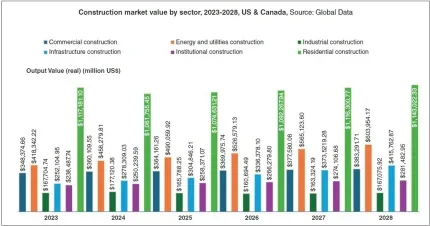
The world’s population is currently estimated at around 8.1 billion people. And this number is rising fast, with a predicted annual growth rate of around 1.25 percent. All these people all need somewhere to live. The world is, of course, a diverse place with people living in a wide range of different forms of housing. As such, a variety of different crane types are being used to help build such a range of residences.
Using the North American construction market as an example, the sheer scale, and dominance, of the residential construction market (in developed countries, at least), compared to other types of construction, is illustrated by data from research GlobalData (sister company of Cranes Today’s publisher, PMI). See Figure 1.
Despite fluctuations from yearto- year, due to macroeconomic factors dictated by things such as high inflation or elevated mortgage rates, it is clear that the residential construction sector, in terms of output value, stands head and shoulders above other the construction categories.
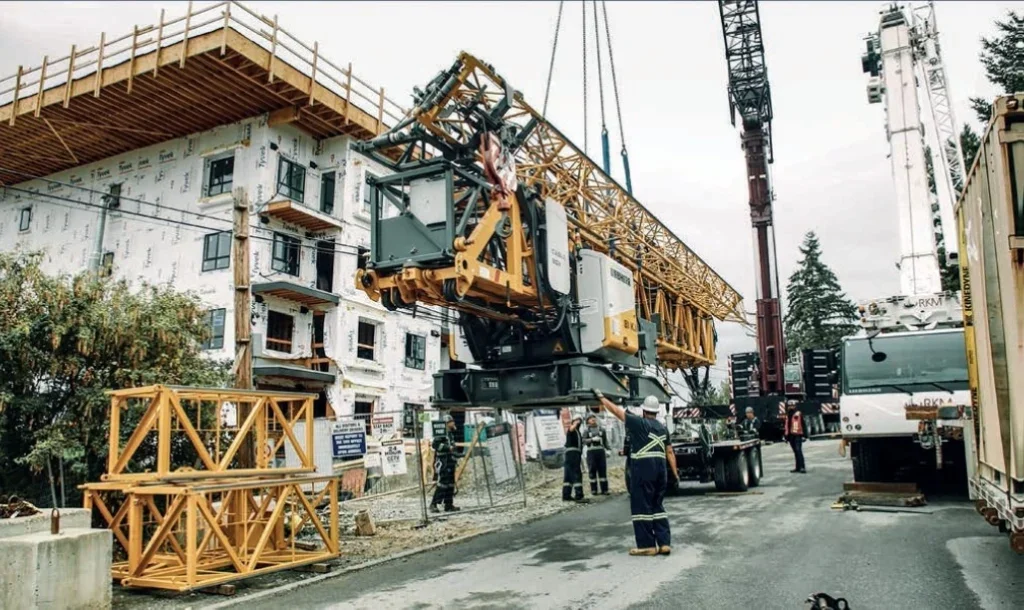
NEED FOR SPEED
In Europe one of the most common cranes used on residential construction jobsites are fast erecting tower cranes. Their rapid erection, ease of transport, small footprint and all-round versatility make them well-suited to building both detached and multi-occupancy houses. And for these reasons this crane type is becoming increasing popular in North America, too.
The multiple benefits that using a fast-erector can bring is illustrated by an example from Abbotsford, Canada-based tower crane and fast erector provider Bigfoot Crane Company which provided a Liebherr 81 K.1 fasterecting crane to help build an apartment complex, in constricted conditions, near Departure Bay in the Canadian coastal town of Nanaimo.
“The fast-erecting crane has played an integral role in various construction tasks, including trailer unloading, concrete work and the installation of rooftop equipment,” says Cale Anderson, managing director at Bigfoot Crane, who sees great potential for fast-erecting cranes in North America.
