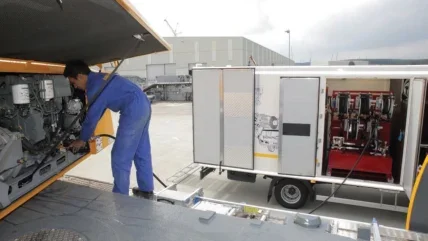
Like many industries, the crane sector is facing a skills gap. In particular, good service engineers and technicians are hard to find, although some crane rental companies are managing better than others. In many cases these companies are turning to the OEM for service and repair, or to third-party repair and refurbishment specialists.
Crowland Cranes is the UK’s largest independent service and repair provider. It is picking up more repair work from crane hire companies who used to do it themselves. “There are a lot of great crane hire companies out there who have excellent workshops,” says Pete Issitt, owner and managing director. “The challenge across the whole industry is finding good people to staff them – and holding onto those people.
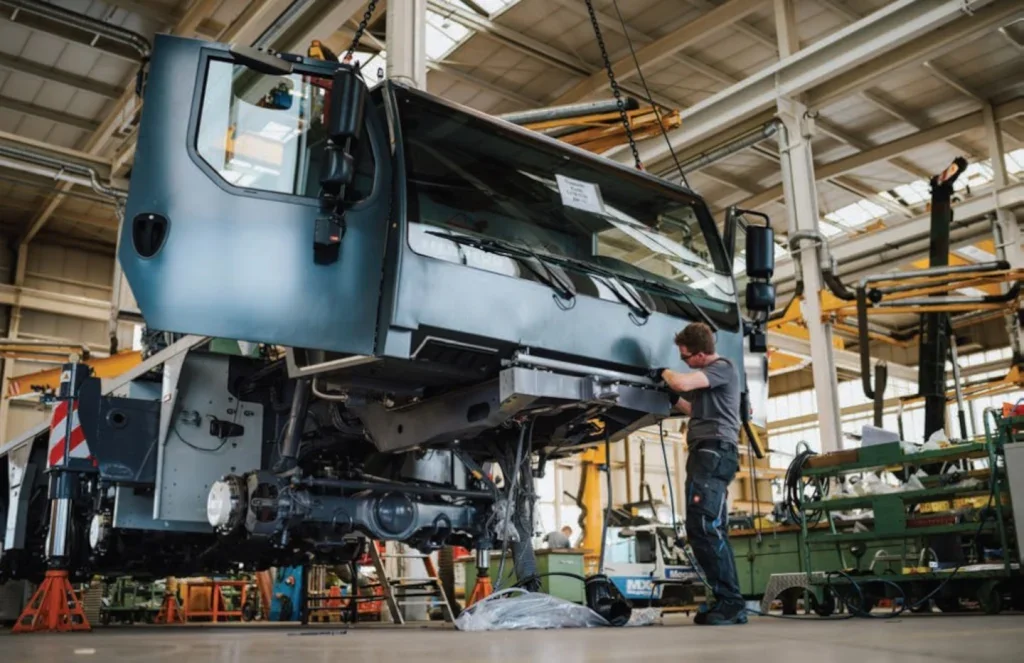
“These companies increasingly rely on us to fill that gap. This is also impacting the OEMs. Because their customers don’t have the skills in house, the OEMs are having to send out technicians to do simple jobs like oil changes.
“Their service and maintenance workload is growing, which impacts their ability to deal with breakdowns as an engineer can’t be in two places at once.”
However, part of Crowland’s growth can be attributed to Pete’s promotion of collaboration rather than competition. “We work with all the major OEMs; they all make use of our facilities in some form or function. We paint cranes for some of them and fabricate for others. Technically we do compete against them for repair and refurbishment work, but in my view, there is plenty of work out there for all of us.”
MARKET ADVANTAGE
Pete believes that Crowland’s unique position in the UK marketplace means it can offer a better service to the crane industry. “In many cases, we can be a lot more fluid and responsive than the manufacturer,” he says.
“We are not a massive corporation, so we can make decisions straight away. For example, some OEM parts can have quite long lead times. We can fabricate the steel parts we need like panel work, which speeds up the process for the customer. We prefer to fit an OEM’s deck panel or cover where we can. However, if the manufacturer is quoting a three-month lead time, that’s no good for our customer. So, we make them one instead.
