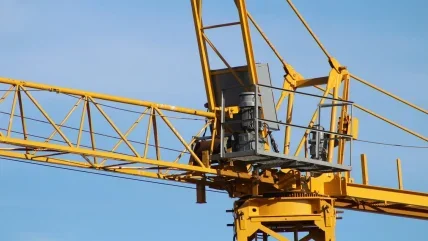
In the modern world two themes have become paramount. One is energy: it needs to be cleaner, greener, and more efficient. The other is pollution: emissions, from all kinds of industrial processes, need to have less particulate matter and fewer pollutants of all kinds.
The energy requirement calls for economies of scale – which adds size and weight to the machines that generate power. Where fossil fuel is used larger turbines with modern designs give greater efficiencies and proportionately fewer emissions.
These components are huge, and consequently heavy. Similarly, scrubbers and the like on industrial plants need changing and improving; and they, too, are large and heavy components. Specialised transport companies are rising to the challenge in impressive and imaginative ways.
Finnish company Boliden, for example, produces copper, nickel, gold and silver in its smelting works in Harjavalta, in the west of the country. It is in fact the only nickel smeltery in western Europe and, compared to other nickel smelteries around the world, Harjavalta has the lowest sulphur dioxide emissions per tonne of nickel produced. In order for this to remain the case the electrostatic filter for cleaning the flue gases has recently been replaced.
The filter to be removed weighed 243 tonnes. Not only is it heavy it is large, too, with a length of 16 metres, a width of 13.80 metres, and a height of 16.60 metres.
It needed to be taken from the operation site near the chimney to the scrapyard for disposal.
The heavy load specialist company Vuorsola from Pori, Finland, was hired for this task. Key to the move was the use of two lines of ten axle Cometto SPMTs in parallel formation.
“First of all, the electrostatic filter was attached to a crawler crane and cut out of the steel construction by experts using a thermic lance,” says Petri Toriainen, project coordinator at Vuorsola, describing the initial steps.
UP AND OVER
The next challenge was that an office block stood four-square in the way. “The hulk – which was as big as a block of four flats – had to be swung over the building and lowered so that it could be transferred to the SPMT combination,” explains Toriainen.
Vuorsola employee Arto Tammelin, together with a colleague, positioned two ten-axle combinations of its brand-new Cometto SPMT precisely under the load and set off. They had to negotiate a tight 90-degree bend immediately after the start.
The high load then had to pass under a conveyor belt. “We lowered the mid driving height of the SPMT’s a little here,” said company CEO Mikko Vuorsola, “in order to gain the last few centimetres of space. The whole thing went like a dream.”
Immediately afterwards, the new filter, standing on elephant feet, was also transported with the SPMT from the assembly location to the crawler crane, so that it could again lift them over the office block.
“Time is money,” says Joachim Kolb, Sales Manager at Cometto, about this speedy handling, “and in the process we once again made an important contribution to keeping the environment clean.”
SCRUBBER SHIFT
A similar problem confronted two sets of contractors in Chile. When a 27 metre and 120 tonne gas scrubber arrived at the ENAP Aconcagua Refinery in Chile each company involved wondered how to handle their portion of the installation process.
DSV Global Transport and Logistics (DSV) needed to transport the scrubber to the crude oil refinery, which processes most of the fuels consumed in the Valparaíso region of Chile. Although DSV had a plan for delivering the scrubber, it required assistance determining the best method to offload the enormous device from its transport vehicle and place it in storage. It called the offices of heavy lift and move specialist Engineered Rigging in Santiago for help.
Engineered Rigging identified the Enerpac SBL500 hydraulic gantry system, equipped with the SSU300 hydraulic side shift units, as being the ideal equipment for the manoeuvre.
Engineered Rigging’s heavy lifting experts mobilised and assembled the SBL500 from the Santiago yard. The gantry has an octagonal boom for added strength and increased capacity and lifting height, and an Intelli- Lift wireless control system. On the appointed day the operator remotely lifted the scrubber from DSV’s specialised transport system and lowered it onto static storage stands. ER’s team then disassembled the gantry and returned with it to Santiago.
“It took us just four days to build the gantry, offload the scrubber and deconstruct the gantry for transport back to our yard,” said Arnol Salicetti M., Engineered Rigging’s director of South America equipment rentals and sales.
