
Global heavy lifting tower crane specialist, Marr Contracting, has been awarded the contract to deliver specialised heavy lifting crane services on the Lostock Sustainable Energy Plant (LSEP) near Northwich, Cheshire, UK.
Once complete, the 60MW energy from waste (EfW) plant will have the capacity to process 600,000 tonnes of waste per year – producing enough power for 125,000 homes.
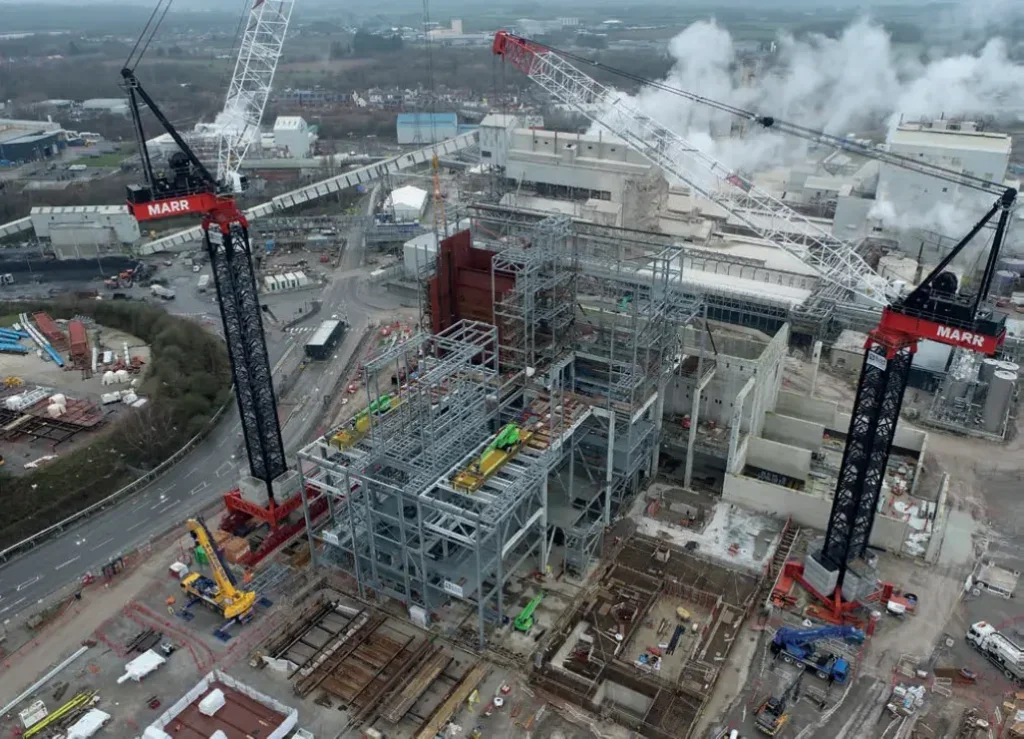
On the site Marr is using two M2480Ds – the world’s largest capacity luffing tower crane. The solution offers lift capacities of up to 110 tonnes and a reach of up to 73 metres to lift the 70-tonne drum and boiler waterwalls weighing 85 tonnes.
The first M2480D is erected on the Marr Transit System (MTS) – a rail system that extends the reach and coverage of the tower crane over the site without any loss of capacity. The second M2480D is installed on a static base.
The solution, says Marr, will allow larger sections of plant and equipment weighing up to 85 tonnes to be installed in fewer lifts.
Cranes Today asked Marr a bit more about the project and why these cranes were selected for the job…
What was it that made the contractor, Black & Veatch, commission Marr and, specifically, two of its M2480Ds for the Lostock Sustainable Energy Plant job?
Craneage is often more complex than what it needs to be. On this project, we took what was potentially going to be a very complex approach and modified it to provide Black & Veatch with a really simple craneage solution that is allowing them to construct the project in the way they wanted to.
Black & Veatch were able to see the benefits that the right cranage solution can deliver to a project. With the ability to lift in larger, heavier components, Marr’s approach supports Black & Veatch’s preferred modern methods of construction (MMC) methodology by allowing larger, prefabricated components and larger sections of plant and equipment weighing up to 85 tonnes to be lifting in a single lift. This in turn will reduce complexity and the number of lifts required, helping to shorten the construction schedule and fast-track the path to commercialisation.
Marr’s experience in the successful delivery of similar large-scale EfW plants in Australia and the Middle East is ideally suited to this project and emerging Modern Methods of Construction (MMC) trends in the UK. Larger plants, like the Lostock Sustainable Energy Plant (LSEP), demand more efficient construction solutions and can really benefit from the use of technology, such as the Marr Transit System (MTS), which extends the reach and capacity of Marr’s cranes. Having both M2480Ds ensured that the project has total coverage over both boiler lines with the capacities required.

What is it about Marr’s solution, or the M2480D, that helped win the Lostock contract?
Marr’s solution for this project helped to reduce complexity while at the same time delivering the lifting requirements needed. This translated into a number of key aspects:
- Addressing the challenge of a constrained site, we have maximised the available space by designing a modular rail system for one crane and a fixed foundation for the other. This freed up space for storage and preassembly areas whilst still achieving the capacity, volume, reach and coverage required;
- The programme demanded a mix of high capacity lifting and high volume to support the general construction activities. These aspects are essential for schedule achievement; and
- The M2480Ds are rated to operate at up to 20m/s – providing the project with outstanding availability and the platform for increased productivity and efficiency.
What are the crane’s vital statistics?
See M2480D specifications and data sheet at www.marr.com.au/cranes/ m2480d/
In total how many M2480Ds does Marr have in its fleet?
Undisclosed. We prefer not to share the details of our fleet size but can say that our M2480D fleet has grown substantially in recent years to support current and future demand, particularly for our heavy lift fleet. Clients are increasingly choosing to engage with us early to secure availability.
Where were these two M2480Ds shipped to the Northwich plant from?
The cranes and their components came from different parts of the world including Australia, Turkey and the UK.
How easy/difficult is transportation of the cranes? How long did it take and how many vehicles did it involve? Does Marr provide these transportation services or did it outsource them?
The transportation of our cranes is a complex multi-modal process. Marr works with haulage and shipping professionals on bespoke solutions for each crane involving a minimum of 56 trailer loads from our laydown facility to site.
At the Lostock jobsite why is one M2480D on a Marr Transit System (MTS) rail system while the second M2480D is installed on a static base?
Simply to support the project requirements for capacity, reach and coverage.
What will the heaviest lifts onsite be?
The cranes are installed with a configuration that allows lifts up to 220 tonnes and a reach of up to 73 metres. Some of the planned lifts include the 70-tonne steam drum and boiler waterwalls weighing 85 tonnes.
Are there many other cranes or infrastructure on site that the luffing jib tower cranes need to avoid? If so, how is collision avoidance ensured?
Most construction sites are complex by nature and constantly evolving. Marr cranes use anti-collision software and can programme zones of operation to ensure avoidance of impact to plant and infrastructure.
How long are the M2480Ds expected onsite and what happens if the job is delayed?
The terms of our contract are commercial in confidence with our client. We work closely with our clients to support their programmes and are generally able to flex our dates to support their needs.
Where are the cranes going after this job?
Marr has a number of yet-to-be announced UK projects on our order book, but we are unable to disclose the details of those projects at the moment.
The global trend towards Modern Methods of Construction (MMC) and Designed for Manufacture and Assembly (DfMA) is resulting in increased demand for Marr’s heavy lift luffing tower cranes in the UK, Australia and other parts of the world, so we are working closely with our current and future customers to ensure a seamless transition from one project to the next.