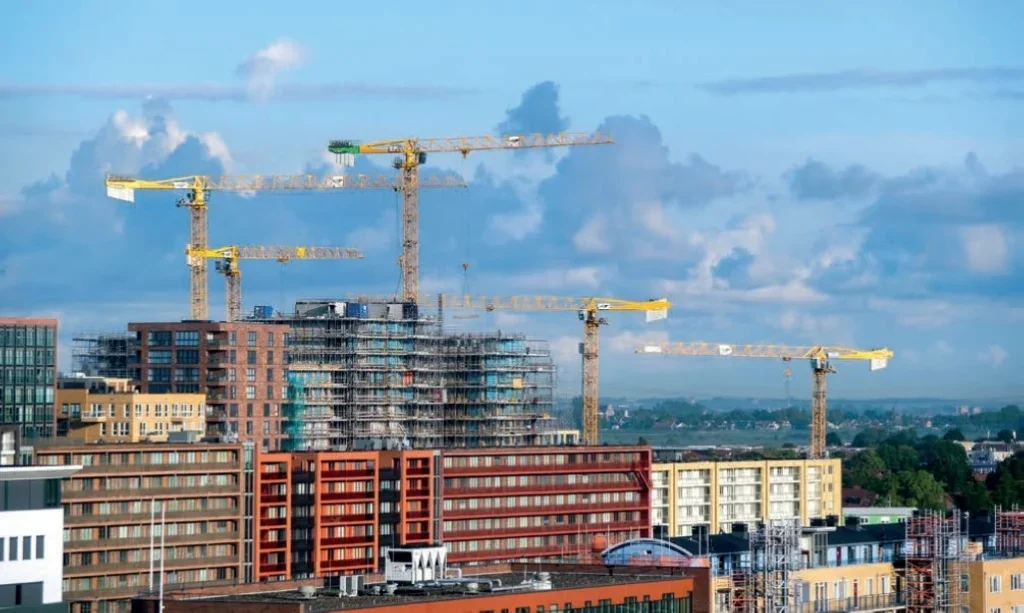
The hoist rope’s two-fall operation and the Load Plus feature are of particularly use; both functions are designed to ensure fast lifting speeds and allow heavy loads to be lifted. “Our customers especially appreciate the crane’s speed and performance that these features make possible,” Anderson says.
The 81 K.1 was used with several other cranes on site. Its maximum hook height of 38.9 metres combined with 2.4 metre tower sections meant it was able to maintain the necessary safe distance between other cranes and buildings in its vicinity and to slew above, or below, other cranes depending on the circumstances.
The 81 K.1 can lift up to 6,000kg. It can reach a maximum radius of 48 metres and has a jib head lifting capacity of 1,350kg.
An interesting aspect of the Departure Bay job, which was conducted for contractor Westurban Developments, was the dismantling of the fast erector. Assembly was, as already highlighted as a being feature of this crane type, quick and easy – conducted on the jobsite’s access road. Disassembly, however, proved a greater challenge. “It’s easy to get a crane onto site when there isn’t a building yet,” explains Anderson. “But additional challenges arise once the building is erected because of its structure. When we’re planning a project we always start by looking at how to remove the crane at the end.”
