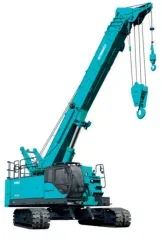
A rough terrain crane (RT) has a telescopic boom and is mounted on tyres. Its extendable boom makes it manoeuvrable and flexible. The rubber tyres, however, mean that the RT needs outriggers on site to give it stability and the tyres don’t cope well with extremely soft ground terrain.
A lattice crawler crane needs no outriggers. It can pick its load and carry it. It can go more on less anywhere on a site – as long as there is space for it. But it is large and bulky. Low bridges can be a problem. And it cannot be transported to the site in one piece: the lattice boom usually travels separately and has to be mounted on-site, which takes both effort and time.
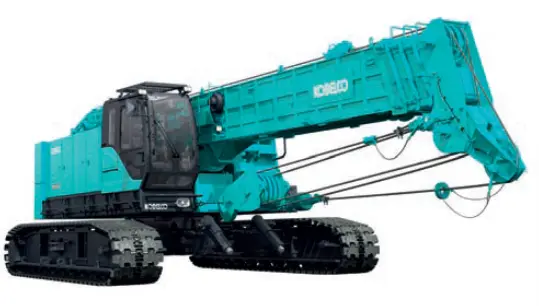
A telescopic boom crawler crane has the best of both worlds. With the boom contracted it takes up much less space so it doesn’t have to be detached for transport. That alone delivers huge savings in cost. The crane can set to work as soon as it arrives on site, so more savings there. It does not need outriggers for stability, so it can pick and carry as desired. The boom can be telescoped to give whatever radius the operator desires to accurately deliver the load; a simple, easier, and less energy-consuming process than having to raise a lattice boom to a steep angle to lessen the radius. And the crawler gear really does enable it to be used on any terrain.
So whichever bright spark thought of putting the boom of a RT on the chassis of a lattice crawler was on to a winner. The combination delvers a crane which is enormously flexible. Applications are more or less anywhere that construction takes place: in infrastructure; in energy; as auxiliaries cranes; even standing in for a tower crane, as the box on the next page shows.
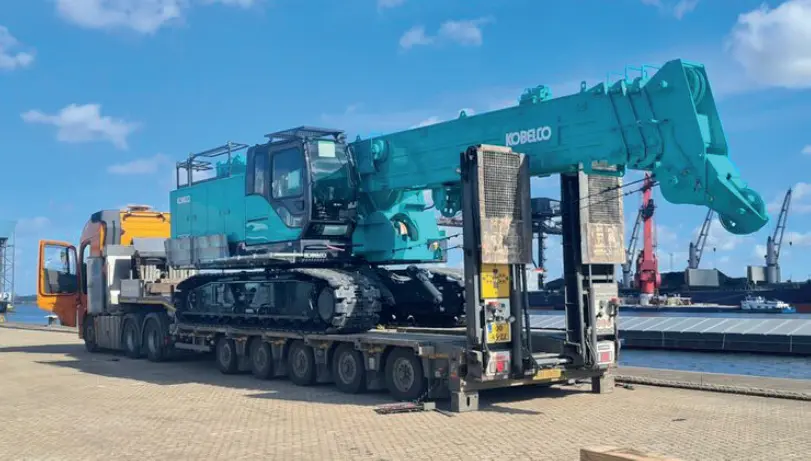
Manufacturers, therefore, have been happy to provide them. Among the latest models Kobelco has a new telecrawler launched in January. The 75 tonne capacity TKE750G is aimed specifically at the European market and continues the same tried and tested technology as the company’s G series lattice boom crawler crane models.
Compared with conventional telescopic crawlers it has a larger engine capacity, says Kobelco, a shorter boom length with a higher winch capacity on standard main/ auxiliary winches, and stronger, thicker, wire ropes. All of which gives the crane a higher capability for foundation works. It can be equipped with vibration hammers, auger drills, and hammer-grabs.