“We have the capabilities to do about 95 percent of it all in house. Pretty much the only thing we can’t make is the specialist hydraulic cylinders. Having this level of control over the entire process means we can quote realistic and accurate lead times.”
INSURANCE BUSINESS
Based in Peterborough, Crowland is an authorised service partner for Dutch mobile crane manufacturer, Spierings. It is also the UK insurance industry’s only approved repair centre.
“Over the years we have always stayed loyal to the insurance industry, and they have responded in kind,” says Pete. “Because of our focus on developing longterm relationships, today about 80 percent of the UK’s insurance business comes through our doors. You can’t ever precisely plan your workload in this business, but the accident repairs from the insurance side ensures we have a steady flow of work.”
In addition, the company is carrying out a major refurbishment contract for the Ministry of Defence, overhauling the army’s crane fleet as part of its service life extension programme (SLEP).
It is also a supplier to major contractors on the HS2 project, fabricating equipment such as lifting beams and outrigger pads.
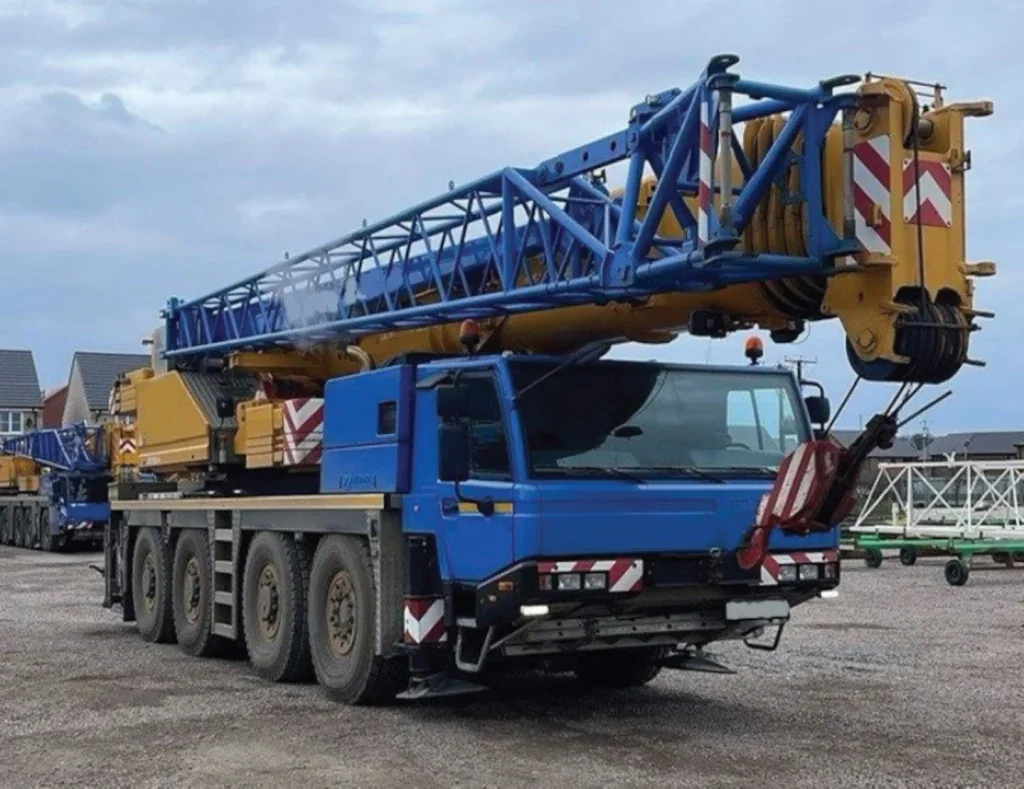
However, reputations can be lost much quicker than they are won. “The challenge as an independent is that the last job always has to be your best job,” says Pete. “And we are unique in that we sit in between the insurer and the crane owner. Both are our customers so that can be a delicate negotiation at times. You have to be sensitive to the needs of the crane owner while also meeting the insurance company’s requirements. We’re often walking a fine line.”
