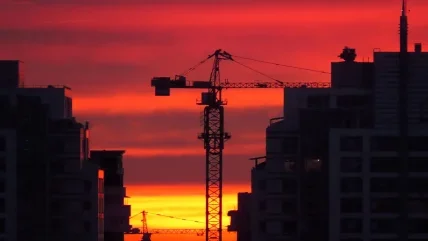
In the history of high-rise construction the idea of putting the lifting equipment on top of the structure under construction has a long tradition. For example the typical skyscraper construction of the early 20th century relied on derricks based on the inner steel structure of the buildings. Since the middle of the last century more and more internal climbing tower cranes took over their job with considerable savings in construction time. However, when topping out the tall building, a roof-mounted lifting device may be the only choice for bringing down the climbing tower crane.
When discussing the special design features and the market prospects of roof-mounted cranes, one can identify five distinct categories:
1. Conventional mobile lattice boom crane uppers mounted on purpose-built adapter frames connected to thesupporting roof. Depending on the required under-hook height of this ‘pedestal crane’, special reeving or dual hoist winches may be required. Depending on the specific job site, maximum load moment generally varies between 50tm and 340tm. In North America Manitowoc, American and P&H crawler crane uppers were used in this way as original successors of the derrick cranes in heavy steel construction. Although this lifting equipment seems to be a simple solution, the heavy rigging weights of the crane components are an obvious disadvantage. Therefore, since the 1980s it has been only a niche market, demonstrated by bridge pylon mounted versions for cable erection in suspension bridge projects. For this special application, Kobelco dramatically modified its standard crawler crane uppers.
2. Stiff leg derricks and modular lattice boom jib cranes made up of lightweight compact crane components up to a load moment of 220tm. Generally these cranes are specialised hoisting equipment belonging to crane rental and rigging companies. Either built or modified in-house, they incorporate the extensive experience of the operating company. Typical examples are the Sheedy 30 US ton (27t) and 50 US ton (45t) crane,Wilbert’s 35tm Wolff 30A recovery crane and the 140tm Favco 240R operated by LCR Lindores.
3. Standard tower cranes, mainly top slewing luffing jib cranes, rigged on limited crane towers or even with not tower sections but instead mounted on a special base frame connected to the roof by anchor screws. The maximum load moment is comparable with that of tower cranes in the manufacturers’ standard product range. Depending on the crane size, up to 2,000tm has so far been achieved. Internationally well-known are the TG (Tower Gantry) series operated by Cornell and Jake’s in North America. However, nearly any other standard tower crane can be converted into a versatile roof-mounted version, as long as the corner loads can be transferred into the building. Instead of a crane tied to the building under construction, there is no interference with the building’s front erection sequence. The higher the building, the more tower sections can be saved.
4. Specially designed pedestal luffing jib cranes, in most cases travelling on rail or skidding devices over a girder framework. Smaller units are mounted on a cruciform base, a limited crane tower or a travelling undercarriage, and they are mainly used as assist cranes on large construction projects or as recovery cranes to dismantle large internal tower cranes. Most Japanese tower crane manufacturers like IUK (formerly IHI), Hitachi,Ogawa, Kitagawa, Koshihara and Sanoyas provide an extensive range of these so-called ‘universal cranes’. Heavylift units with a load moment of up to 3,500tm built by Kitagawa and Sanuki Iron Works are suitable for heavy steel erection work like boiler house construction at power plants or bridge construction. While in Japan the era of these giant machines is linked with the massive suspension bridge construction programme of the 1980s and ’90s, in Europe boiler house construction in the 1970s led to the development of special roof-mounted slewing cranes like the Liebherr 350L/ 450 with a maximum capacity of 24t at 13.5m. Due to a change in construction methods for bridge erection and the increased capacity of flexible tower crane designs, development of larger capacity units ceased.
