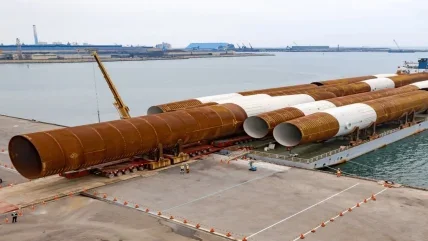
Renewables are gathering pace. New wind farms, on and offshore, are being installed. It used to be a difficult, challenging, slow business. It is still difficult and challenging… but it is no longer slow. Speed has become a priority. There is an urgency both for supplying clean energy – accelerated not only by the Ukrainian crisis and sudden cessation of Russian energy supplies to Europe but by the need to achieve carbon net zero as rapidly as possible in order to keep climate change within any form of achievable targets. So methods that speed installation are at a premium and efforts to devise them are intensive.
As an example of the scale and pace of offshore installation, Dutch maritime company Van Oord has just successfully installed the last of 70 monopile for the Hollandse Kust Noord wind farm. The farm is 18.5 kilometres off the coast of the Netherlands and is being built and run by Crosswind, a joint venture between Shell and Enerco.
When finished it will have a total installed capacity of 759 MW, generating at least 3.3 TWh of renewable energy per year – which is enough to meet nearly 3% of the Netherlands’ electricity demand.
The first monopile was installed in mid-October 2022 and it has taken just five months to install all 70 – and that was despite strong winds and cold weather. “The installation of the monopiles was an immense operation, with the monopiles weighing between 788t and 960t each,” said Wybren de Vries of CrossWind.
Van Oord engaged DEME, a specialist in the dredging, land reclamation, marine infrastructure, offshore energy and environmental remediation sector, to deploy the jack-up vessel Innovation to install the monopiles. Van Oord’s offshore installation vessel MPI Resolution is currently installing secondary steel to complete the foundations. The sets consist of boat landings, main access platforms (with davit cranes) and internal platforms. The platforms will be used for maintenance activities once the wind farm is operational.
In March, the cable-laying vessel Nexus began installing the cables for the project.
FURTHER WIND FARMS
Europe, the North Sea in particular, has been at the forefront of offshore wind. Northern Europe already has 40 offshore wind farms in operation and another 40 will be installed in the coming 10 years.
This year the Crown Estate, the controlling authority for the UK seabed, is issuing leasing rounds for up to 4 GW of electrical energy from floating offshore wind to be deployed by 2035, with a follow on 20GW anticipated by 2045.
Progress in Asia has been similarly rapid and the USA is catching up. Mammoet has secured contracts for two large offshore wind projects in the United States – both of which begin in 2023. Together, the contracts cover a range of port scopes, including the load-in, load-out, handling and temporary storage of XXL monopiles (XXL being the current largest size, at up to 100m high and 1,200t weight), plus the pre-assembly of turbines in a US marshalling port.
“Offshore wind in the United States has been a long time coming,” said Rick Bohne, Jr., director of sales & marketing for Mammoet in the USA and Mexico. “Our Mammoet colleagues have been executing these projects globally for some time so this is an exciting opportunity to leverage the combination of our technical experience with our local market experience.”
Mammoet’s recent offshore wind projects include the load-in, load-out and transport of jacket structures for Seagreen Offshore Wind Farm in Scotland, and component handling, storage, transport and crane lifting to assemble Hywind Tampen in the Norwegian North Sea, the world’s largest floating wind farm.
Mammoet is also supplying onshore heavy lifting and transport for the staging and assembly of turbine components for Dogger Bank Wind Farm in the UK, and onshore heavy lifting of turbine components in France.
SPEED AND SIZE
Liebherr is also focussing on speed and size. Its heavy lift crane HLC 295000 is the largest, and the most powerful, crane the company has ever produced and it has been designed for offshore wind installation.
