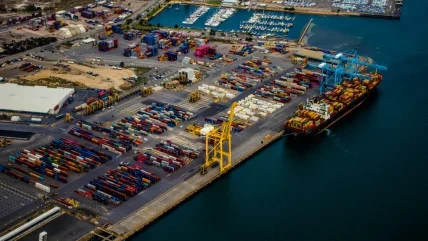
Elsewhere in this issue we have highlighted how the quest for cleaner energy is driving the heavy transport sector to handle evergreater, ever-larger loads. The same trend can be seen in the dockside industry. Standard machinery is becoming greener, and ports, cranes and vessels are adapting to the increasingly challenging size and scope of offshore wind installations. The towers and turbines of seabed offshore windfarms we have seen so far are awe-inspiring; but a new generation of floating windfarms promises to be several times larger and more efficient – and a lot further from shore. They need deeper ports, larger loading and assembly machinery, with more carefully controlled load positioning and rigging. Hence Mammoet’s justified pride in its installations and operations at Gulen harbour on the west coast of Norway on what will be the world’s largest floating windfarm – see the box opposite
Offshore is always demanding. Even getting operatives and service personnel on to a tower or nacelle has difficulties and dangers hardly changed from the days of Victorian lighthouse keepers who could on occasion be stranded at their rocky outposts for weeks on end, relief boats being unable to get close enough to their wave-swept islets even for an exchange of personnel.
To address the problem, and to save maintenance staff from the hazardous leap from swaying transfer vessel to small metal platform at the base of offshore towers Cargotec has introduced a movement-compensated walkway for support ships (see box below).
That piece of ingenuity may be helpful rather than gamechanging; greening developments, however, are major pointers for the future. The move away from diesel is gathering pace; and ports and docksides are pioneers here. Thus, for container ports, US material handling equipment manufacturer Hyster has announced a 100% battery-powered empty container handler. Destined for the CARU depot in Rotterdam, The Netherlands, the handler will be powered by 650-volt lithium-ion batteries, with electricity sourced from solar panels on site at the CARU depot.
In 2021 more than 95% of CARU Container’s Scope 1 CO2 emissions came from its diesel forklifts and empty container handlers. The electric handler can therefore help the company to significantly reduce its greenhouse gas emissions while helping to reduce its operational expenditure since its diesel costs are, of course eliminated, and most of its electricity costs are covered by the capital in the solar panels.
“As a global market leader in container trade, we are keen to integrate sustainability into our entire value chain as we are striving to be net zero before 2030,” said Thirza Belder, sustainability officer for CARU Containers. “Therefore, we started discussions with Hyster in 2021 to provide electric lift trucks and equipment for our depot, which later led to the electric empty container handler.”
CARU already possesses a 240 kilowatt-hour capacity battery that can store enough energy to charge the empty container handler for most of the year. It will be supplemented with grid power when solar energy is less efficient during shorter winter days. This solution is expected to supply enough charge to allow the truck to complete five to six required hours of work during a shift before being recharged overnight. CARU has installed measuring devices throughout the site to calculate what percentage of the energy used comes from solar.
“This is a great application for a fully electric vehicle on a site that produces its own electricity,” says Jan Willem van den Brand, director, Global Business Development Big Trucks, Hyster. “The fully electric empty container handler we are supplying to CARU follows years of research and development into sustainable technologies for the port and container handling industry.”
This is the latest in a series of developments from Hyster at the forefront of electrifying higher-capacity port equipment. Traditionally such equipment has relied on internal combustion.
Hyster is also providing an empty container handler powered by hydrogen fuel cells, another advanced electric power technology, at a terminal in Hamburg, Germany.
In addition, the company is currently testing the first-ever real-world pilot of a hydrogen fuel cell-powered container handler, at the Port of Los Angeles, and has previously announced a pilot of a fuel-cell powered ReachStacker at the Port of Valencia and a partnership with Capacity Trucks to develop electric and hydrogen powered terminal tractors. Hyster draws on extensive experience in electric truck design with its line of smaller industrial trucks, for which Hyster offers extensive battery electric and hydrogen fuel cell power options.
“For some operations, lithium-ion power might be the answer, but for others, hydrogen is the right choice,” says van den Brand. “The answer depends on so many factors like duty cycle, utility grid capacity and fuel availability. Our customers deserve choices that allow them to build the right solution based on their needs – not shoehorning a single technology into their operation.”