MAXIMISED UPTIME
OEMs are also investing heavily in service and repair. “Cranes are highly complex machines,” says Vincent Stenger, manager customer support development at Tadano Europe. “While owners can handle some basic service tasks, the majority of repairs – especially those involving structural components, hydraulic systems, or electronic controls – require specialised expertise.
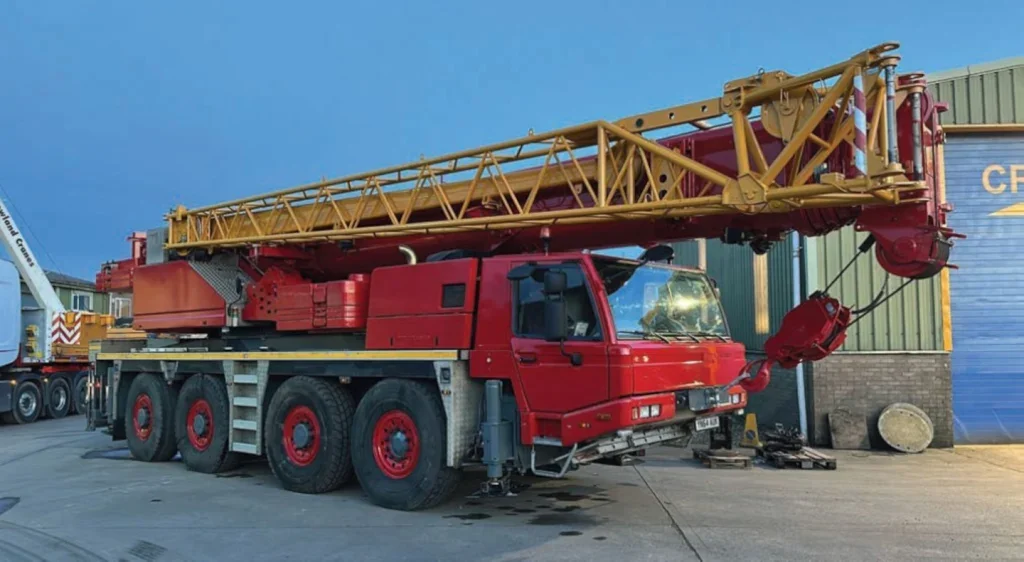
“Many customers who traditionally maintained their own workshops now face difficulties in recruiting skilled technicians. This challenge is exacerbated by the retirement of experienced mechanics, making it harder for crane owners to sustain in-house service capabilities. As a result, we anticipate that OEM support will become even more critical in the coming years.
“Our role as a manufacturer extends beyond repairs – we provide knowledge, training, and direct technical support to ensure that customers can operate their cranes safely and efficiently.”
Tadano’s provision includes service and maintenance, accident repairs – including structural repairs – and crane refurbishment.
“Our expertise as an OEM allows us to perform these services with unparalleled precision, backed by engineering data, manufacturing insights, and direct access to highquality spare parts,” says Stenger.
Tadano lists five key benefits of choosing an OEM for repair and refurbishment. Guaranteed compliance means that OEM repairs maintain the crane’s certification and compliance with safety regulations, avoiding legal and operational risks. The customer also gains access to proprietary expertise, as only the OEM has the complete engineering data, material specifications, and calibration knowledge necessary for high-precision repairs.
Crane owners can also benefit from higher residual values. “Cranes serviced by the OEM retain their value better than those repaired with non-OEM parts or methods,” adds Vincent.
The final two benefits are warranty protection and risk mitigation. “Non-OEM repairs can void warranties, whereas Tadano’s repairs ensure continued coverage,” says Stenger. “Unauthorised repairs can introduce safety hazards, lead to structural weaknesses, and even result in accidents or machine failures.
“There is no substitute for an OEM repair. Tadano’s service network ensures that every repair is performed with precision, using original parts, manufacturerapproved methods, and certified technicians.”
For Liebherr, it is about ensuring the highest possible uptime for its customers. Harald Hummel is head of customer service for what Liebherr defines as Region 1. This includes its heartland of Germany along with Austria, Switzerland, Italy, Benelux, Ireland, and the UK.