It has a lifting capacity of up to 5,000 tonnes and a maximum lifting height of 175 metres above deck. It is installed on the specialist vessel Orion and has successfully completed its first offshore projects by lifting a substation platform and installing the largest monopiles ever produced in Europe.
The tasks were performed in the Baltic and the Channel. At the Arcadis Ost wind farm, in the German Baltic Sea, the HLC 295000 was used to install 28 monopile foundations – each up to 110 metres long and weighing up to 2,100 tonnes.
A few weeks later vessel and crane set down the 1,300 tonne jacket foundation onto a prepared seabed site for the French Fecamp farm off the Normandy coast and then installed a transformer platform weighing 2,200 tonnes on the foundation. It was particularly important not to lose sight of the tight schedule in the weather conditions off Normandy – where the Channel and the Atlantic meet; the Orion’s good dynamic positional system and the highprecision control of the HLC 295000 were vital here.
The Orion is unique in that it has ability to install monopiles while it is floating. This means that no time-consuming jackup process, raising the ship on legs up out of the water, is necessary as has been the case up to now. Jack-up vessels have been a requirement for monopile installation; now, it seems, that is no longer the case.
“Our initial experience indicates that the installation times of previous vessels of about 3 to 3.5 days per monopile can be significantly reduced to about 0.9 to one day per monopile with the use of the Orion and our HLC295000,” says Robert Pitschmann, global application manager at Liebherr-MCCtec Rostock.
The HLC series, and the expansion of the heavy-duty crane range, are firmly anchored in Liebherr’s strategy not least because of the energy transition and the increase in numbers and size of offshore wind turbines this is bringing. For the construction of these modern wind turbines the lifting height of the HLC 295000 is a decisive factor. There is also, as a by product of increased renewables, a trend towards decommissioning disused offshore oil and gas platforms. This involves dismantling large and heavy parts on the open sea – which again is an important task for which Liebherr’s HLC series is well suited thanks to its huge lifting capacities. In dismantling the old and building up the new energy, Liebherr point out that the HLC series is involved ‘at both ends’ of the transition.
Two new methods for North Sea lift by mammoet, SHL and dockwise
Cyprus-based Seaway Heavy Lifting (SHL), an independent offshore installation contractor with experience in the transport, installation and removal of offshore oil and gas platforms, subsea structures and the installation of wind turbine foundations, worked with Mammoet and maritime service provider Dockwise to perform an unusual North Sea lifting operation for Siemens which involved two revolutionary techniques.
The task was to install the SylWin alpha converter platform, which will act as a giant ‘power socket’ for the DanTysk, Sandbank and Butendiek wind farms off the German and Danish coasts of the North Sea. Together the farms consist of 240 wind turbines and represent a generating capacity of 864 megawatts. The platform transforms the alternating current generated by the wind turbines into direct current that is transported by a 160km long seabed cable and 45km of underground cable to the onshore Büttel high-voltage station, where it connects to the German national grid.
The converter platform is 83m long, 56m wide and 26m high and weighs 14,000 tonnes; built by Siemens it is the largest ever installed in the North Sea.
As it exceeds the lifting capacity of fl oating cranes, the ‘float-over method’ was used to move it from a pontoon onto the already installed jacket or base of the platform. This approach has been used successfully in the Gulf of Mexico and in the Far East, but this was the fi rst time the method has been used in the North Sea. The platform was fl oated out to the jacket on its pontoon and was positioned over and between the jacket’s legs. It was installed onto the legs of the jacket by ballasting the pontoon, thus lowering the platform. Dockwise was responsible for this phase.
The second new procedure was devised by Mammoet. It used strand jacks to lift the platform 15 metres up onto its fi nal position on the jacket. The use of strand jacks is not unusual but Mammoet devised a time-saving method, customised for this project, that allowed much faster removal of the strand jacks after the lift. In a revolutionary move, Mammoet reversed the normal positions of the lifting equipment to raise the platform. As a result, installation time at sea was reduced by 30 days.
