
The continuing and rapid expansion of the wind industry around the globe has been of particular benefit to the specialised transport industry in terms of creating demand for transportation services and stimulating the development of new equipment to meet the evolving needs of wind industry players.
Equipment-wise Italian selfpropelled modular vehicle and heavy load transporter brand Cometto, for example, has just launched a hybrid powered version of its ModulMAX SP-E model SPMT. The company believes the hybrid-powered SPMT will be of benefit to players in the wind industry in face of increasingly strict eco regulations.
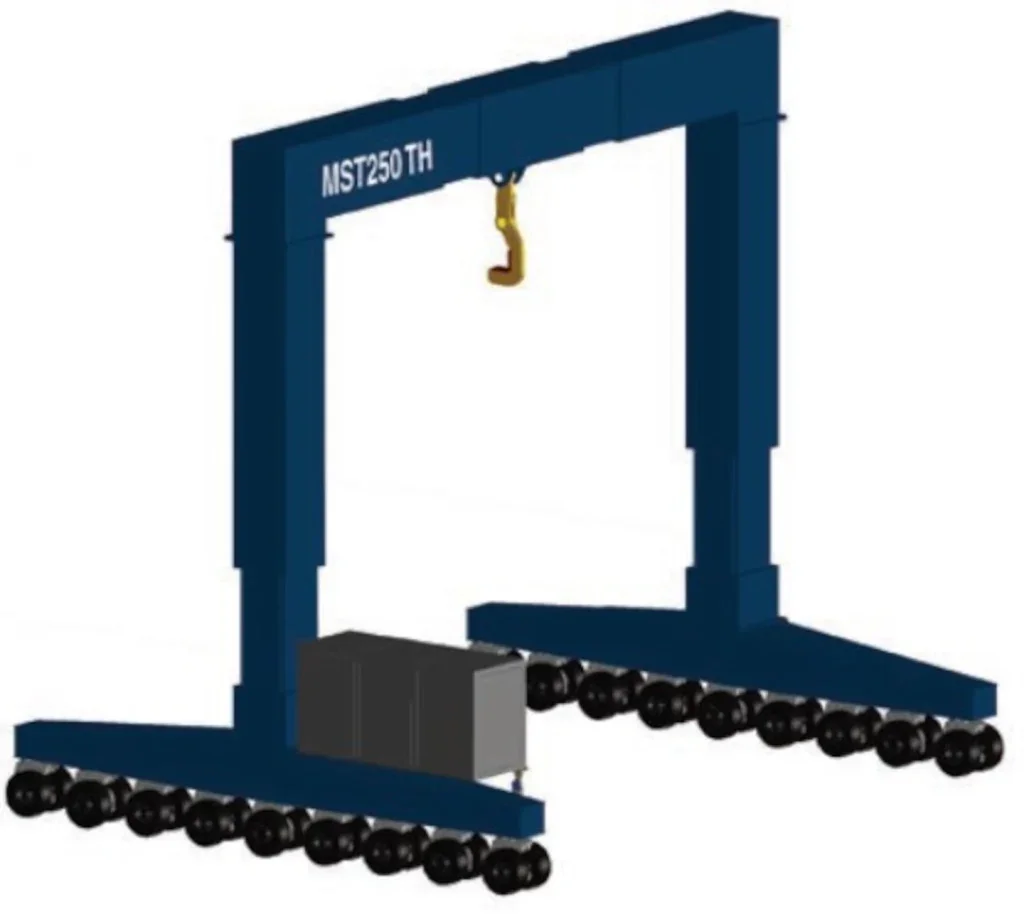
The six-axle ModulMAX SP-E, with electronic steering, has a hybrid Power Pack Unit equipped with a 186 kW diesel engine and a 100 kW electric motor with a corresponding battery pack. These are charged via the diesel engine in combustion engine mode.
The company says it has created the hybrid version in response to new legal requirements that are prompting companies, particularly in the wind industry, to adapt their processes.
Cometto illustrates this using Denmark as an example. In Denmark, until now, SPMT vehicles have been able to drive into factory buildings to pick up heavy components and transport them to open-air storage. New regulations, however, mean that when diesel-powered transport vehicles are now used indoors then all employees must leave the area. Only when the hall has been properly ventilated and measured can the staff return to work.
Cometto believes other countries will soon follow the Danish example.
Cometto has already supplied the hybrid version of its SPMT to a customer in the Danish wind industry that it says is looking to avoid disruptions to its production line and adhere with the latest Danish regulations.