“Our goal is always to ensure that we maximise uptime for our customers,” he says. “Aftersales service is incredibly important to our customers. We know that if we can deliver the best possible service, this is the best reason for the customer to come back.
“We are the market leaders in Europe and North America, and one reason for our success is the quality of our support. My philosophy is to focus on my own job and ensure that we are the best we can be, so we don’t worry too much about what our competitors are doing. However, customers often tell us that our service and repair are first class, which is very pleasing to know.
“Mobile and crawler cranes are deployed on construction sites to carry out important lifts. Very often, if this lift cannot go ahead then all work on the site comes to a halt. So, a rapid response is essential for our customers. This is why we invest so significantly in supporting our customers. Globally we have hundreds of personnel, doing service on cranes.
TRAINING INVESTMENT
One of the building blocks is good technical knowledge, which comes from continuous training.
“Every service technician spends about three weeks of each year in training, typically at our training centre,” says Hummel. “This gives us a big advantage as we are constantly upskilling our workforce. We have the most experience with our own products, which is very difficult for a third party to replicate. And the foundation for this is our investment in training.
“Everyone knows that there are skills shortages, and some companies are struggling to find good people in technical service roles. They rely increasingly on us as the manufacturer to solve their problems. We still have customers who have excellent technical teams and can deal with a lot of issues by themselves. For those customers it is more about ensuring we have fast delivery of the parts they need.
“However, we also have other customers who rely on us for the full solution including regular service and maintenance of their cranes. For example, we have mobile service vans in Germany that are equipped with all the oils they need to carry out a full oil change on a crane.
“Similarly, many crane companies do not want to invest in full workshop facilities, whereas we have high quality workshops capable of full repair and refurbishment. We even have the capabilities to repair booms that have experienced impact damage.
“Liebherr is also the biggest used crane dealer in the world. Of course, many of our customers trade in their old crane when they buy a new model from us. We are selling 250 to 300 used cranes per year. We need world-class repair and refurbishment capabilities to support this business and ensure we provide used cranes in excellent condition.”
TECHNOLOGY’S ROLE
Technology increasingly plays a big part in supporting faster resolution of issues. “This can be as straightforward as the customer calling us on their mobile phone and showing us the problem on the phone camera,” says Hummel. “And we also have remote diagnostics so we can often connect directly to the crane.”
Liebherr offers all its cranes with a data modem and SIM card, with five years of data included. “This is absolutely helping to increase uptime,” says Harald. “Of course, the crane operator could instead send us the error code by email or phone. But the advantage of being able to dial into a machine is that we can ask the operator to activate certain functions of the crane and view in real time how it is working.
“We can identify the issue before we send out an engineer, and we can ensure that the engineer has the right parts when they arrive. This undoubtedly gives us a better first-time fix rate, meaning uptime has increased.”
Liebherr is also pioneering the use of augmented reality (AR) technology in its repair centre. “With AR we can more quickly and accurately identify areas of damage, for example,” says Harald. “We have trialled this and will explore opportunities to roll it out as it has proved very useful, particularly with identifying impact damage and when the chassis has distorted.
“Cameras are also proving to be very useful. During covid we had a customer in Japan using a camera on a helmet. This enabled us to advise them in real time how to repair a crane 10,000km away from us.
“In the future I think this technology will become more prevalent. The ability for us to see what the operator or the technician sees is very powerful. Already I know of many cases where using a camera has ensured a very fast resolution to a problem, particularly when we receive out of hours calls.”
Tadano is also witnessing the positive impacts of new technologies. “Technology is transforming crane maintenance and repair, making diagnostics faster, service interventions more efficient, and customer support more interactive,” says Vincent.
Tadano is employing AI powered diagnostics to analyse error codes. “Operators receive immediate troubleshooting guidance, reducing downtime and enabling faster first-time fix rates,” says Vincent.
In addition, new software can automatically recognise and identify spare parts within an assembly, making buying replacement parts quicker and more accurate. And it is also looking into augmented reality (AR). “Future developments include interactive service tools such as voice-guided troubleshooting and smart glasses, allowing technicians to receive real-time support from expert engineers,” adds Vincent.