The electric empty container handler at the CARU depot is expected to operate for approximately 2,000 hours per year. It is an electric equivalent to the Hyster H10XD-ECD8 doublecontainer handler, which can create stacks of up to eight containers high while handling two at a time. This design approach offers a level of familiarity for operators who have experience with other Hyster big trucks, as well as helping to control the cost of design, manufacturing, service and maintenance.
SUSTAINABLE STEEL
On a similar note, Kalmar has introduced what it claims to be the world’s most sustainable reachstacker. It is electric-powered, of course, but Kalmar customers now have the option of having their electric reachstacker constructed with 47% SSAB Zero steel – which is made from recycled steel and produced using fossil-free electricity and biogas. Kalmar and SSAB announced their partnership to bring SSAB Zero to the cargo and loadhandling industry in May this year.
In addition to SSAB Zero steel, customers have the option to replace standard fossil-based oil with PANOLIN biodegradable hydraulic oil, and to extend tyre lifetime through eco driver training – gentler accelerations apparently work wonders in reducing wear – and a tyre pressure monitoring system. Even the counterweight can be made more eco-friendly: Kalmar is introducing a new emission-reducing one made from unprocessed naturally heavy material to replace the standard cast-iron.
Kalmar’s electric reachstacker We mentioned above that CARU in Rotterdam is powering its new equipment from its own array of solar panels. It is an indicator of the fact that electrification is not a piecemeal business. The entire infrastructure of the dockside needs to be integrated to reflect the power requirements of its machinery – and the advance of automation makes the case even stronger. To ease this transition to the all-electric port Kalmar, in June, announced the launch of its ‘Electric Straddle Carrier Charge Family.’
Straddle carriers and smaller cargo handling equipment, such as reachstackers and forklifts, with their various lifting capacities and operating patterns, all need charging. The Charge Family is aimed at optimising the process so that no operation is delayed through a flat battery on a particular vehicle. The family includes battery technologies, charging solutions and software to support operators of both manual and automated terminals with their transition towards decarbonised operations.
Within it are two electric straddle carrier options: one with a highenergy battery capable of up to four hours of continuous operation with a charging time of 45–50 minutes; the other with a high-power battery (previously known as the Kalmar FastCharge straddle carrier) capable of only 50 minutes of continuous operation but with a very much faster charging time of five to six minutes using FastCharge technology.
Two different charging options are available: a standard CCS charging interface compatible with any commercial charging station; or the optional FastCharge technology where the onboard battery is charged via a pantograph.
SOFTWARE SOLUTIONS
Also in the family is Charge Optimiser software which automatically assigns charging tasks to the operator to avoid queues at the charging stations and the Kalmar One Fleet Optimiser software for AutoStrads, which handles job scheduling and dispatching, including assigning charging tasks to equipment. The Kalmar Insight Energy Module provides visibility over battery charging status, energy utilisation and charging KPIs.
“The Charge Family is a comprehensive suite of solutions that enables terminals to transition to fully electric straddle operations quickly and smoothly,” says Arto Keskinen, Kalmar’s senior vice president for Horizontal Transportation. “We have developed this offering in close cooperation with our vast customer base. The feedback from our customers has shown us that there is not only a need for alternative charging solutions but also for supporting software solutions that allow them to make efficient use of their electrified equipment and to identify areas for improvement through monitoring and data analysis. The Electric Straddle Carrier Charge Family allows our customers to choose the path to electrification that best fits their operational and strategic business needs.”
It is clear electrification is here to stay and it is, perhaps, at its most interesting stage of development: that point where the technology moves from the possible but unwieldy and niche towards the easy-to-use, widespread, commercial standard.
Historians of technology tell us that this is the stage at which many and widely-varied new designs evolve towards the most efficient ones that are best suited to their purpose. The designers and engineers who make all this possible generally receive little public recognition or praise; which is regrettable. It is easy to talk green, and to wish for a more sustainable planet. To actually help to make it happen calls for ingenuity, and hard work, and the investment of money and resources- and sometimes to take risks – to make the changes happen. This is happening in docks around the world right now.
Mammoet assembles world's largest floating wind farm
Floating wind turbines are mounted on very deep-draught spar buoys. A smooth production line is needed from component load-in to turbine assembly but the deep draught requires high lift capacity far from the quay edge.
Floating offshore wind will be key to delivering cheap renewable energy worldwide. The largest floating wind farm to date is Hywind Tampen, currently under construction in the Norwegian North Sea. Energy major Equinor is the project’s operator: taken together, Hywind Tampen and Equinor’s earlier Hywind Scotland pilot project will generate around half of the world’s fl oating wind power.