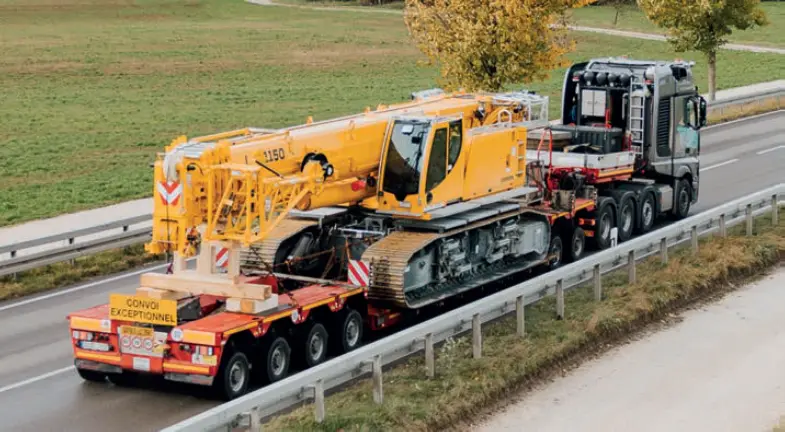
The TKE750G has an exceptionally stiff four-plate box structural boom which, again, has been specially designed with foundation work in mind. The short boom length, with a side deflection-resistant fully powered boom, makes the crane well-suited to working on compact jobsites says Kobelco.
The main and auxiliary winches are positioned vertically at the rear end of the machine, helping maintain a compact main body. The 22mm diameter wire rope has 7.0 tonnes of rated line pull.
The TKE750G is powered by a Mercedes-Benz E9H01 (Daimler OM936LA) 7.697l water-cooled, in-line six-cylinder direct injection and turbo-charged engine, with a rated power output of 254kW/2,000 min-1, compliant with NRMM (Non-Road Mobile Machinery – Europe) EU Stage V regulations. This degree of power output offers higher hydraulic performance which, Kobelco says, is especially important during foundation operation.
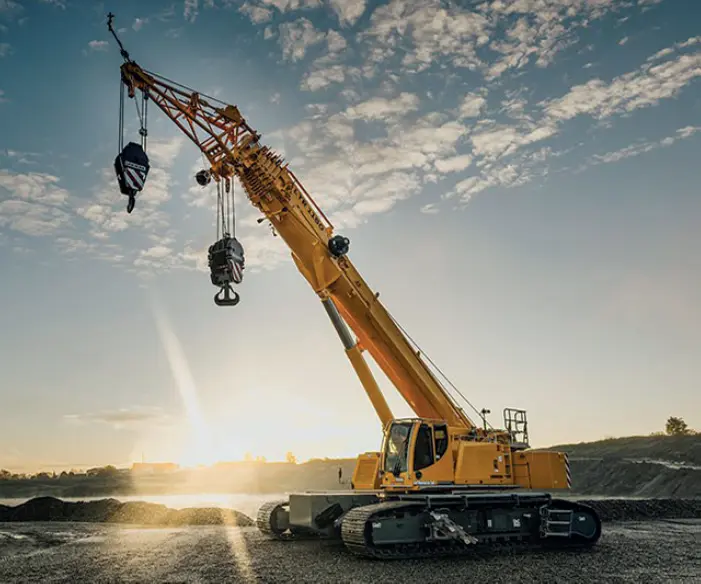
Kobelco’s KCROSS (Kobelco Crane Remote Observation Satellite System) is retained on the TKE750G model. Machines fitted with KCROSS transmit working conditions, locations, and maintenance history to provide owners with fact-based information for their asset management. The TKE750G will be available from mid-2024 onwards.
WIND WORK
Liebherr has also expanded its telecrawler range, in this case with a 150-tonne machine: the LTR 1150. With windfarm work in mind, Liebherr’s engineers have prioritised the crane’s transportability, control at hight, and pick and carry capabilities. The LTR 1150 is positioned between the LTR 1100 and the LTR 1220. In launching it Liebherr says it is responding to the requirements of crane operators faced with lifting jobs that are beyond the capacities of the former but for which the LTR 1220 is overkill.
