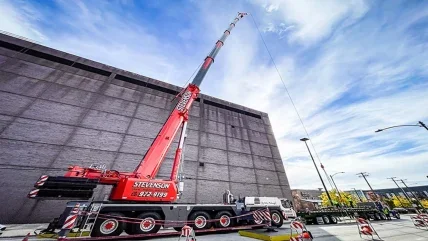
The 250–300t segment is one of vigorous competition and fine differentiation. It includes both five- and six-axle cranes, dividing at the 300t mark, with a wide variety of boom lengths. Liebherr, for example, offers a 60m boom, on the five axle 250t LTM 1250- 5.1, and an impressive 90m on the six axle, 300t, LTM 1300-6.3.
In Europe, crane owners can find plenty of taxi crane work, in densely packed and closetogether cities. For fleets like this, a compact crane, able to navigate constricted urban roads and job sites, with a long boom, able to work immediately without extensive rigging is key. The same sort of requirements apply to fleets working in US cities like New York or Chicago.
But the USA is a big country. Road regulations are set by local states and municipalities and often vary between neighbouring jurisdictions. Cranes for this market – like those in other big countries such as Australia – must be designed for long distance travel, at the lowest possible axle loads, and highest possible speeds.
That has shaped the development of cranes by the only Western manufacturer with an all terrain factory outside Germany: Kentucky’s Link-Belt. Since 2008 the company has been making use of its own boom forming machine and turned out more than 1,000 booms a year, producing its 10,000th boom in 2017.
The company’s self-formed booms were at the core of the design of its five-axle 275USt (250t) ATC 3275 and are now being used in the largest all terrain in its line-up: the five axle 300USt (275t) 300|AT. This is the highest capacity five axle all terrain on the market and carries a 72.5m main boom, the second longest on a crane in this class.
A key focus of a crane like this is its roadability and, as Link-Belt product manager Andrew Soper told Cranes Today at ConExpo, this has driven its design in many ways.
“It offers excellent mobility with just four overflow loads needed in America,” Soper says. “In North America, the typical payload for one truck is 44,000 lb. We design and optimise our counterweight splits to maximise counterweight on trucks.”
Around the world, mobile phone companies are increasing data transfer speeds by installing new 5G masts. Compared to their 4G predecessors these typically transfer data faster but over a smaller area. Old cell towers must be upgraded and new ones built. That’s perhaps not such a challenge in cities but will demand frequent travel between sites for crane owners serving this market in America’s rural and ex-urban communities.
“Cell towers typically have a very restricted work area,” Soper continues. “Where we’re from, they’re always on the top of a mountain and they’re hard to get to and it’s hard to get trucks up there. So not taking a lot of trucks is a good thing. Being able to take one truck and do long boom, tight radius, high tip height work is a big advantage for this.
“A crane operator in Texas, for example, has the ability to carry the counterweight tray on the deck of the crane, which is going to improve their flexibility and efficiency in transportation because they’re now carrying more counterweight in two trucks than they would be otherwise. In other markets where they can’t carry counterweight, it’s still very efficient. Some of our competitors in this class require five truckloads to take all their counterweight.”
Maximum counterweight is just over 73t with four overflow truckloads, and for improved mobility and efficiency for a variety of job site scenarios the 300|AT can be set up with two overflow loads and 33.6t of counterweight.
With its maximum boom and jib system, the new AT|300 can reach a height of 112m. This is slightly more than that offered on Manitowoc’s GMK5250XL-1, but the five-axle 250t Grove has, as the name suggests, an extralong 78.5m main boom. The next highest capacity crane in the segment, Liebherr’s LTM 1300-6.2, also has a longer boom, at 78m, but only reaches a slightly higher maximum system height of 114m.
Those long distances and the need to navigate multiple jurisdictions at low axle loads, helps explain this different approach to boom length. European cranes typically carry their main boom over the cab, allowing them to handle tighter corners. But this adds to axle loads. All terrain owners who want to travel longer distances, often want to carry the boom behind the cab, on a boom dolly, for lower axle loads. It makes sense for a boom designed from the start for use with a dolly to be slightly shorter.
“That allows you to distribute the vehicle weight over more axles by putting the boom in a trailing dolly,” says Soper, “You’re under regulation weights for multiple states, so you don’t need to stop [at state borders] and wait for your paperwork.”
According to Soper this approach is followed across the crane’s design: “We have a higher travel speed at 55 mph. That’s on the high end for the all terrain frame market. Typically all terrains are road speed limited at 49mph. We’ve also incorporated a two fuel tank system with a maximum capacity of 160 gallons of fuel. Being a single engine crane you have to be able to get to the job and have enough fuel to do the work.”
