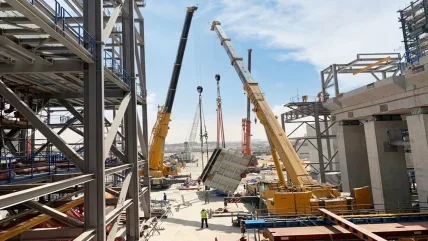
When it comes to lifting there’s more to the Middle East than simply oil. A variety of amazing lifts for a whole range of projects, from industrial to entertainment sectors, from religious buildings to hotels, are being carried out across the region. And rental firms operating there are rising to the occasion, tackling a whole host of lifting challenges with innovative solutions, as seen in this snapshot of the region’s lifting landscape.
Dubai, UAE-based heavy lift and transport specialist AL Faris claims to have the largest fleet of cranes and heavy transport equipment in the Middle East. “We have around 2,500 cranes and heavy equipment with a value exceeding USD 1.5 billion,” says Al Faris executive director Kieve Pinto. And this number is rapidly increasing…
The company’s rationale is that by buying state-of-the art heavy-lift and power generation equipment it can take on new work in new areas. “We’ve ramped up investment to acquire state-of-theart heavy-lift and power generation assets to meet the standards of the region given the array of new ventures,” qualifies Pinto. “We already have the largest on-land transportation fleet in the UAE and we are in the process of acquiring marine assets for transport of OOG cargo. This would greatly enhance our capabilities and help us meet the growing demand of the market and our clients. It would also widen the scope of the potential projects we could cater for across the Middle East.”
The company’s fleet is currently receiving a boost with 27 new Liebherr mobile cranes, ordered at Bauma 2022, which follows 24 Liebherr cranes delivered in 2022.
The order, which will continue into 2024, includes six additional LTM 1300-6.3s. “The concept of the LTM 1300-6.3 with its 90-metre telescopic boom combined with compact dimensions is perfect for universal operations here in the Middle East,” said Al Faris shareholder Keonne Pinto. “This type of crane is eagerly awaited in the UAE and Saudi Arabia.”
Al Faris is one of Liebherr’s largest customers worldwide and currently has around 460 Liebherr cranes in its fleet – including mobile cranes ranging from the LTM 1030-2.1 to the LTM 11200- 9.1 and crawler cranes ranging from the LR 1350 to the LR 11000.
Al Faris has also added a Tadano GR-800EX rough terrain crane to its fleet, as announced by Tadano earlier this year. Al Faris will use the Tadano GR-800EX on a variety of infrastructure projects. The crane was purchased through Tadano’s distributor, United Al Saqer Heavy Equipment L.L.C.
According to Al Faris the crane meets all the requirements that industrial customers have for crane service providers, including excellent performance characteristics, cutting-edge technology, high fuel efficiency, and the ability to flexibly work with various outrigger spreads.
“The GR-800EX has all this and more which is why it meets our needs perfectly,” said Keonne Pinto, who points to the Smart Chart system and the crane’s twostage swing-around jib as specific examples. “Thanks to these exceptional characteristics, our GR-800EX will quite literally pay for itself very quickly.”
He added that the high reliability of the GR-800EX, as well as the associated low maintenance costs, is something that the team at Al Faris finds invaluable.
Demand for crawler work is strong, too; not surprising given the scale of many jobs and the harshness of the jobsites.
SAVING TIME
Scale was a challenge for project consultant, Fluor, at the Umm Wu’al Sulphuric Acid and Power Plant, owned by fertiliser manufacturer Ma’aden Waad Al Shamal Phosphate Company (MWSPC). The plant is in the northeast of Saudi Arabia where a new industrial city is being built.
The plant is structured around three sulphuric acid trains containing a total of nine vast process towers; it produces almost 14,000 tonnes of fertiliser a day. MWSPC was looking to upgrade the facility and replace the original towers with cleaner, more efficient equivalents. It needed to keep downtime to an absolute minimum. The problem was the towers were not designed to be lifted in one piece when they needed to be replaced and the conventional approach for dismantling them piece-by-piece would take several months for each train.