Meanwhile, the general contractor, Echeverria Izquierdo Montajes Industriales (EIMISA), had completed its preparations for installing the new equipment within the refinery. It needed to move the scrubber from the storage stands to its permanent location inside the plant. It too needed help and, by coincidence, also called on Engineered Rigging for this final portion of the project.
Three technicians assembled and tested the SBL500 hydraulic gantry, while a crew of four assembled and tested a Goldhofer self-propelled modular transporter (SPMT) provided by ER’s South American partner Tecnogruas. The Engineered Rigging (ER) team then hoisted the scrubber from the storage stands and lowered it onto two Goldhofer PST/SL-E six-axle SPMTs, each powered by individual power units. The gantry was then repositioned next to the crane that would place the scrubber in its final site within the plant.
In a single day ER transported the scrubber nearly one kilometre within the refinery. This included a 90-degree turn which required each SPMT and associated power pack unit to operate independently of each other. This type of turn is only possible because of the SPTM’s ability to move sideways as well as forward and back. ER technicians then used the SBL500 hydraulic gantries to offload the scrubber from the SPMTs. The mammoth gas scrubber was moved safely, on budget, and in only five days.
Mammoet tailors approach for Triple journey across Uzbekistan
There were good wide paved roads and narrow unsurfaced ones; there was also hilly terrain with tight curves and weak bridges. The varied topography of the route turned a di cult transport job, of 2200 km no less, in effect into three distinct journeys.
The loads were three gas turbines weighing 517 tonnes apiece, destined for the Sirdarya power plant near the city of Shirin, Uzbekistan. The combined cycle power plant is designed to improve generation e ciency and capacity in the country while reducing the environmental impact. It has two 750 MW power generation units with an e ciency of more than 60 percent and will deliver annual savings of up to 2.2 million tons of carbon dioxide emissions. But bringing the gas turbines to the site was a very major challenge.
Uzbekistan is landlocked. The turbines had to be moved from a port on the Caspian Sea in neighbouring Kazakhstan to the plant in Uzbekistan. And each of the three different sections of the route required a different, specially tailored, solution.
Mammoet Kazakhstan found the solution in its robust and reliable THP/SL heavy-duty modules from Goldhofer. In combination with two Goldhofer ‘ADDRIVE’ modules, plus ‘ADDRONIC’ for the synchronisation, more than 68 axle lines were in use at peak times.
For the fi rst 500 km section, mainly on good roads, a THP/SL 19-axle side-by-side combination was chosen to transport the gas turbines. Up to five prime movers (three in the front and two at the back) were used to handle the many steep gradients. MAN 41.680 heavy-duty trucks with V8 engines developing 680 hp ensured that su cient traction and pushing power were available.
The second section through Uzbekistan had steep curves, narrow unsurfaced roads, and bridges with limited load bearing capacity. To negotiate the curves, and to achieve optimum weight distribution on the bridges, the 15 m long and 6.3 m wide gas turbines were transloaded onto Mammoet’s high girder frame AL600, then mounted front and rear on a 20-axle THP/SL P(1+1/2) combination with two ‘ADDRIVE’ modules, which were synchronised using ‘ADDRONIC’. This allowed the two modules to be fully integrated in the combination for additional traction and pushing power on steep inclines. The full power was available at a click of a button to bring the convoy to top speeds of up to 18 km/h.
The combination gave enough tractive power to carry the ultra-heavy loads up the hills, and also provided the braking power needed for safe travel on the downhill sections. At higher speeds, the »ADDRIVE« modules switches off automatically and then switches back on again when the speed falls again.
The main obstacles on this section of the route were the many bridges whose load-bearing capacity was far too low for such a combination. The 60 axle lines of the THP/SL heavy-duty modules alone were insufficient to meet the maximum axle load requirements. To observe the limits on the individual bridges the heavy-haul experts at Mammoet employed a strategy that they had already used many times before: They positioned an eight-axle Goldhofer modular vehicle, known as a belly trailer, directly under the high girder bridge to let it take a share of the heavy load directly – see diagram below. “The eight axles under the high girder bridge had to be steered separately front and rear. Continuous monitoring and adjustment of suspension on the belly trailer enabled us to pass over each of the bridges safely and reliably at walking pace,” says Marek Lysko, operations manager at Mammoet Kazakhstan.
On the last section of the journey, Mammoet loaded the turbines on a heavy-duty self-propelled combination, which covered the last kilometres to the power plant.
“We were able to plan and implement the whole operation with such precision because Goldhofer’s heavy-duty modules can be combined with extreme fl exibility and confi gured to meet very specifi c requirements,” said Marek Lysko.