5. Compact derricks and portable cranes with telescopic booms or short sectioned lattice booms up to a load moment of 20tm. All crane components are small enough to be transported by conventional elevators, moved by pallet jack and manhandled for positioning and assembly. This category includes the revolutionary telescopic boom mini-crane concept of Herkules, Lasco, Potain PC10 (which can be traced back to Ron Laczko’s original LL10T design) and the more recent Xena
Applications
The broad field of applications of roof mounted cranes only leaves room for a close look at some extraordinary machines and their adaptation to specific site requirements.During the massive Japanese bridge building programme of the 1980s and ’90s, on medium sized cable-stayed bridges conventional tower crane uppers were set on top of the bridge pylons for cable installation. However, longer span bridges like the Akashi Kaikyo and the Kurushima Kaikyo Bridge,with pylons up to 282.8m high, needed a new approach. In case of the Akashi Kaikyo Bridge, a total of 50,500t of main steel cable had to be installed. In addition, a catwalk system had to be put in place beforehand for the safe erection procedure. Because bridge tower construction was carried out by a large climbing tower crane capable of lifting 160t at 35m, it was feasible to install a preassembled 63t crawler crane upper – in a single lift – onto the bridge tower’s top. To cover the working area for both mainbridge cables, normally two cranes had to be installed into limited space on top of each bridge pylon. Therefore a small tailswing on the cranes was essential.
Kobelco modified the 7150 series crawler crane upper, a 150t capacity rated machine, specially for this application. Two similar hoisting drums with 680m of wire rope on each drum are connected by chain to drive as one unit providing a four fall line operation to manage the required 309m lifting height. A special hook block arrangement keeps the two dual line falls from each drum an equal length. Capacity at 15m radius is limited to 20t while at 28m maximum radius 8.3t can be lifted. Instead of the standard diesel drive whose fuel supply would be risky under hazardous working conditions, an electrical motor was installed. Safe access to A-frame,boom and the machinery deck was assured by additional platforms and handrails within the relevant 5.6m counterweight radius. Over the course of four years, about 15 units of these Kobelco 7150BP-A models were built with undercarriages specially designed for each individual bridge pylon shape. Bringing down the cranes required a climbing jib crane or truck crane operating from bridge road level.
Although it looks like a standard lattice boom crane upper, the Sheedy 30 ton crane overcomes the traditional disadvantages of a heavy one-piece machinery deck by extensive modifications. The Sheedy Drayage Co designed and built the crane to assist construction of high-rise buildings in California and to bring down climbing tower cranes, such as on the prestigious tratosphere tower project in Las Vegas. Sheedy converted the original Clyde frame six double-drum hoist to hydraulic power drive by a Cummis diesel engine. The derrick hoist is made up of a modified American 90-B two-drum hoist driven by an hydraulic motor powered by a 40hp (29.8kW) electric motor. Up to 1,368m wire rope can be stored on the hoist drum for four fall operation at 300m height. With a maximum component weight of about 3.5t, the crane can be easily dismantled with a small derrick or mini-crane. With 33.4m maximum working radius, a wide area can be covered. The 50 ton version even reaches out to a radius of 47m by using a boom and fixed jib combination. This larger crane with its back mast looks like a small lattice boom crane with ringer attachment. At 5.2m counter radius the ballast carrier is rotating on a 9.8m x 9.5m grid which can even be equipped with rail going bogies. California-based Bigge Crane & Rigging Co also operates a 30 US ton capacity roof-mount lattice boom crane, this time based on a modified P&H lattice boom crane.
In October 2002 Sydney’s 134m-high Hilton Hotel tower, built in 1974, was closed for an intensive 18-month refurbishment programme. When it re-opens in a few months’ time, it will stand 3m taller, be surrounded by a new transparent opened-up podium and have a new name – Grand Hyatt. General contractor Leighton engaged crane hire specialist LCR Lindores to install tower cranes on top of the building as main lifting devices. Rigging the 55t cranes on top of the 44-storey building in the inner city provided a challenge and the erection steps were carefully planned over the course of 12 months before the project started. Design and positioning of the assembly cranes was critical. 3D modelling was used to ensure that boom and A-frame installations were not impeded by the assembly crane’s jib and working radius. Firstly, a 150kg capacity barrow hoist was moved on top of the building by an levator to lift components of a lightweight gin pole derrick from the podium level to the roof. Aided by the assembled gin pole crane, a stiff leg crane reached roof level. This crane, with a capacity of 3t at 15m, was in turn used to assemble a Favco 240 R recovery crane (capacity: 14t at 10m) and its supporting grillage anchored to the building. With a maximum component weight of only 3t and self-dismantling devices, this special crane has found a niche market in Australia since 1989. The 26m-long boom had to be assembled on the Hilton Hotel roof by pushing it out as new sections were added. Finally, the diesel-hydraulic Favco 240R assembled one Favco 1000E series II and a further Favelle 310D tower crane on a special roof-mount adapter frame. Both conventional tower cranes, with a maximum load moment of 375tm, were equipped with split machinery deck to reduce the weight of the heaviest component to 8.5t.