“Over time, we expect a growing proportion of issues to be diagnosed and resolved remotely, reducing the need for on-site interventions and minimising machine downtime. While some of these technologies are still emerging, they represent the future of crane servicing — faster, smarter, and more efficient maintenance solutions that benefit both owners and operators.”
GLOW-UP FOR 50-YEAR-OLD GROVE

A rough terrain crane in Kenya will mark its 50th birthday looking as good as the day it was built – and performing even better.
Cranes are renowned for their long working life, but 50 years is still an exceptional achievement.
The Grove RT75S rough terrain crane has been in service since 1975, and is currently deployed in Malindi, Kenya. The crane is owned by a multinational organisation that gathers and transmits satellite messages and works at a remote facility near the equator.
The owners wanted to give the crane a new lease of life, so they turned to Manitowoc’s local dealer, Ports & Harbours Support Services, a logistics and equipment company based in nearby Mombasa.
Glyn Cross, the sales and marketing director of Ports & Harbours, led the team in evaluating the crane before any work started. Through their detective work they discovered that the machine had been manufactured at the Shady Grove factory in Pennsylvania, U.S., back in 1975. But unfortunately, there were no records available to help – no manuals, load charts, nor displays.
Undeterred, the team assessed the work required to bring the crane back to operational status, also calling on the expertise of Manitowoc’s EnCORE refurbishment specialists.
The restoration plan included:
- Re-sealing of the hoist cylinder
- Re-sealing of outrigger cylinders and jacks
- Complete refurbishment of service and parking brake systems
- Replacement of all gauges
- Full service of the engine and transmission
- Installation of a completely new LMI system
Ports & Harbours sourced the spare parts through Manitowoc and called on the company’s EnCORE consultants for insights and guidance.
The refurbishment took a full week, but has completely restored the crane’s functionality.
“Manitowoc’s parts support and its EnCORE specialists really came through for us for this project,” said Glyn. “The customer was thrilled that their nearly 50-year-old Grove crane continues to deliver value.”
CHOOSING TO REPAIR MEANS PRESERVING RESOURCES, SAYS AVEZAAT
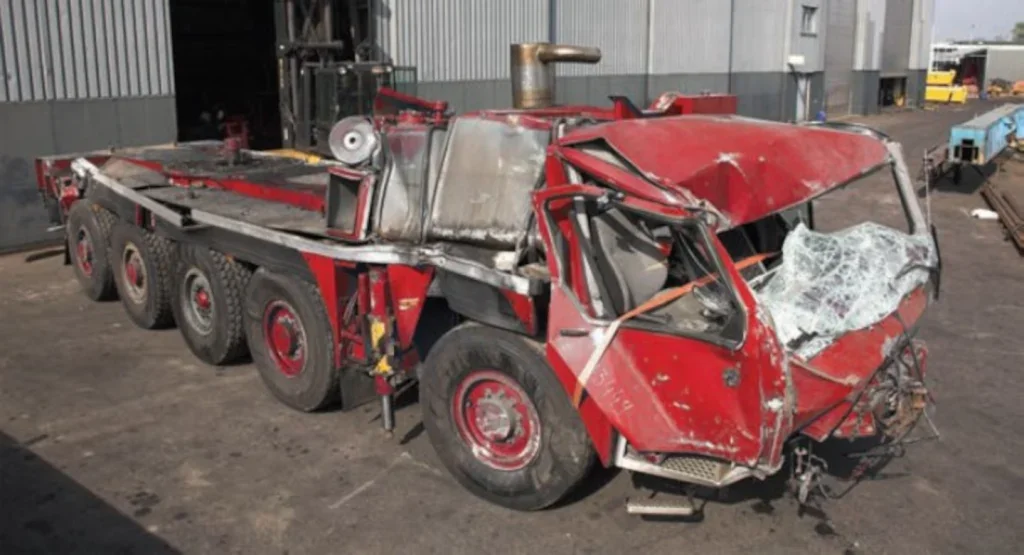
Dutch independent repair and refurb specialist Avezaat Cranes repairs all brands and types of cranes. It is, however, particularly specialised in the repair and overhaul of lattice boom crawlers and telescopic boom cranes. The company is keen to point out the ecological benefi ts of repairing equipment…
‘In a time when we are all becoming more aware of our impact on the environment, we want to highlight the benefi ts of repairing booms and other mobile crane related parts,’ it says. ‘Repairing is most of the time not only faster and more cost-effective, but it’s also a significantly less environmentally impactful than replacing with new parts.