Transport of rail locomotive 2,250 km across Mexico takes 14 days
Some loads should clearly travel by rail. Railway engines are a prime example; but there are cases where the locomotive is present but the rails are not.
Mexico’s Tren Maya is a showcase infrastructure project involving the construction of a 1,500 km railway line linking Mexico's tourism destinations and Maya sites. For the new railway, the Pesado heavy haul company was commissioned to transport an electric locomotive weighing 180 tonnes from San Luis Potosi to Valladolid, Yucatan. The locomotive is 18 m long and 4.7 m high; the distance involved was 2,250 km.
Heavy haul expert Pesado, which was formed in 2012 from the construction company ESEASA Construcciones, has a lot of experience in transporting heavy and oversized loads – especially under challenging conditions – and is well known for reliable transportation and punctual delivery of the heaviest loads in Mexico.
For this job it chose a Goldhofer 12-axle THP/SL heavy-duty combination with a drop deck designed for a payload of up to 300 tonnes.
According to Pesado the drop deck was necessary because of the locomotive’s 4.7 m overall height. Thanks to the drop deck it was possible to reach Valladolid on a more or less direct route and mainly using federal highways.
The departure from the loading yard was the first test of the Pesado team’s capabilities: the combination load was 69 metres long. But with a 55° steering angle and +/-300 mm hydraulic axle stroke, no serious problems were caused by the tight spots on the route including roundabouts and junctions. “It was a challenging journey through tourist areas with narrow roads and tight radii, but the precision steering available with Goldhofer’s THP/SL modules made safe and accurate maneuvering possible even under such conditions,” said Ramiro Muñoz Martinez, specialized transportation engineer from Pesado's Heavy Transport division.
The combination was powered, sometimes in the push-pull mode, by two 515 hp Western Star 6900XD 8×6 heavy-duty tractors. The 335 tonne rig, with an overall width of 3.3 m and a total height of 5.06 m, reached its destination in Valladolid, Yucatan in 14 days.
500 tonne Submarine travels on german road
German transport specialist Spedition Kübler transported a 50 metre long submarine weighing almost 500 tonnes from the harbour in Speyer, Germany, on the river Rhine, to the Technik Museum – a total distance of four kilometres.
To transport the submarine Spedition Kübler utilised 30 Scheuerle InterCombi axle lines as part of a push-pull trailer combination measuring up to 90 metres in length at times.
Scheuerle believes it may have been the longest rigid platform trailer combination ever seen on public roads in Germany and the move took five years of planning.
According to Scheuerle, the manoeuvrability and robustness of its InterCombi modules were key to the success of the project, overcoming multiple challenges along the way.
The first challenge was getting the submarine onto the trailer. The submarine had been transported from the Kiel Fjord, across the North Sea on an ocean-going fl oating pontoon, followed by a long journey down the Rhine. Once at Speyer the trailer reached the shore-connected pontoon via a ro-ro ramp where the submarine was hydraulically raised to a height of 1.4 metres using eight hydraulic cylinders, each with a lifting capacity of 100 tonnes, so that the 30 axle lines could be pushed underneath.
The sheer weight and length of the load and trailer combination on the road was the next consideration. By using the 30 InterCombi axle lines Spedition Kübler was able to reduce the load weight on the road down to 2.48 tonnes per wheel. At times additional towing and pushing vehicles were required to protect the road surface from the immense traction, meaning that the vehicle combination grew to around 90 metres.
Spedition Kübler also used the InterCombi’s maximum +/- 60 degree steering to navigate a sharp bends.
The high axle compensation of the hydraulically supported pendulum axles, totalling 650 millimetres, was also necessary in order to drive the load over roadway obstacles such as kerbs or to negotiate inclined grassed areas at the side of the roads covered with metal sheeting by means of the automatic load levelling.
Just a few hundred metres before the submarine arrived at the museum Spedition Kübler also encountered an unexpected set of traffic lights and a parked car; both had to be removed.
Finally, a fi re alarm pillar at the Technik Museum, which had not been dismantled for safety reasons, protruded into the designated route by just a few centimetres. This was enough, though, to require the vehicle combination, which measured over 70 metres long at this point, to reverse out before trying the approach again. On the second attempt the submarine was successfully installed in location at the museum.
In 2024 the submarine will once again be moved from the museum in Speyer to the Technik Museum Sinsheim, approximately 40 km away.