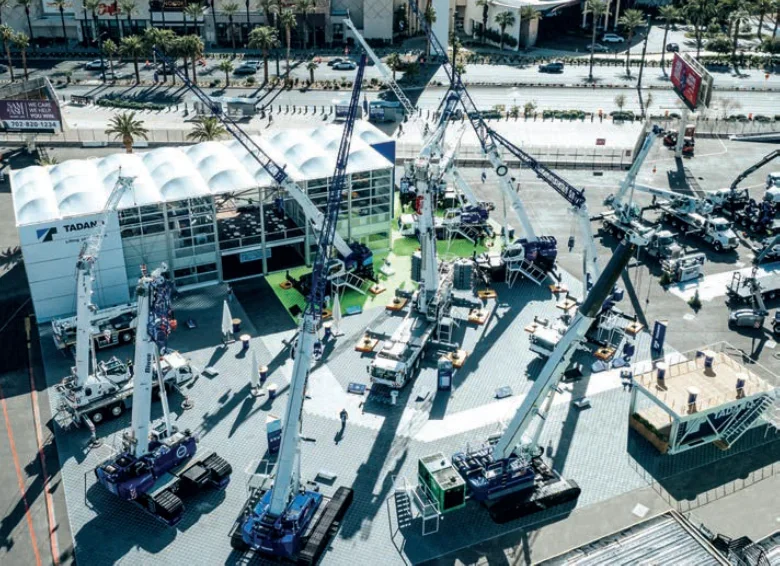
The new crane offers around 50 per cent more lifting capacity than the LTR 1100; despite this increase, however, Liebherr says it can be transported just as easily and economically as its 100-tonne sibling. Complete with crawler carriers on low loaders it comes in at a total weight of 60 tonnes and a transport width of 3.5 metres. Optionally the crawler carriers can be removed for transport which results in a weight of just 38 tonnes and a width of only three metres.
To transport the crane without the crawler carriers a jack-up erection support, consisting of four swivelling cylinders, is required. This supports the crane on the ground while the tracks are removed and the low-loader positions itself under the crane. This method has been tried and tested with Liebherr’s 100-tonne LTR 1100.
The LTR 1150 also has a new automatic support system to assist the operator. Liebherr says this was developed to allow faster and easier assembly and disassembly of the crawler carriers.
The two crawler carriers, each weighing 11 tonnes, can be transported together on a standard semi-trailer with an economical width of 2.55 metres. The integrated access steps are folded in during transport.
Ballast distribution has been carefully thought out. The entire counterweight can be ballasted on the crane with only four lifts: two lifts for the two 11-tonne central ballasts and two for the maximum slewing platform ballast of 41 tonnes. As with the Liebherr LTM cranes, this is attached to the slewing platform using a hydraulic ballasting device. Liebherr-AutoBallast is designed to support the crane driver during this process. The support for the slewing platform ballast is integrated in the central ballast.
Liebherr’s VarioBase variable supporting base system is wellknown. The LTR 1150 is its first telescopic crawler crane to be equipped with it. It determines the optimum load capacity in real time taking into account the fixed track width and the variable rotation angle. The company says that not only does it provide greater safety for telescopic mobile cranes but also allows significantly higher load capacities, especially for lifts directly over the supports. Liebherr says the greatest advantages in terms of load capacity are achieved when performing lifts over the corners of the tracks, especially with reduced track widths. The maximum track width of 5.8 metres, a reduced width of 5.0 metres, and a narrow 3.5-metre track width are available.
As with the other Liebherr LTR cranes, the LTR 1150 is equipped with load charts for slopes up to a maximum of 4° – in gradations of 0.3°, 0.7°, 1.5°, 2.5° and 4°. For the first time for its telescopic crawler cranes Liebherr has also calculated ‘WindSpeed Load Charts’ for the LTR 1150, which make it possible to work safely and flexibly at higher permissible wind speeds of up to 15.6 m/s – and this is the case even with the full load capacity in many boom positions.