The crane is designed with a low emissions future in mind. Arguably, just by forming booms on site, the manufacturer is cutting the embodied emissions of its cranes: it’s slightly more efficient to ship flat plate and then form it, than to ship formed booms. But day-today, the crane cuts emissions with an efficient modern engine, which is ready to be used with HVO fuel.
Soper sees potential for the crane in the telecoms, heavy civils, wind farm assembly, and oil and gas sectors. At the same time, he says, the crane is well suited to taxi work.
LONG LIEBHERR
Liebherr’s LTM 1300-6.3 takes a markedly different approach to boom and carrier design. This crane, like all of the 300 metric tonne cranes on offer, travels on six axles. Other cranes in the segment, including Liebherr’s LTM 1300-6.2, Manitowoc’s GMK6300L-1, and Tadano’s AC 6.300-1, have booms of around 80m (the other Liebherr is a couple of metres shorter, at 78m). The LTM 1300-6.3, launched in 2022, adds ten metres to this, with a boom length of 90m. Maximum height for all four cranes ranges from 114m on the shorter boom Liebherr through to 123m on the Tadano.
Like the new Link-Belt the big Liebherr is well-suited to work on telecoms masts, Liebherr says, but it also can be used for tower crane erection. Being able to turn up to a city centre job site, set up your outriggers asymmetrically, and start lifting on a 90m boom, can help reduce the need for road closures.
To achieve these impressive main boom lengths and accommodate the additional boom section needed compared to other cranes in this class, Liebherr has focused on a highly optimised use of steel.
Larger cranes used on tower crane erection, and other jobs, will often offer the option of rigging a luffing jib. The new 300-tonner does not but it does offer a range of lattice boom extensions, many of which can be shared with other cranes in the Liebherr range.
The crane can be transported with its full boom, outriggers, and hook block, within axle loads of 12t. Even this is not light enough for some transport routes, where uses must keep below 10t per axle. To meet these requirements, the crane features Liebherr’s teleseparation system. This allows individual boom sections to be removed easily, simplifying the process needed to get the six-axle crane down to a total load of 60t.
Boom removal and reassembly can be made even easier with Liebherr’s self-assembly system. This allows the boom to be removed and fitted, without the need for an auxiliary crane. Like many of the crane’s lattice sections, this system can also be used on other cranes in the range, such as the larger LTM 1650-8.1 and the LTM 1450-8.1. That could make the six axle, 90m main boom, 300-tonner a useful part of a fleet of urban taxi cranes, able to take on occasional work at considerable heights, with a single boom selfassembly system and some lattice jib components, shared efficiently between larger cranes.
SET-UP SELECTION
All of the Western mobile crane manufacturers have, over the last decade or so, been working to improve the optimisation of crane capabilities in awkward set-up conditions.
Link-Belt’s system, offered on the 300|AT, is V-Calc. Liebherr has been something of a leader in the development of these systems, and implements them in different combinations on different crane types.
Liebherr’s variable outrigger system is known as VarioBase. Like other systems, it lets an operator set outriggers up according to the space available, and then clearly see lifting capacities at different points around and away from the crane.
On the LTM 1300-6.3, Liebherr is offering its VarioBase Plus system. This incorporates a double-stage extension system on the rear outriggers, increasing their maximum spread by two metres, to 9.4m. The front outriggers, with their single stage extension, do not reach out as far, but are lighter. This allows operators to increase the crane’s stability, while helping to optimise transport weights.
Ballast can similarly be Liebherr’s LTM 1300-6.3 has a 90m boom adjusted to balance transport weight, set up space and tailswing restrictions, and lifting capacity, using Liebherr’s VarioBallast system. On the 300-tonner ballast can be set at 4.94 m or 5.94 m and is easily adjusted using a mechanical system. This allows the latest version of the crane, the LTM 1300-6.3, to achieve similar lifting capacities to the earlier 600t model, the LTM 1300-6.2, with 8t less ballast. That ballast can be secured on the crane’s turntable using Liebherr’s ‘one button’ Auto- Ballast system.
Wind speeds increase with height. The ‘canyon’ effect of skyscraper-lined city streets can further increase gusting. As the crane industry learned in the first years of widespread wind farm development, the effect of wind on loads can be catastrophic. So it makes sense that Liebherr should transfer some of the lessons learned from the wind energy sector to a tall city-focussed crane like this.
