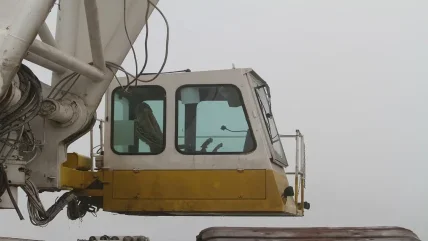
In Japanese there is a term that describes the connection between a driver and a car where the machine feels like an extension of the body. The term is "???" (ittai-kan), which can be translated as ‘oneness’ or ‘unity’. Ittai-kan embodies the idea that the driver and the car become a single entity, working in perfect harmony. This concept is often used to describe the ideal driving experience, where the driver feels completely connected and in control of a vehicle's movements.
In most mobile and fixed cranes the cabin is where this connection between operator and machine takes place. The cab is a key component of the crane and, in turn, comprises a multitude of components all designed to enhance this man and machine unity. The crane cabin is the headquarters and its various components – from the seat to the joystick to the control screen – all play a part in human and machine working together in harmony. But for how long will the cabin remain an integral, physically part of the crane?
CABIN COMFORT
Before we look to the future, though, let’s see what’s happening right now with current crane cabs. It’s a given that, with operators potentially spending a lot of time in the cabin, comfort is a priority. Operators need full focus whilst working and anything that can assist this is welcome. And crane manufacturers are going to great lengths to ensure they provide this comfort, as seen in one of the most recent tower crane cabs on the market: the Lumina X from manufacturer Raimondi.
Launched at Bauma 2022, the cabin incorporates an integrated refrigerator, multiple drawers, coat hangers, a wireless phone charger station, as well as USB plugs and a Bluetooth audio system. The operator sits on a pneumatic seat that has a memory layer and is designed to stabilise according to their body weight. Over 80 percent of the cabin is made of shatterproof glass and, to prevent it from overheating, all glass surfaces are athermic.
The cabin has a new control system, visible on a ten-inch monitor – although an even bigger 15” monitor can be specified.
The control system can instantly detect and report any system errors, malfunctioning and faults while also allowing crane operators to fully calibrate the machine directly from the in-cabin station or via radio control.
An integrated live camera and anti-collision technology is also being introduced.
Down on the ground, mobile crane operators also need cabs that support their particular requirements. Cabin access might be easier for them but mobile crane operators can spend many hours driving to and from jobsites so comfort remains key, as demonstrated by the new cab on Liebherr’s LTM 1100-5.3 mobile crane – which also launched at Bauma 2022.
The cab has a new multifunction steering wheel, a side roller blind on the operator’s door, improved instruments and modules as well as new displays and a central locking system with remote key. A new automatic heating and air-conditioning system in the operator’s cab and in the crane cab features an adapted design for a high level of comfort. A sun sensor detects strong sunshine and automatically adjusts the heating settings accordingly.
The cab comes with a new control system, LICCON3, the system’s third generation. It includes a new software package and programming language as well as a faster databus, more storage space and more computing power.
Proven hardware components, such as the mobile operating and display unit, have been kept. Liebherr says the touchscreen function on the large new display in the superstructure cab means that it is now even easier and more comfortable to control and the way in which the information is shown has also been revised and simplified.
It seems the operator has never had it so good in terms of working environment. Manufacturers, too, benefit from the multitude of parts suppliers – enabling them to pick ‘n’ mix from sub-suppliers and component distributers in their quest to build the perfect cabin.
SITTING COMFORTABLY?
A key component of any cabin, critical to the comfort of the operator, is their seat.
“Construction operators work in extreme environments and often suffer with back issues from vibrations or long hours,” says Mark Vivian, sales manager at independent UK-based seat distributor TEK Seating. “Protection is crucial so it’s important that drivers understand how their seat works and that it’s correctly fitted for their weight and body shape. In the long run it’s certainly worth investing in a comfortable, safe seat.”
TEK stocks seats from manufacturers including Grammer, United Seats, KAB, Isringhausen and Milsco – so it is well placed to advise on the various attributes of its stock.
To help minimise vibrations in construction environments, for example, TEK highlights the KAB 600 series, from Kab Seating, which offers high and medium back air suspension.
Alternatively, it can also supply the Actimo Evolution P premium comfort seat with pods from manufacturer Grammer. It has low frequency air suspension, an automatic positioning system, adjustable shock absorber, electronic weight adjustment, and pneumatic lumbar support.
