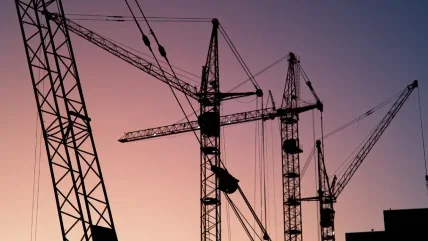
Micha Gouweleeuw is director and owner of the of Netherlandsbased company bearing his name. It specialises in repair and refurbishment and repainting of all types of lifting equipment – ‘vertical transport equipment’ is the phase that the company uses. A recent project includes the restoration of a Goldhofer THP/ST special transport trailer for client Allelys (see box on p23). Mobiles, tower cranes, all terrains and crawlers are all within its remit.
“Delivery times for a new crane can be up to two years,” Gouweleeuw outlines. “The cost of a new crane has risen 25% over the same time period. A crane that might have cost one million euros back then will be 1.2 or 1.3 million today.
“So an owner with a crane that is six or eight or ten years old will ask: ‘is this crane finished as a useful lifting machine?’ And the answer is: 'No: it is not.’”
Cars quickly lose their value with age; cranes not so much. “Depreciation on a crane after the first few years is almost zero,” Gouweleeuw says. “A crane that is ten years old can sell at the same price as a crane that is 50 years old: the value depends on whether they are in good working order, not on their age.”
A complete restoration of a crane, he says, can take up to five months depending, of course, on the crane’s condition; but after that the crane is as new: “We take the cab off, we take all the electrics out, we completely dismantle the entire machine.”
Spare parts, or parts that need replacing, do not have to be backengineered: “OEM manufactured parts are not a problem: we have good relationships with Manitowoc, Liebherr, Tadano – we do work for them, painting their new machines pre-delivery to customers – and supply lines are very short; we can consult their technical guys at any time if we need to.”
A recent project was a Terex Demag TC 2800-1 restoration for Global Crane Services in Aberdeen, Scotland. “The crane had been six years working on the North Sea coast,” explained Gouweleeuw. “Everything was shot; we gave it a complete restoration.” The crane was fully stripped down and dismantled. Just lifting the crane body from the chassis was a 50-tonne lifting job, handled by one of Gouweleeuw’s two overhead cranes. That was one of the five-month jobs.
At the end of it the restoration the crane was shipped back to Scotland in its bright-orange newpainted- by-Gouweleeuw livery.
But even a paint job on a crane can be no small matter – indeed Gouweleeuw describes it as ‘a profession in itself’. The company has a 35-metre mast hall, where mast sections can be extended; their two overhead cranes, with heavy-lift forklifts, enables it to paint cranes of up to 1000 tonnes.
WORKING RELATIONSHIP
Repair and restoration specialist Crowland Cranes is based in East Anglia, UK. It is an insuranceapproved repairer for both the crane and plant industry.
It also carries a stock of parts from manufacturers that are no longer in existence.
Avezaat Cranes is a Dutch company with similar specialist skills. It is known in the industry for its structural and boom repairs and has a talented skill base and the necessary infrastructure to ensure work can be completed in-house.
In December 2022 Crowland Cranes and Avezaat joined forces; they are now officially ‘joint service partners’.
“This is, to my knowledge, the first time this has happened in this field,” says managing director Pete Issitt. “And it is a good thing for us both. Sharing our experiences and using each company’s services only strengthens both our positions when completing crane repairs.”
The companies had already worked closely over the past few years on various crane repair projects. "The new arrangement opens new channels for both of us,” explains Issitt. “We can both benefit from the experience and knowledge that we each hold within the crane repair business.”
On the Dutch side Bert Avezaat Jr is equally pleased: “We have been working with Crowland Cranes already for many years and completed a lot of projects and have learned to know them. We are looking forward to expanding our working relationship.”
MANUFACTURER REFURB
Almost all crane manufacturers offer after-sales services while some go even further with complete refurbishment, remanufacture, and used-crane sales departments.
