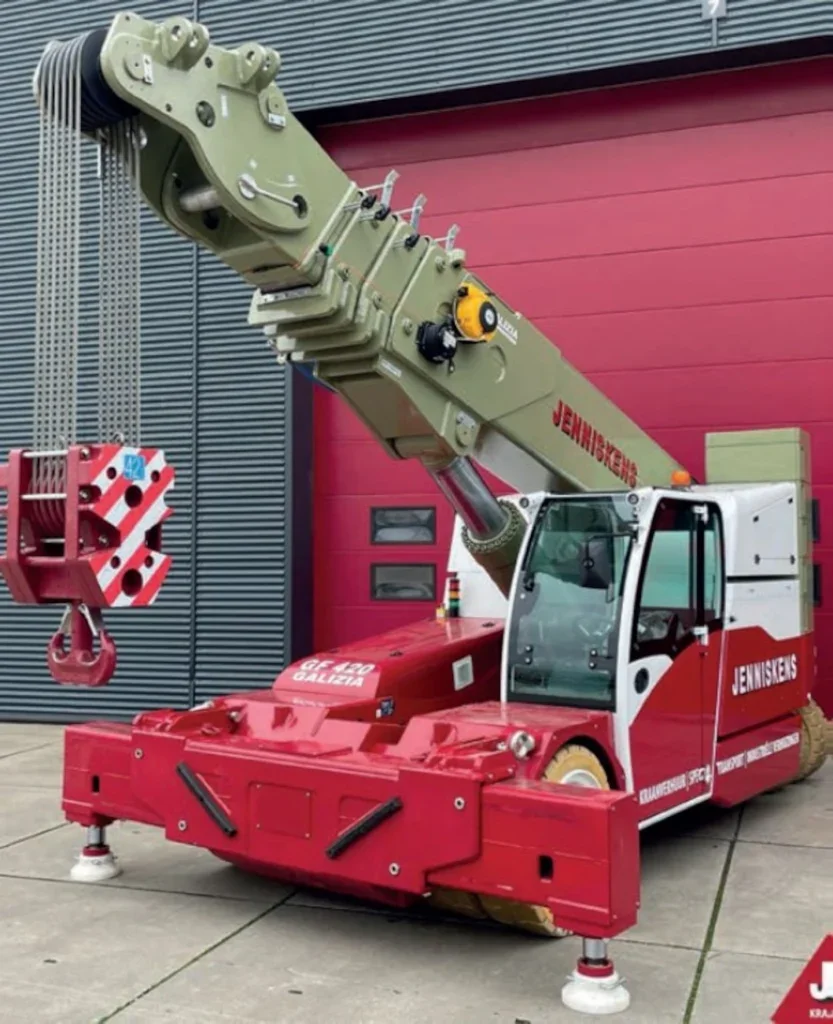
The crane, which offers a maximum capacity of 60t at 1 metre from the shield, now has a “super tapered front”, says managing director Fabio Vercelli, in order to improve visibility for the operator both from the cab, and when operating the crane by radio remote control. This design also features on other cranes in Galizia’s portfolio.
The company has also introduced a version of its 42t-capacity GF420 pick and carry crane with a lithium battery following a special request from Netherlands-based crane rental and special transport company Jenniskens.
The LiFePO4 solution was requested by the customer in order to have higher efficiency, to last longer with less downtime, and reduced costs across its service life, says Vercelli. The battery can stay on board for fast recharging, with no maintenance, watering, or swapping required.
The crane also features extendable front outriggers to increase capacity. Based on the same technology that Galizia previously applied to its GF180 cranes, the system replaces the standard fixed front outriggers enabling the operator to extend the stabilisers laterally to increase the crane’s support width, plus increasing capacity.
Demand for zero-emission pick and carry cranes is ongoing, says Vercelli, with focus on precision and safety. More innovation will come from his company, he adds: “Galizia is a pioneer in its sector thanks, for example, to the ‘two motors in the front with counter rotation solution’ and ‘radio remote control application’ designed and installed a long time ago, revolutionising the pick and carry concept – and we are ready to launch next year a pair of new great pieces with unique solutions.”
POLISH INDUSTRIAL MACHINERY RELOACTION SPECIALIST UTILISES JMG FLEET
MS Industry is a Poland-based provider of transportation for industrial machinery in the automotive sector and beyond.
Based in Bielsko Biała it counts amongst its customers Opel, Volkswagen, Magna, Samsung, Bosch, Siemens, and LG. Its services include assembly, disassembly, transfer and installation of production equipment.