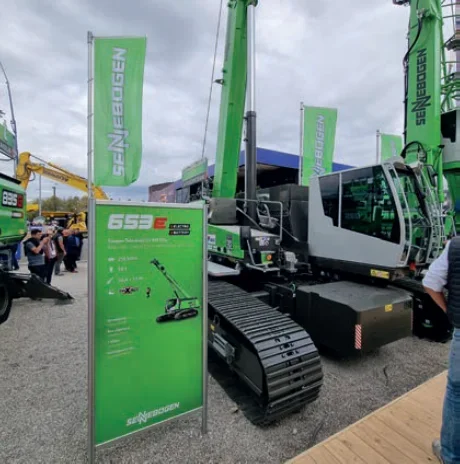
Liebherr believes the LTR 1150’s performance and pick and carry characteristics mean it will particularly appeal to users in the wind farm erection and construction industries. It is capable of assembling crawler cranes up to the 1,000-tonne class and can move components weighing over 60 tonnes. Its short, powerful erection jib and additional hoist gear mean the LTR 1150 can move loads of up to 34.6 tonnes into position. The range of working equipment for the 52-metre telescopic boom also includes a hydraulically adjustable double folding jib and telescopic boom extensions that enable hoisting heights of up to 83 metres.
SHOW ‘N’ SHINE
Tadano has been building telescopic boom crawler cranes for more than 40 years. Its GTC range has models from 35 tonne to 200 tonne capacity class. Versatility is one of the virtues of the teleboom. Set-up is simple – no on-site assembly of a lattice boom is needed; the machine simply arrives at the worksite with its boom in place.
“That simple setup and configuration gives advantages over lattice booms, especially for road construction and bridge work,” says Julie Fuller, president and COO of Tadano Mantis Corporation, Tadano’s North American division, speaking at last year’s ConExpo tradeshow in Las Vegas – where Tadano had no less than three telecrawlers on display (GTC 1300 / GTC 1600 / GTC 2000). “The product line also offers pick and carry over the entire load chart, which offers versatility for unique job site challenges,” Fuller says.
Like we saw with the latest Kobelco crane earlier in this article, Tadano also identifies foundation work as being a key application area for its telecrawlers. “We offer many unique features to support foundation work including a third winch with controlled free fall power pack mounting and factory approved use of foundation tools,” Fuller adds. “Tadano’s GTC models have strong out of level capabilities including market-leading four degree out of level charts.”
On the other side of the Las Vegas showground at ConExpo 2023 Link-Belt displayed its 55 ton (51 tonne) TCC 550 – which had been bought by the ALL Family of Companies. Billed as ‘the future of how tough jobs get done’ the crane, which launched in 2021, has a four-section 36.8–115 ft full power boom and an optional two-piece lattice fly for a maximum 172 ft of tip height. It can be transported in one load under 100,000 lbs (45,359 tonnes) with standard counterweight.
“Hydraulic telescopic crawler cranes are an integral part of our fleet,” says ALL Family of Companies. “Their transportability and quick setup as well as their ability to handle rougher terrain often make them the crane of choice for a variety of construction work.”
At the start of 2023 Straubing, Germany-headquartered crane manufacturer Sennebogen debuted the 80-tonne capacity 683 E. It is a fifth-generation model, the ninth in the series, and is in the manufacturer’s medium-size class, fitting perfectly into the gap between the existing 673 E and the 6103 E. For an example of the capability and flexibility of this machine, see the box – it does not even need an operator on board!
ELECTRIC DREAMS
A recent and exciting development in the telecrawler sector has been the growth of electric-powered cranes. Sennebogen has its 653 Electro Battery, which can be operated in battery-only mode (it is a 210kWh Li-ion pack), from the mains supply by cable, or by battery while charging from the mains. This allows it to work without time limit. When in ‘supply-cable’ mode the mains power is used for lifting activities and excess energy fed in is simultaneously used to recharges the batteries.