Liebherr has its ‘Reman’ programme: designed for mobile and crawler cranes it offers three different levels of remanufacturing levels and demand has been such that last year (2022) Liebherr relocated its German repair facility for it from its manufacturing base at Ehingen (where it had been for 40 years handling around 200 used machines a year) to new and larger premises at nearby Berg.
“The move means we can handle emergency repair work at short notice,” says Andreas Leicht, manager of the repair centre, “so we can get cranes up and running again quickly.”
The space at Ehingen that has been freed up by the move is being used to build up a new spare parts warehouse, which will also speed up services and repairs.
“We are still only five kilometres away from Ehingen so we will be receiving material from there every day; and our experts from the design and production departments can be consulted quickly if we have any questions,” says Leicht. “That creates perfect conditions for us, even if we are facing complex repair work.”
General overhaul is the lowest cost option from the Reman programme. The components are removed from the machine, remanufactured to return them to as-new condition and brought up to the latest technical standard where possible, and then returned to the machine. The entire component is covered by the same warranty as a new part. The machine is obviously out of commission at the Liebherr works while the work is done; but by planning ahead, say Liebherr, downtimes can be avoided.
Exchanging components – refurbished for old – is the fastest option; The components are replaced by a remanufactured component with the same warranty as a new part. Service life and performance are identical to those of a new part. In addition, Liebherr will pay a part-exchange fee if you return to them an old part which can be repaired.
Repair is the damagedependent option. After dismantling and inspection, an individual quotation is prepared for repairing the component. The warranty covers the repair work or the entire component depending on the extent of the repairs and the component.
Remanufacturing a component – that is restoring the defective part to its original condition – offers savings in time and cost, says Liebherr. This is thanks to its standardised processes that give fast turnaround times for component remanufacturing and because the remanufactured part is cheaper than a new replacement. It is also ecofriendly; reusing a part clearly takes fewer of the earth’s resources and emits less carbon than making a new one. Liebherr’s exchange parts, general overhaul or repaired parts offer the same original-manufacturer quality and come with a warranty for longterm use.
ENCORE UNE FOIS
Manitowoc offers remanufacturing through its EnCORE programme. It applies to tower cranes as well as to mobiles and includes repair, rebuild, remanufacture, and component exchange elements. On occasion it goes the extra mile for a customers – see box on p19.
Rebuilds are by factory-trained technicians to OEM standards. The process can include everything from rebuilding cabs or boom cylinders to updating all systems and renewing electrical harnesses, instruments, drive-lines, hydraulic components and hoses. Remanufactured parts include engines, transmissions, hydraulic cylinders and more; each part comes with a one-year warranty and the crane, says Manitowoc, will be restored to original engineering specifications.
For Potain tower cranes Manitowoc offers three service levels. The ‘Check-up programme’ includes complete inspection of the crane including powered tests; a detailed report that describes the condition of more than 300 checked components.
The ‘Working Condition programme’ adds mechanisms and safety devices repair, slewing ring bolts check, new hoist and trolley wire ropes, and the crane ready to work on your jobsite with six months warranty on parts and labour.
The ‘Premium programme’ includes dismantling and inspection of all components, with shotblasting, zinc primer coat and finish coat, mechanisms and safety devices refurbishment (rather than repair), replacement of all wire ropes, and a new slewing ring and new slewing ring bolts.
Manitowoc has EnCORE Certified Partners located throughout the world and EnORE also offers sales of refurbished used cranes with a stock of 70 or more usually available.
Whichever route a crane owner takes, specialist or manufacturer, the repair and refurbishment of cranes plays a pivotal role in enhancing efficiency, safety, and sustainability. Through this process, outdated and wornout cranes are transformed into robust, modern machines capable of meeting the demands of today's dynamic work environments. By upgrading key components, implementing advanced technologies, and adhering to rigorous safety standards, companies can maximise their return on investment while minimising environmental impact. Moreover, the refurbishment process contributes to the circular economy by promoting reuse and reducing waste.