The inability of the upper building columns to support the uplift of the cranes was overcome by coring down through two levels of the structure and clamping high-tensile threaded bar to the structure’s walls. Adding to the complexity, the hotel was still in operation while the cranes were being installed and all lifts from street level had to take place at night with full road closures. After finishing the renovation project the two cranes will be returned to the ground by the specialised recovery cranes.
In Europe, the Wolff 30A is one of the very few recovery cranes in operation. It belongs to tower crane rental specialist Wilbert Kranservice in Germany. Recently the former government district in the city of Bonn got a new landmark with the topping out of the Deutsche Post AG headquarters, called Post Tower. This 41-storey glass-clad building is made up of a pair of semielliptical towers with their flat sides facing each other. General contractor Hochtief used two external climbing Liebherr 180 EC-H tower cranes on 500 HC mast sections to reduce the number of tie in supports to raise the concrete structure. Subcontractor Stahlbau Queck was responsible for steel erection, including rigging an 11m-high penthouse structure on top of the 158m building, together with a facade border surrounding the building’s edge at the same height. Because the Liebherr cranes climbed down before this work started, an extraordinary crane concept had to be developed.
First attempts to bring in long reach mobile cranes were quickly abandoned because the necessary road closures were prohibited. An alternative installation of 160m free-standing tower cranes was too expensive as they would only be used for three months. Wilbert identified two roof areas next to the lift shafts to install two Wolff WK 92 SL saddle jib tower crane uppers directly mounted onto the ballasted undercarriage, fixed on a purpose-built steel grid supported by the 151.4m high roof and the lift shafts, 7.2m higher, at the corner of each tower shaft. At their maximum 30m radius the Wolff cranes still can lift 3.25t. The first WK 92 SL could be rigged with the assistance of the last Liebherr 180 EC-H tower crane climbing down the side of the building. However, another solution was needed to erect the second crane and bring them both down. Wilbert brought in the lightweight Wolff 30A recovery crane, strategically placed on the roof to assemble the second WK 92 SL. Its central ballast was made up of special low weight 2.5t concrete slabs instead of standard 5t units. This meant that the remaining components of the WK 92 SL,weighing up to 4t, could be easily handled by the electro-hydraulic driven Wolff 30A. Due to space estrictions on the curved roof, the saddle jibs of the WK 92 SL had to be prerigged on roof-mounted support frames above penthouse level. Derigging of the two WK 92 SL cranes required replacement of the Wolff 30A on the roof. The compact crane could cope with such difficult working conditions thanks to its self-ballasting equipment and ability to self-assemble the jib above ground level, by inserting jib sections through a kind of climbing device. The mast climbing platform system used for glazing the Post Tower was also used for taking down the Wolff 30A after it had dismantled the WK 92 SL cranes.
The Wolff 30A can be operated on a 2m x 2m base frame anchored to the building (like on the Post Tower project) or mounted on a cruciform undercarriage made up of lightweight components, specially designed by Wilbert. Whether stationary or travelling on rails, a site specific lay out is achieved. Up to 25.8m of jib can be rigged, providing 1.25t capacity at a maximum radius of 25m, while the maximum load of 6t can be handled up to 6.8m radius. In single fall condition a maximum under hook height of 600m can be obtained. Together with the small sized components which fit into a lift, this feature makes the crane an ideal lifting tool for service work on high rise structures, especially in cases where helicopter lifting is prohibited and other cranes would need to be too large to be economically viable.