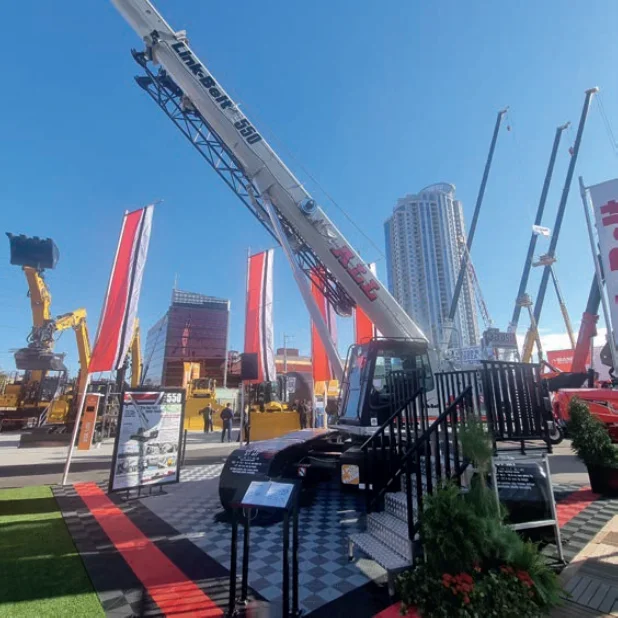
In ‘mains cable’ mode the power supply is via a 63A CEE socket; the power is supplied to the undercarriage which allows 360 degrees of boom and cabin rotation without interference from the cable.
Piacenza, Italy-headquartered crane manufacturer Marchetti has a fully-electric version of its 25-tonne CW25.35 crawler. The battery pack is Li-ion and gives 90kWh, which the company says will supply eight hours of continuous working. The motor delivers peak power of 110 kW and has a 22kW onboard charger.
PV-E Cranes is a Dutch company based in Oosterhout whose focus is on the development, production, and marketing of 100% electric crawler cranes and related accessories. The PV-E electric fully battery powered telescopic crawler cranes range from 70-120 tonnes capacity and come with a standard set of two battery packs to give at least eight hours of work – interchangeable battery packs are available if you need to work longer.
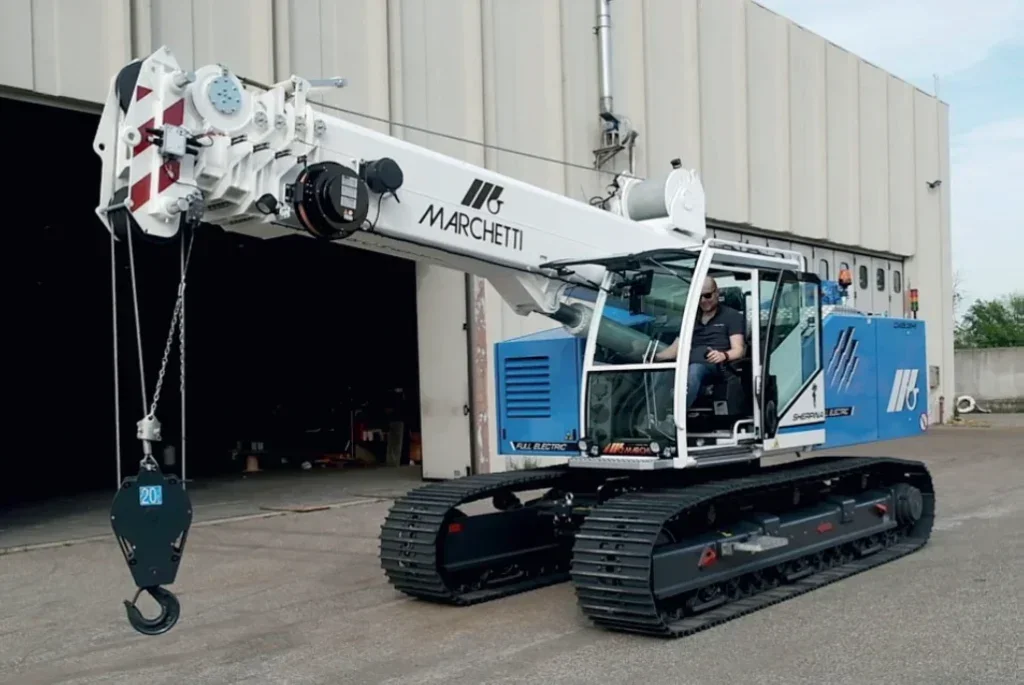
And there’s Chinese construction equipment manufacturer Sany with the SCE800TB-EV. It is a like-forlike variant on the diesel-powered SCE800TB. The electric machine offers a capacity of 80t, with a 47m main boom and 17.5m lattice jib. The crane is designed to be transported in three loads: the base machine, at 39.5t; car body and other components at 28t; with counterweight tray and six pieces of ballast coming in at 26t.