Water depth and seabed geology in the Tampen area make it impossible to install conventional fixed-bottom turbines, so floating foundations were required. The fl oating wind market is still developing, and although various component designs, installation techniques and deployment methods are being considered and prototyped, none have been commercialised at full scale.
A critical challenge at Tampen is the work involved in assembling the entire 8.6 MW turbines – including tower sections, nacelles and blades – onto huge 107m spar buoys that lie mainly underwater. This needs to be performed in the controlled environment of a port – where the whole system could be kept as static as possible – before the completed turbines are towed out to their installation site.
With such huge floating foundations, the port requires an exceptionally large draught – ruling out jack-up vessels, whose legs would be too short to assemble the turbine sections. Also, though conditions at the site of the work, Gulen Industrial Harbour, were calm, using crane vessels would require transfer of the loads between two fl oating objects, which would increase the complexity of assembly engineering. This could, in turn, delay the integration phase and lengthen the offshore installation campaign, increasing project costs.
A spacer barge between the quay and spar foundation was needed to ensure adequate clearance between the base of the foundation and the seabed. Turbine components would therefore need to be lifted over the quay edge, over the spacer barge, then onto the foundations themselves – a distance of around 143m.
Following its experience during the deployment of the world’s fi rst fl oating wind farm, Hywind Scotland (also operated by Equinor), Mammoet was engaged to undertake turbine assembly and associated port handling work.
Martin Tieman, project manager for Mammoet, explains: “We recognised that we would need a crane with a huge outreach to make the required lifts. The majority of land-based cranes in any fl eet would not be able to achieve a 143m distance at these weights, but we knew that if it could be done the project would benefit signifi cantly. This would create a smooth production line from marshalling yard to turbine assembly to commissioning – all at the same location – optimising the use of offshore assets.
“This led us to look at the use of our PTC 200-DS ring crane, which is proving to be in high demand for big sea-bed offshore wind projects such as the Greater Changhua development in Taiwan and Seagreen Offshore Wind Farm in Scotland.
“The port confirmed that the quayside would be able to provide the required ground bearing pressures, so we were able to put together a plan that would deliver a comprehensive package of port handling and assembly of all eleven turbines of Equinor’s development.”
In addition to the draught of the port, weather conditions also posed a challenge. Although large ring cranes are built to withstand strong gusts, components such as these – with a large surface area designed specifically to catch the wind – are another matter.
To counteract this the PTC 200-DS was modifi ed to ensure precise control of components even when winds were strong – meaning that there would be fewer potential stoppages due to the weather and the turbines could be completed sooner.
These modifications allowed the crane to work with third-party blade yoke and tugger winch systems, which orient the load under hook without the need for taglines operated by hand. This prevents damage to relatively delicate turbine blades, and increases levels of safety on site.
Besides lifting, strong port handling capabilities were required to receive tower pieces, nacelles and blades from vessels and store them so they could be retrieved quickly, maximising utilisation. Mammoet managed this scope, assuring the main lifting asset was in use for as much time as possible.
Alongside the PTC 200-DS, 24 axle lines of SPMT and a range of smaller cranes were used to handle the movement of components; an LR1750 crane assisted the PTC during lifts that required rotation of components. This further helped to keep idle time as low as possible for all assets, minimising handling manoeuvres overall.
“Having worked on numerous large-scale offshore wind projects, we understand how important the logistics between port delivery and installation are to maintaining schedule” says Tieman. “Our specialist team has successfully executed this scope for some of the biggest offshore wind projects in the world, giving us the experience to maximise utilisation of key assets and so deliver the highest levels of project cost-e¢ ciency.”
Hywind Tampen offshore wind park started producing power during the third quarter of 2022.
Walk to Work at sea
MacGregor, part of Cargotec, has received a contract from wind-farm operators Edda Wind for more units of its Horizon walkto- work technology. Horizon is a gangway, mounted on a support vessel, which has all-electric active motion compensation; in other words, it joins ship to tower with a level, smooth and hardly-moving bridge that is fully enclosed against the weather. It has, says MacGregor, an industry-leading internal clear width, and can have integrated personnel elevators and good elevators as options. The purpose is to increase the speed, safety and e? ciency of offshore wind maintenance operations.
Its safety and efficiency are enhanced by an augmented reality operator station (AROS), which also increases logistics support by allowing a single operator to seamlessly change between crane and gangway operation from a centralised control station on the vessel's bridge. The system is also interconnected to a Colibri 5 tonne 3D motion compensated crane, whose design is distinguished by its agility in compensating loads in 3D mode.