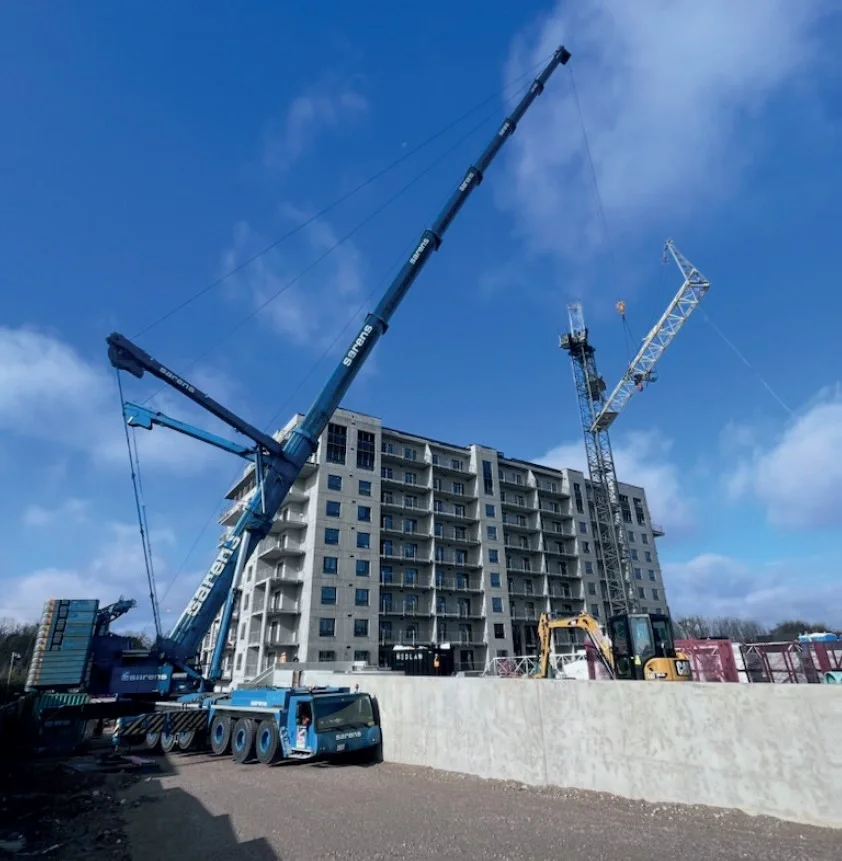
In this instance the completed building was in the way as far as normal dismantling was concerned. “This meant the fast-erecting crane had to be lifted over the newly constructed building,” Anderson continues. “A large Liebherr mobile crane was used to safely set the 81 K.1 down on the other side of the building.”
EFFICIENCY GAINS
For longer term residential construction jobs contractors may opt to utilise tower cranes, which can offer higher lifting heights and heavier lifting capacities than their ‘fast erecting’ relatives whilst retaining similar advantages of versatility and a small footprint.
Another key reason tower cranes are often used for residential construction is that, in many cases, one tower crane can be used to do the work that would otherwise require multiple smaller or mobile cranes.
Such was the case for Moldovian real estate construction company Filli Partner which bought a used Potain MD 305 B top slewing tower crane for work on its City Plaza development, a residential project under construction in central Ungheni. Building work is set to last two years, with the project’s opening scheduled for the first quarter of 2025. Once complete the City Plaza project will cover 24,000 square metres of residential space dedicated to 234 homes.
“Selecting this model eliminated the need for two cranes, delivering significant efficiency to our project,” says Iurie Gisca, founder and administrator of Filli Partner.
The Potain MD 305 B has a maximum capacity of 12 tonnes, with up to 70 metres of jib available, and the ability to lift 3.2 tonnes at its jib end. On the City Plaza job, the crane is working with its full 70 metre jib, allowing it to cover the entire jobsite.
For even larger residential construction jobs multiple tower cranes may be required. Such was the case for Dutch crane company Multi-Crane which has deployed six Potain MDT topless tower cranes (three MDT 319s, two MDT 389s, and one MDT 308 A) for the De Zaanse Helden residential project in Zaandam, near Amsterdam, in the Netherlands.
The project, consisting of ten buildings with solar panels and rooftop gardens, will add 607 apartments to the city. The Potain cranes are being used for a range of work – including lifting and placing precast concrete, formwork, floor panels, and steel structures.
The topless tower cranes were deemed essential for this project largely due to its confined space. Multi-Crane collaborated with contractor Stebru Bouw to carefully plan the crane positioning, hook heights, and oversailing – creating numerous drawings to optimise the site layout and logistics.
Commenting on the choice of Potain MDT cranes for this project Ralph Breijer, CEO of Multi-Crane, says: “Our Potain MDT topless tower cranes, with their easy erection, excellent manoeuvrability, and compact footprints, were the perfect fit. Their ability to operate effectively in tight spaces allowed us to maximise lifting capacity and efficiency, ultimately contributing to the project’s progress and success.”
Tower cranes, however, can also pose similar dismantling challenges as highlighted above with Bigfoot Crane’s fast erector. For example, another Canadian contractor, Oxford Builders, was involved in the construction of the Watson Parkway Apartments residential building in Guelph, Ontario. When it came to dismantling the tower crane that had been used for the job it needed to call upon the specialist services of international crane rental, heavy lifting, and engineered transport specialist Sarens.
