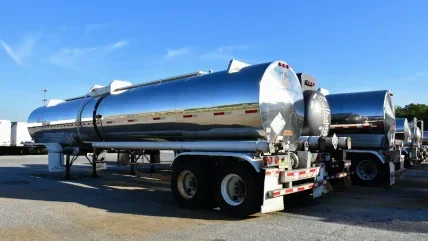
One of the many effects of Russia’s invasion of Ukraine has been that it has concentrated minds on energy supply. With sanctions applied against buying from Russia, and pipelines shut down or blown up, a freezing, oil-and gas-rationed winter was feared for many countries in Europe. Fortunately the winter was kind. Even Germany, the most dependent country in Europe on Russian gas, got by. But huge efforts were made by many to locate and secure alternative sources of oil and gas.
Germany’s breakneck-speed installation of two floating terminals for LNG deliveries at Mukran and at Lubmin on the Baltic coast are just prime examples among many.
Much of the LNG it now imports comes from the US – which, in response, is building three export terminals on its east coast. Australia, too, is positioning itself as a major LNG exporter and is upgrading its facilities – see the box on page 38. And whatever the eventual outcome of the Ukraine invasion, and whenever it might come, experts are united in forecasting that Europe will not return to a dependence on Russian gas afterwards and that Russia will seek instead markets in China.
This complete change in the gas market will require almost global changes in the infrastructure for export – and hence work for the lifting industry.
There is more. The pandemic had already thrown both supply and demand for the oil and gas industries into disarray. The Ukraine invasion compounded it. But despite both of those immense disruptors, and despite the astonishing rate of wind power and other renewable installations worldwide, fossil fuel demand and extraction of oil and gas is very much on the increase. It might not be good for the planet but it is happening… and at record rates.
GLOBAL DEMAND
The International Energy Agency’s Oil Market report for January 2023 finds global oil demand set to rise by 1.9 million barrels a day in 2023, to a record 101.7 million barrels per day.
Nearly half the gain is from China following the lifting of its Covid restrictions. And for those that imagine all oil flows from the Middle East, know that in 2022 the US overtook both Russia and Saudi Arabi as the world’s largest oil producer and now ranks as the world’s leading source of supply growth. Along with Canada, Brazil and Guyana, its annual production was a record for a second straight year. The US ended 2022 with a production of 11.9 million barrels of crude oil per day, 0.7 million barrels per day more than the previous year. These figures have allowed the US to become, for the first time in two decades, the world’s leading oil producer.
As if to reinforce that message, in March president Biden gave the go-ahead for the massive, controversial, and much-opposed Willow oil drilling project in Alaska.
So it is not just liquefied petroleum gas export infrastructure than needs cranes; the oil and gas extraction sector is also in business. Belgian headquartered crane rental services, heavy lifting, and engineered transport service provider Sarens reports that in order to meet the increase in supply and in demand the US energy sector needs to start a multitude of new extraction projects, especially in the state of Texas, which is responsible for approximately 42% of all domestic production. Sarens collaborates on a daily basis in the construction and maintenance of oil infrastructures and for years has led projects in the oil sector in the USA.
An example is the construction and improvement work carried out at the Corpus Christi refinery in Texas, carried out together with Kellogg, Brown and Root. In this project Sarens used a variety of its largest capacity cranes, including Liebherr LR1350S 385t crawler cranes transported from Australia, to lift and position the two hydrocracker reactors from the plant and 58 modules, essential to the operation of the plant. All operations were carried out while the facility was still in full operation. The project was completed on schedule.
Internationally, the company has carried out major projects in locations such as Angola, in the Norwegian sector of the North Sea, and in South Korea, where it is especially involved in the expansion of the Ulsan oil plant. For that project it created a custom-made gantry system for heavy lifts. The system is embedded in the client’s steel structure and is capable of a wide variety of lifts. The expansion of the plant was reflected in South Korea’s economy; it created more than 20,000 jobs and raised the country’s export power by 2.5 trillion won (US$ 2 billion) per year.
Netherlands-headquartered lifting and transportation specialist Mammoet can report similar success, this time in boosting a more traditional oil-producing economy. The Fujairah F3 power project will be the largest independent combined cycle power plant in the UAE. Located 300km northeast of Abu Dhabi, the 2.4GW plant is being developed as an Independent Power Plant (IPP) project, incorporating an efficient combined cycle technology, and it will make a crucial contribution to the country’s power generation sector.
TURBINE TRANSPORT
Mammoet was tasked with receiving, transporting, lifting and installation of components, including the three largestcapacity and most efficient gas turbines in the UAE. In total 105 powerplant components needed to be transported 23km from the Port of Fujairah in Abu Dhabi to the project site. All routes bar one passed on steep slopes through the mountains inland and so were too restrictive. The only viable route also presented a big challenge.
The route had an overhead bridge with a maximum clearance of 7.3m while some of the components, such as the gas turbines, needed a clearance of 7.5m – including the trailers. To allow the cargo to pass under the bridge Mammoet’s engineers loaded the turbines directly onto the trailers without the use of standard transport beams. This reduced the overall transportation height by approximately 30cm but meant the cargo could not be offloaded on stools for temporary storage and would need to be lifted off the trailers and installed directly upon arrival at the site.