The ModulMAX SP-E SPMTs bought by the Danish wind industry company can negate any delays by switching to electric-only mode when being used indoors. In addition, Cometto says, its hybrid SPMTs have exceeded the contractually agreed electrical-only range of the hybrid PPU by double.
Another plus, Cometto says, is reduced noise levels. The noise levels are now below 80 dB(A). This means that, according to Danish law employees can work in the hall for up to eight hours without requiring hearing protection in the immediate vicinity.

“Using hybrid technology, it is now possible to drive completely emission-free within the hall with the battery pack and the electric motor,” says Cometto sales manager Joachim Kolb. “And when the transport combination arrives outside, the driver can switch to the diesel engine at the touch of a button and then drive the long distances with the combustion engine. And if even more power is required, the diesel engine can be additionally boosted by the electric motor – just like in Formula 1.”
SPMT/CRANE HYBRID
The increased need for the safe and efficient transportation of wind turbine components has led N.C. Nielsen, a Scandinavian supplier of forklift trucks, terminal tractors and special machinery, to develop a completely new type of machine. Named the ‘HH Pick and Carry’ the machine is, N.C. Nielsen says, a hybrid between an SPMT trailer and a crane and is the first of its kind in the world.
The HH Pick and Carry is available with lifting capacities from 200 to over 500 tonnes making it possible to handle heavy loads in areas such as factories, warehouses and ports.
The HH Pick and Carry is designed so that its chassis legs can be shifted in width. This, says N.C. Nielsen, makes it ideal for handling wind turbine towers with diameters up to 8-10 m. It also means it can have a short turning radius.
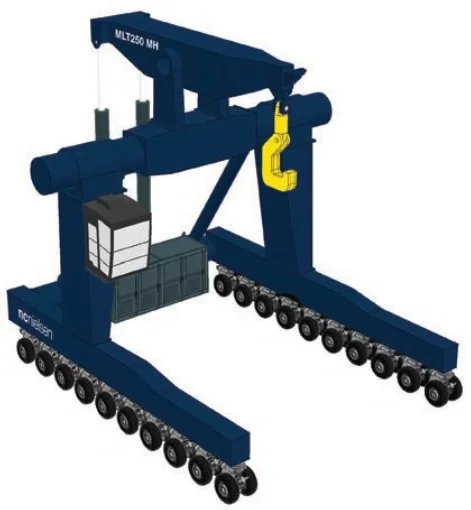
The HH Pick and Carry can be operated remotely by a walking operator, from the platform, or from the cabin.
“The new solution is based on requests from the wind turbine industry for very heavy lifting,” says Jørgen Peter Lund, sales manager at N.C. Nielsen.
“We’ve focussed on working smarter in less space, despite the goods having grown much larger. So the HH Pick and Carry machines are a natural development of this.”
The HH Pick and Carry is being available in three models: the Tower Mover; the Multi Handler; and the Mobile Straddle Transporter.
The Tower Mover is particularly suitable for wind turbine towers and elongated structures, says N.C. Nielsen.
The Multi Handler is designed for various single lifting tasks of components for the wind turbine industry such as monopiles, TPs, hubs, bearings and nacelles, but can also be used as one of the components in driving towers.
And the Mobile Straddle Transporter can be used independently for heavy lifting and flexibly in combination with the other two basic models, and this model can run over the entire item if two machines are needed to lift it on board a RoRo ship.
According to N.C. Nielsen a key element the three HH Pick and Carry machines have in common is their flexibility and versatility. “The wind turbine industry has many time-bound projects and mobile lifting machines come with many options and low installation costs compared to stationary harbour cranes, overhead travelling cranes etc. and are relatively simple to move from site to site,” notes Lund. “They optimise logistics and can manoeuvre in a relatively small working space, which is often the reality at a port terminal.”
The HH Pick and Carry can be equipped with optional equipment such as a hydraulic beak, intermediate yoke and special attachments that mean they are suitable for a variety of internal transport tasks. The machines are available as fully electric versions or as a combination.
TURBINE FACTORY
One of the newest, and biggest, production site for offshore towers in Europe is currently being built on the island of Ostrów, off the Polish harbour city of Gdansk.
Here the company Baltic Towers is building a huge hall measuring 135 metres wide, 430 metres long, and almost 36 metres high. The construction phase began in June 2024 and Baltic Towers plans to start producing the offshore towers from the second quarter of 2025.