It is powered by an LFP (lithium iron phosphate) battery pack from Chinese supplier CATL. The two companies announced a strategic partnership in 2020, with CATL with the move opening new opportunities for both companies. The two companies are also collaborating on the data side of electrification developing battery behaviour tracking and fault selfdiagnosis. Electric power is made useful by a motor from Danfoss.
The crane can be fast charged at 200v with a single gun charger, or 400v with a dual gun charger; where these options aren’t available, it can slow charge on a 63A connection. It can also work while slow charging.
Sany is offering the crane in Europe through crane dealer UCM Holland. In the UK, it is working with Foster Cranes, and in Norway, with Seatraders. One of the first companies to buy one is Tutt Bryant in Australia.
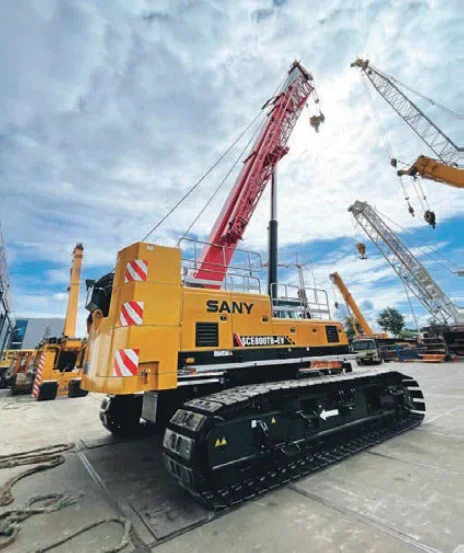
By blending the best attributes of rough terrain and lattice crawler cranes the telecrawler provides a pragmatic lifting solution. Its adaptability and efficiency make it a preferred choice across a range of applications, from foundation works to wind farm installations.
And as manufacturers continue to refine its features, including electric options, the telecrawler crane remains poised to play a significant role in meeting the evolving needs of the construction industry.
SENNEBOGEN REPLACES TOWER CRANE AT THE TOUCH OF A BUTTON
A Sennebogen telecrawler has performed the functions of a tower crane on a site in the French riviera. A new, nature-oriented residential complex in the municipality of Hyères les Palmiers is being constructed by Comet Paca, a major company specialising in detached houses and apartment blocks. Local regulations prevented the use of a tower crane on the entire con-struction site so it used a Sennebogen 683 E telecrawler, supplied and operated by French transport, lifting and handling specialist M&S Translev, instead.
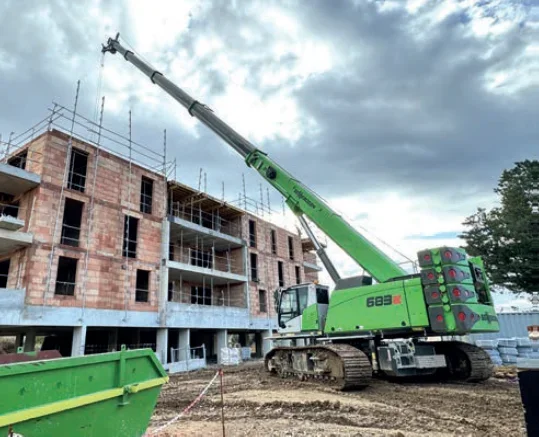
The telecrawler carried out the shell construction work. It handled all the lifting work in one part of the construction site and fulfilled the transport requirements for the three four-storey building complexes.
The Sennebogen 683 E was used to lift common precast elements, conventional and insulated blocks, concrete buckets, rubble, plus conventional building components such as columns, beams and formwork.
It has a 42 m full-power boom, so can cover a large working area to ensure the simultaneous construction of all three buildings. The crane is positioned in the centre of the site and moves on its crawler tracks as required to meet the needs of each team. Moving and telescoping under load over the entire length of the boom is no problem at all.