To dismantle the tower crane Sarens used one of its Liebherr LTM1500 mobile cranes which conducted the dismantling in seven separate loading and unloading procedures. The operation was preceded by a major pre-planning study so Sarens could determine exactly where the crane needed to be located for effective, safe and rapid dismantling without disrupting traffic. Thanks to this the crane was dismantled successfully in just ten hours. This included the move from its Cambridge, Ontario branch to the site, the deployment of the 276ft crane boom and the loading of the crane components, weighing approximately 15 tonnes.
READY-MADE
A residential building technique that is currently enjoying a revival is prefabricated construction – specifically Prefabricated Prefinished Volumetric Construction (PPVC).
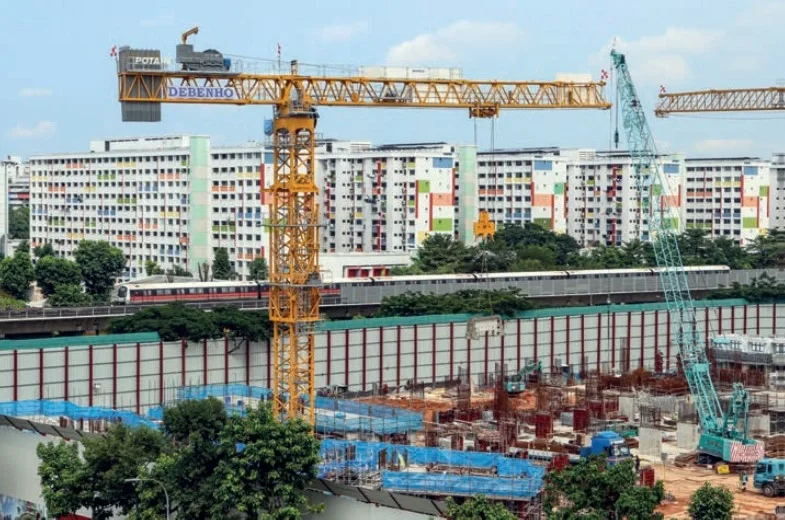
The technique is designed to increase productivity, as three-dimensional modules are completed with internal finishes, fixtures and fittings in off-site fabrication facilities before being delivered and installed on-site. With some PPVC elements weighing up to 25 tonnes strong cranes are required, with tower cranes being well-suited to this.
Illustrating this is Singapore contractor Debenho which has used the first Potain MCT 1005 tower crane in the country to construct a new PPVC housing development.
The crane was purchased by crane rental firm Manta Equipment and rented to Debenho. It is being used to place precast modules for the Yishun Central 1 (N9C3) housing development.
According to Manitowoc, with its 50 tonne capacity, 80 metre jib and up to 1,070 metres of rope on the drum, it’s exactly the type of application the Potain MCT 1005 was designed for.
For added versatility on-site there’s also a choice of counterjibs – from 15 to 20 metres.
At the Yishun Central jobsite the MCT 1005 will reach a final height under hook of 55 metres and has been configured with a jib length of 35 metres, supported by a 15 metre counterjib. This will allow it to lift and place all the heavy PPVC sections as the jib can support over 34 tonnes at almost 35 metres in this configuration. With an 80 metre jib, the MCT 1005 can handle 50 tonnes between 3.5 and 16.8 metres, and 6.5 tonnes at 80 metres.
MOBILITY MATTERS
It’s not just tower cranes, however, being used for prefabricated residential construction. Mobile cranes are being used for prefab work, too.
VDL De Meeuw, a prefab specialist construction company in the Netherlands, bought its first Grove crane last year. One of its first jobs was on seven residential buildings, comprising 500 apartments, in NDW21, a growing area in the city of Nijmegen.
VDL De Meeuw produces industrially manufactured modules at its factory in Oirschot. These were transported to site where the GMK5120L lifted them into place. Speed was of the essence as there were 1,500 modules, with each measuring 7.5 x 3.3 metres and weighing between seven and 12 tonnes. To place them the GMK5120L was configured with a main boom of 39.1 metres and 30.7 tonnes of counterweight. In this configuration, the crane can lift 12 tonnes to a radius of 22 metres.