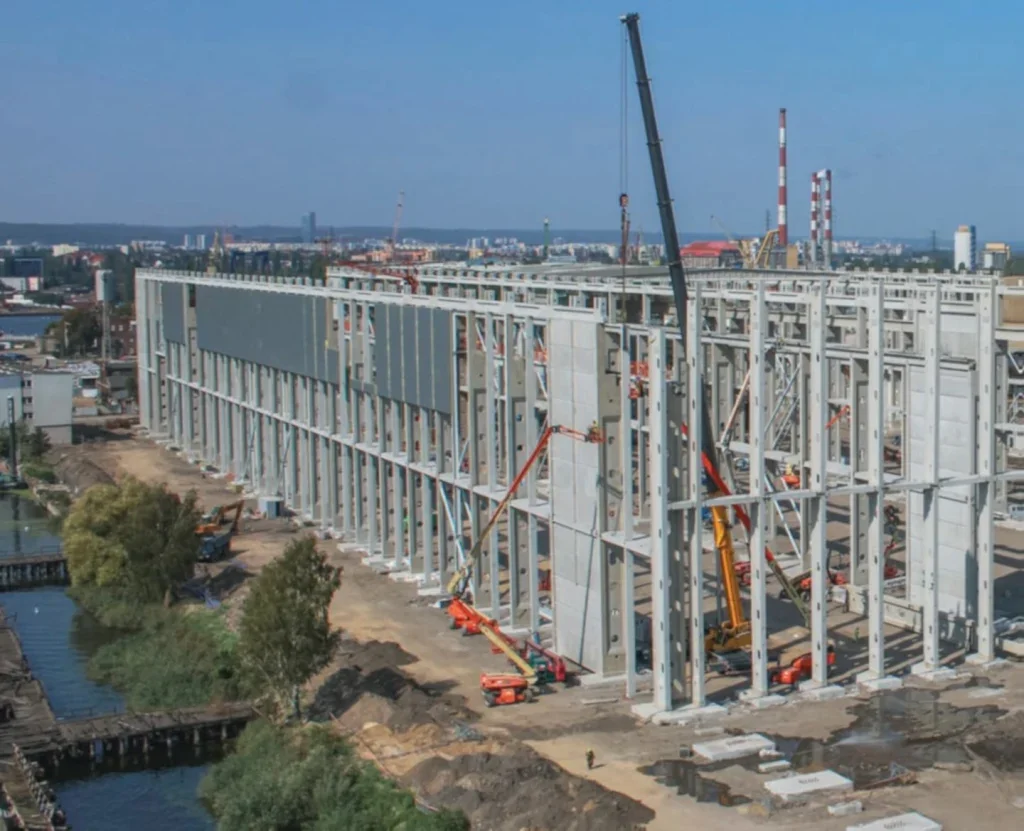
The result will be tower segments with a diameter of 11 metres, a length of 50 metres and a weight of 500 tonnes each. The production capacity is estimated at 150 towers per year.
As part of the project Baltic Towers has ordered 48 SPMT axle lines from Cometto’s 48T series with four Power Pack Units. These self-propelled modules will be used to transport steel plates, tower sections, and even entire towers to the right place in the production line – such as to the storage area or on to the ship loading area.
“The SPMTs to be delivered will be the backbone of our production line,” says Tomasz Bogdan from Baltic Towers, emphasising the importance of the new vehicles.
Baltic Towers was established in 2023 as a result of cooperation between the Polish Industrial Development Agency S.A. and the Spanish company GRI Renewable Industries, S.L.
The joint project is a significant factor in strengthening the Polish offshore wind energy supply chain.
IN THE FIELD
Out in the field the wind industry is driving innovation by specialised transport equipment end users, too. Cologne, Germany-based heavy haulage specialist HKV, for example, has used a 12-axle combination of Cometto SPMT powered by a 202 kW Power Pack in order to achieve timeefficiencies on a windfarm job site north of Wolfsburg.
The company was using one of its Liebherr LR 1700-1.0 crawler cranes to assemble multiple wind turbines. The track between the wind turbines was too small for the crawler crane to move itself, plus they were a distance of between one to two kilometres apart.
Rather than disassemble the crawler crane after each turbine, HKV used the SPMT to transport the crawler in just two main loads.