A high-capacity tower crane would normally be used on such construction sites. Using a telecrawler in its place is unusual, and the way in which it was used was also different: it was entirely controlled by radio.
Moving (with or without a load), lifting and positioning were all controlled remotely. Sébastien Greuzard, managing director of M&S Translev, was the operator. “It is unique that I can operate the crane precisely with radio control. I can carry out lifting operations and position the loads precisely by being right next to the workers in the assembly areas. I can be on the ground or in the working area on the floors of the buildings.”
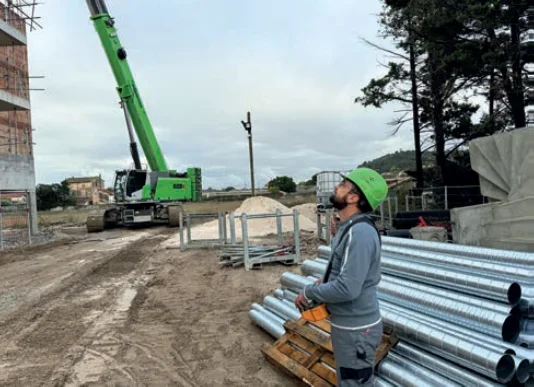
The increased safety is an essential element that was also highlighted. As the teams on the construction site put it: “With this working technique and thanks to this crane, the operator has the entire working area of the machine directly in view. Manoeuvres are much safer when the crane operator is operating close to his colleagues instead of blindly with a radio link or a camera.”
A video of the job can be seen here: https://youtu.be/BIALm1IXvBE?si=EVnMIdv5qUTbuf_O
PARK LIFE: TELECRAWLER AT SOLAR FARMS
Bavarian construction company Autodienst Eineder has been using a Liebherr LTR 1060 since October 2022. The Liebherr 60 tonne crane does most of its work in solar parks. The Bavarian company uses the telescopic crawler crane for the economical installation of transformer stations due to its off-road capability, manoeuvrability, and its ability to travel with a full load which means less time and lower costs.
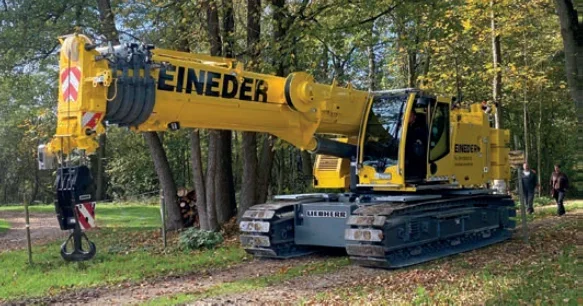
“Its offroad capability and manoeuvrability makes the LTR 1060 ideal for jobs in solar parks,” says Autodienst Eineder’s MD Peter Eineder. “Its pick and carry mode is particularly good as it enables us to carry transformer stations weighing up to 20 tonnes straight from the transport vehicle to the installation site.” If the terrain means that the LTR 1060 cannot carry the load over it, Eineder uses a heavy-duty transport crawler to move the transformer stations to the solar parks.
The LTR 1060 normally runs on 4.8 metre wide track, but it can also work safely on a track width reduced to three metres using the crane control system. This can help get in between tightly packed rows of solar panels. “It is a major benefit on constricted sites,” says Eineder. “We also appreciate the sensitive control of the LTR 1060 when things are tight.”
Transporting the crane is also easy. The crawler travel gear can be retracted to a width of three metres. The low crane height of 3.15 metres means that economical standard semi low loaders can be used to move it. The LTR 1060 weighs just 62.6 tonnes complete with turntable and central ballast. The axle loads for transport are less than 12 tonnes for a three-axle tractor unit and a five-axle low loader. By removing ballast the transport weight can be reduced to the net weight of the basic 37.5 tonne machine. Axle loads of less than 10 tonnes can be achieved using a three-axle tractor unit and a four-axle low loader.
Once at the site, the crane can assemble both the central ballast and the slewing platform ballast itself without requiring an auxiliary crane. “The LTR 1060 is a fantastic crane. Even as a 40 tonner without ballast, it is perfect for many jobs, including installing small transformer cabinets,” says Eineder.