Fluor reached out to heavy lift specialist Mammoet for a solution. Using 3D computer modelling Mammoet determined that, by using its 1,600t capacity Demag CC8800-1 and 1,250t capacity CC6800 crawler cranes, in combination with its 3,200t MSG-80 ring crane, it would be possible to reach above the confines of the site, extract all nine of the towers intact, move them to a central staging area, and hoist replacements into position.
To convince MWSPC and Fluor that this operation could be achieved, Mammoet prepared a detailed engineering study.
A finite element (FE) simulation showed how the towers would respond to the pressure of being hoisted out of the plant. And a series of bespoke frames and slings were designed to safely cradle them throughout the move.
Abdullah Terkaoui, project manager for Mammoet explains: “Our methodology enabled our customers to reduce the planned shutdown schedule for each train from 120 days to 45 days. Then, as the operation progressed, further time savings were realised: the complete shutdown of the first train was completed in 30 days; the second shutdown, where the lifts took only seven days, enabled completion in 22 days; and, for the third, the lift took just three days, with a total mechanical completion in 19 days.
“This meant that, thanks to the entire project team and everyone involved, all three shutdowns were completed two months (64 days) ahead of the original schedule – a time saving of over 50%.”
BETWEEN PRAYERS
Using a Demag CC2200 and a 100 tone Liebherr mobile crane Dubai, United Arab Emiratesheadquartered crane rental firm Johnson Arabia worked on the construction of a 168,000 square foot mosque, with a dome adorned with the verses from the Quran, in Abu Dhabi.
The build was awarded to Arabian Construction Company for a AED 600 million. The initial start date was December 2013 with a completion predicted in 2016. However, the project was subsequently delayed by a review of major projects that slowed the pace of development in Abu Dhabi. This project was completed in 2019 and recently Johnson Arabia was contracted for lifting services for the improvements on the Mosque that were initiated in 2022.
The project improvements included installing sensor activated shade canopies for the outdoor prayer areas. To provide shading for such massive areas multiple 22 tonne and 12 metre high steel columns needed to be erected and so it commissioned Johnson Arabia for this.
Based on the size of the columns and lifting plan Johnson Arabia used the Demag CC2200 350 tonne capacity crawler crane and a 100 tone Liebherr mobile crane to perform an almost tandem lift where the columns were lifted off the flatbeds and then the CC2000 was used to position the column upright and the Liebherr was used to keep the bottom of the column off the ground for accurate positioning. The biggest challenge for Johnson Arabia was the visibility of the ends of the column so the rigging team made sure to communicate with each other for every step of the lift and consult with the installation team for accuracy of placement.
Another challenge was converting the parking space near the mosque to a high load bearing area. This was achieved by strategic placement of crane mats after ground pressure calculations to ensure full safety of the equipment and lifts. Finally the team had to obtain very special permits for this job due to its high profile nature and ensured that no work was done or lifts were performed during prayer times. As prayer times occur five times a day the engineers had to carefully plan lifts that could be performed in specific time windows or ensure full safety of the columns if any of the columns were mid lift.
BALLROOM LIFT
International heavy lift specialist Sarens utilised one of its 750 tonne crawlers for a high profile build: hoisting trusses for a ballroom at the new Four Seasons hotel in Jeddah, Saudi Arabia.
The Al-Hashemiah Contracting Company called upon Sarens which used its 750-tonne LR1750 crawler crane. It successfully installed trusses weighing up to 63.5 tonnes at heights ranging from 30 to 90 metres. Lifts were performed using four lifting points without a spreader, with the crane slewing and crawling in SLDB 119m and SWDB 77m main boom + 70m fly jib configuration.
A total of 35 trailers drove the crane across 1,400 kilometres of road, a five-day journey that required special permits from the Kingdom of Saudi Arabia. Six crew members then assembled (and later disassembled) the crane, which remained on site for six weeks.
The location of this soon-to-be luxury property is near the sea, but that presents its own challenges as high wind speeds were a concern during crane operation. The twoperson Sarens team also had to contend with a worksite located in a busy residential area, and traffic management was a major concern. To perform each lift, the crane had to park in the middle of the road, which required road closure permits from assembly through full disassembly.