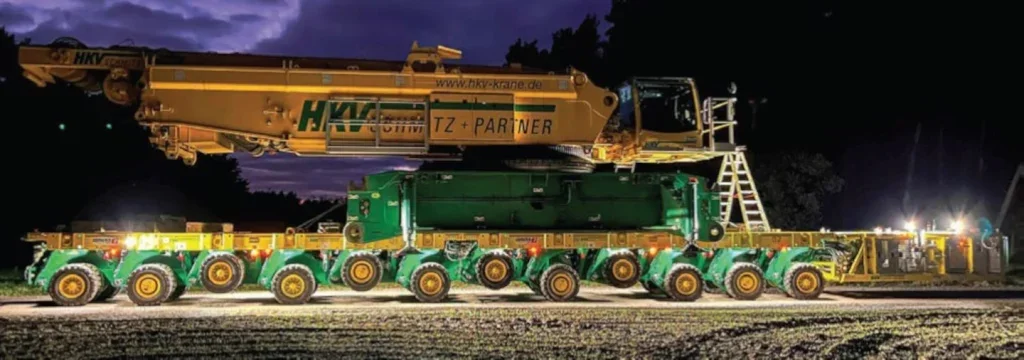
First of all the 105 tonne upper and undercarriage, with winch and A-frame, were moved. This was followed by the complete derrick boom, 42 metres long and weighing a total of 53.8 tonnes, as well as the ballast weight of 200 tonnes.
“Thanks to the SPMT solution, our customer HKV has reduced the relocation time of the crawler crane by around 1.5 to 2 days,” says Joachim Kolb, sales manager at Cometto. “This meant that the overall construction of the wind farm could be considerably shortened and accelerated.”
With a basic width of just 2,430 millimetres and electronic multi-directional steering, the self-propelled MSPE 48T module is well-suited to such narrow routes, says Cometto. The axle and ambient lighting with the night light kit on the vehicle also had a positive effect, as this ensured safety during night-time transport.
FLEET EXPANSION
International heavy lift and transportation specialist Sarens is undertaking a large amount of wind power-related transport work. Most recently it has announced the signing of a Memorandum of Understanding (MoU) with the Porto do Açu and Prumo in Brazil. It says this marks a major step forward in supporting the offshore wind energy sector there.
This collaboration focuses on the development of innovative logistics solutions for the transportation of large and complex components, such as turbines and blades, requiring specialised crane services and complex heavy lifting.
It’s no wonder, then, that Sarens is expanding its SPMT fleet. At the end of October the TII Group announced a large axle line order of its Scheuerle K24 SPMT by Sarens. The latest order will, it says bring the total number of Scheuerle K24 SPMTs on its fleet to almost 2000.
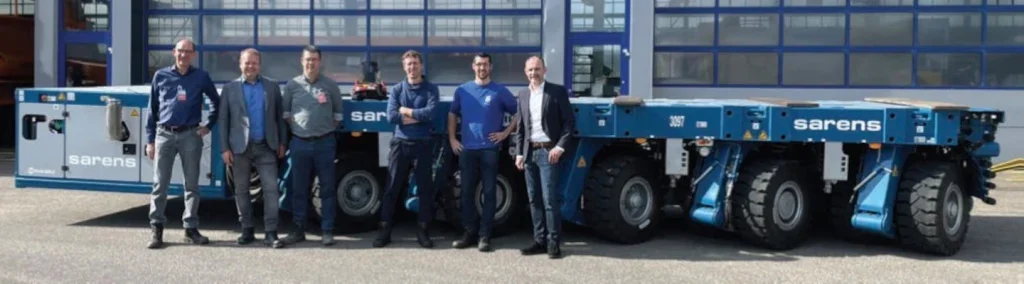
According to the TII Group, Sarens has been using the K24 since 1985 when it bought its first module. This has been helped by the ability for older K24 models to be coupled with newer versions.
The SPMT K24 is suitable for the transport of rotor blades, wind tower segments, nacelles, tripods, monopiles, and power plant modules moving payloads ranging from several hundred to several thousand tonnes, says TII Group
Sarens uses its K24 SPMTs for a broad spectrum of applications including transporting oil and gas platform modules, bridges, and other oversized and heavy components, in shipyards, construction, and mining sites; but it’s the wind sector that’s currently a key driver of work.
For example, Scheuerle’s K24 SPMT are being used by Sarens in the construction of the Hai Long Offshore Wind Farm in Taiwan where 73 wind turbines are currently being built.