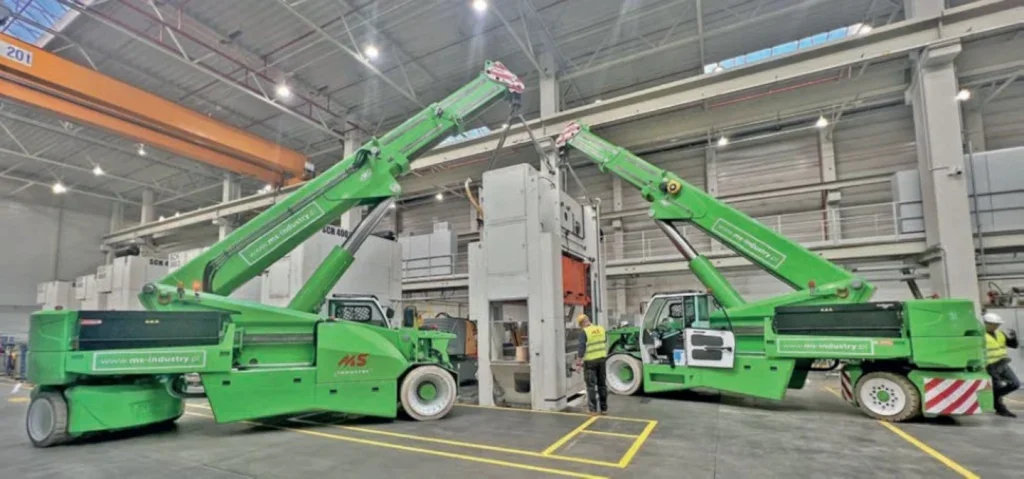
The company has focused on JMG for its fleet of pick and carry cranes. This, says the manufacturer, is due to various qualities the cranes offer.
Besides being the most compact pick and carry crane available on the market today they are equipped with a 180° steerable rear axle, which allows them to rotate along a very small turning radius, and they are characterised by a modern, attractive design, MS Industry says.
Manufacturer JMG reports that MS Industry also values its cranes’ all-electric power supply, high lifting performance combined with compact dimensions, excellent maneuverability, good versatility, and the possibility of remote control via radio remote control that allows full control of the work.
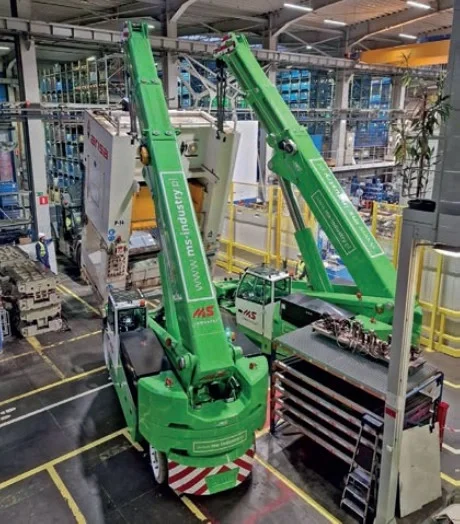
This, JMG says, is extremely important when moving large and heavy machines.
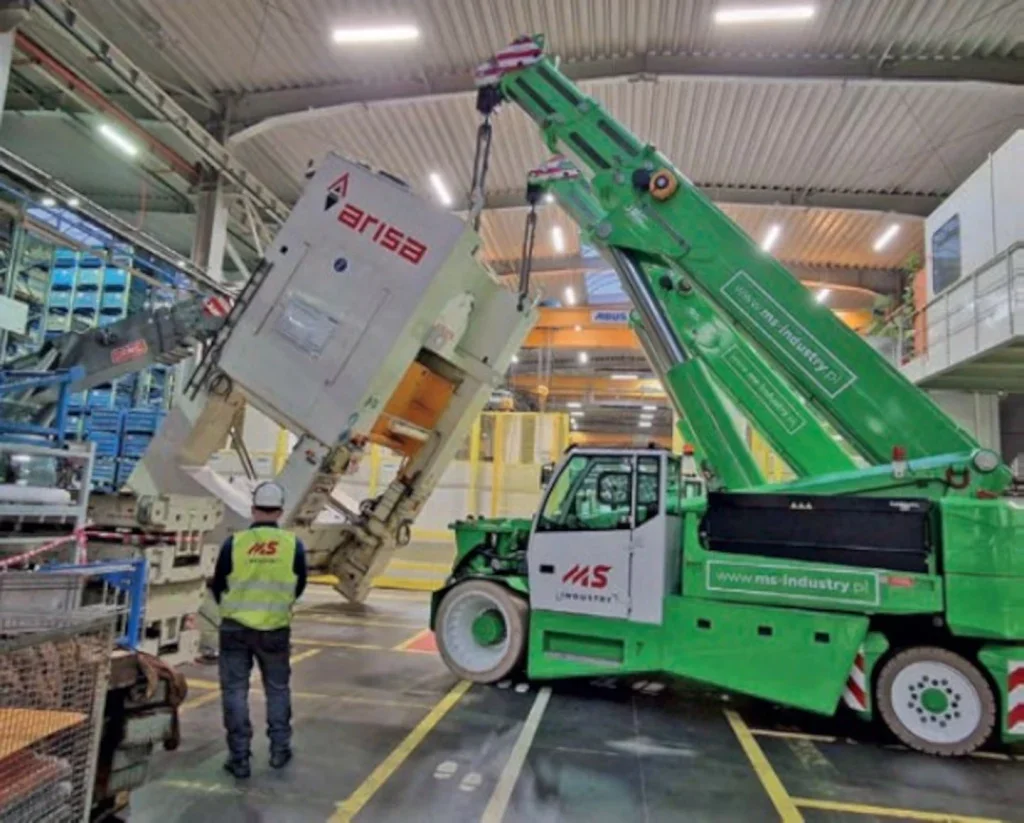
MS Industry operates throughout Europe, undertaking projects such as using two cranes in tandem to assemble, disassemble and transfer large presses. The company has also recently moved into the cardboard industry, where it moves and assembles production lines which are often housed in narrow and difficultto- access spaces.
JMG’s R&D team is now working on MS Industry’s next request: a new model of crane that can lift 80t while remaining the same size as the existing MC580.