Liebherr has developed load charts for different wind speeds, allowing work to continue, within safe limits, even when gusts exceed the 9 m/s that is typically the maximum for crane operations.
The new load charts allow operators to work at 11.2 m/s, or even 13.4 m/s, when using lattice equipment. In pure telescope mode, the tables even allow for a speed of 15.6 m/s. They are all stored on the crane’s control system computer, allowing operators to switch between them when needed. If the wind speed measured on the crane’s boom during a job exceeds the set chart wind speed, the crane operator can simply switch to a load chart with a higher maximum wind speed, Liebherr says, which will often allow the job to be continued.
GOING ‘EXTRA LONG’
All of the most recent versions of cranes in this class offer substantially improved boom lengths compared to predecessors. As we’ve seen, a long boom can let you get to work quicker, and often means less loads needing to be carried to site. Today, all cranes in the 250-275t class offer at least a 60m boom, compared to the 50m that would have been standard a few years ago.
In fact, only one crane in the group – the Liebherr LTM 1250- 5.1 – reaches to just 60m. The Link-Belt ATC 3275 reaches 68m, and its bigger successor, the 275t 300|AT, reaches 72.5m. Manitowoc’s GMK5250L-1, along with Tadano’s AC 5.250-1 and upcoming AC 5.250-2, all offer a 70m main boom. With the GMK5250XL-1, Manitowoc has gone extra long. The five axle crane carries a hefty 78.5m main boom.
That’s 8.5m longer than any other 250t crane, an extra 50cm of main boom reach compared to the six axle LTM 1300-6.2, and only slightly shorter than most other cranes in the sixaxle, 300t class (with the exception of the new LTM 1300-6.3).
The crane’s extra-long boom allows it to be used flexibly, on a range of challenging job sites. Two recent tandem lift jobs by Spanish rental company Tinlohi demonstrate the wide range of requirements the crane can meet.
On both jobs, one on a wind farm and one at an industrial facility, Tinlohi used its XL crane alongside a GMK6400. On the wind farm, the company had been contracted to dismantle a turbine in Palencia, in north western Spain. The GMK6400 was rigged with 35t of counterweight to support its maximum 60m boom plus a 30m fixed jib. It lifted just over twothirds of the load.
Alongside it, the five-axle GMK5250XL-1 was also rigged with its maximum boom and fitted with a 9.4 m jib. The counterweight was 30.5t for the GMK5250XL-1 to manage its role in supporting one-third of the load. Components were lowered from a height of 90m. The company was able to complete the job in a day, including crane set-up.
In nearby Valladolid, Tinlohi took on another dismantling job, this time at an industrial facility, where they were to remove a drying tube from a gasification plant. The cranes were set up to split the 55t load equally, with the larger crane set up with boom extended to 40m, and carrying 45t of counterweight, while the XL crane’s 72.5m boom was at 41.2m, with 65t of counterweight.
“This was another challenging project, as we had to coordinate the swing of each lift to pass the tube section between silos into the staging area,” said Tinlohi commercial director Alberto Lozano. “Nevertheless, all of the work – including preparation – was completed without a hitch before lunch.”
UPCOMING ATTRACTIONS
Tadano’s focus at ConExpo was very much on its new green solutions, including the electric rough terrain that we previewed in the last issue of Cranes Today. But, late last year, the company released preliminary load charts for the new generation of its fiveaxle 250-tonner: the AC 5.250-2.
Both cranes feature broadly similar characteristics, with the new crane carrier slightly longer. The preliminary load chart for the second generation model suggests more flexible options for jib extensions, offering a little more overall system height. One exciting result of the Tadao acquisition of Demag, perhaps, is the fact that this crane is able to be fitted with Tadano’s HTLJ, or hydraulic telescoping luffing jb, which has often been used in Japan to extend over buildings. Many installers of rooftop HVAC units or telecoms cells may see good uses for a crane with a 70m main boom, which can also carry a load up to 20m horizontally over obstacles.
Tadano highlights the same sort of variable set up systems now common across its cranes, and those of its rivals. These include IC-1 Plus, the company’s variable counterweight system, and IC-1 Remote, its cloud-based management tool. Other system include Surround View, the company’s camera based system, which eases positioning on job sites and helps reduce the risk of colliding with pedestrians and cyclists on the road.
Detailed lifting characteristics for the new crane weren’t available at the time of writing, However, Tadano says that it will offer ‘bestin- class performance for a 250t crane with a 70m boom’.
It looks likely that this segment will remain one of intense competition, with a wide range of options for crane buyers, for years to come.