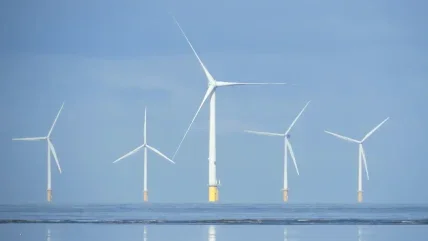
Talk sustainable energy sources – wind, solar, hydro, tidal, geothermal, perhaps nuclear – and wind power is the most visible of them. It is also the one that, arguably, offers the most immediate, and one hopes heartening, progress towards large scale green energy supply. This is particularly true of offshore wind where the towers and blades used can be several times greater than their onshore cousins. Jackets and monopiles are reaching both heights and weights that are pushing the capacity of lifting apparatus to the limits. We wrote recently, in the dockside lifting feature in our June 2023 issue, about how dockside installations have been increasing in size and capacity to manage the everincreasing lifting demands of offshore installations. We make no apology about returning to the subject here. Climate change, and the energy transition that perhaps may limit it, is a defining challenge of our time. The progress, the scale, indeed the speed of development here is immense and lifting companies are at the forefront of it.
One consequence of their efforts is that the costs per generated gigawatt of offshore windfarm installation have fallen by more than 60% over the past three years (source: industry body Wind Europe). A significant bottleneck, though, is the availability of dockside installations that can handle the huge components.
WORLD’S LARGEST ELECTRIC CRANE
As an illustration of that problem, and of the measures being taken to tackle it, consider this: the world’s largest electric crane is now being built. And it is being built specifically for offshore wind.
The Mammoet SK6000 is a ring crane with a capacity of 6,000 tonnes. It has been some time in gestation – the project was announced in 2020 – but its first parts will soon be delivered to Mammoet’s central engineering plant in The Netherlands. Fabrication and production will continue through the year to ready it for its first project, with delivery scheduled in 2024.
Mammoet has announced the crane will have a fixed-jib configuration that will allow offshore wind developers to reach deeper waters and significantly cut the cost of floating wind assembly. Lifts of 3,000 tonnes at 220 metres height will become a reality. The new configuration means that the crane can load out floating foundations using its main boom, then immediately use its fixed jib to assemble the turbine tower.
No reconfiguration will be necessary between scopes, further improving build efficiency.
The crane sets a new standard in worldwide heavy lifting, says Mammoet. Its outreach, hook height and lifting capacity allows customers to construct with heavier and larger components than ever before.
The new ring crane shares the same engineering DNA as its predecessor, the SK350, with similar design principles and lifting techniques. “This was always the basis of our original design philosophy,” says Mammoet technical expert Jeremy Haylock. “We wanted to develop a product that would be scalable and agile. Because the world is developing so quickly, and the changes around us are so vast, our aim was to deliver a product that would allow us to grow in real-time with our customers.”
Like earlier models, the SK6000 is containerised, enabling swift mobilisation and on-site assembly. It has been designed with next generation offshore wind farms in mind and will serve all global energy markets where additional lifting capacity is needed.
“As the industry moves towards 20MW turbines, offshore wind components continue to grow in size and weight,” Haylock continues. “More lift capacity is needed. The SK6000 delivers this capacity and unlocks a major design constraint. It will enable customers to integrate higher and bigger turbines, and launch heavier foundations, be they fixed or floating.”
And for those who suppose that diesel is indispensable to heavy lifting it shows these heaviest of offshore lifts can be carbon free.
The SK6000 will be operational very soon; it is at present, nevertheless, a work in progress. For an example already in operation point to Mammoet’s PTC210-DS ring crane installation at the port of Nigg, Scotland, where it has been serving the Seagreen offshore wind farm. It has taken years of planning and work to bring crane, and project, to fruition. A defining issue was the high tides at the port. The final wind turbine, however, was installed at the end of June this year and two-thirds of the project’s 114 turbines are already supplying green energy to consumers. The box on page 32 tells the full story.
FLOATING FARMS
Mediterranean tides are much less problematic than North Sea ones. They average only around half-a-metre, one-eighth of the range at Nigg, which means that on-loading windfarm components by SPTM remains a sensible option. Provence Grand Large offshore windfarm, off the coast of Marseille, is France’s first pilot floating wind farm.
Southern France has a very narrow continental shelf, which limits the potential for farms on the seabed. Instead, Provence Grand Large will have three 8.4 MW wind turbines from Siemens Gamesa erected on innovative pyramidshaped floating foundations; they are anchored by tensioned mooring lines which do not disturb the seabed or its ecology. Their footprint on the maritime domain is reduced to a few dozen metres compared with several hundred for existing technologies.
The first phase of the project, the onshore lifting of components for assembly, has been completed; the second phase, the weighing and load-out of the three floating foundations onto the outgoing barge, began in March this year (2023) by Sarens. Each floating foundation weighed around 2800 tonnes and was 45m high and 70m wide. Each had to be weighed then transported to, and positioned on, a semi-submersible barge.