There, according to TII Group, its SPMTs are handling a wide range of heavy components. The SPMTs also face additional challenges there, says TII Group, such as monsoon weather and seismic activity.
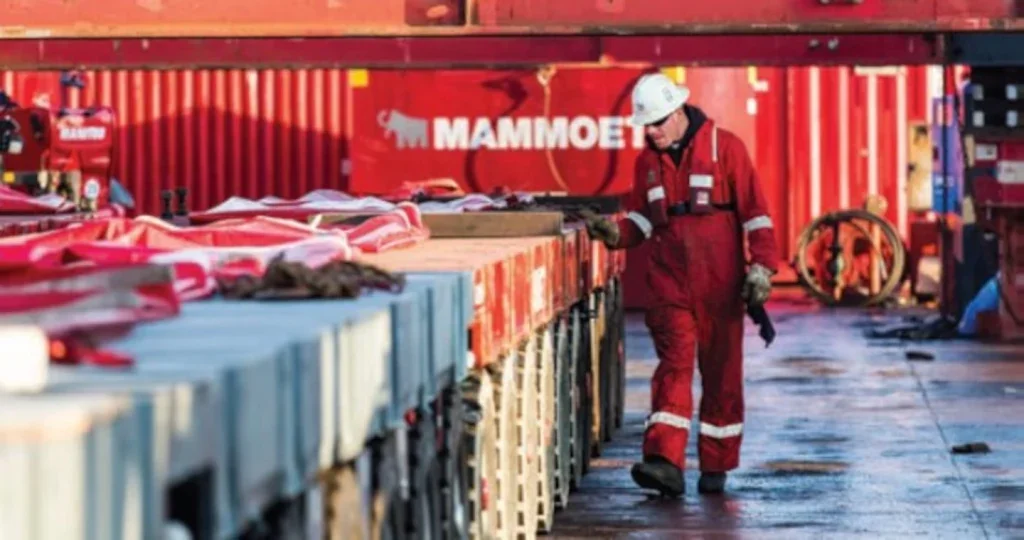
MARSHALLING MONOPILES
In November heavy transport specialist Mammoet inked a deal to move over 100 monopiles for wind turbines over the course of a year on site. The contract is with Buss Ports to marshal wind turbine generator foundations for two of Europe’s biggest offshore wind farm projects – RWE’s Nordseecluster A (Germany) and Thor (Denmark).
The Nordseecluster, with a planned capacity of up to 1.6 GW, is one of the largest offshore wind energy projects in Germany and will be constructed in two phases (A & B).
Thor, with a planned capacity of more than 1 GW to power more than one million homes, is Denmark’s largest to date.
Mammoet will manage the phased loadin, temporary storage and loadout of 116 XXL monopiles for both wind farm projects at Buss Terminal Eemshaven in the Netherlands.
The largest foundations will weigh around 1,700 tonnes and measure 96 meters in length.
The monopiles will be offloaded onto the quay using a RoRo linkspan ramp and transported using SelfPropelled Modular Transporters (SPMTs) fitted with saddles.
The SPMT trailers will then drive the monopiles onto storage dunes, ready to be called off and shipped to the wind farms located in the German and Danish waters of the North Sea.
DOLL BLADE ADAPTOR
Also in November UK specialist heavy haulage company Collett & Sons completed the delivery of all 90 wind turbine components to Cushaling Wind Farm in Ireland, working on behalf of Vestas.
For the job Collett utilised its latest renewable energy fleet addition, the Blade Adapter trailer (also known as the clamp and dolly system), to transport the blades.
This design, made by German trailer manufacturer DOLL, was also used for the first time in Ireland and the UK.
Collett says it provides improved ground clearance, enhanced manoeuvrability and greater stability compared to standard Super Wing Carrier trailers.
According to Collett its Blade Adaptor requires two metres less space for turning at bends than a 65 metre platform trailer, ensuring safer driving with high centres of gravity. Despite the total vehicle length of 93 metres, Collett’s adapter is designed to be universally compatible with blades of up to 120 metres.
RECORD BREAKER
All components, including nine nacelles, nine hubs, nine powertrains, 36 tower sections and 27 blades, were stored and loaded from Port of Waterford, Ireland. This included recordbreaking 80metrelong blades, the longest onshore turbine blades ever delivered in the history of the Ireland and the UK.