“The Four Seasons project was interesting,” says Sarens project engineer Shuaib Kadhem. “The site was very congested for a big crane like the LR1750, so the team had to communicate closely throughout the entire operation. The challenging part was the rigging arrangement: we had four lifting points with an eccentric centre of gravity, which meant the use of a spreader was not an option. Despite installations as high as 90 metres, we lifted all the loads safely.”
TOWER CRANE DEMAND
Demand for Terex tower cranes has come from Israel where Tel Aviv, Israel-headquartered automotive specialist Mayer’s Cars & Trucks (MCT), which is also a distributor for Terex Tower Cranes, has ordered 15 new Terex tower cranes. This follows an order for 11 placed at the end of 2022. Terex says the fleet will support MCT in serving the growing demand in the Israeli market for tower cranes.
The latest order consists of a variety of flat top and luffing jib tower cranes, including the new CTT 292-12, a flat-top 12 t capacity crane with a jib length of up to 70 metres and a tip load of up to 3.06 tonnes.
Lee Maynard, global sales director – Terex Tower Cranes, said, “We are delighted with this significant order and furthermore, MCT’s commitment to our partnership. Having been in Israel in December, it’s clear the opportunities there are vast for both Terex and MCT during this year, and the years ahead. I believe our timing is perfect to enter this market, with a first-class partner in MCT.”
Terex is also enjoying expansion in Oman where its Australiamade Franna brand of pick and carry cranes and its rough terrain cranes, which are manufactured in Crespellano, Italy, are now available through construction equipment distributor International Integrated Equipment (IIE).
To mark the partnership the companies conducted a ceremony at IIE’s office in Muscat. At the ceremony Ajit S. Nair, head of sales, Middle East & Asia, Terex rough terrain cranes and Franna pick and carry Cranes, said, “The Middle East is an important region for Terex in terms of current and future potential. We have been a leading crane brand in the Middle East region for many years and to enhance our capabilities even further and to serve customers better we have a clear strategy of going with the distribution model.
“It is imperative to have the right partner; we invest in them, they invest in us and we grow together. IIE, a Suhail Bahwan Group company, is a highly reputed organisation, has the market knowhow and is focussed on customer service. We are delighted to have IIE as our partner in Sultanate of Oman.”
Overall, it seems that the lifting landscape in the Middle East is thriving, driven by increased investment, technological advancements, and the ability of rental firms and heavy lift specialists to tackle complex challenges with innovative solutions. The region’s commitment to delivering impressive lifting projects sets the stage for continued growth and development.
The ‘King of barges’ buys the very first Liebherr Lr 1400 SX model in the Middle East
Al Jazeera Shipping Co. W.L.L. is one of the largest marine operators in the Gulf region with a fleet of over 150 units consisting of various sizes and types of tugs, barges and other equipment. It has extended its crane fl eet with Liebherr’s brand new LR 1400 SX crawler crane.
According to Liebherr, back in early 2022, Mr. Ali Hasan Mahmood, managing director of Al Jazeera Shipping, commonly known under his alias ‘The King of Barges’, expressed his desire to renew one of his used older generation crawler cranes. This led him to various suppliers and his attention was caught by the latest addition to the Liebherr crawler crane range: the 400-tonne LR 1400 SX.
Liebherr says apart from the crane’s load curve and safety ratings, Mr. Ali Hasan’s decision to go with the LR 1400 SX was driven by the model’s short assembly time, its preselection feature of individually customised load charts and, its capability to preselect barge inclinations which automatically applies the permitted load curve. The LR 1400 SX has been commissioned and is working on several projects with Bapco and its refinery in Bahrain.
Al Jazeera Shipping Co. W.L.L. has been active in both the maritime and the offshore and oil industries for over 45 years. The main activities of the company include chartering tugboats, supply boats, accommodation and work barges, as well as leasing offshore construction equipment. The company also has its own marine fabricating yard to carry out the associated repair and maintenance jobs. It covers an area of over 80,000 square metres with 300 metres water frontage and is adjacent to the Mina Salman Port area.
“We are proud to be the first company in the Gulf to receive the Liebherr 400-tonne LR 1400 SX crawler. Hopefully more Liebherr crawler crane purchases are to come with the assistance and full cooperation from Liebherr. A great association,” said Ali Hasan Mahmood.