For the weighing Sarens used nine 500 tonne load cells, the same number of hydraulic jacks, three hydraulic power packs, and a weighing interface.
The load-out took place in June and involved two trains of K24ST SPMTs; six powerpacks – four in use, two as spares; two six-axle SPMTs for auxiliary works; and four 30-metre MB1500x1000 modular beams.
The foundations were transported by the two SPMT trains a distance of 50 to 150 metres to the quay wall. Crews worked in two shifts to keep up with the vessel float-off operation and finally loaded out the floating foundations onto the barge.
Provence Grand Large is a pilot project intended to demonstrate that offshore floating windfarms can become economically viable and is France’s first ‘precommercial’ floating offshore wind farm. It is scheduled to begin producing power at the end of this year.
PRECISION ALIGNMENT
Construction of windfarms is not complete when the towers and nacelles are erected. The blades still need to be attached and this can be one of the most delicate and difficult parts of the operation. It has to be done on-site – which is generally windy and blades, of course, are of a shape that is designed specifically to catch the wind. Controlling these monsters – they can be 100m long and more – at great height, and aligning them with absolute precision so that the fastening bolts can be secured, is no task for the fainthearted.
Huisman and Siemens Gamesa have combined their expertise to develop a solution. It is especially intended for blades but can also be used for nacelles and tower segments. Its Travelling Load Stabilising system can be applied universally, it claims, on heavy lifting cranes to stabilise wind turbine components during installation.
It consists of a combination of two pairs of tuggers working in unison to control the load. One pair, fitted to independent trolleys, can travel along integrated rails – with one set on each side of the crane’s stiff boom. The trolleys are thus separated by the width of the boom. Lines from them run to separate positions on the load and keep it from rotating in the horizontal plane. They automatically follow the crane’s main block to stay level with the load.
The second pair of tugger lines is deployed from the crane tip – again one from either side of it, so again separated by the width of the boom. Their tugger lines provide a vertical force, perpendicular to the first pair of tuggers, and keep the load steady in that plane. By approaching the load from two different directions the system provides significantly more control than a conventional single pair of tuggers.
The tuggers are always at the optimal elevation and the boom trolleys have much higher stiffness than flexible taglines, increasing control and workability.
A specially designed control system holds the actual position of the load, resulting in a much stiffer restraint, and therefore higher positional accuracy compared to conventional tugger systems that rely on constant tension. In case of an unexpected overload the system will give way but will return to its position setpoint when the force drops below the threshold again.
The Travelling Load Stabilising System functions as an integral part of the crane and can be operated from the crane's cabin as well from an optional walkaround box.
The system makes blade installation feasible even under challenging wind conditions. “This is crucial for the technical readiness of next-generation offshore wind turbine installations,” says Jesper Moeller, chief engineer execution at Siemens Gamesa. “The resulting increase in installation uptime will be accompanied by a positive effect on operational activities in general, as well as on-site safety. We see the system as a potentially new industry standard with benefits for the whole wind industry, providing more productive vessel days.”
As we approach the milestone of passing the one-terawatt mark in installed wind-powered generation capacity, it is clear that the offshore wind sector, bolstered by innovative crane technology and collaborative endeavours, will play a pivotal role in shaping the future of sustainable energy supply. The continued dedication to pushing the boundaries of what is possible in lifting reaffirms the industry's commitment to meeting the demands of our time and driving us closer to a cleaner and more sustainable energy landscape.
Smooth operator: change of plan ensures No tide delays at Nigg
The port of Nigg is a marshalling facility for Seagreen Offshore Wind Farm. Seagreen will be the world’s deepest fi xed-bottom offshore wind farm. It lies 27km from the coast, where winds are stronger and more reliable. It is due to become operational this year and will be capable of powering two-thirds of Scotland’s population.
The 114 wind turbine foundation jackets at Seagreen stand 95m tall and are robust enough to support the new 10MW variants of Vestas turbine. They weigh 2,200 tonnes apiece. They arrive by sea and are loaded-in and loaded-out onto their transport barges at Nigg.
Nigg is tidal with water levels rising and falling by more than four metres every six hours. This extreme tidal range is difficult to compensate for using ballasting; you cannot keep the barges level with the quay. So load-in or load-out of large jackets is delayed when waters are too high or low; that leaves the installation vessel waiting, miles offshore, with no work to do. And the installation vessel is the project’s most critical asset.
Working years in advance, Mammoet proposed a solution to speed up the work.
The need was to fi nd a methodology that would keep the installation vessel as productive as possible. In other words, it needed always to have a jacket to hand, on a barge at the offshore site, ready and waiting to be set on the seabed. The team looked beyond the jacket handling scope to determine how all scopes could be optimised to protect this critical path of the installation campaign.