Also from Grammer is the Primo XM, designed for construction vehicles with a lowprofile suspension. It is available with pneumatic or mechanical suspension and quick weight adjustment and also offers support when driving backwards due to lumbar support.
From seat manufacturer Isringhausen TEK stocks the 6000/577 SK mechanical suspension seat and the 6500/577 24-volt air seat. Both feature front operating controls, armrests, horizontal adjustments and seat contact switches.
If comfort and style are key requirements, TEK says the high spec NTS2 seat from ISRI is a good option. It's pre-finished for different types of cabins and includes variable height adjustment with memory; tilt and seat fore/ aft adjustment; and an integrated three-point safety belt.
To ensure the backrest fits the body’s contours it also has a pneumatic system.
THE SCIENCE OF CONTROL
Once comfortable in their seat the operator typically controls the crane via the use of a joystick. Here comfort, intuitive use, configurability and control are key attributes to aiding man and machine unity.
According to Saanichton, Canada-headquartered custom control solutions supplier Sure Grip Controls there is a science behind designing a joystick for maximum operator comfort, configurability and durability, as demonstrated in the development of its new Endurance Series joystick.
The Endurance Series joysticks have been optimised to reduce user fatigue and repetitive strain injuries. To achieve this the company started by considering the anthropometrics of its users by utilising databases to evaluate the smallest and largest physical dimensions of operators; it then designed the joystick to be used comfortably by both.
It also utilised user feedback to tweak the joystick’s design resulting in a dual-angle faceplate that moves the upper controls closer to the user’s thumb. This, it claims, reduces the need to reach, which improves control and minimises strain on the thumb. The faceplate angle also matches the natural resting position of a thumb relative to the rest of the hand.
The Endurance Series is available as right and left specific handles.
Another piece of feedback that the company received during development was that many ergonomic right and left handles are directive, forcing users to hold the handle in one specific way. In realuse situations being able to change your grip style can help to prevent fatigue and injury, it found.
With the Endurance Series, it took this feedback into account and designed the handles to be comfortable in different hand positions. For example, the joystick is comfortable to use whether the user wants to rest their hand on top of the grip while working or hold the joystick by its shaft with the hand naturally cradled by the hand rest at the base of the grip, it claims.
Configurability is another key characteristic of an ergonomic handle, says Sure Grip, because different applications need different controls. It offers a wide range of faceplate and trigger control options allowing users to select the best layout.
In its Endurance Series it has also introduced new high-visibility LED buttons that are visible in full sunlight but can be adjusted to the right brightness to reduce strain on the user’s eyes. The RGB LEDs can also be configured to any colour.
DEMANDING ENVIRONMENTS
Another joystick manufacturer, Curtiss-Wright Corporation – which is headquartered in North Carolina, USA, but has factories and operations internationally, has launched the JC8100 joystick controller. It’s an updated version of its well established JC8000 series.
For demanding construction site environments the joystick has been built to be extra strong, with a low pivot point designed to reduce angular deflection and wiring wear. It also has a centre detent for enhanced return-tocentre operation and a high mechanical strength for heavy-duty applications, says Curtiss-Wright.
Half-effect sensor technology further eliminates contact wear and provides safety functionality via dual analogue outputs with sense options per axis or J1939 or CANopen output options.
For maximum ergonomics a choice of multi-function grips is available, including those with up to four axes of additional proportional control and featuring up to ten finger/thumb controls including pushbuttons, rocker and momentary switches, proportional rollers, etc.
The joystick can also be supplied as ‘base-only’ enabling custom grips to be fitted.
REMOTE WORKING
So what does the future hold for the crane cab and its various components? Northampton, UKheadquartered tower crane hire and contract lift service provider Radius Group believes that there is a way to increase operator comfort and safety whilst also enhancing performance by removing the cab from the crane completely and having the operator work remotely.
Radius says it is the first lifting provider in the UK operating a tower crane using a teleoperated ground control system. It is working in partnership with Skyline Cockpit, an Israeli company formed by Skyline Cranes and Technologies – one of the largest tower crane owners in Israel, and says the development marks a monumental leap forward for the crane and construction sector.