The three turbines, each weighing 528 tonnes and measuring 13.6m long, 6.1m wide and 6m high, and their three gas turbine generators, each weighing up to 395t and measuring 11m long, 5.8m wide and 5.2m high, were delivered to the site, safely crossing beneath the bridge with around 10 cm to spare.
They were then lifted off the trailers and directly installed onto their foundations using Mammoet’s gantry.
Mammoet also used its 1,250t and two 400t crawler cranes for the installation of other components on the project, including 45 modules for a Heat Recovery Steam Generator (HRSG). Each module, weighing up to 338t, needed to be lifted out of its shipping frame before being installed inside the HRSG unit.
Located in Fujairah’s Qidfa area, between the existing Fujairah F1 and Fujairah F2 water and electricity plants, the Fujairah F3 will be able to power the equivalent of 380,000 households once operational. It will incorporate advanced ‘JAC’- class gas turbine technology and will utilise the most efficient combined cycle technology in the region.
MOBILE CRANE DEMAND
Saudi Arabia is, of course, a key player in the oil and gas field. Liebherr in December 2022 shipped no fewer than 18 of its mobile cranes to Saudi-owned Gulf Haulage Heavy Lift (GHHL).
The cranes are of up to 300t capacity and include six roughterrain cranes and 12 all-terrains. The new cranes will expand the Saudi Arabian crane and transport company’s fleet of cranes between 100 and 300 tonnes lifting capacity.
“The requirements in the Saudi market are growing and we are seeing a growing demand for mobile cranes especially in the class between 100 and 300 tonnes,” said GHHL chairman Hussein Ali Al Anazy.
The order GHHL placed with Liebherr comprises six LRT 1100- 2.1 rough terrain cranes, six LTM 1120-4.1 all terrain cranes, four LTM 1150-5.3 models and two LTM 1300-6.2 cranes.
Until now, GHHL’s primary focus has been on large and lattice boom cranes. “The mobile cranes we have ordered will expand our new class of cranes, which will complement our heavy-duty cranes and enable us to offer complete crane solutions for our customers,” says Sanjay Pachisia, CEO of GHHL. The group operates more than 90 cranes, the largest of them being a 750-tonne Liebherr LR 1750 crawler. They are used in infrastructure and construction projects, as well as in the traditional Saudi market for oil, gas and the petrochemical industry. In addition they are also used in the renewable energy sector.
In similar vein, Descon Engineering received last year four new Tadano GR rough terrain cranes for its branch in the United Arab Emirates. They are one GR- 800EX-3, one GR-500EX-3 and two Tadano GR-1000EX-4 units. Descon will use the new cranes on the site of its Gasco Habshan 5 gas processing plant.
Tadano’s presence in Algeria has also grown: long-time customer Sarl Meliah Makoudi Services recently took delivery of a GR-900EX-4 rough terrain crane. The company works with customers for a variety of handling and lifting jobs, currently managing a fleet of 11 cranes, six of which are from Tadano.
NORTH SEA SUCCESS
Moving to colder climates, Sparrows Group, the UK engineering and maintenance services specialist for the global energy and industrial sectors, is seeking to expand its service roster in the North Sea, to replicate there the drilling services success it has already had in the Middle East and Asia. To support its remarket entry Sparrows has recruited an experienced member to its team with the appointment of Sandy Main as drilling services manager – Europe. Main has more than 30 years’ experience in the drilling services sector and will be based at the company’s headquarters in Aberdeen, Scotland.
The appointment follows a contract worth approximately £50 million that Sparrows secured in the summer of 2022 with a major UK Continental Shelf operator to provide crane management services across its operating assets in the North Sea.
The five-year agreement, which also has two extension options each of two years, will see Sparrows deliver crane operations and maintenance services across ten of the operator’s assets in the region. Stewart Mitchell, chief executive officer at Sparrows, commented: “This new five-year contract is in addition to the inspection services work which we were awarded by the operator two years ago.”
It means that Sparrows will continue with the provision of operation, maintenance, and engineering services to ensure the safety and reliability of 38 cranes. The scope includes development and implementation of planned maintenance routines, as well as undertaking planning and risk assessment for all lifting operations.
All onshore support will be carried out from Sparrows’ Aberdeen headquarters, including technical and safety audits, and repair and refurbishment work as required.
“Although we have been diversifying into the renewables and onshore industrial markets in recent years the North Sea remains a core area in the business, so we’re pleased to continue working with the operator across these assets,” said Mitchell.
shut-down work down under
Grove all-terrains also are well represented in the oil and gas sector. Two more of them have joined antipodean fl eet operators Tutt Bryant Heavy Lift & Shift to work on a major Australian LNG plant turnaround. The project is at one of the world’s largest, most complex processing plants, the INPEX-operated Ichthys LNG facility near Darwin in Australia’s Northern Territory.