Converter platforms are designed to be lifted at sea after installation on the jacket. Each of the six platform legs has a jacking house built around it at deck level. The conventional method for the installation of converter platforms is to mount strand jacks at the jacking house and anchor blocks on top of the platform leg.
The jacking house is a small space, which makes installing a 4500kg strand jack complicated work. A similar problem occurs during disassembly. Removal of the strand jacks from the jacking houses involves rigging the anchor block, removing the wires and the anchor block, and fi nally removing the strand jack itself. Given that no fewer than 44 stand jacks were used on the lift, the procedure would have taken around 50 days.
But Mammoet invented a way to install the system, which basically meant turning it on its head. Mammoet installed the strand jacks on top of the platform legs instead of on the jacking house, using special constructions called strand reel frames that were designed especially for this project.
The reel frames were constructed so that the wires would wind back up on the reel while pulling up the platform, eliminating the need for time-consuming wire removal. In turn, the anchor blocks were installed at the jacking house.
To remove the jacks Mammoet simply lifted the anchor blocks onto a pallet truck and rolled them in and out of the jacking houses. Since the anchor blocks weighed just 600-800kg apiece this presented few problems. The Mammoet method made it possible to remove the strand jacks straight after the lifting operation, without having to remove the wires from the unit first.
With the new method, it took just ten days to complete the operation at sea. Lifting only took one day, and removal of the equipment was just eight, making it possible for the platform to be commissioned a month early.
Tugdock develops new lifting technology for offshore wind
The speed of offshore seabed wind installations has revealed a forthcoming problem: a lack of places to put them. Most of the suitable sites – of shallow seas, close to shore – have wind farms on them already or have been earmarked for them; yet the need for more capacity remains.
The solution is fl oating farms which, anchored by cables to the seabed, can be placed in deeper waters further from shore. As an added advantage winds are stronger and more consistent in these locations.
Floating wind farms, however, present other logistical problems: the towers, and in particular the fl oats that support them, are immense – so large, in fact, that most harbours cannot handle them.
In February a UK startup company by the name of Tugdock, located in Cornwall, announced a partnership with Sarens to offer a novel solution. Lucas Lowe-Houghton, director of business development for Tugdock, explains: “The fl oating offshore wind sector is expected to continue to grow rapidly. However, very few of the world’s ports have suffi cient water depth and assembly quay space to build the huge turbine fl oaters required, and conventional dry docks are not wide enough as they were originally designed for ships.”
Tugdock’s patented marine buoyancy bag technology solves this issue. “It has been designed to help ports play a bigger role in fl oating offshore wind turbine assembly. It allows fl oating dry docks to be delivered by road in modular form and assembled at the port to dimensions far wider than most of the world’s existing dry docks. The fl oating platform is then towed to deeper water for launching of the turbines. Our submersible fl oating dry docks can operate with as little as fi ve metres draft, enabling more effi cient wind turbine fl oater construction.”
This technology can greatly increase the capacity of docks such as Pembroke Port, in Wales; a £60 million project is underway to adapt infrastructure there to accommodate the growing number of renewables developers who are seeking to base themselves there due to its proximity to the Celtic Sea, which has some of the best wind resources in Europe.
Simulations are under way of the processes of manoeuvring large fl oating wind turbines into, and out from, Pembroke Port using the Tugdock technology. These will give a detailed understanding of the sequence of events that need to take place to successfully complete these phases of turbine recovery and deployment and help steer future planning for the port.
“More than 8% of the total cost of a fl oating offshore wind farm is accounted for by assembly and installation” says Lucas. “So any innovation that allows this process to be carried out more effi ciently and quickly will have a big impact on profi tability for developers.”
Carl Sarens, director of global operations, technical solutions and engineering at Sarens, said: “Through this partnership with Tugdock we are able to streamline the solution we offer to developers. By signifi cantly reducing time and costs our alliance will deliver a step change for wind turbine construction. In addition, Tugdock’s fl exibility and reusability is useful to global developers as the units can be reused from one port or project to another regardless of changes in turbine size or foundation weight.”