The refurbishment of cranes will remain a critical practice for crane businesses seeking to optimise their operations, enhance productivity, and remain competitive in a rapidly changing world.
keeping the operator happy
Skilled labour is increasingly hard to fi nd, so when a company fi nds the right candidate it’s worth making an effort to persuade him to sign up. A steel-erecting company in The Netherlands needed a crane operator. Van Gerstel Montage, based in Kaatsheuvel, had found the perfect candidate to join its expert and close-knit team. But there was one problem: the operator was currently working on an older Grove GMK3050 and he liked this crane model so much that he wanted to continue working on it into the future.
“We asked him what it would take to get him to join us,” said company owner Rens van Gestel. “And he said, ‘a nice, pristine, original GMK3050’.” That was easier said than done. The GMK3050 is a crane that was introduced over a quarter of a century ago in 1996 and discontinued in 2006. Grove’s current model is its third-generation successor, the GMK3050-3. “But we talked to the guys at Manitowoc EnCORE in Breda” said van Gestel, “and they got to work. In no time at all, they had found an original GMK3050 that fi rst rolled out of the plant 21 years ago. So once we identifi ed the crane we then had to figure out the best way to give it a new lease of life.”
Despite its two decades of service the crane had only covered 80,000 km and clocked up 8,000 working hours under its two careful owners. It is a durable design and the crane was still in extremely good condition when the technical team from EnCORE started their work. An inspection suggested a range of repairs, revisions, and cosmetic work to return it to its former glory. With agreement for the updates from Van Gestel Montage, refurbishment began.
Major components including the boom and winch underwent specialist refurbishment; a suite of other minor repairs and upgrades followed. Then the bodywork received some attention; every dent and crack repaired before the crane received a full respray, finished with clear coat paint and carbon decals. Following the commissioning of the crane in mid-November at Manitowoc’s Breda facility, the customer took delivery of its latest addition. Just a day or two later, the crane was out and working for Van Gestel Montage, proudly sporting its new livery and with its new operator at the controls.
Happy Birthday john sutch! A blast from the past from Crowland
John Sutch of John Sutch Crane Hire celebrated his 70th birthday last year and asked for an unusual present. The fi rst crane he ever operated, as an apprentice back in 1973 at the age of 20 and 17 years before starting his own fi rm – was a Hydrocon Highlander, a two-axle truck-mounted latticeboom manufactured by Lambert Engineering in Scotland. The company ceased operation in the 1980s. Sutch asked Pete Issett of Crowland Cranes if he could fi nd and restore a Highlander!
“We found one, parked up in a wood near Tonbridge in Kent,” says Issett (pic 1). “It was well overgrown; it had been there for some time and appeared to have become part of the woodland. Records showed that it had been manufactured in 1966 and had not been road-taxed since 1985 – which presumably meant that it had been left in the woods for some 30-odd years.” Crowland took it back to its yard (pic2) and took on the job of restoration.
Over a period of two years it stripped the machine back to its base (pic3), sandblasted, cleaned and rebuilt it. The cab was removed and restored (pic4) and the correct tartan upholstery for the doors sourced (pic5). Originally in a brown livery, the crane was sprayed-painted in John Such’s company colours (pic 6); and on Fathers’ Day last year the completely restored machine (pic 7) was presented to John Sutch. Today it is in Liverpool standing proudly stands outside the company’s office.
Gouweleeuw restores Allelys' transport trailer
Gouweleeuw was faced with a Goldhofer THP/ST special transport trailer owned by Allelys to bring back to good condition.
First, the wheels of the Goldhofer were disassembled and cleaned separately – the Goldhofer has eight wheels per axle, and ten axles, so this was not a small task.
The Goldhofer was then cleaned in the company’s dedicated washing area. By using the maintenance pit and the landing, thorough cleaning was possible from all angles.
The parts that did not need to be blasted were masked after cleaning and sanded manually or prepared by machine. This was followed by blasting with Speedblast; this is a very fi ne metalfree sand-blasting material.
After preparation the Goldhofer was sprayed with a primer coat, followed by a red paint coat. The wheels were re-mounted and fi nally the quality controller checked whether the result met the quality requirements. The Goldhofer now a fresh look and can perform many years of work again.