For the fi rst stage, the shut-down (which took place in 2021) Tutt Bryant sent a fl eet of eight mobile cranes mostly made up of Grove all-terrains in a mix of four-, fi ve- and six-axle machines: a GMK4090, two 100 GMK4100L-1 units, a 95t GMK5095, a 130t GMK5130-2, a 150t GMK5150L, and two 300t GMK6300L cranes. They covered multiple tasks with Manitowoc providing two on-site technicians to ensure maximum uptime. For the second stage, in 2022, the new cranes – a GMK6400 and a GMK5250XL-1 – provided added lifting power.
“We carefully selected this fleet to provide a good mix of capacities for maximum fl exibility, with their class-leading boom lengths providing optimised access to all areas of the plant,” said Rob West, senior divisional manager at Tutt Bryant. “We added the new models for extra capacity, fl eet refreshment, and to provide more versatility. The long-boom GMK5250XL-1 means it can take on work where we previously relied on larger cranes. We purchased the GMK6400 because we knew we could use it for some heavier tasks, but we also knew we’d get good utilisation from it in the future.”
Of particular value to the project was the Grove GMK5250XL-1, which launched in 2019. It offers the longest boom of any fi ve-axle crane, a 78.5m, eight-section Megaform boom, but this can be made longer still with an 8m extension or with an 11.2m or 17.8 m swingaway jib plus 8 m jib extension. All these options mean that 33.8 m of additional reach is possible. The crane can handle 9.9 t when the standard boom arrangement is at maximum height, or 1.3 t when at maximum working radius of 74m.
“The lifts we undertook on the turnaround are all well within the capabilities of the cranes,” said West. “But it was vital that work progressed smoothly as there were a lot of picks to perform so the plant could get back online as soon as possible. We’ve been really pleased with the reliability of the Grove cranes, as well as their speed, fl exibility, and manoeuvrability.”
Adding pressure on the cranes was the extreme heat and humidity of the area, plus a requirement for them to fi t the 24/7 work schedule. The cranes have air-conditioned cabs. If any issues arose one of the two Manitowoc technicians was on hand to offer support, keeping unexpected stoppages to a minimum. “I can’t speak highly enough of those technicians,” said West. “On the project there are no cell phones allowed. We expected this to cause some delays with service, but the Manitowoc guys have found solutions in minutes, rather than hours.”
MyCrane sources 400t crawler crane for Chinese refinery work
Dubai-base MyCrane describes itself as ‘a digital disruptor for the cranes and construction space.’ It was founded in 2021 and is in effect an on-line service that links crane users to crane renters: it is a digital site that allows users to post their lifting requirements free of charge online. Crane rental companies then respond directly with their commercial offers, eliminating the need for customers to make multiple offl ine requests and allowing them to save time.
Beijing-based Haihua Industry Group, involved in chemical industry products and equipment for the oil and energy sectors, made use of MyCrane’s online crane rental platform. Using the service Haihua was able to source a 400t crawler crane for use on three column installations at a refi nery. Critical lift was required at 28m radius and 77m height for the 22.8t column sections.
After receiving a range of easily comparable commercial offers, Haihua awarded the lifting contract to Sinopec Heavy Lifting and Transportation Co Ltd., who proposed a Sany crane, SCC4000A, in LJ confi guration (super lift). Assistance with the contract, preparation of engineered drawings, and client support up to safe execution were all provided by MyCrane.
Mycrane founder and CEO Andrei Geikalo, a former commercial director at Mammoet said, “In our initial discussions it became apparent that most contractors known to the client were unable to meet its requirements, particularly in relation to site space and budget constraints.
“Fortunately, the client was able to use our rental platform to quickly access a range of additional suppliers who were able to propose different options, and then award the project to their preferred contractor based on technical and commercial criteria.”
The client was able to select a crane already located in the same region as the job site, which MyCrane says generated savings of 30% compared to other quotes. The Mycrane service is operational in a number of key global markets, including the United Kingdom, United Arab Emirates, Qatar, Oman, India, Singapore, Thailand, Indonesia, Kazakhstan and Uzbekistan.
Liebherr ships two offshore cranes for a gas project in Azerbaijan
At the end of December 2022 Liebherr-MCCtec Rostock, the maritime sector of Liebherr, shipped two BOS 2600 and two BOS 4200 offshore cranes to the Umid Babek Operating Company (UBOC) in Azerbaijan. The delivery is for UBOC’s Umid-2 gas project in the South Caspian sea. The BOS 2600 cranes have a maximum lifting capacity of 45 tonnes; the BOS 4200 models can lift 50 tonnes. Both models have a lattice boom with a maximum outreach of 48 metres on the main hoist and 53 metres on the auxiliary hoist. They are electro-hydraulically driven and equipped with Liebherr Litronic, a control system for precise crane operation.
The four cranes were shipped end of 2022 by the cargo ship ‘E-ship 1’, which is equipped with two Liebherr ship cranes and, unusually, four Flettner rotorsails. These are vertical rotating cylinders which generate propulsive air pressure akin to a ship’s sails, and greatly reduce fuel consumption and hence emissions.