Modern office towers are often made up of a slipformed concrete core system, supporting the building and providing space for elevators and mechanical systems. Once a core is finished, structural steel is installed around it to form the floors. Normally, tower cranes serve the concrete core construction. Generally the free-standing tower height of luffing jib cranes usually serving such sites is restricted to 50m or 60m. As the core climbs, the tower crane has to be tied to the core at various levels to allow the crane to be extended. Should the same cranes be kept on site for steel erection, their capacity has to be considerably higher than for the concrete work. Concrete construction uses luffers in the range of 100tm to 180tm. Steel erection needs luffers of 250tm to 450tm, with considerably stronger – thus more expensive – mast systems. Furthermore, necessary tie-in supports will impede the cladding or glazing of the building’s facade.
At the 34-storey One Churchill Place project at London’s Canary Wharf, the new headquarters of Barclays Bank, a sophisticated but economic solution was found. The massive concrete cores were constructed by assistance of four tied-in Wolff luffers ranging from the WK 180B to the WK 320BF. Before the Wolff luffers climbed down beside the cores, four massive Comedil CTL 400-24 luffers and oneComedil CTL 250-16, supplied by rental company Select Tower Cranes,were rigged directly on top of the cores. Select used special frames with anchoring screws to install the cranes either on purpose-built small mast sections, leaving just enough room for the swinging counterweight above the core edge, or on a single standard tower section. Towering in this way about 160m above ground level, the cranes carried out all necessary structural steelwork. This solution, unlike internal climbing cranes, avoiding getting in the way of fit-out work on the cores and the installation of lifts and services. In contrast to a tower crane sat on the ground, the rental rate is dramatically reduced because tie-in supports, climbing frame and a large amount of tower sections are not needed. Furthermore, no free-standing large tower crane will affect the temporary foundation or get in the way of piling machinery. However, the tops of the cores have to cope with the forces generated by the cranes. As the design of skyscrapers has been reviewed after the attack on the New York World Trade Center in 2001, robust large scale concrete cores are available, limiting the additional requirements for top mounted cranes. A further benefit of the roof mount crane concept is the absence of any risky and time consuming climbing procedure.
Other special machines have been developed to cope with niche market conditions. These include the mini telescopic boom models in the tradition of the Lasco or Herkules models. There are also mini towers. UK-based Vanson Cranes introduced the MC6/MC12 mini tower crane to its home market. With a maximum capacity of 1t and a saddle jib length of 12m this lightweight Micro Crane, following the flat-top design features, replaces the Tornborgs Magni- Lite S-1000/6 cranes. A more unusual crane concept is the Vanson VC20.1L micro luffing crane, which has a tip load capacity of 1t at 20m radius. The A-frame and ballast of the compact crane is only 2.5m high and the counter radius is limited to 2m. Therefore it can even beoperated as a floor crane on high buildings under construction. The heaviest component, which is the upper slew ring,weighs only 184kg, so the crane can be rigged by manpower where site logistics demand. If required, the VC20.1L can even be rigged on a conventional tower crane mast overslewing obstacles on the building roof.
Also from the UK is Xena Cranes, which built its 10t capacity XP25 telescopic mini crane with numerous options in mind such as crawler tracks, various winch sizes and fly jibs. The XP25 can be even be rigged with lattice boom providing a larger outreach up to 19m, compared to the 11m telescopic boom.
Timberland Equipment, the Canadian manufacturer better known for its derrick cranes, offers the even smaller electricdriven portable luffing jib PC2.5-25-20EH crane, with a maximum capacity of 2.2t and maximum working radius of 6.10m at which 1.3t can be lifted. The crane is equipped with a main hoist and a luffing hoist. The latter can serve as erection hoist to lift the main hoist and power unit module to the roof, if there is no elevator that reaches roof level.
In Japan, Koshihara developed a telescopic boom climbing jib crane called the KCS-1010. With a self-climbing device on a 500mm diameter circular post mast, up to 13.44m free standing height can be achieved. Alternatively the compact crane upper can be rigged directly on the 2.3m x 2.3m cross base. Maximum outreach of the three-section telescopic boom is 10.75m, while maximum capacity is restricted to 1.5t. Also in Japan, Uchimiya Transportation & Engineering has a lightweight pillar-mounted 2t mini crane with up to 8m of lattice boom.