The conventional approach would have been to mobilise a fl eet of SPMTs, then use these to complete all manoeuvres to place the jackets onto barges. It is the obvious solution and was, in fact, the initial plan.
But Mammoet realised this would impose limitations on how the work can be performed as it needs the barge to be level with the quay. On days with high tidal range the operational window would thus be closed.
Also, if SPMTs need to drive on and off the barge then deck space needs to be permanently cleared. This limits the area available for stowing the jackets, grillage beams and sea fastenings. Larger and stronger barges can overcome these limitations, but this reduces the size of the fl eet that can be used for the project, causing supply chain issues. Since 114 jackets required load-in and loadout ine? ciencies would quickly add up.
So Mammoet suggested a different approach: a combination of SPMT transporters and the company’s PTC210-DS ring crane. This approach removed the impact of tidal shifts on the project schedule. The fi vehour operational time that would be expected for an SPMT load-out of this nature typically allowed only a single manoeuvre per tide. Crane lifting has no such limits as the barge deck no longer needs to be level with the quay.
The ring crane also enabled smooth parallel operations, as it could load-out jackets to a waiting vessel while SPMTs offloaded others. Outside the delivery windows, jackets could be brought to the quayside, within lifting range of the crane, well in advance of a vessel arriving from offshore, cutting down on crane waiting time and so maximising the output of the installation vessel.
MAXIMISING OUTPUT
Where it takes around one shift to load each jacket using SPMTs – even if conditions are good – the PTC210-DS has been loading-out two jackets in a single shift, providing there are barges ready for it. This has increased the feeder vessel cycle time and reduced downtime for the installation vessel at sea.
Was the decision to use a large ring crane a simple one? “Not at all,” says Mammoet UK technical sales manager Oliver Smith. “As ever, when an organisation is deciding on a project of this scale, cost-e? ciency is always an important factor. We were involved with this project years in advance, well before some of the full details came to light. It was only further down the line that we needed to reassess the situation and move away from SPMT-only operations.
“This change in plan wasn’t small either. We knew that our customer would, in turn, need to secure buy-in from their customer that the proposed solution would deliver results. We integrated engineering teams to demonstrate the fl exibility of the solution and work through the risk, while in parallel we were working with our customer on the commercial calculations, proving that the numbers did indeed add up.”
The first jackets were delivered to Nigg Energy Park in July 2021. They were loadedin using SPMTs, then o? oaded and stored in their pre-positioned blocking arrangement on-site. In September that year the jackets were lifted from this arrangement and transferred to the quay edge, again by SPTM, and from there were loaded onto the feeder barges using the ring crane. They were then towed in a 36-hour journey to the installation vessel and set up 27km from the coast.
Smith says everything proceeded as planned and the feedback from the client has been positive: “We knew this method was safe, flexible and more cost-effective than using SPMTs. Now we can share it with the wider industry so it can serve as a template for how to get offshore wind infrastructure in the water faster and more cost-efficiently; especially where tidal variances are high.”
Carbon Storage becomes reality in north sea
The offshore environment offers more than wind farms in the transition towards carbon neutrality. Carbon storage is another possibility that is now becoming a reality. The idea is to capture C02 emissions at their source, to liquefy them, and then to transport them offshore by pipeline to inject the liquid into saline aquifers or the voids left by oil extraction beneath the North Sea.
In May this year the North Sea Transition Authority, the body that regulates the energy industry in the UK’s sectors, offered 20 carbon storage licences at offshore sites, including some near Aberdeen, Teesside, Liverpool and Lincolnshire. The licences total around 12,000 square kilometres, which makes them a little bigger than Yorkshire. The aim is to store up to 30 million tonnes of carbon dioxide per year by 2030, which is approximately 10% of total UK annual emissions in 2021. The first injection could come, it says, within six years.
Norway, the other major owner of North Sea economic zones, is further ahead. Its ‘Northern Lights’ programme is already developing the infrastructure. A CO2 receiving terminal in the municipality of Øygarden in western Norway is under construction and will be ready for operations in 2024. It will receive CO2 by ship, then send it by pipeline to safe and permanent storage in a reservoir 2,600 metres under the seabed.
For several weeks in January, Sarens was involved in moving 12 carbon dioxide tanks on behalf of the project. The transport operation called for 24-axle K24ST SPMTs and two Maxi power pack units.
Load capacity was critical at the site: it was crucial to stay below fi ve tonnes per square metre. The SPMTs transported each tank from the quayside to the storage area, a distance of approximately 600 metres. Each of the 35-metre long, 230-tonne tanks was moved along two lines of 12-axle SPMTs with two power pack units. The tanks had to be transported at a certain height to pass though the fi xed entry gates at the jobsite. For this reason high cribbing on the trailers was required.
The weather in Norway was windy and unpredictable, but with patience and skill the team was able to complete the operation successfully.