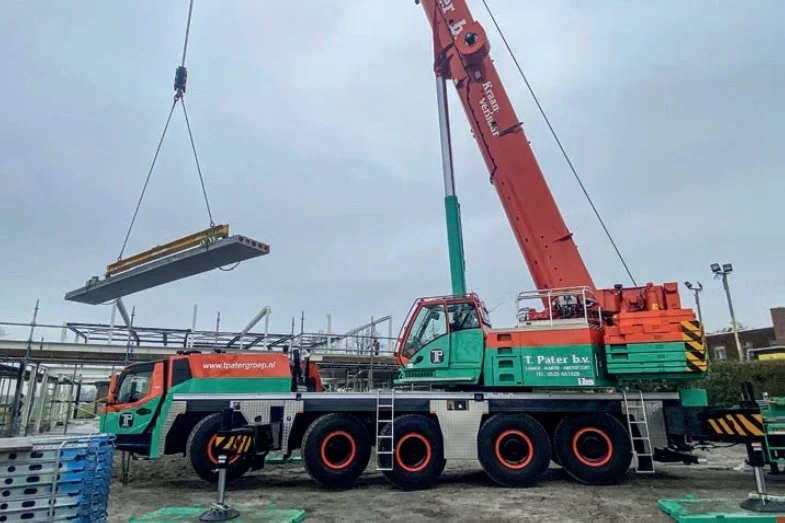
In addition to placing the modules, the crane was also used to install staircases and other items inside the developments.
“Our Grove GMK5120L completes the work as a oneman machine,” says Oscar van Sambeek, team lead of transport at VDL De Meeuw. “We don’t need to send any additional counterweight or equipment by truck. It’s a unique package and is helping us complete the work in the most effective way possible.”
Also in the Netherlands, Dutch crane rental and transport company, Kraanverhuur T. Pater, has replaced an older five-axle Grove crane with a newer, stronger option due to the increase in prefabricated construction work.
Kraanverhuur T. Pater upgraded its Grove GMK5095 all-terrain crane for a larger 150 t GMK5150XL because its customers in the construction sector are increasingly looking to lift bigger prefabricated loads.
One of the first projects for the GMK5150XL was in the village of Tienhoven where it lifted concrete floor panels for a community building and sports hall. It placed a number of six tonne panels at a radius of 16 metres and lifted them from a narrow footprint, aided by to the crane’s MAXbase variable outrigger positioning system.
In Germany, crane specialist Schußmann, based in Mammendorf (near Munich), used one of its most powerful mobile cranes, a Liebherr LTM 1450-8.1, to assemble 158 prefabricated timber-hybrid modules that will be used as resident’s rooms at Germany’s largest care home in Vöhringen.
With its 85-metre telescopic boom the LTM 1450-8.1 was able to assemble all the 15-tonne modules from just three different locations on the construction site without the need to set up a lattice extension.
Each of the fully equipped accommodation units is 4.4 metres wide and 7.8 metres long and not includes flooring materials, wall panelling, built-in cupboards, electrics and plumbing fixtures. On the top floor of the complex the 450-tonne Liebherr crane worked with just 34 tonnes of ballast.
Finally, in the USA, lifting, heavy-rigging, and heavy hauling specialist Barnhart utilised a 220 tonne (265 US ton) Liebherr LTM 1220 crane to lift and set seven small prebuilt homes for a ‘no income’ housing community initiative in Vancouver, Washington. Each home was 14ft wide x 44ft long, weighed 34,000 lb and contained 735 square feet of living space. They were brought in by trailer to be set onto their designated pads. The footprint of the entire community was small and there were power lines to consider and avoid.
For the job Barnhart’s Oregon branch deployed a ground crew team comprising one lift director and three riggers. Precision was required to successfully lift the units up in the air, manoeuvre them in place and set them in position. The job even made the news. Watch the news story here: www.youtube.com/ watch?v=luHxpGFNEm0
The homes will house up to five people each, giving those who are struggling a way out of homelessness.
In conclusion, we see that increasing global demand for housing is driving the use of a diverse range of crane technologies. Factors such as efficiency, speed, and versatility are paramount, whatever type of crane is used; finding the best solution, especially given the varied logistical challenges contractors face in residential construction, relies upon a flexible and forwardthinking approach from both crane users and, ultimately, crane manufacturers, too.