The Skyline Cockpit transforms the traditional tower crane operator’s cabin into a ‘smart’ ground controlled computerised cockpit, using new technology and advanced military-grade camera systems. According to Radius, using the system’s input, the operator can precisely identify where the crane’s hook will land, as well as receive indications regarding crane height, load weight, wind speed and direction, work speed and more, ushering in a new era of efficiency and safety.
The advantages of the Skyline Cockpit, it says, include: improved operator wellbeing, eliminating the operator’s need to climb, and it enhances the operator’s working/ sitting position. The company says the system also increases efficiency and safety, is accessible to operators with physical disabilities, and will help attract a younger generation of operators.
The system works by harnessing the power of Artificial Intelligence (AI) and Augmented Reality (AR) to provide operators with what Radius calls ‘unparalleled precision and situational awareness’.
As operators no longer need to climb up and down daily, Radius says accidents and incidents are reduced significantly. Comprehensive data recording means that any issues that do occur can be identified.
From the comfort and safety of an on-site ground cabin, users can navigate the tower crane using an advanced technological interface displayed on three large panoramic screens. Radius says this provides operators with an unobstructed view of the load line and the entire construction site. Offering a clear line of sight minimises the chances of collisions or accidents caused by limited visibility. This proactive approach enhances safety measures, ensuring the wellbeing of individuals and protecting the surrounding environment, it adds.
Operators benefit from improved working positions, Radius claims, promoting their wellbeing, while fostering inclusion and diversity by accommodating older, infirm and disabled individuals.
Operator welfare is increased with less isolation and a more convivial working atmosphere, resulting in a more efficient, quicker workflow on site, it adds.
Utilising advanced algorithms and machine learning, Skyline Cockpit includes intelligent assistance and analytics features. The system predicts potential risks, provides recommendations for optimal lifting techniques and optimises crane performance based on historical data.
The system provides real- time data on factors including load weight, wind speed and direction, crane height and work speed. With this information at their fingertips Radius says operators can position the crane’s hook with pinpoint accuracy, mitigating risks and optimising productivity
PROOF IN THE PUDDING
Radius recently debuted the Skyline Cockpit to the lifting industry at its headquarters in Northampton. The event, it says, was a success – providing and opportunity to see the system’s safety, wellbeing and efficiency benefits first-hand.
For some of attendees the opportunity of using the Skyline Cockpit helped quash any doubts they may have had. Former Select Plant Hire crane operator Katie Kelleher, who is now technical and development officer at the UK’s Construction Plant Association, tried the system at the demo day. “Like most people I turned up with ideas of how it would be and not many positive ones,” she revealed. “I was concerned it wouldn’t feel real, that the consequences of operating something so big and not being near it wouldn’t feel real and tangible. I am glad to say I was wrong, after speakin? to the operator Dale and having a go myself…… it’s brilliant! It feels tangible, the viewpoints work really well and I surprisingly adapted to it really quickly.”
Whatever the future holds for the crane cabin, remote or otherwise, as long as humans are involved in any part of crane control there will be a need for components that to facilitate Ittai-kan between human and machine.
Seeing is believing
With good operator visibility being so critical for safe working it’s logical that glass traditionally comprises so much of the crane cab. A problem with the medium of glass, however, is that it can smash causing dangerous visibility issues, says Saudi chemical manufacturing company Saudi Basic Industries Corporation (SABIC), which is 70% owned by oil and gas giant Saudi Aramco.
SABIC warns that tempered glass can shatter while laminated glass may exhibit white-out or fail when hit violently by heavy objects or flying debris – potentially causing harm, disrupting work and requiring costly replacement.
Other potential drawbacks of glass as a medium, it claims, are: its weight – which makes it challenging to transport, handle and install; it is difficult and expensive to create curved windows; and, finally, untreated glass does not fully protect against harmful ultraviolet (UV) radiation.
SABIC’s solution? It offers the option of replacing glass in cab windshields, enclosures and guarding with a its LEXAN polycarbonate (PC) sheets.
It says its LEXAN sheet’s light weight (50% less than glass) makes replacement glazing easy to transport and install in the fi eld. Plus, the option to use existing framing can save time and money.
It can be used for both flat and formed windshields, side, back and door glazing, visors, skylights and guards.
In addition, coatings can be applied to the surface of PC sheet to offer enhanced properties including abrasion resistance, UV protection, chemical resistance, anti-fogging, graffiti removal, and water run-off for visibility.
Specifi cally for crane applications, the company recommends its LEXAN MARGARD sheet and ULG1003 sheet.