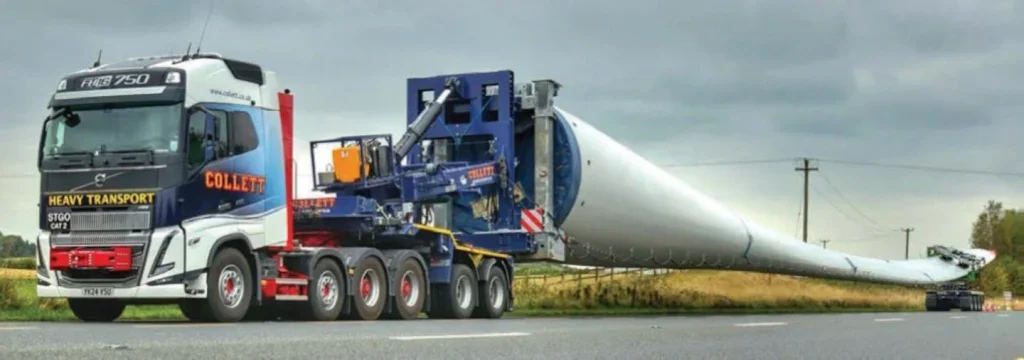
Once operational, Cushaling Wind Farm will feature nine V162 Vestas Enventus turbines, the first of their kind used in both countries.
The powertrains and hubs were transported on eightaxle and sixaxle steerable trailers respectively, while the nacelle components were delivered using 37 Nooteboom clamps. All tower sections (bottom, mid 1, mid 2, and top) were transported using Collett’s 37 Nooteboom clamps.
All components, except the blades, were transported directly from port to site, following a 295km route. Undertaking nighttime deliveries in order to minimise road traffic disruption, the route took approximately 10 hours including a rest break along the M4. Due to the blades’ length, distance and complexity of the route, a different route was utilised and spread over two nights.
The wind power industry continues to drive remarkable advancements in the specialised transportation sector, fostering innovation that addresses both the increasing scale of turbine components and increasingly stringent regulatory requirements.
The large scale projects referenced above highlight the global momentum behind wind energy and its reliance on specialised transportation systems.
The future of wind energy is bright, and the specialised transport sector will undoubtedly remain a vital partner in its ongoing success.
FAYMONVILLE TO SET UP ‘MADE IN AMERICA’ PRODUCTION FACILITY IN ARKANSAS
Luxembourg-headquartered trailer manufacturer The Faymonville Group has announced plans to set up a USA-based production facility and has already selected a site in the port of Little Rock, Arkansas.
Faymonville says a team in Luxembourg is currently working on new products that it says will bring significant added value to the US. market. In the fi rst phase, individual components will be manufactured in Little Rock, while preparations for in-house production are underway in phase two.
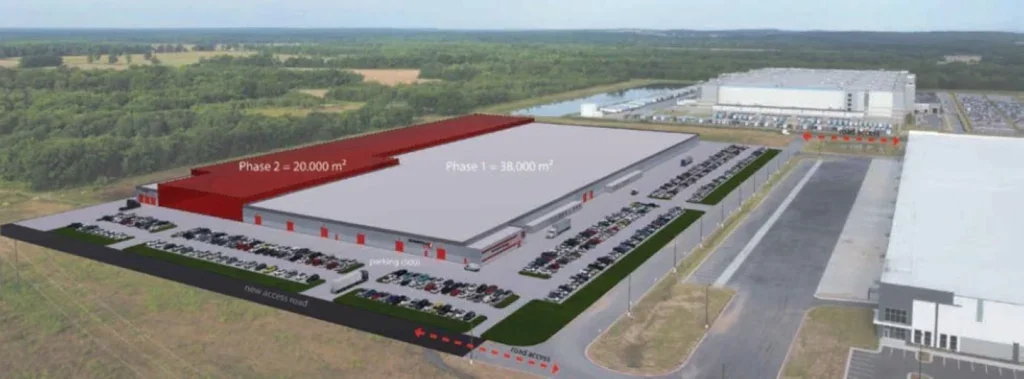
Additionally, service and spare parts support for Cometto-branded vehicles will be strengthened. “By early 2026 the production will be operational and the vehicles will proudly bear the ‘Made in America’ label, with the goal of long-term success in the US market,” said Faymonville managing director Alain Faymonville.
“We proudly delivered our fi rst vehicle to the US in 2016,” added Alexander Fickers, CEO of the Faymonville Group. “What we particularly value about the US market is its enormous potential, its practical, solution-driven mindset, and the much simpler administration compared to Europe.”