‘By choosing repair, you are contributing to preserving valuable resources and reducing the environmental footprint of your projects… At Avezaat Cranes, we believe in sustainability by reducing the environmental impact of manufacturing new crane parts and cranes.’
The company claims that it’s its combination of skilled and certifi ed employees, specialised tools, and three wellequipped workshops that enables it to repair damaged lattice booms and jibs, in particular, at competitive prices.
The company also sees value in stockpiling. It says that thanks to its approximately 2,800 tonnes of stock (comprising plate, main chord and lacing materials) it can, subsequently, offer short delivery times for customers.
Keeping a large and varied stock of steel materials in plate and tubular materials also helps protect Avezaat, and its customers, from variations in steel availability, it says..
The company uses European and Scandinavian mills for its steel materials, from S690 to S1300 quality.
TADANO FAUN REPAIRS WATER TENDER OWNED BY LAUF FIRE BRIGADE
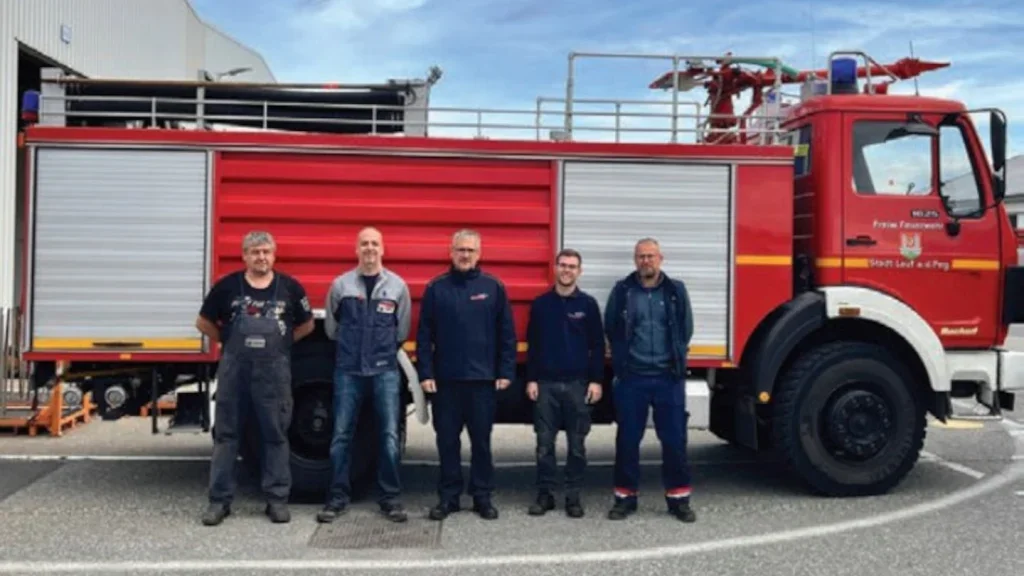
The volunteer fi re brigade in Lauf, a town at the western periphery of the Black Forest, Germany, faced a challenge: its TLF 24/50 water tender, which has been in use for nearly 40 years, required urgent repairs.
The vehicle is an essential part of the brigade’s equipment and features a water tank with a capacity of 5,000 litres, which means it plays a vital role in any local fi re emergencies.
A leak caused by aging meant that the TLF 24/50 had to be temporarily removed from service. But Tadano Faun stepped in repaired the damage in its workshop. “We have the necessary equipment and qualifi ed personnel right here, so we were more than happy to accommodate the fi re brigade’s request,” explains Dr. Martin Schuster, general manager Production at Tadano Faun in Lauf.
Over three days the Tadano specialists sealed the leak and the the outside of the tank and repainted it.
Captain Oliver Heinecke had nothing but words of praise for the company: “It’s really something that Tadano stepped up to the plate and helped us so quickly. Without that, we would have defi nitely been in quite a bit of trouble.”
The repairs were made free of charge, as Tadano Faun felt it was important to support its local fi re brigade.